Dimethyl Ether (DME) is made by converting hydrocarbons which are first converted to methanol and then to DME (Molar 13). It can be made from other sources such as wood byproducts, household and crop waste, or from algae biomass. It’ chemical formula is CH3OCH3 and is considered a more clean fuel than methanol. It’s uses include making dimethyl sulfate, a methylating agent and for making acetic acid. Dimethyl Ether is only useful in very low temperatures, limiting its usefulness.
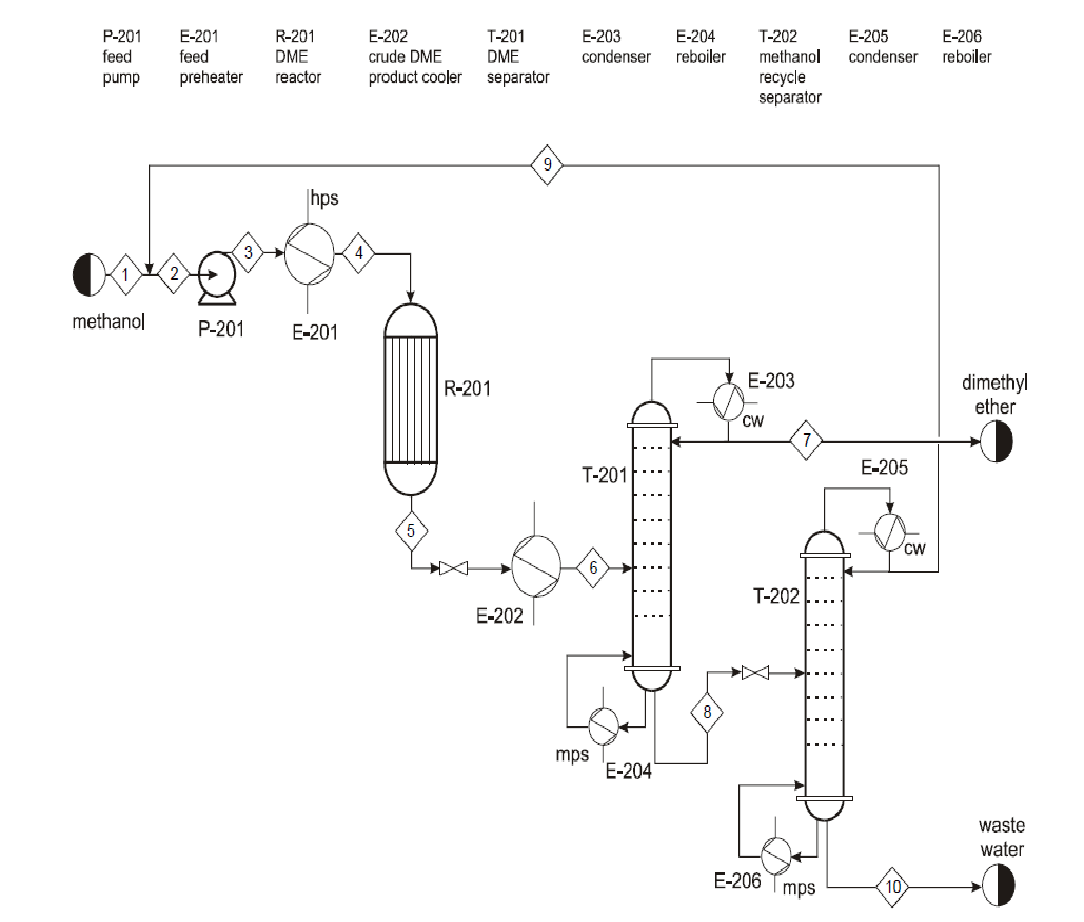
Conversion process
The process of making Dimethyl ether can be summarized in the following equation:
In this reaction, the assumption is that methanol, the only raw material, is in its pure form and the DME produced is pure.
Methanol is fed at 1 atm pressure and 250c. This is methanol from storage as well as recycled methanol from the methanol recycle separator at the end of the process. The pumps and valves in the process are for regulating pressure. Temperature is regulated by using a preheater at the beginning of the process and condensers. The dimethyl reactor converts pure methanol to Dimethyl ether and water which are then separated in a distillation column. Pure dimethyl has to be condensed before storage since it has to be stored in very low temperatures.
Cost analysis and profitability
To obtain costs, several assumptions were made. It was assumed that methanol used was pure, making its cost of purification pure. It was assumed that distillation columns had 100% efficiency, meaning there was no waste of methanol of DME during conversion. The recycle separator for this project was assumed to have an efficiency of 100%, leaving the cost of water treatment at zero. The project runs for 330 days a year to allow time for maintenance and shut down. All calculations were therefore based on a 330 days/year basis.
From this experiment, the costs of operation are steam production, fuel gas for heating, electricity, and cooling water.
From the calculations, the cost of production is $ 8.65/ 1000kgs of DME produced.
Step by step calculations
Assuming 50% conversion of Methanol to DME from the equation
The process will need 200,000,000kgs of methanol to produce 100,000 tonnes of DME per year.
I gallon of methanol = 6.6 pounds
To make 100,000,000 kg of DME, assuming methanol is converted to 50% water and 50% DME, the process would require 2,000,000kgs methanol.
Therefore 2,000,000kgs methanol = 4,409,245.24 pounds = 688,067.46 gallons
Cost of methanol = $ 0.60/gal
Cost of 688,067.46 gallons = $ 400,840.476
Cost of steam $ 1,084,377.35/ yr
Cost of fuel $ 637,776 / yr
Total cost of production = $ (400,840.476 + 1,084,377/35 + 637,776)
= $ 2,122,993.826/ 100,000,000 Kgs of DME produced.
Assuming: The cost of production is 25% of the total product costs
Packaging expenses takes 55%
10% labor costs and administrative and labor costs
10% miscellaneous costs
This means $ 2,122,993.826 = 25%
100% = $8,650,000 which is the cost for every 1,000,000,000 Kgs of DME produced.
These translates to $ 8.65/ 1000kgs of DME produced
Profitability
The cost of dimethyl ether in the market is $ 0.43/lb or $ 0.43/0.45359237kgs
1 pound=0.45359237kgs.
Therefore 1000kgs of DME are worth $ 1055.
Since the cost of production amounts to $ 8.65/ 1000kgs as calculated earlier, this translates to a profit of $ 1046.35 for every 1,000 kgs of DME produced.
In this experiment, the desired production rate at an optimum level is 100,000 tonnes/year.
The project then translates to a profitability of $104,635/year.
It is therefore clear that producing DME from methanol proves viable from the figures, with a profit of $ 104,635/year, assuming a production of 100,000 tonnes/ year. Methanol is easily available considering it can now be produced easily from natural gases. It can also be made from H2 and CO2, increasing its availability. This makes it a reliable source for the manufacture of DME.
Recommendations
Dimethyl ether has more hazardous fires as a result of its low flash points. It has a flash point of -410c causing it to form explosive mixtures easily (Albright 13). Any experiment involving DME should be done under professional supervision and uncompromisable safety measures. The process requires a lot of water for cooling and condensation. DME manufacturing plants should be located in places where water is easily accessible. Since the biggest cost of production is that of energy, the project can be made cheaper by using renewable energy such as solar where applicable.
References
Albright, Frederick. Chemical Engineering Handbook. Boca Raton: CRC press, 2009. Print.
Molar, Aresta. Carbon Dioxide Recovery and Utilization. New York: Kluwer Publishers, 2007. Print.