Introduction
Corrosion is defined as the breakup of materials to its component atoms after series of chemical reactions caused by its immediate surrounding or immediate environment. This article is going to examine the dynamics involving corrosion of materials. The corrosion of materials is attributed to a number of factors that are contributed by the environment. Corrosion contributes to loss of materials especially metallic in nature. The word corrosion has often substituted the word chemical oxidation in most literature. Metals are the most affected materials and this affects the operations of most machinery made of metallic materials. The smooth operations of metallic parts in a machine can be greatly hindered by corrosion of the moving parts.
Definition of corrosion
Metals are susceptible to chemical reactions which results in them being eaten away through oxidation processes. This also results in the change of composition of its atoms making the metal much weaker. Corrosion of metal manifests itself in the form of rust. In his studies Brewster (2007) states that the degree of corrosion also varies from material to material as the chemical composition of every material differs from each other. There are some materials that corrode due to mere exposure to moisture in the air; while there are some metal are corroded after heavy exposure to moisture in the form of water. There are several methods of mitigating the effects of corrosion on materials. While they may vary in terms of actual results, some of them have been proven to work. An example of a preventive measure is to oil the moving parts and chromate conversion. According to Clark (1992), corrosion is a long term, process and also matters to the environmental factors. Cars found in coastal towns exhibit heavy signs of corrosion due to the heavy humidity.
Corrosion in Other material
Polymers are the best examples of material other than metals that undergo corrosion. There are changes in the structure of the polymer which results in the weakening of the material if exposed to environmental elements such as heat, rain and other elements. Polymer cracks when corroding and loses weight. Corrosion in polymers is be due to the large size of the molecules which reduce the tensile strength of the polymer and results in further cracking and general disintegration. Apart from the environmental factors, polymers can also be degraded when exposed to chemical agents such as alkali and acid.
Factors contributing to corrosion
Corrosion is affected by many factors but the main ones include, temperature, size of the metal, type of the metal, climate. Temperature increases the rate of disintegration of a metal. Any rise in temperature alters the chemical structure of the material. A hot and moist environment is sure to have a great effect on the rate of corrosion and this explains the reason why corrosion happens faster in coastal towns. Another factor that affects corrosion is the size of the metal. A metal that displays thick structure characteristics is more susceptible to corrosion. This fact is clearly manifested during the treatment of the metal, the thinner sections of the metal are often found to have a lower level of corrosion attack than the rest of the metal which is thicker. When treating the metal, it is advised to first identify the integrity of the metal and strong points of the major parts, this will ensure that corrosion is detected first and preventive measures taken in order to stop it from spreading to other parts of the metal. Another factor that has an inclination towards the rate of corrosion on a material is the presence of foreign material. Foreign materials are manifested through soil, foreign residue and even atmospheric dust. Soil that can be trapped between the materials can increase the rate of corrosion as it becomes more and more humid as it absorbs atmospheric moisture.
Chemistry of Corrosion
The chemistry of corrosion refers to the forces that drive the metals to disintegrate from their original chemical structure, to become weaker. Energy is required in order to liberate the metals from their original compounds. Reactions occur as a result of swap over of electrons. Corrosion is mostly contributed from an electrochemical progression on the material. Environments with acid and one that is salty hasten the rate at which materials are degenerated. Such environments support the formation of electrolytic cells on the material that leads it to be eaten away. Corrosion can also be presented in the formation of green sediments in the materials. The temporal presence of corrosion in metallic form is what causes the degeneration. It is necessary for the material to soak up and store up energy that is necessary for the liberation of the material from their original compound.
The environment is controlled by factors such as the alkalinity of solution where the material could be exposed to. An alkaline environment is one that is composed of excess hydrogen ions that could be present. The hydrogen ions contribute to acidity and the hydroxyl ions contribute to the alkalinity of the solution. The solution can also change in its other properties without necessarily increasing in acidity. This can be shown by the example whereby hydrogen ions can be formed in water by the bringing in hydrochloric acid or sulfuric acid, both of which are immaterial. Corrosion affects mostly iron and steel after oxidation. There are metals such as aluminum which react to environmental oxidation by forming an outer shell which is a tough oxide that links itself to the metal surface and thus limiting further exposure of the metal from further effects of corrosion and oxidation agents. It is also important to note that corrosion happens in areas where moisture is evident. Moist air can also cause corrosion as in the case of most metal corrosions, this leads to the phenomenon that is mostly referred to rusting of metals. This is explained using the chemical equations below.
Fe ——-> Fe+2 + 2 e–
The quantity of water that can b complexed with the iron (III) oxide that is also referred to as ferric oxide, this amount also determines the color of rust or corrosion. In his experiments Talbot (2008), reports that corrosion can be seen through many colors from yellow to orange and sometimes orange brown. The next step of events is characterized by the presence of moisture in the form of water and oxygen. The process of oxidation results in the formation of ferric ions as illustrated below:
Fe+2 ————> Fe+3 + 1 e–
Reduction of oxygen is done through electrons that have been supplied from the oxidation steps that have been shown above.
O2 (g) + 2 H2O + 4e– ——> 4 OH–
Formation of ferric oxide is aided by the combination of oxygen and ferric ions. The oxide is filled with various amounts of water in its process of hydration. This is because of the actual electrons is generated through actual oxidation of the metal which in our case is iron. The electrodes are conducted through the process of diffusion in the water and transferred to another point where there is sufficient oxygen. Varshneya (2006) states that he resultant reaction is an electrochemical cell whereby the iron acts as an anode; oxygen gas bubbles act as the cathode while the aqueous solution acts a salt bridge. Moisture increases the rate at which rust formation occurs. A salty environment also increases the rate of electrochemical rusting.
Corrosion Thermodynamics
Damage is determined by reactivity of local environment. Thermodynamics has been used to estimate any theoretical activity of any metal or alloy in a situation that supports corrosion. This can be done when the chemical composition of the metal is known. It is important to note that the environment where the metal is exposed to is just a variable which can easily vary with time and set conditions. The environment plays a major role in influencing the formation of rust. The environment to some extent matches the micro environmental conditions. In his discussions this can be best explained as the confined environment at the external shell of the metal. Thee extent to which the metal or material is corroded is determined by reactivity of this confined environment, which is also determined by factors such as ion flow, number of pH cells ands deposits.
Corrosion Kinetics
Corrosion situations can be best explained using a number of thermodynamic principles. The situation encompasses the stability of the chemical species and the reactions linked to the process. If two metals are in contact with each other, they can generate a voltage as in an electrochemical cell. In his discussions Clark (2002) explains that the galvanic series determines the anode from the cathode. Materials that are higher in the galvanic series have a tendency to sustain a cathodic reaction. Metals such as iron will tend to corrode when attached to graphite or platinum. Varshneya (2006), states that as much as the galvanic series tries to present a clear view, it cannot forecast the rate of corrosion. Balancing processes that can take place over surfaces that are metallic; the resultant potential from such reactions is often conciliation between different equilibrium potentials of all reactions drawn in. Polarization is referred to as the variation between potential (E) and each reaction equilibrium potential, Eeq. This can be illustrated through the chemical equation below:
h=E-Eeq
Where h is defined as over potential. The polarization can be referred to as anodic, when the electrode process is stepped up in terms of speed of reaction.
Corrosion Prevention by Electrochemical Methods
Corrosion in materials can be avoided by applying electrochemical principles that are categorized under two classes. There are sacrificial anodes and cathodic shielding by the application of currents. In the sacrificial anodes, the process of corrosion is permitted to take place on a metal piece that could be superfluous to the metal structure. An example of this can be shown when apiece of zinc metal is attached to a steel hull of a ship or boat. This can be shown by an Evans Diagram below.
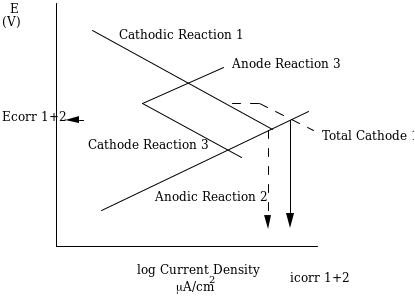
According to the Evens diagram, anode # 3 is shown as being protected from corrosion and disintegration by the reaction of anode #2. Application of this method can be shown in the Galvanized bolts, automobile steel among other metal applications. We can again see that the galvanic series, playing a role as characteristic coating that work on the principal of the sacrificial anode are zinc on steel, aluminum and cadmium on steel. It is important to note that cadmium is just below steel in the series; hence it is limited in terms of “throwing power”. In his book Moran (2005) states that throwing power can be best defined as the ability to shield metal from corrosion over large distance.
Cathodic Protection through application of current: Voltage or cathodic current is applied to the metal with the sole purpose of ensuring that the metal requiring protection is kept at its cathodic region. A diagram illustrating the whole process is as shown below:
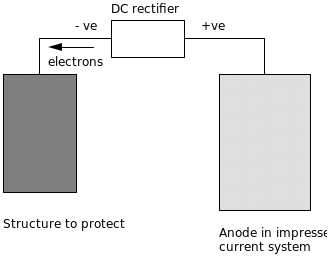
The anode in this case can be consumable and made from the less costly materials such as scrap metal. In his book, Riquelme (2009) concludes that there are also incidences where the anode is not consumed at all and such a case of cathodic protection is of steel in concrete that is reinforced. It has been found that it is difficult to replace anodes. Varshneya (2006) states that this method is limited by a phenomenon often referred to as stay currents. This phenomena occurs when a short circuit path becomes is present between the anode and cathode, whereby the current is transmitted away. A good illustration of this would be the close proximity of a second metal conductor to both anode and cathode. The short circuit component has the effect of corroding the anode, hence limiting the protection.
Methods of Control
Anodic protection: A current can be applied to a material in order to induce the drawing out of electrons out of the metal until it reaches a state where it penetrates into the passive region. The main advantage to this is that it is much cheaper to run such a system. The main disadvantage of such is that it is a complex system that requires specialized persons and can easily become hazardous in a case where power fails. It can also become unsafe as such a scenario can become uncontrollable. It is because of this that such a system is not very popular.
Inhibitors: Inhibitors are implemented in the reduction or blocking of corrosion as they adapt several mechanisms such as Adsorption inhibitors which shield the metal from corrosion by adsorption on the metal that could be presented to the electrolyte. Another technique of using inhibitors is through the introduction of poisons that act as inhibitors limiting hydrogen ion reduction or generation of cathodic reduction involving hydroxyl ions. The third type of inhibitor mechanism is through filming inhibitors which is through the formation of protective films through the addition of particular ions that have high redox reaction potential.
Types of Corrosive atmospheres
There are several types of corrosive atmospheres where they are defined by the number of corrosive elements that could be present. It has been found out that the more aggressive the corrosive environment, the higher the importance in choosing a proper protective coating that can withstand it. Basically there are four types of corrosion environments such as industrial, marine, rural and indoor environments. A manufacturing environment is full of contamination that comprises of sulfur and other lethal compounds which aids in the formation of acid rain. When the rain falls on metallic objects, it corrodes the metals as it combines with smog and other gaseous compounds to form acidic rains. It is also important to note that an acidic environment is also full of other compounds such as chlorides that are even more corrosive. Corrosion caused by chloride compounds is more pronounced than in other compounds.
Marine environment: In his research Kaesche (2004) concludes that the degree of corrosion id determined by the quantity of salt deposited which is also dependent on the speed of the wind which carries fine particles of salt. An exposed metallic surface can cause a corrosive external metal shell. The rate of corrosion has been observed to decrease as one gores further away from the sea as the salt deposits become fewer and fewer because of the effect of wind currents. Equipment that are exposed to the sea water are the most affected as the continued splashing and spraying of sea water subjects them to continued cycle of corrosive agents in the form of salt crystals.
Rural: Metals rural atmospheres are exposed to the byproducts of materials found in the farm. Such materials have been found to be extremely corrosive. Waste products from animals, farm pesticides are just a few examples of rural materials that can corrode metals.
Indoor: Indoor environments are the least severe corrosive environments as factors such as wind and extreme heat are absent. However indoor environments provide constant condensation which can be highly corrosive to metals within the confines of the rooms. Indoor environments should be properly ventilated in order to allow the flow of air in to the rooms.
Factors affecting Atmospheric Pollution
Atmospheric pollution is determined by the moisture content in the atmosphere, formation of rain or relatively high humidity. All these factors play a very big role in atmospheric corrosion. Rain also has an important role of washing away salt deposits that may have accumulated on exposed surfaces but also on the other hand it has the effect of corroding metals that if subjected to the metals for a longer time. Dew can become soaked with salt from the oceans and hence thus offer an electrolyte that aids in deterioration of metals.
Measurement of atmospheric factors
There are several techniques which govern how environmental factors will be measured. In his studies Ojovan (2007) explains that the factors measured are the pollutants in the atmosphere, amount of sediments collected on the metal surface and the difference in the time interval between the times that the atmospheric factors have had their effects on the material. Factors such as the temperature, relative humidity and wind direction can be easily measured but some factors such as the time of wetness which is the period between the times that the water settles on the metallic surface are hard to measure. The time of wetness is also the time that the relative humidity is higher than eighty percent. Another method of measuring atmospheric corrosion factors is through the quantity of pollutants that are measured in terms of the rate of salt deposition. Other methods include measuring the salinity of airborne chlorides and measurement of atmospheric corrosivity through coupon exposures.
Pipeline Corrosion
Pipelines deteriorate after some time which is affected by quality of the pipe and environmental effects. Some pipes have been found to last around seventy years if the quality of the metals was found to be high. This lifetime can be increased by implementing coatings and also utilizing methods such as Cathode protection of the metal comprising the pipeline.
Pipe line corrosion in oil & gas pipes (petroleum) & how to treat it
Corrosion in petroleum pipes is estimated to cost petroleum companies about 5.4 Million dollars annually in form of failures and repairs. These companies have resulted in the development of risk management strategies that involve prevention of corrosion in the pipes. Mitigating factors include, Cathode protection of the pipes, regular inspections carried out to evaluate any cases of impending corrosion. Detection of flaws is implemented through smart pigging which involves
Treatment of the flaws after detection is done through, coating of the pipe and performance of cathode protection on the pipes.
Forms of Corrosion
There are several forms of corrosion that exists and are manifested through the degree of attack and the visual observation that can be recorded from the metals. Uniform corrosion reduces the size of the metal as it becomes thinner and thinner over duration of time. This form of corrosion attack can be prevented through coating of the metal, providing cathodic protection and introduction of inhibitors.
Crevice Corrosion: This type of corrosion is linked with small volumes of dormant solutions. This solution can cause holes, and lap joints in stable metals and thus is referred to as crevice corrosion.
Pitting: This form of corrosion often leaves holes on the metal thus causing weaknesses in the structure of the metal. This form of degradation leads to loss of manufacturing apparatus to fail as numerous machine damage leads to systematic structural loss of the metal. This form of corrosion is also difficult to detect as symptoms show up after the full effect has been detected. The other forms of corrosion have less impact but also contribute to the weakening of the metal structure; they are Intergranular corrosion, selective corrosion, erosion corrosion, stress-corrosion cracking
Galvanic Corrosion: This type of corrosion occurs when two metals are in contact or could also be connected through electrical means. The metal that has a lesser resistance becomes anodic, and because the corrosion is between two different metals, it is thus referred to as galvanic corrosion.
Intergranular Corrosion: This type of corrosion is further heightened by surface tension.
Selective Leaching: This process involves the selective elimination of zinc away from alloys such as brass and other alloys.
Erosion Corrosion: This form of corrosion can be detected by the appearance of grooves and rounded holes in the metals. It is also characterized by short duration in which it attacks the metals and resultant rapid degradation of the material.
Stress-Corrosion Cracking: This type of corrosion is characterized by coincident cracking which can be manifested through fine cracks which can be detected when viewed keenly. The metal is virtually un-attacked on the surface but is attacked on the grain of the metal. Cracking appears through the metal hence compromising its strength.
Corrosion testing & monitoring
There needs to be control measures in the mitigation of corrosion effects. The close monitor of metallic characters can decrease the overall effects of corrosion on metals. The benefits of such measures greatly outweigh the costs of undertaking such strategies. These strategies should be done periodically. The timely shut down of systems such as pipelines and factories in order for monitoring to be done is important so as to detect and mitigate corrosion effects. There are several systems in the market that vary both in cost and complexity. We have hand held loggers that are used in the surveillance of atmospheric corrosivity. There are also systems that relay information directly and simultaneously to control rooms and persons. Such information is important as they are able to pin point the area where corrosion is about to affect the whole industrial system. These methods are performed using high precision sensors which are able to dwell on every detail within the metal structure hence prolong the life of the metal.
Protective Coating
This is the most widely used technique of controlling corrosion as the coating separates the surfaces are subject to corrosion from the factors in the environment that heavily cause corrosion. Coatings are important when combined with other techniques of corrosion prevention such as cathodic protection.
Effects of coating on corrosion
Coating assists in the control of corrosion as various coats that are resistant to the corroding factors is highly wanted. Such coatings include powder coatings, which are applied to metallic shells. Many types of coatings have different characteristics that need to be understood before being applied in any environment. Such considerations include the physical properties of the metal where the coating will be applied, the mechanism associated with the coating to be applied and the general environmental elements that the metal is subjected to. Coating also assists in protecting the metals from the environmental element such as heat and excess moisture. Another type of coating used in the prevention of corrosion is through electroplating which is mostly utilized through the passage of current in liquid containing metal ions that are in a liquefied form. The other form of coating is zinc coating which uses other the advantages found in zinc metal. Zinc displays outstanding characteristics such aas its resistance to corrosion in most interior and exterior environments. Zinc coating can also be applied to most metals without any problem occurring hence making it to be one of the best coating materials. The third type of coating that can be applied on metals is through electroless plating which utilizes electroless nickel. Pack cementation is widely used in present resistance to ferrous alloys. The whole process of cementation includes aluminizing, chromizing and introducing silicon to the metal. The other type of metal includes metal cladding and thermal spraying which involves putting in energy to the metallic surfaces in order for adhesion to occur. Plasma are applied in the reduction of the high temperatures that happen in the process. Corrosion prevention can also be done through physical vapor deposition which is very clean whereby the coating is dumped over the entire material concurrently as opposed to one particular area.
CP Design Systems
Cathodic protection designs are first implemented by conducting the required testing and conduction of site evaluations. Cathodic protections assist in the protection of structures as corrosion effects are mitigated fully. This method utilizes metals that could be in contact with each other. A metal that could be in touch with the other is fully induced with a polarized current that is strained against the interface. Polarization of the metals results in the metal achieving a homogeneous interface which is able to withstand corrosion and corrosion effects.
Factors affecting CP Design: The design of a Cathodic protection system involves many factors such as the selection of a material that fulfils the requirements set for a suitable material that will act as the anode, the physical dimensions of the material and the technique in which installation of the galvanic methods. The design values of the cathode protection are also to be taken into consideration; this includes the current densities which is the current per unit surface area. Another factor that needs to be taken to consideration is the coating effect in respect with the demands placed on current.
Cathodic Protection
CP. shields metals by interfering with natural actions of the electrochemical cells accountable for metal deterioration. CP. can be implemented to manage the metal surfaces that are open to environmental elements. This is done in order to provide the necessary electrical current to the galvanic anode protection.
Conclusion
Corrosion has the effect of deleting the metallic structure which greatly inhibits the performance of equipments and machines. Greater emphasis on research into ways of reducing the effects of corrosion should be developed in order to mitigate the financial cost that is experienced by most persons especially those in the industrial sector.
List of References
Brewster, M. (2007) Fundamental aspects of corrosion films in corrosion science. California, Springer.
Clark, E. (2002) Corrosion of Glass, Ceramics and Ceramic Superconductors. Sydney, CRC Publishers.
Kaesche, H. (2004) Corrosion of metals: physicochemical principles and current problems. Sydney, Longman Publishers.
Moran, C. (2005) Corrosion monitoring in industrial plants using nondestructive testing and electrochemical methods. Perth, ASTM International.
Ojovan, M. (2007) New Developments in Glassy Nuclear Waste forms. New York, Nova Science Publishers.
Riquelme, R. (2009) Corrosion: understanding the basics. London, Oxford Publishers.
Talbot, E. (2008) Corrosion science and technology. New York, CRC Press.
Varshneya, A.K. (2006) Fundamentals of inorganic glasses. London, Oxford publishers.