Problems Facing Eastern Gear
The rapid increase in costs can be viewed as the primary problem that the company has to face in the environment of the increasingly high competition. Therefore, the current strategy regarding the management of costs needs to be addressed properly. Another factor that can be viewed as the cause of major concerns is the fact that there is no special workflow for the orders of different sizes. While utilizing the given approach made sense when the company was dealing primarily with small orders, it hampers the work process at present. Now that the organization leaders have decided that the entrepreneurship’s capacities can be increased, there is a strong need to redesign the current approach toward the workflow.
Problems Analysis and Suggested Solutions
First and most obvious, the issue regarding the expenses that the firm has been suffering needs to be dealt with. On the one hand, by entering a new market and considering the provision of new services, a firm is likely to expect a rise in costs. On the one hand, an efficient cost control policy needs to be in action so that entrepreneurship could remain profitable. Therefore, a detailed analysis of the costs taken by the organization will have to be carried out (Schroeder, Goldstein, & Rungtusanatham, 2013a).
For instance, one should pay attention to the fact that the company employs the staff that is both skilled and semi-skilled, yet does nothing to improve their abilities. Therefore, investing in staff could be a reasonable step to take. By providing employees with an opportunity to improve their skills and gain new knowledge, the firm is likely to increase its profit margins significantly. The reasons behind the above speculations are rather simple. First, by enhancing the staff’s expertise, the organization is likely to reduce the instances of errors in the production process significantly.
As a result, an impressive drop in defective goods will ensue. The reduction in the number of faulty products, in turn, will allow for a rapid increase in income and the rates of customer loyalty. Consequently, the company will gain not only a financial profit but also the competitiveness that will help it remain efficient in the target market. Next, by investing in the staff, the firm will display its readiness to cooperate and value its members as an important resource that it will cherish and promote growth for. Hence, the employees will appreciate the offer of the entrepreneurship and display higher loyalty rates to the company. Thus, the efficacy of their work will also rise.
As far as the issue of the workflow is concerned, the workflow, can be improved significantly once the departments are located more reasonably. The premises can be described as rather spacious; therefore, the functions of some of the rooms can be switched around so that a considerable amount of time and effort could be saved. For example, it can be suggested that the room where the drilling process occurs should be located closer to the one with milling machines. The shipping dock along with the storage room for the related tools can be located further from the finishing and grinding center, as Figure 1 shows. Thus, the production process will occur at a faster pace, time is used more carefully.
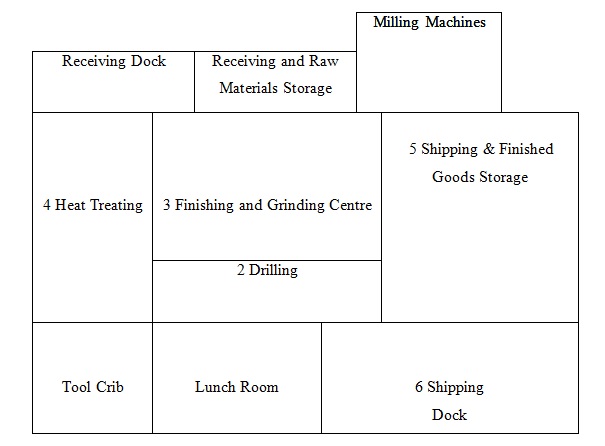
Recommendations
The solutions to the current state of affairs outlined above must have a positive effect on the organization, leading to a rapid improvement in its performance. However, one must admit that the promotion of these changes may take considerable time, especially given the fact that the training process will have to be designed elaborately and carried out among the staff. Therefore, the reconsideration of the company’s use of resources is highly desirable so that the firm could maintain its current position. The promotion of the principles of sustainability in resource use is, therefore, the option that the company will have to accept. By using the principles of sustainability, the firm will be able to relocate the resources so that the expenditures could be reduced and that the areas in need of enhancement could be supported (Schroeder et al., 2013a).
Apart from the concept of sustainability, the use of an appropriate leadership model that will help motivate the staff and get them ready for the changes in the organization will have to be adopted. A redesign of the supply chain is likely to cause concern among the employees since they will have to alter their behavioral patterns to meet the new demands (Schroeder, Goldstein, & Rungtusanatham, 2013b). Therefore, the principles of transformative leadership along with the introduction of the tools that will help transfer the necessary data fast and efficiently are highly recommended. As soon as the actions of the members of every department are coordinated, the entrepreneurship is bound to regain its position in the target market and accept the new tasks and challenges successfully.
Reference List
Schroeder, R. J., Goldstein, M. J., & Rungtusanatham, S. M. (2013a). Service delivery system design. In Operations management in the supply chain: Decisions and cases (pp. 86–109). New York City, NY: McGraw-Hill Education.
Schroeder, R. J., Goldstein, M. J., & Rungtusanatham, S. M. (2013b). The operations function. In Operations management in the supply chain: Decisions and cases (2-60). New York City, NY: McGraw-Hill Education.