Introduction
Aircraft building is a complicated process that requires meticulous selection of the right materials. Engineers must fully understand the qualities and limitations of all construction materials in order to make the right selection. Ideal metals for aircraft production often have minimal weight, are corrosion, fatigue, heat, and crack resistant, and also have high strengths. Since it is difficult to find metals with all these qualities, then manufacturers often resort to a combination of materials. Nonetheless, the chief metal used in a certain alloy will have a direct impact on the traits of the alloy and hence their applicability in airplane construction.
Aluminum
Perhaps the most widely used metal in the aircraft industry is aluminum. Its mechanical, chemical, and physical properties make it ideal for this purpose. First, aluminum is readily available and low in cost. Additionally, it has low weight and high strength. Since several aircraft parts ought to be corrosion resistant, the materials used in manufacture should possess these traits. Aluminum has this property, particularly when forming alloys with other metals. The metal is highly malleable in that manufacturers can easily shape and extend it. Aircraft construction is a relatively complex process; consequently, one must select metals that are easy to work with. Aluminum requires uncomplicated processes and has minimal restrictions on the nature of the environment they require. In essence, manufacturers need to control dust or temperature before working on aluminum. Airplanes must operate in extreme conditions of weather such as high temperature and moisture. Therefore, materials used to construct them must demonstrate high resistance to these conditions; aluminum has those qualities. Owing to the high level of availability of the metal, it is easy to obtain empirical data about it and thus make wise decisions concerning its use. Other qualities that make aluminum desirable in the aerospace industry include are its recyclability, the ease with which one can inspect parts as well as the simplicity of the repair process. Aluminum manufacture has changed dramatically because of the introduction of fasteners and rivets; this has streamlined aircraft manufacture substantially (Crane 2012). Shown below is an aluminum plate that represents some of the properties exhibited by aluminum.
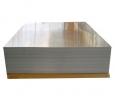
Within the aircraft industry, one is likely to find aluminum in the form of alloys, which mitigate some of the unwanted properties of aluminum and strengthen its desirable ones. The two most prevalent alloys of the metal include the 6061-T6 variety and the 2024-T4 variety. These alloys contain elements of copper, silicon, chromium, magnesium, manganese, and chromium in variable percentages. Various aspects of aircraft construction rely on aluminum and its alloys. In certain instances, they make jetliners, airplane engines, and other aircraft parts. Most times, these could be related to their fabric design or the steel tube under consideration.
In the industrial sector, a popular method of applying aluminum in aircraft construction is through the use of sheet metal. Sheet metal was an evolutionary and cost-effective way of doing aircraft construction. Engineers in the aerospace construction industry need to combine structural integrity with ease of building. aluminum manufacture, through the use of sheet metal, was an effective way of achieving this. In this process, manufacturers make extensive use of rivets in order to ascertain that the construction process is as straightforward as possible. In the past, several airplane builders utilized bucked rivets, but this made the process longer. One must be an expert in bucking and hammering. It was also necessary to include extra processes in airplane construction, like air compression and bucking-bar assortment. This meant that manufacturers needed more experts, and they had to be quite skilled. Conversely, when using aluminum in the sheet metal process, one does not require all these processes. Standard rivets are available, and any amateur can use them to construct aircraft. This is the reason why stakeholders call them standard rivets. They only require bucking on one side. Additionally, builders can access any side of the rivet without having to change any side. As a result, it is possible to build airplanes at a much faster rate than was previously possible. The aluminum rivets make it quite easy to join different parts in airplane construction without creating a smooth aesthetic finish. These tools have a long grip area such that users do not need to invest in various sizes to suit their needs. This saves them a lot of expenditure on rivet financing. As such, one may say that aluminum rivets are essential in making airplane construction easy, durable, and strong.
Qualities of aluminum in aircraft construction and their applicability.
Source: US War Department 2011, Aircraft sheet metal work, Lindsay Publications, Chicago.
Titanium
The use of titanium within the aerospace industry came as a result of the limitations of aluminum. aluminum alloys largely exhibited low heat resistance. Furthermore, some of them could not withstand complicated conditions of pressure, radiation, and corrosion. As a consequence, titanium became the preferred metal in these types of conditions.
Some of the qualities of Titanium that make it ideal for airplane construction include its high corrosion resistance. Many airplane parts interact with composite materials that could be susceptible to corrosion. Therefore, a material that resists these types of conditions is highly desirable. The metal is inert and does not react with chemicals in the aircraft. Titanium can resist high temperatures thus making it ideal for combustion parts in an aircraft. Some airplane parts may be loaded with heavy cargo; consequently, they require materials that are hard and strong. Titanium possesses both these qualities (US War Department 2011). Shown below is a diagrammatic illustration of the qualities of titanium.
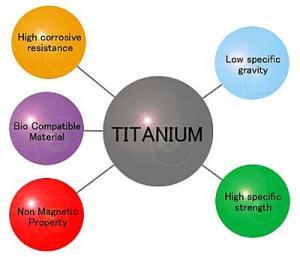
Owing to the above qualities, titanium has wide applicability in several air parts. For instance, engineers use the products to fabricate doors and hatch edges. The metal is desirable in this situation because it can resist high levels of corrosion. Doors must come in contact with a lot of moisture during flying. As mentioned earlier Titanium is resistant to high temperatures. This makes it ideal for use in various parts of an engine. They are also highly applicable in making cargo cabins because of their hardness and strength. One is also likely to find titanium in planning parts, and wings because they are hard and withstand heavy loads. There is no end to the applicability of this metal in airplane construction. Titanium alloys exist in steering wheels, wings, hydraulic systems, lead pipes, fasteners, panels, and airflow ducts. Most companies prefer to obtain prefabricated titanium parts in order to create their own aircraft. These semi-finished products often come in the form of sheets, flaps, rails, and plates.
Stainless steel
Stainless steel is also another metal that is gaining increased applicability in the aerospace industry. This stems from the need to minimize product life cycle costs. In aerospace, stainless steel is mostly applicable as a superalloy. Through upgrades using other metals like chromium and titanium, the products can be applied in different parts of airplane construction. As the name suggests, stainless steel is corrosion-resistant, which is a highly desirable quality in the aerospace industry. In countries like the US, aviation stakeholders lose about 279 billion dollars annually due to corrosion. Consequently, these parties can save a lot of money if they utilize a material that is innately corrosion resistant. On the flip side, stainless steel, as a material on its own, cannot withstand tough aviation conditions. They are not strong or tough enough to operate within those conditions. As a result, they must be combined with metals that possess these desirable qualities (FAA 2012).
High-strength stainless steel is one of the most useful ferrous alloys in the aviation industry. It is suitable for aircraft construction owing to its corrosion resistance, which allows aircraft to interact with the environment and other liquid components without a problem. This corrosion resistance is prevalent even in high-stress situations. Additionally, this metal has high strength thus making it suitable for parts that are susceptible to heavy loads. Toughness is also another desirable quality that makes the product yield effective outcomes. Not all versions of stainless steel exhibit the same characteristics under varied conditions of temperature and pressure. Therefore, one must select an alloy that maintains the desired traits under certain conditions of pressure. Stainless 475 is one such version that can show considerable ductility and toughness even under increased conditions of temperature and pressure. Stainless steel alloys are also showing damage resistance, which is a quality that is indispensable in aviation. Shown below is a table with different versions of stainless steel and their qualities. All versions make structural components of aircraft’s.
Source: Crane, D 2012, Aviation mechanic handbook: The aviation standard, Aviation supplies, and academics, LA.
Owing to the above qualities, different versions of Stainless Steel are suitable for different parts of airplane manufacture. For instance, 465 Stainless steel is appropriate for making landing gear, flap tracks, and actuators because of its hardness and strength. Additionally, the corrosion resistance of the metal makes it ideal for such situations. Furthermore, parts that interact with external environments often benefit from the qualities inherent in such metals. Other versions of stainless steel are also appropriate for airplane frames because of their rigidity. The material may also be found on nuts and bolts used in plane undercarriages, main plane reinforcements, and engine beams. Shown below is a diagrammatic illustration of the stainless steel making process.
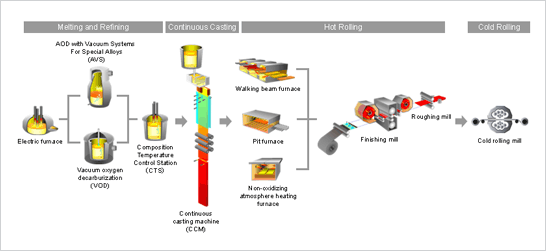
Magnesium
Magnesium is highly desirable in aircraft construction owing to the weight of the material. On the flip side, the metal is not strong enough to be used in airplanes without other metals. Therefore, magnesium may be combined with manganese, zinc, and aluminum in airplane construction. Since the metal is widely available in seawater and other waste solutions then engineers need not worry about its dwindling supply. Manufacturers may decide to what extent their aircraft will contain magnesium. Some commercial aircraft may use a substantial proportion of the metal alloy and end up weighing much less than a comparable aluminum type. While the density of aluminum alloys lies between 2.5 to 2.8, most magnesium alloys will have a much lower density; these often lie between 1.76 and 1.83 (Nelson 2008). Therefore, one can understand why aircrafts made of magnesium alloys would be much lighter.
One of the qualities that make magnesium a good option for making planes is its response to forging. Magnesium alloys can be easily forged depending on what one is looking for in their respective engines. Additionally, the product has high thermal conductivity and a favorable melting point. This means that most of the applications that utilized aluminum can also depend on magnesium for the same. Perhaps the most noteworthy characteristic of magnesium is its lightweight. The product is highly applicable in making helicopters because these aircraft need to be as light as possible. When combined with other elements, magnesium displays high strength levels, which are indispensable in aviation. The melting point of magnesium is 650 degrees Celsius, which is comparable to the melting of aluminum (6600C). This means that the way aircraft parts will respond in similar ways to heat at those temperatures. Minimal changes to manufacturing processes will be necessary when dealing with these components. The diagram below compares the densities of magnesium and an aluminum piece.
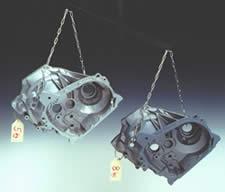
During the alloying process, most manufacturers prefer to use hydraulic processes or mechanical presses for forging. Other processes include quenching, aging, stabilizing, annealing, and heat treatment. Annealing takes place through a rolling mill. Here, one is likely to find a heat treatment solution that covers the solid magnesium. The result is a stronger and more ductile product than before. Aging then follows heat treatment in order to increase the strength and hardness of the alloy. One should note that magnesium reactivity with fire is a point of concern during the manufacturing process. When magnesium chips/ dust are prevalent in the factory or workshop, they can easily catch fire. Consequently, utmost care should be taken to ensure that the material is not easily available in this form. Elements that are central to the alloying process include manganese, zinc, and aluminum.
The metal is mostly applicable in turbine engine casings. It is also appropriate for brackets used in engine mounting as well as engine crankcases. Turbine engines have casings that also consist of magnesium alloys. Piston engines may also consist of these components. Oil tanks, ducts, and nose-wheel doors have magnesium. Wingtips, floorings, and instrument panels are some of the many applications used to make magnesium-derived airplanes.
Copper
Many engineers know copper for its electrical conductivity. The quality has made it one of the most widely used metals in electrical applications. In the aerospace industry, a lot of instances necessitate the use of materials with high electrical conductivity. On the other hand, copper is a relatively heavy metal; this limits its use to mostly small items that do not account for the bulk of the aircraft (Snodgrass and Moran 2011).
Some of the qualities of copper that make the metal appealing for aircraft construction are its ductility and malleability. This means that it can be bent and fabricated into a wire that can be used in different electrical systems. As mentioned earlier, the product has a high thermal and electrical conductivity, which means that it is ideal for electrical systems in an aircraft. Tensile strengths for copper and its alloys are also acceptable. However, they can be reworked and improved through cold rolling. In fact, the ability to alter the chemical and physical properties of copper easily through synthetic processes makes it quite suitable for the aviation industry. For instance, the elongation of copper can be substantially increased through the addition of nickel and beryllium. Additionally, it is possible to increase the tensile strength of the metal from 70,000 psi to 20,000 psi using heat treatment. Even the addition of other metals in brass makes a copper change from a ductile substance to a strong one. Copper could also be a constituent of aluminum alloys. One of the widely known forms of the material is T3, which is heat-treated into the product needed in aviation.
In aircraft, one is likely to find copper in landing gears, brackets, lock wire, bus bars, or bonding. The latter three applications are all-electric systems that substantially depend on copper. When one uses copper in sparing quantities with aluminum, one is likely to find it in aircraft rivets, truck wheels, fittings, and compressor rings. The diagram below is a series of bus bars used for the transmission of electricity.
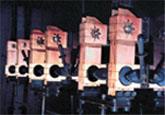
The following are some copper alloys that many use in the aerospace industry extensively.
Source: Crane, D 2012, Aviation mechanic handbook: The aviation standard, Aviation supplies, and academics, LA.
Shown below is a summary of aircraft components in order to demonstrate parts where the above metals are applied.
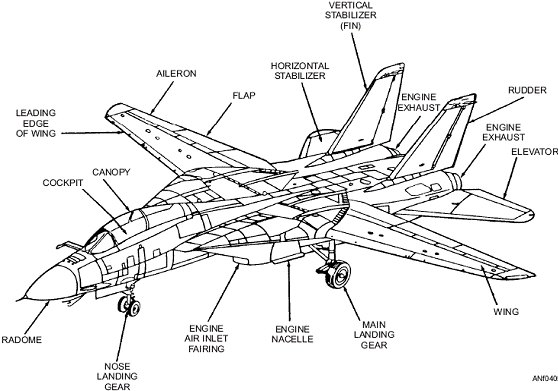
Conclusion
aluminum is the most commonly-used metal in aircraft construction; this stems from the ease of availability, weight, and ease of fabrication of the metal. However, alloying it with other materials mitigates its deficiencies. Other common metals in aerospace include titanium, magnesium, stainless steel, and copper. Most of these materials cannot be used in their natural state owing to certain deficiencies. Therefore, manufacturers must combine them with other metals that minimize their weaknesses and increase their strengths. Usually, this stretches some of the qualities inherent in the products.
References
Crane, D 2012, Aviation mechanic handbook: The aviation standard, Aviation supplies and academics, LA.
FAA 2012. Federal Aviation Regulations for aviation maintenance technicians, Aviation Supplies and Academics, Washington.
Nelson, W 2008, Airplane lofting, McGrawhill, New York.
Snodgrass J and Moran, J 2011, ASM Handbook, ASM, New York.
US War Department 2011, Aircraft sheet metal work, Lindsay Publications, Chicago.