Abstract
This report is about B31.11 code that outlines technical requirements for slurry piping systems. B31.11 is a standard code for inspecting and examining piping systems installation procedures, conducting mechanical and physical tests, and evaluating them for fitness of purpose in terms of meeting outlined technical and maintenance requirements to ensure the general public, workers, and piping systems are protected against any form of damage and destruction that may be intentional or accidental. The pipes are used to transport slurry from one plant to another and within terminal points. The piping nomenclature was developed by the American Society of Mechanical Engineers commonly referred to as ASME.
It was principally developed to cover technical requirements for the construction, installation, and maintenance of pipes in slurry piping systems. These standards define technical requirements for pipes used above the ground and the underground. It also covers the materials used for their construction and a typical analysis of the mechanical the properties of these materials. Other substitute materials such as plastics are covered in the report. It highlights API in relation to B31.11’s limitations in terms of cost and certifications.
B31
B31.11 is a code that was developed principally to cover technical requirements for the construction, installation, and maintenance of pipes in pressure piping systems. The code was developed by the American Society of Mechanical Engineers commonly referred to as ASME. This standard is applied across a spectrum of piping systems which include transportation of gases and liquids, heat transfer systems, process and gas piping systems, general piping in buildings, and pressure transmission systems. The code was previously known as ANSI B31.11 before it converted to B31. The standard was designed to ensure safe use of piping systems in all areas of application.
B31.11
B31.11 is a standard code for inspecting and examining slurry piping systems installation procedures, conducting mechanical and physical tests, and evaluating them for fitness of purpose in terms of meeting outlined technical and maintenance requirements to ensure the general public, workers, and piping systems are protected against any form of damage and destruction that may be intentional or accidental. It has further established standards for ensuring the polluting effects of the slurry on the environment are mitigated. These pipes are used for transporting slurry from one plant to another and within terminal points.
The code specifies technical and a safety requirement for transporting aqueous slurry that is characterized by non-hazardous materials. They are also used in pressure pumping and regulation stations, with clear technical specifications for all piping pressures. The code specifies lower and higher operating temperature limits which are in the range of -29 to 121 degrees centigrade. However, the code falls short of specifying technical requirements for auxiliary piping which includes water, fuel, gas, steam, and lubricating substances.
It also outlines inspection specifications for slurry piping systems where pressure releases from these systems are extremely high. Under this code, piping systems that accommodate pressure with a lower limit of 15 PSIG and upper limit of 16 PSIG are specified. This code was established in 2001.
In addition to that, the B31.11 code provides minimum standards that slurry piping systems adhere to. Standard requirements in the slurry transportation system include design requirements, systems construction procedures, methods, and standards for producing and inspecting the pipes. Other specifications outlined here include standard requirements for slurry systems security, methods and standards used for insulating these pipes when they are used in piping systems that transports dangerous and hazardous materials. That is in addition to the requirements for transporting slurry between processing and receptor plants. This code was established in 2002 by the American Society of Mechanical Engineers
B31.11 and API
API is an abbreviation for American Petroleum Industry. An interface between API standards and B31.11 standards designed by ASME provides technical requirements to qualify piping systems for the petroleum industry.
Where the B31.11 code was used
Standardized pipes have two distinct areas of application. One of them is power piping and transportation of slurry for companies that are involved in mining activities. The second one is in pressure transfer systems particularly for boilers, generally referred to as pressure piping. For boiler systems, B31.11 code covers specifications for boilers and valves used in power piping. In addition to that, the code covers all connection specifications made on boilers including and other technical requirements that are outlined in the 1972 ASME specifications. In addition to that, the code covers requirements for repairing broken pipes, modifying these pipes, and the piping components incorporated in the design (Moles &Zhang, 2008).
It’s worth noting that the code is divided into sections that are divided among task groups. These task groups include general requirements for materials used to design and built these pipes, task groups entitled with the design of these pipes, groups tasked with examining and evaluating these pipes, tasks groups entitled with special duties and groups that evaluate the performance of piping systems and offer recommendations on their installation and usage.
Slurry
Slurry is a fluid that consists of an aqueous suspension. Slurry can be transported through standardized pipes from one location to another for industrial use. Slurry is used in a variety of applications. One such critical area where slurry is used is in the power industry for ensuring these industries operate in an efficient and clean environment. Power industries have to efficiently dispose of ash and other products that result from their activities in an environmentally friendly manner. This approach ensures that land can be reused again and again. Typical characteristics of sludge vary from industry to industry and requirement for their disposal also follow suit.
The B31.11 code specific piping can be used in coal mining activities particularly in pond excavations, dewatering mines, desluddging mines, and in backfilling mines.
The use of sludge as waste disposal mechanism comes with a variety of advantages. Among these include significant amount of energy savings, waste transportation in small volumes. Significant savings on costs are experienced by companies piping systems in the transportation of slurry. Preservation of existing lands and deposits remain stable for long periods of time.
Ecological advantages of disposing slurry through this system ensure minimum ecological contaminations, better rehabilitations, and minimal water consumption or usage.
Where they are used
B31.11 pipes can be used for above the ground or underground piping. Each of these pipes comes with their specification requirements. B31.11 pipes used in pressure transmission piping typically includes areas such as power generation plants. In these power plants, high pressures and temperatures are experienced by these plants that require standardized piping systems. Geothermal heating systems are another area where these standardized pipes are used. These pipes are used for the piping or transportation of metallic or non metallic materials. Other areas include the transportation of aqueous substances, in power regulating stations, and pressure piping regulations. However this does not include the transportation of water, gases, fuels, and air or steam.
Materials for above ground pipes
Two basic characteristics help determine the properties for above ground materials. One of these factors is the wide range of fluids they transport. In addition to that, these materials are subject to varying temperature ranges over different periods of time. This leads to a wider selection of materials for piping systems (Michalopoulos & Babka, 2000). These materials are classified by ASME standards or ASTM standards.
However the criteria for classifying these materials are the same for both standards. They are classified into AS and SB categories. Basically these materials are differentiated by using these letters though they are basically the same for both standards. Slurry piping materials constitute ¼ Chrome Carbide ¼ with carbon steel. They possess the structural strengths and appropriate properties to withstand the forces and chemical processes such as corrosion taking place in this environment.
Properties
Above ground pipes should be characterized by corrosion resistance particularly due to atmospheric chemical actions. In addition to that, they should have high resistance to shock, high ductility and to a specific extent malleable to accommodate flexibility arising from twists that occur above the ground (CHECK AT THE APPENDIX).
Above ground pipes
A wide range of technical requirements are specified for above the ground pipes. These are used to identify specific materials for specific applications in addition to an appendix that is used to approve new materials that are consistent with B31.11 code. Michalopoulos and Babka (2000) argue further that the code explains the mechanical properties, chemical compositions, and tensile strengths of these materials.
Buried materials
Buried pipes, usually made of carbon steel carry smaller volumes of sludge compared with above the ground pipes. The yield strength for these pipes varies between a minimum of 42,000 units and a maximum of 80,000 units. The thickness of these pipes is determined by the length or distance they cover in the transportation of these materials (Masters, n.d). These pipes are designed from high tensile materials and have a cost disadvantage over ductile materials. However, ductile materials are likely to break compared to tensile materials when used on long distance transportation lines.
However, the cost outdoes the disadvantage. B31.11 emphasizes on API 5 L pipes which have clear specifications for toughness. However, this code does not specifically deal with impact testing. These tests are covered by B31.11 specifications.
The allowable stresses for B31.11 buried piping are based on minimum yield strength values. In addition, the allowable minimum temperature reduction factor is always above 1. The effect of this value does not influence the resulting calculations. In addition to that, the thicknesses for these pipes are nominal with respect to pressure effects. B31.11 provides the lower and upper tensile limits for these materials, yielding values, minimum and maximum creep values, and minimum and maximum stress raptures for these pipes. The calculated minimum thickness values for these B31.11 pipes are 0.245 min.
Each of the pipes used has different technical requirements specific to the specific area of application. These areas can be farmlands or wastelands, sparsely or densely populated areas, and traffic utilities. The flowing table provides a summary of categories where different pipes characterized by different design factors are used in terms of location and class.
Other tests done on these pipes include vertical earth load tests. This is more important to consider when designing pipes used at rail or road crossings. The trenching, soil friction, backfill, and soils cohesion are used to determine the loading on these pipes hence the design factors. Other test and design considerations include deflection test and surface live loads. Live loads can be used to determine the pressure transferred to pipes currying slurry appropriate load concentrations on the pipes. Ovality tests that include crushing of the walls, ring buckling, fatigue. Surface impact tests are done to determine the behavior of these materials when a significant load is dropped on these pipes. Figures are tabulated below against which strengths for these materials are compared.
In addition that burred materials can be tested based on the classification of soils and the corrosion effects on different soils.
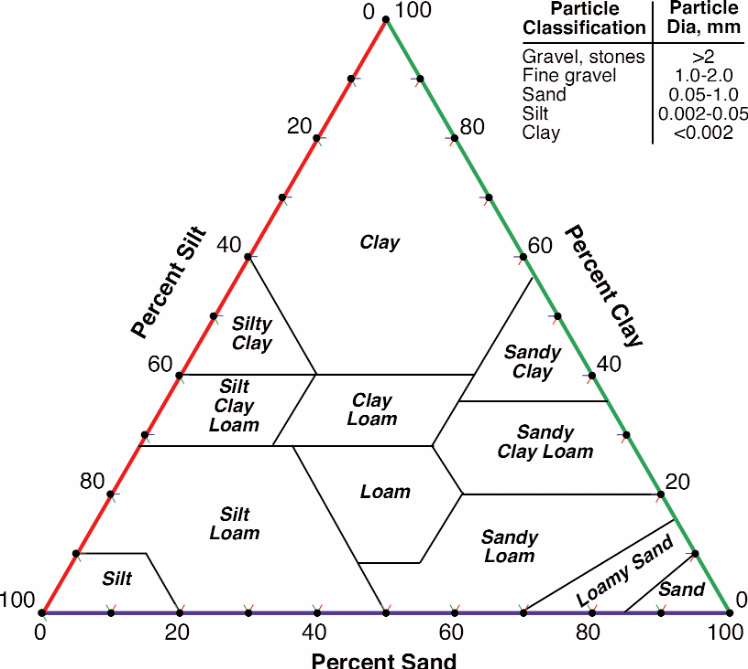
This analysis is also based on the facts that ground water contains organic substance, gases, various minerals, and some soluble salts. These elements have the corrosive effects on these pipes. Thus, they should be treated appropriately by determining their usage and location where they to be used to identify the best chemical compositions for them.
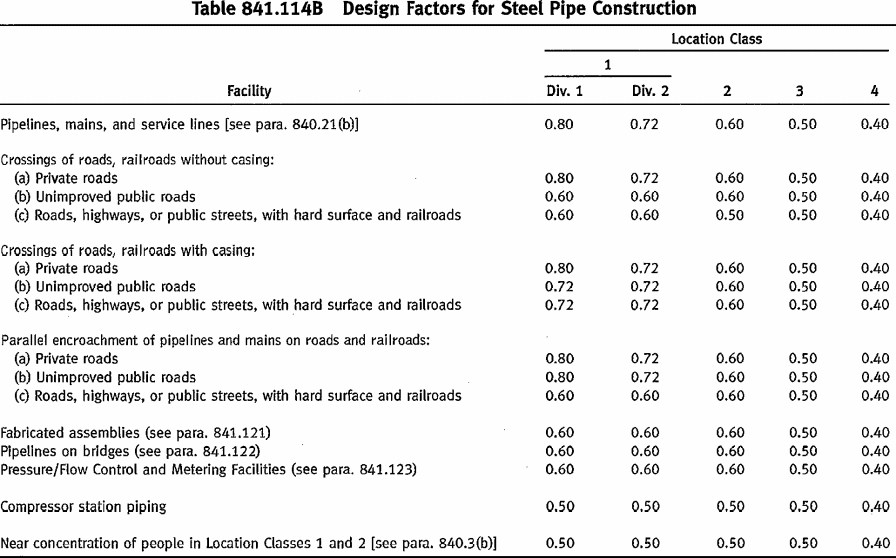
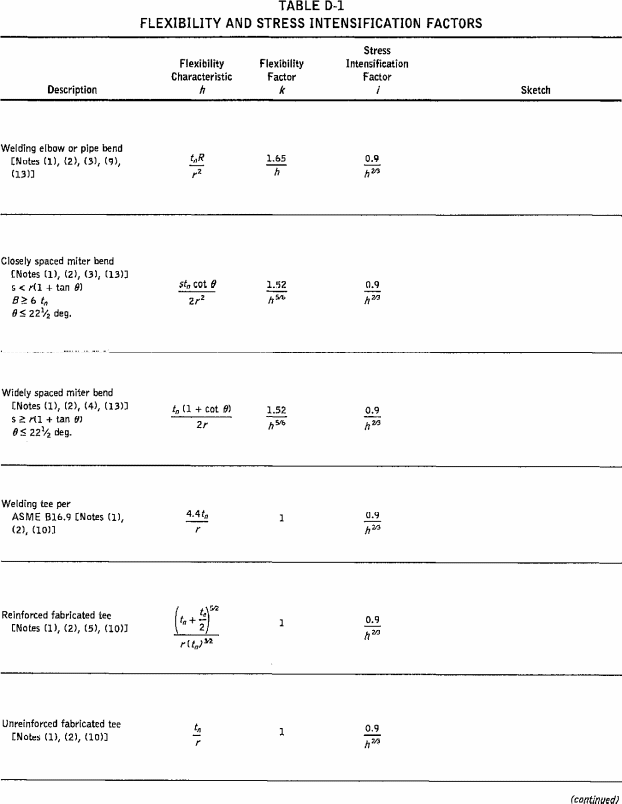
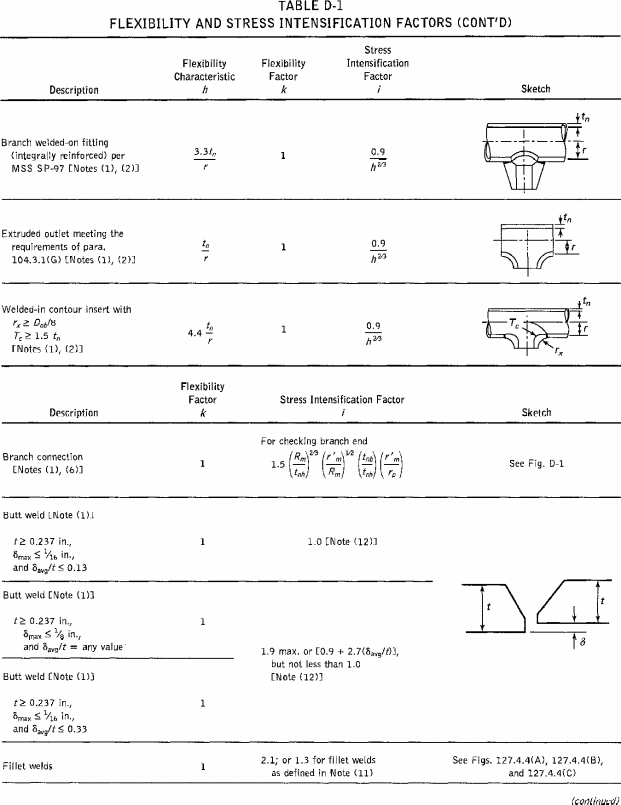
In the design and testing of B31.11 pipes, stress factors are calculated to determine the yielding and their applications points for these pipes.
A variety of tests are done on these pipes to determine the target pressure, actual tensile strengths, thickness requirements, and specific diameter for specific applications.
Ellenberger (2005) provides detailed design specifications for and specific properties for different materials are analyzed to identify the best materials for different load, pressure, temperature and other operating conditions. One of these properties is brittleness. Brittle materials show a tendency to undesirably fail when operating under stress at low temperatures which they can withstand when subjected to similar amounts of stress at higher temperatures. Different engineering materials show different charpy effects when subjected to stress at different temperatures. In addition to that, different fluids exhibit different behaviors under different conditions. The above tests include impact and toughness tests to identify the behavior of these materials under impact and straining forces.
Materials and their usage
Seamless carbon steel is used for pipes whose descriptions on the ASM standards include A 106 Gr B, APL pipe type GrB and fittings. In addition to that, nipples are made of this type of carbon steel. Piping systems are made of this carbon steel. The NPS range for these pipes vary from.75 to 12. Fittings and flanges are made of forged carbon steel. On the other hand, gaskets and bolts are made of low alloy steels that meet the temperature and tensile requirements for materials operating under these conditions (Ellenberger, 2005).
Chemical compositions
Chemical compositions for these materials determine their application areas. A heat and cast analysis shows percentage variations for different material. For carbon, the variations are.19 and.26 percent, Manganese is 1.65 percent. For phosphorus it is.40 percent, and nitrogen with a maximum of 0.03 percent. Alloying enhances machineability and other properties (Kiefner & Vieth, 1989).
One example is the application of NS S31803 alloy for the construction of ASME B31.11 standardized pipes. Chemical compositions for this material are chromium and molybdemium. These pipes are used when longitudinal tests, pressure tests, and corrosion tests are outlined in the B31.11 standards manual have been done (Ellenberger, 2005)
Typical stress analysis
When designing and developing these pipes, pressure and temperature conditions should be factored when making calculations. The design allows material temperatures of up to 250 degrees F. This is provided for by the B31.11 code.
Stress analysis includes areas such as jacket piping, all vacuum sealing lines, all points that are always stationary, all relief points, piping and points that are non metallic, all lines that are subjected to stress and different tensile forces, and all lines that lie on racks.
Different materials have different stress patterns. The basis for evaluating the stress patterns includes thorough examination of their tensile strengths, the lower and upper yielding points, their creep values, and minimum and maximum rapture values. However materials characterized by similar stress-strain behaviors can be evaluated on a different criterion. Allowable temperatures vary with the chemical composition and different behavior patterns of these pipes to pressure and temperature changes. Some chemicals become more corrosive with varying temperature and pressure changes.
Fracture criterions
Fracture is necessary for this code. All materials operate under different mechanical forces that tend to fracture these pipes. Standard requirements outline appropriate mechanical properties in the design of these pipes to resist the effects of such forces.
Besides that, fracture criterion is necessary for this code particular when these pipes are used systems that operate at different temperatures as discussed above. Different materials behave differently under different temperatures and pressures (Cosham & Hopkins, 2004).
Maintenance
Ellenberger (2005) provides detailed examination, maintenance and corrosion evaluation procedures for B31.11 for both above the ground and underground pipes. Corrosion control entails appropriate preparation of the surface of these materials to mitigate the effects of corrosion in identifying appropriate coating materials with sufficient adhesive properties. Coating materials should have excellent ductility properties to resist cracking from tensile forces (Cosham & Hopkins, 2004).
External corrosion control maintenance requirements demand visual inspections for pipe coatings. These inspections help identify bare spots and other general damages on these pipes. Internal corrosion controls entail using appropriate materials that meet the standard requirements outlined in the B31.11 code. To evaluate a system for corrosion maintenance, testing include ultrasound, visual and radiographic techniques.
Once defects have been detected in the piping system, modifications can be done based on documented data yielded from tests done by each company. Replacement and maintenance requirements are specifications are found outlined in the B31.11 standard. These can be accessed from the American Society of Engineers Association (ASME) upon a payment of a fee prescribed by the organization.
Problems, concerns, and limitations of the code
Klemm (1999) asserts that it is difficult to identify genuine manufacturers and distinguish standardized pipes from those without standardization marks. In addition to this, inspection costs are high. Standards specified by this code are not universal.
Metallic pipes
According to B31.11 code, the 105.2.1 requirement specifies that ferrous pipes are not applicable in transporting flammable materials or toxic fluids due to their chemical compositions, tensile strengths and corrosion. However, the requirement considers cast iron to be fit for the manufacture of pressure vessels and pipes as specified in the B31.11 code.
Nonferrous materials
These include pipes made from copper and lead and their alloys. They can be used in transporting water and steam operating at pressures lower than 1750 kilopascal and a temperature less than 208 degree centigrade (George, 1990). Pipes made of alloys of copper can be used as admissible but cannot carry combustible flammable fluids.
Alternatives
These are nonmetallic and can be used to carry water and other fluids but must operate within the manufacture’s specifications. These include reinforced thermoset plastics, reinforced concrete pipes, and polythene pipes. Different operating temperatures and pressures are recommended for these pipes by different manufactures.
The chemical compositions of materials used for different pipes under the B31.11 code are detailed below.
Above tabulations provides testing benchmarks for different materials with different chemical and mechanical properties. A detailed comparison of tensile strengths and hardness conversions are also provided.
Conclusions
The B31.11 standard remains an ideal nomenclature for piping systems despite the limitations and cost overheads associated with adopting standards outlined in this code in industry. This could ensure minimum safety standards are adhered to by ensuring standard construction, installation and testing procedures are carefully followed. However, there is urgent need to enforce these standards through legal systems to ensure conformance to help improve environmental protection and safety standards for people working on slurry piping systems. Different tests need to be conducted on a continuous basis to evaluate compliance to safety standards for slurry piping systems.
These include impact test, ovality tests, penetration tests, hardness tests, buoyancy tests, and thermal stresses among others. Disastrous can be detected long before hand and the occurrence of disasters minimized like the recent deaths experienced at an oils rig off the coast of Mexico.
References
Cosham, A., & Hopkins, P., 2004. An Overview of the Pipeline Defect Assessment Manual (PDAM). 4th International Pipeline Technology Conference, Oostende: Belgium. Web.
Ellenberger, J.P., 2005. Piping Systems & Pipeline. ASME code simplified. McGraw- Hill: New York.
George, K. 1990 Steels: Heat Treatment and Processing Principles. ASM International, Materials Par: Ohio.
Kiefner, J.F. Vieth, P.H., 1989. A modified Criterions for Evaluating the Strength of Corroded Pipe, Final Report for Project PR 3-805 to the Pipeline Supervisory Committee of the American Gas Association, Battelle: Ohio.
Klemm, R. E.,1999. Abrasion Resistant Steel Piping Systems for Slurry Transport in Mining Applications. Ultra Tech: Port Washington. Web.
Michalopoulos, E. & Babka, S.,2000. Evaluation of Pipeline Design Factors. Task Report. One State Street Hartford. Web.
Moles, M & Zhang, J. 2008. Curved arrays for improved horizontal sizing in small pipe welds, Insight, British Institute of non-destructive testing.50( 5) P. 1.
Appendix
Chemical properties table.
Operating Parameters
Physical Properties
Relative Abrasion Resistance (Wet Sand Test)