Introduction
Graphene as 2D one atom thick sheet has excellent electrical and mechanical properties but scale production of Graphene in this format remains a major challenge. Researchers have concentrated instead on the fabrication of graphene like materials such as reduced graphene oxide and COG to maintain the outstanding properties of graphene at large production scale. The study was focused on the characterisation of COG/Latex & COG/BN.
Objectives and Aims
The purpose of this research is to explore and exploit of the properties of carbon-based nanoparticles such as graphene and conductivity- optimised graphite (COG); namely their temperature deponent electrical conductivity, thermal and mechanical properties in applications in the field of latex composites/ boron nitride (BN) hybrid. In addition, to make the characterisation of BN exfoliation to prepare the hybrid with COG. Composites/ hybrid provide a crucial route to transforming these nanomaterials into nanocomposites/ nanohybrid that can be used for applications such as temperature sensors. The main study aims are as follows:
- To produce a highly conductive COG-latex based thin film nanocomposite.
- To understand the interaction mechanism between the COG – Latex polymer matrices through an aqueous medium.
- To explore the thermoelectric properties as a function of different load of COG – Latex composites.
- To develop BN exfoliation.
- To produce nanohybrid of COG and BN.
- To examine the conductivity, and strain sensor thermoelectric properties of COG and BN nanohybrid.
Literature Review
Graphene
Graphene is a two-dimensional allotropic modification of carbon, formed by a layer of carbon atoms one atom thick. Graphene has excellent rigidity, thermal conductivity, and charge mobility, making it a promising material for use in a wide variety of applications, especially in nanoelectronics. The charge carriers in graphene behave like relativistic particles with zero effective mass, making it possible to create devices operating at terahertz frequencies, which, for example, are unavailable to silicon. The use of a set of properties and their optimisation and control are in demand and are currently being studied in detail by scientists worldwide.
Obtaining high-performance materials based on graphene is achieved in various ways, tailored to specific goals and technical tasks. Liquid phase separation, a typical manufacturing process, has several disadvantages. Water-based manufacturing processes have been proposed to achieve better properties, including exfoliation steps, inkjet optimisation, and material hybridisation with polyvinyl alcohol. These methods aim to improve the conductivity of materials, thermoelectric power, and the Seebeck coefficient, which reflects the magnitude of the induced voltage in response to a temperature difference. The essence of thermoelectricity in this case is to create an electric potential due to the temperature difference in a liquid conductor. Each of the presented approaches is of great practical importance.
For example, the quality of graphene nanosheets is critical in producing high-frequency radio antennas and thermoelectric applications such as generating energy from device body heat. The conductivity is influenced by the lateral dimension of the resulting sheets and the choice of starting graphite material. At the same time, the optimized materials have better conductivity values even with fewer layers of nano sheets. The production of such substances is shown in Figure 1. The ink material in nanosheet inkjet printing and the use of a hybrid substance also increase the heat transfer performance, achieved by controlling the ingredients in the form of polymer additives or alcohols. In addition, these methods are pretty simple in production and scaling, which makes it possible to adapt them in many application areas.
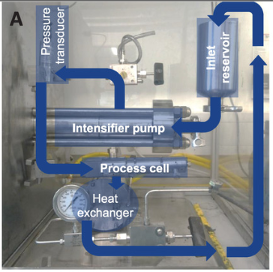
Latex
Latex is an aqueous solution of dispersed particles of polymer emulsions containing salts, proteins, and rubber. The resulting particles result from colloidal dispersion, where active chemical additives, such as plasticizers and rheological modifiers, achieve essential properties that distinguish the latex film from other substances. The film is formed during the transformation of an aqueous dispersion of particles into a continuous material, the properties of which, among other things, depend on the minimum film formation temperature.
The formation of the material is subject to external and internal factors such as environmental conditions, the complex of active additives, and the original structure of the latex particles. The constant development of methods for synthesizing compositions leads to a wide field of study of the causes of particle deformation.
The classic process, from a stable dispersion of colloidal polymer particles into a continuous film, is called latex film formation. It involves several steps, from a dilute to a concentrated dispersion, into a full array of particles to a continuous polymer film, as shown in Figure 2.
In the first stage, which corresponds to the initial wet stage, the distance between the particles is reduced due to surface tension and capillary forces, and the concentration increases until a dense packing of spheres is achieved. In the second stage, the particles start deforming, and this part is essential for film formation.
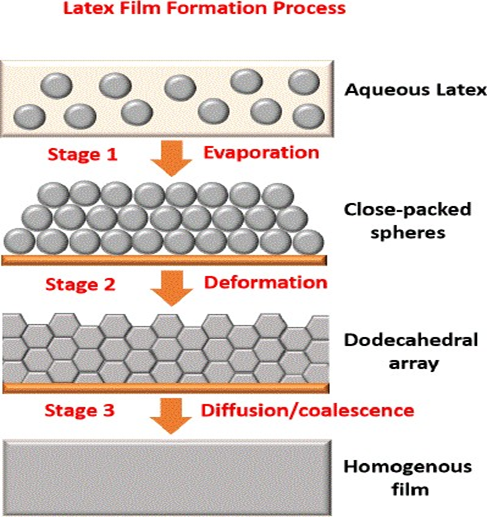
Optimisation processes can be applied at various stages of the formation of a solid material. For example, controlling the assembly of nanoparticles can help obtain materials with high optical conductivity. The most popular methods for controlling these stages in the course of technological progress are direct nonradiative energy transfer or atomic force microscopy. However, there is still a huge potential to control the formation of latex structures through experiments with the composition of the polymer composition or control of the conditions accompanying each stage, which is dictated by the wide use of the material in various human applications.
Exfoliation of BN
Many applications of boron nitride require exfoliation of the BN in various fluids in order to take advantage of the chemical properties of the BN. This material has high thermal conductivity and flatness, as well as an important set of optical, electrical and mechanical characteristics, which makes it popular in nuclear energy, oil industry and other areas.
Methods for Exfoliating Liquid Phase of Boron Nitride (BN)
There are many methods for exfoliating the liquid phase of BN. The first is solvent stabilisation, which uses the model of the Hildebrand and Hansen parameters to describe the miscibility of an element. General approaches in this group can be classified into three subgroups: covalent, non-covalent and alternating.
Secondly, surfactant stabilisation is applied, described by the DLVO theory. In such cases, as a rule, electrostatic repulsion and attraction are evaluated, which are described by the degree of overlapping of double layers and van der Waals forces, respectively – high stability is described by low values of the zeta potential.
Finally, a huge number of exfoliation approaches are distinguished, including chemical peeling with NaOH or KOH, intercalation complexes, ultrasonic treatment, mechanical splitting, thermal peeling, controlled gas, quadrupole field or laser-plasma peeling. An analysis of the structure of such materials is also often described by the percolation theory: when the percolation threshold is reached, the filler concentration is reached, for example, in the nonconductive matrix of the BN nanosheet. Therefore, depending on the goal, approach, and available resources, a variety of boron nitride exfoliation methods are allocated.
There are several modifications of this substance, which have different compositions and, as a result, different technical and operational characteristics; however, all of them are actively used in such areas as vacuum and semiconductor instrumentation, the creation of high-temperature lubricants, electrical and thermal insulators, as well as the synthesis of superhard substances. Boron nitride nanosheets are studied by various methods to optimize and control properties, but the spectroscopic analysis is most often distinguished.
The constancy of Raman scattering, which does not depend on the size of the nanomaterial, is used to estimate the thickness of the layers of the resulting composition. The process of nanotube exfoliation can be studied using the methods of ultracentrifuged and dilute dispersions of single-walled tubes, and the quality of the material can vary significantly, depending on the method chosen. The unique complex of properties and methods of exfoliation with different results gives a wide scope for the study of hBN and its application in various fields of human activity.
Graphene Hybrid with BN
Graphene and boron nitride have similar structures but are opposed in characteristics. Despite this, their everyday use in hybridisation allows access to various features of the synthesized materials. For example, using the exfoliation method and a mixture of acids as a catalyst, it is possible to obtain a hybrid substance of graphite with boron nitrite, the nanosheets of which will form the structure of this material.
At the same time, the mechanical properties, including the fracture strain and tensile strength, increase significantly compared with the initial substances. The electrical component of the union of a dielectric and a metal with high conductivity changes as the band gap of graphene opens. Thermodynamic abilities also expand the possible characteristics, including thermal stability: new materials can withstand up to 8000 kelvin. Accordingly, this material has vast potential but a relatively complex production process.
Technical applications of graphene hybirds with BN often require delamination to reach the liquid phase. The process is typically described as dispersing, stabilizing, and controlling properties with surfactant additives. Researchers evaluate suitable solvents for graphene as the basis of nanomaterial using the Hildebrant and Hansen solubility indices. The optimized values are 23 MPa1/2 and 7.7-18 MPa1/2, respectively. For these coefficients, the unit of measurement is calories per cubic centimeter to the power of ½, which is equivalent to pascals to the same power when converted through Joules.
The process of self-dissolution is often considered when substances with a surface tension close to the surface tension of graphite are used, for example, N-methyl pyrrolidone. Processing methods at high concentrations include ultrasound and centrifugation to obtain stable substances with multiple nanolayers.
In addition to external influence, an important role is played by choice of a solvent whose nature can be stabilizing or vice versa: NMP or water are used as examples, respectively. Graphene is also used in combination with nanotubes and MoS2 nanosheets, however, the field of application of these substances is different. The quality and properties of the obtained nanosheets of the material depend on the solution; however, the storage performance and the possibility of transportation are generally improved.
Experimental Section
COG/ Latex
Three steps required to fabricate COG – Latex nanocomposites films. In the first step both the COG and Latex used underwent preparation were diluted with DI Water and mixed in different mass fraction as follows (0.2, 0.4, 0.6, 0.8, 0.85, 0.9, 0.95) mg/mL as showing in Figure 3, A. All mixed dispersions underwent small tip sonication to obtain homogenize dispersions. The second step (Figure 3, B) is the deposition process; here spray deposition was chosen as the preferred method in order to create uniform film with a controlled film thickness measured set to a few micrometers. The spray dispersion was applied to optical glass and sets on a hot plate at 110℃. In the third step, the fabricated films (Figure 3, C) was ready for further electrical and thermoelectric characterisation.
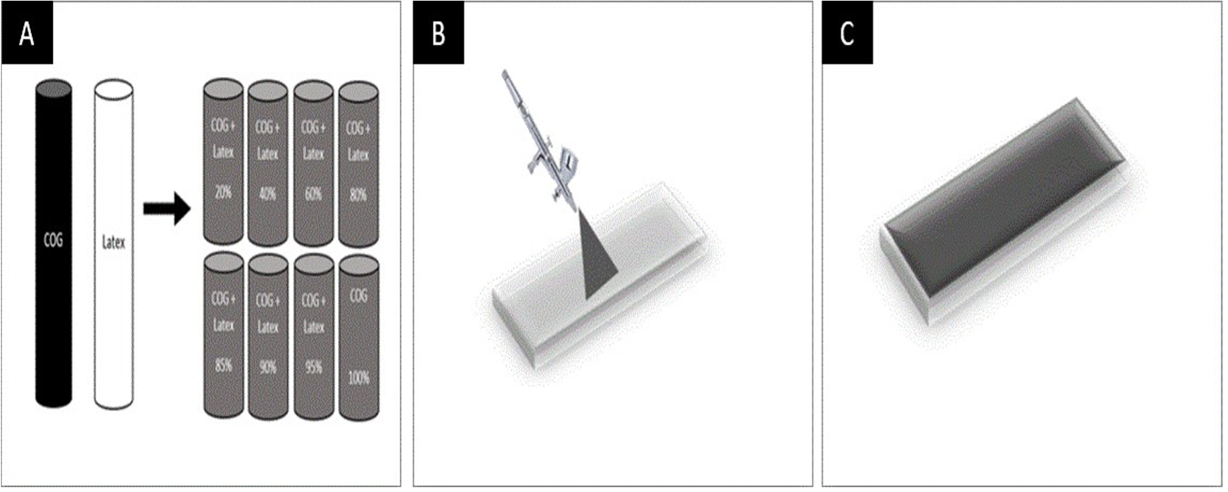
Electrical Conductivity of COG and NRL Nanocomposites
After the fabrication of the COG/Latex composites films, five silver paint electrodes were placed in the film to provide better contact during the electrical conductivity measurement carried out via a two-probe system as described in chapter 3 where the I-V curve was measured through silver electrodes The electrical conductivity can be calculated using Eq. 1.1.
Eq. 1.1: σ = 1 / (t x R)
Here σ is the electrical conductivity in S/m, t is the film thickness and Rs is the sheet resistance. In this experiment T measured using Profilometer while R is measured using millimeter in respect to electrodes geometry ratio and using the slope between measured R and the length-width ratio (L/W) as showing in Eq.1.2.
Eq. 1.2: Slope = R / (L/W)
Figure 4 shows the trend in electrical conductivity vs different mass fraction of COG-Latex from 0.2 mg/mL COG-Latex to pristine COG (1 mg/mL). Measured electrical conductivity gradually increased as COG content introduce to the latex composites. The highest COG-Latex recorded is 19K S/m for 0.95 mg/mL COG-Latex. However, the electrical conductivity of pristine COG reached almost 40K S/m.
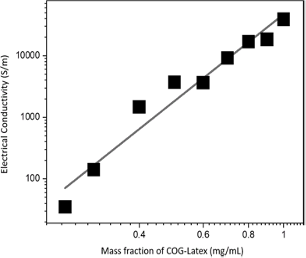
TGA of COG/ Latex
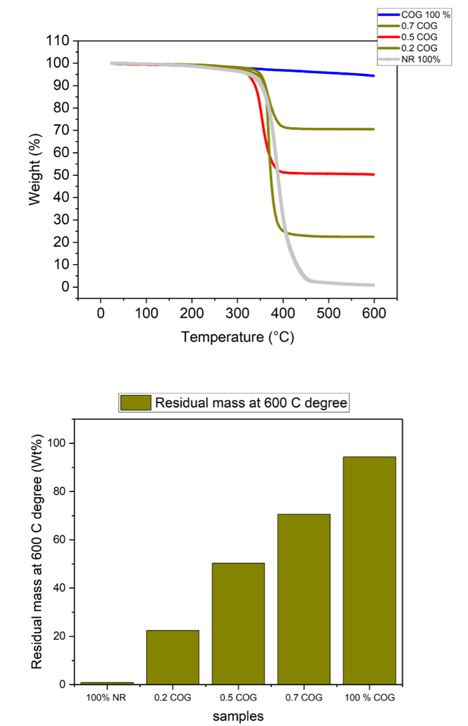
In this Nanocomposite of COG/Latex weight loss varies according to increasing volume of COG. At 400C, the weight lost in the sample comprising of 100% latex was 99,6g while the weight loss in the sample comprising of 100% COG was 0.4g.
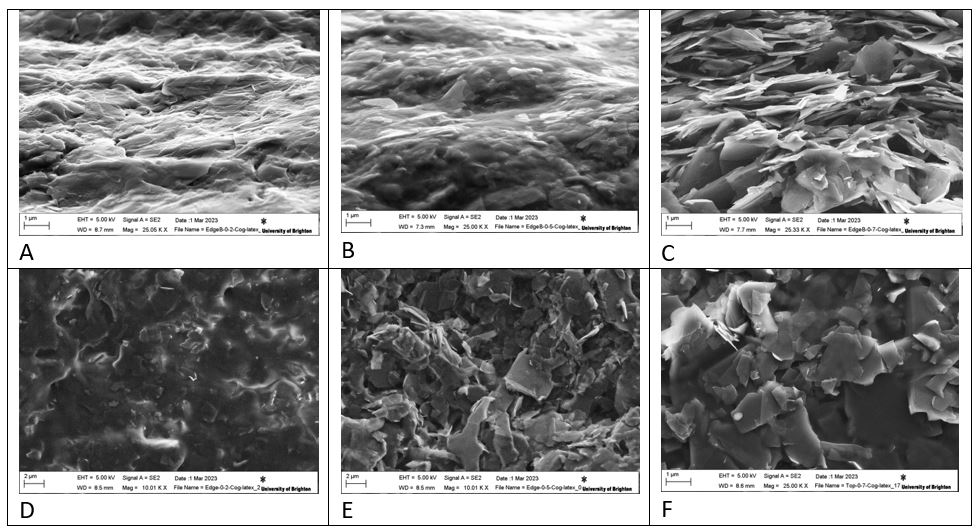
Figure 6 shows the crosse-section morphology A, B, and C characterisation by SEM (Figure 6). D, E and F showed surface morphology which observed: images C&F show more structure of the electrodes of COG/Latex composite film with a COG wt% of 0.7 while it is observed in images A&D electron micrographs of natural rubber in the composite with the decrease of wt% of COG to 0.2. The observation in images B&E that there is no clear visible of COG sheets according to the wt% of COG/latex which is 0.5 & 0.5 of latex.
Electrical Conductivity of COG Nanocomposites
Figure 7 illustrates the measurement of ∆V as a function of ∆T in pristine COG (A), 0.8 mg/mL COG-Latex in (B) and 0.7 mg/mL COG-Latex in (C). These measurements performed as one end of the substrate is heated inducing, a potential difference across the film. In both COG-Latex nanocomposites substrates shows the same behaviour with Seebeck coefficient value at17.25 ∓ 0.17. The pristine COG shows the same trend of ∆V as a function of ∆T but with higher Seebeck coefficient value (24.05 ∓ 0.99). As this measurement still in progress the other mass fraction will be tested and both Seebeck coefficient and power factor values reported later following the way that previous study have done; [14],[10]and [15]. This evaluation required in order to correlate the thermoelectrical properties response according to different mass fraction of COG-Latex nanocomposites.
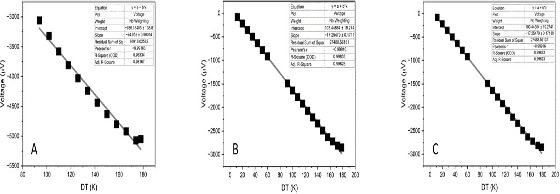
Exfoliated of BN
An experiment using Sodium cholate hydrate (Na3 C6H5O7) in solution with different weight percentages of the solution vs, deionised water was repeated five times and results are shown in the table below.
Three steps were taken to exfoliate BN. In the first step, BN powder was mixed with five different weight presentation of the surfactant NaCho (0.1,0.5,1,2,3.5) mg/ml. in step two, all mixed dispersion underwent large tip sonication to exfoliate homogenised BN for five hours. During the third step all the five different concentrations went into the centrifuge under two different g forces: firstly, 200 g force for 20mins and secondly, 5000g force for 30mins.
Figures 8-10 illustrate steps two & three of this process.
Step Two: Tip Sonication
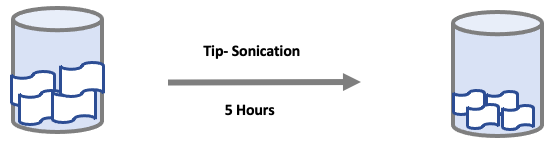
Step Three (1): Centrifugation @ 200g * 20 Minutes.
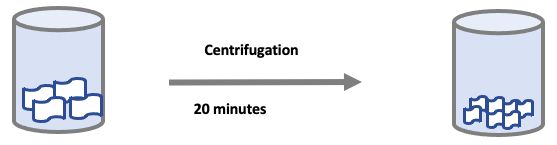
Step Three (2): Centrifugation @ 5000g * 30 Minutes
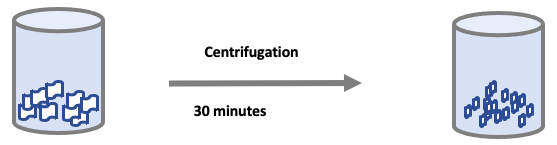
These steps ultimately produced the five different concentrations illustrated in Figure 11.
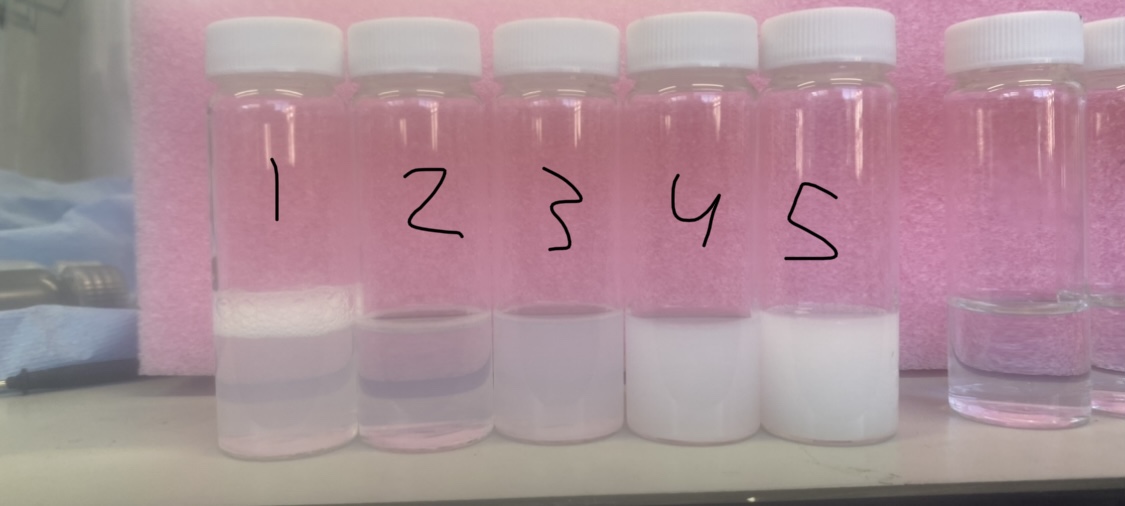
The Results
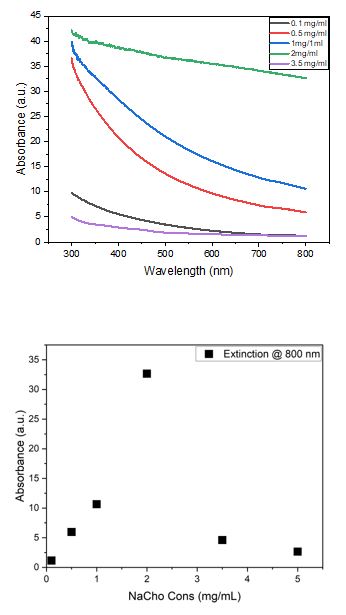
The results of these experiments with BN were evaluated in terms of the concentration, measured through UV-visible extinction spectroscopy. As a function of wavelength, UV can measure the concentration of BN by applying wavelengths of 800 nm. The results show that “Sodium cholate hydrate” (NaCho) solution can exfoliate BN more efficiently with 8g of solution + 12g of deionised water “2mg/ml” as shown in Figure 11.Figure 13 shows the size distribution of the high concentration 2mg/ml.
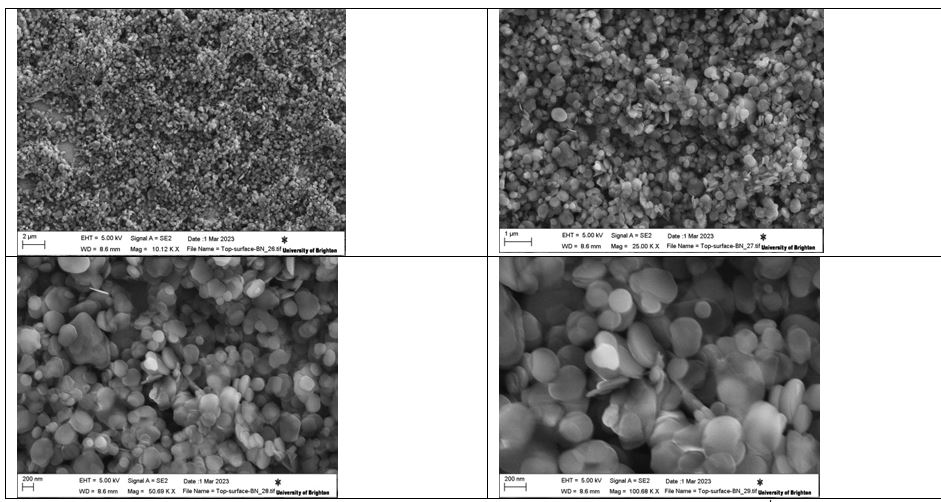
Graphene Hybrid with BN
Two steps were undertaken to fabricate COG – BN nanohybrid films. In the first step, both COG and BN were prepared and blended using speed mixer “ FlackTek” with different mass fractions of COG (0.1, 0.2, 0.3, 0.4, 0.5,0.6,0.7,0.8,0.9,1). All mixed pastes underwent different FlackTek speed cycles to obtain- homogenised pastes of COG/BN. In the second step, the nanohybrid of COG/BN is printed in the substrate of glass as shown in Figure 14. This measurement process is ongoing and will eventually include the remaining mass fraction (0.6,0.7,0.8,0.9) of COG not illustrated below.
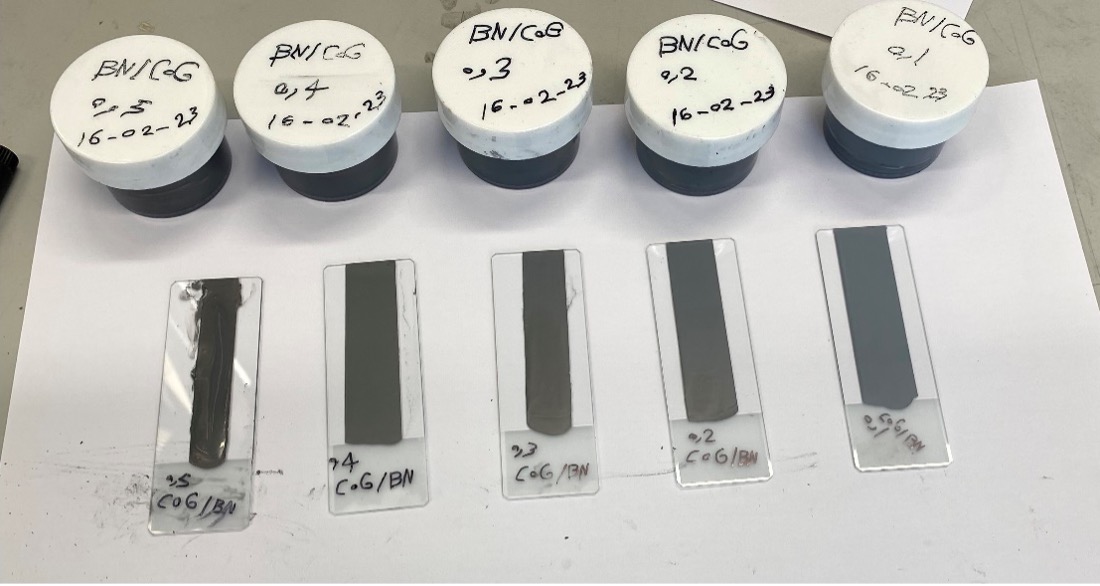
Conclusion
In conclusion, a nanocomposite of 2D material such as COG/latex can maintain the same conductivity with carcinisation of the composite. Nanocomposites and Nanohybrids can be deployed in high potential applications in, for example, high performance- transistors, electrical , and mechanical systems. This study presents the conductivity behaviour of nanocomposite of COG/latex and proposes to map the behaviour of the mechanical properties. In addition, the study has demonstrated the use of BN exfoliation to find the high concentration, @ 2mg/ml of the surfactant Nacho. BN is selected as the preferred hybrid with COG as it acquires potentially greater importance in some applications. The conductivity, mechanical, and electrical properties of hybrid COG with BN will be further tested as this study progresses.
References
Barwich, S., Khan, U., & Coleman, J. N. (2013). A technique to pretreat graphite which allows the rapid dispersion of defect-free graphene in solvents at high concentration. The Journal of Physical Chemistry C, 117(37), 19212-19218. Web.
Bergin, S. D., Nicolosi, V., Streich, P. V., Giordani, S., Sun, Z., Windle, A. H. & Coleman, J. N. (2008). Towards solutions of single‐walled carbon nanotubes in common solvents. Advanced Materials, 20(10), 1876-1881. Web.
Cathcart, H., & Coleman, J. N. (2009). Quantitative comparison of ultracentrifuged and diluted single walled nanotube dispersions; differences in dispersion quality. Chemical Physics Letters, 474(1-3), 122-126. Web.
Coleman, J. N. (2009). Liquid‐phase exfoliation of nanotubes and graphene. Advanced Functional Materials, 19(23), 3680-3695. Web.
Eshkalak, K. E., Sadeghzadeh, S., & Jalaly, M. (2018). The mechanical design of hybrid graphene/boron nitride nanotransistors: geometry and interface effects. Solid State Communications, 270, 82-86. Web.
Griffin, A., Harvey, A., Cunningham, B., Scullion, D., Tian, T., Shih, C. J. & Coleman, J. N. (2018). Spectroscopic size and thickness metrics for liquid-exfoliated h-BN. Chemistry of Materials, 30(6), 1998-2005. Web.
Güler, Ö., & Güler, S. H. (2016). Production of graphene–boron nitride hybrid nanosheets by liquid-phase exfoliation. Optik, 127(11), 4630-4634. Web.
Lisuzzo, L., Cavallaro, G., Lazzara, G., Milioto, S., Parisi, F., & Stetsyshyn, Y. (2018). Stability of halloysite, imogolite, and boron nitride nanotubes in solvent media. Applied Sciences, 8(7), 1068. Web.
Joni, I. M., Balgis, R., Ogi, T., Iwaki, T., & Okuyama, K. (2011). Surface functionalization for dispersing and stabilizing hexagonal boron nitride nanoparticle by bead milling. Colloids and Surfaces A: Physicochemical and Engineering Aspects, 388(1-3), 49-58. Web.
Gautam, C., & Chelliah, S. (2021). Methods of hexagonal boron nitride exfoliation and its functionalization: covalent and non-covalent approaches. Rsc Advances, 11(50), 31284-31327. Web.
Garcia, J. R., McCrystal, M., Horváth, D., Kaur, H., Carey, T., & Coleman, J. N. (2023). Tuneable Piezoresistance of Graphene‐Based 2D: 2D Nanocomposite Networks. Advanced Functional Materials, 2214855. Web.
Hernandez, Y., Lotya, M., Rickard, D., Bergin, S. D., & Coleman, J. N. (2010). Measurement of multicomponent solubility parameters for graphene facilitates solvent discovery. Langmuir, 26(5), 3208-3213. Web.
Jiang, H., Yu, K., & Wang, Y. (2007). Antireflective structures via spin casting of polymer latex. Optics Letters, 32(5), 575-577. Web.
Juntunen, T., Jussila, H., Ruoho, M., Liu, S., Hu, G., Albrow‐Owen, T. & Tittonen, I. (2018). Inkjet printed large‐area flexible few‐layer graphene thermoelectrics. Advanced Functional Materials, 28(22), 1800480. Web.
Keddie, J. L. (1997). Film formation of latex. Materials Science and Engineering: R: Reports, 21(3), 101-170. Web.
Keddie, J. L., Routh, A. F., Keddie, J. L., & Routh, A. F. (2010). An introduction to latex and the principles of colloidal stability. Fundamentals of Latex Film Formation: Processes and Properties, 1-26. Web.
Khan, U., Porwal, H., O’Neill, A., Nawaz, K., May, P., & Coleman, J. N. (2011). Solvent-exfoliated graphene at extremely high concentration. Langmuir, 27(15), 9077-9082. Web.
Large, M. J., Ogilvie, S. P., Amorim Graf, A., Lynch, P. J., O’Mara, M. A., Waters, T. & Dalton, A. B. (2020). Large‐Scale Surfactant Exfoliation of Graphene and Conductivity‐Optimized Graphite Enabling Wireless Connectivity. Advanced Materials Technologies, 5(7). Web.
Mahmoud, L., Abdul Samad, Y., Alhawari, M., Mohammad, B., Liao, K., & Ismail, M. (2015). Combination of PVA with graphene to improve the seebeck coefficient for thermoelectric generator applications. Journal of Electronic Materials, 44, 420-424. Web.
May, P., Khan, U., Hughes, J. M., & Coleman, J. N. (2012). Role of solubility parameters in understanding the steric stabilization of exfoliated two-dimensional nanosheets by adsorbed polymers. The Journal of Physical Chemistry C, 116(20), 11393-11400. Web.
Nguyen, H. T. (2019). Graphene layer of hybrid graphene/hexagonal boron nitride model upon heating. Carbon Letters, 29(5), 521-528. Web.
Smith, R. J., King, P. J., Lotya, M., Wirtz, C., Khan, U., De, S. & Coleman, J. N. (2011). Large‐scale exfoliation of inorganic layered compounds in aqueous surfactant solutions. Advanced Materials, 23(34), 3944-3948. Web.
Sperry, P. R., Snyder, B. S., O’Dowd, M., & Lesko, P. M. (1994). Role of water in particle deformation and compaction in latex film formation. Langmuir, 10(8), 2619-2628. Web.
Varrla, E., Backes, C., Paton, K. R., Harvey, A., Gholamvand, Z., McCauley, J., & Coleman, J. N. (2015). Large-scale production of size-controlled MoS2 nanosheets by shear exfoliation. Chemistry of Materials, 27(3), 1129-1139. Web.