Executive Summary
This paper focuses on supply chain management in the context of the Dell Company which is one of the leading computer-related technological companies. The research indicated that the company uses a direct model of supply chain management to reach its customers directly. This system enables the company to cut its production cost, cut the inventory and use negative capital. However, the direct model has two critical problems. First, it increases the cost of support services which should be otherwise catered by the retailers. Second, the daily orders from customers are required to be recorded and transferred on a real-time basis hence complications of the process.
To combat these two problems, the paper proposes that the company should undertake validation. As a result of hardware validation and inspection, the company will transfer minimal defects to the customer. This will, therefore, require the customers to seek minimal support from the company and hence the inherent cost will be reduced. Also, the company should ensure RFID enabled and online system to track orders from customers across the globe. The system updates the orders and they are received by the manufacturing floor for assembly to start. This will ensure that the company does not use manual ways of order tracking which can otherwise handicap the process in terms of efficiency and timeliness. The six sigma analysis was also found to have a critical implication on quality improvement. This will ensure that the products’ quality is improved using a DMAIC methodology which is data-driven.
Introduction
About Dell
Dell is a technology invented by Michael Dell and incorporated in America. This company has grown to become one of the largest and leading technology companies with a multinational customer base. Indeed, the company is involved in the development, repairing, and selling of the PC around the world as well as providing customers’ support. Whereas its main focus lies with personal computers, Dell develops and sells other electronics such as servers, cameras, and software among others. As such, it commands a vast customer base both in the USA and other parts of the world. In addition to the extensive customers’ base, the company has employed about 103300 employees around the world. This implies that the logistic process and supply chain system adopted by Dell must be efficient, fast and effective to ensure success.
Supply Chain Management
Supply Chain Management is one of the most fundamental business undertakings (Balakrishnan & Geunes, 2010). It is a process that ensures the delivery of quality services to customers and maintains the sustainability and stability of the business by organizing all undertakings involved when the products leave the company to the customer (Chang & Graham, 2012). Supply chain management involves various players that include the manufacturer/company, the suppliers of the products, transporting system, wholesalers, retail sellers and the customers (Carls, 2011). In principle, Supply Chain Management is meant to improve the value of goods and services to fulfill the needs of the customers since the clients are the most crucial stakeholders of a business. As stated before, Dell is involved in the manufacturing, repairing and supporting of computer-based and PC products. Due to the increasing customer base and the growing employees’ population, the company has noted that its supply chain has become crucial. Importantly, the company has attained a global status that warrants an efficient worldwide supply chain. As such, efficiency is now an important requirement if Dell has to retain its competitive advantage on the fact of the rising competition in the computer industry (Du, 2007). Understandably, a slight ignorance of the supply chain management can facilitate its fast deterioration and eventual insolvency especially when companies such as Apple and HP are exploiting the power of innovation in all areas of business processes including supply chain (Arthur, 2012).
Paper Classification
Bearing in mind the importance of supply chain management when it comes to the solvency and profitability of Dell, this paper seeks to analyze the company’s supply chain. It will first focus on identifying a supply chain system that is similar to the one adopted by Dell. After the identification, a literature review will be undertaken concerning the supply chain to identify its framework, advantages, limitation and then make the necessary recommendations as part of the review’s conclusion. The paper will also focus on the operation of the supply chain system to identify some of the critical logistics involved in the company. Importantly, the paper will touch on some of the critical problems facing the company’s logistics and supply system. In addition to the problems, it will seek to identify some of the capabilities associated with the chain to help in the next category. As such, the next category will involve a re-designing of the company’s logistics process to ensure the reduction of cost and time consumption.
Literature Review
Overview of Other Logistics Systems Close to Dell
Indeed, Dell company uses an essentially similar logistics system to Apple Company since they both use the direct model supply chain. In this system, the companies deliver products to the customers directly rather than involving the retailers and the distributors. In this system, the companies are capable of creating a direct relationship with their clients because of the ordering and delivery is conducted directly. The customers can follow up the transportation and later make queries to the company if any issues arise. The system has segmented the customer base into three distinct segments. These segments include small and medium-sized businesses, large organizations, and individual customers. However, Dell applies a unique additional logistic system that does not appear in Apple. In this case, Dell uses the Build-to-Order system where the customers make their product order and the information is sent to the manufacturing store and the assembly starts immediately (Dura & Isac, 2012)). This approach becomes very effective because the market is more predictable when the customers are allowed to order and the assembly is done.
Framework
Dell’s supply chain system in diagrammatic representations is represented below.
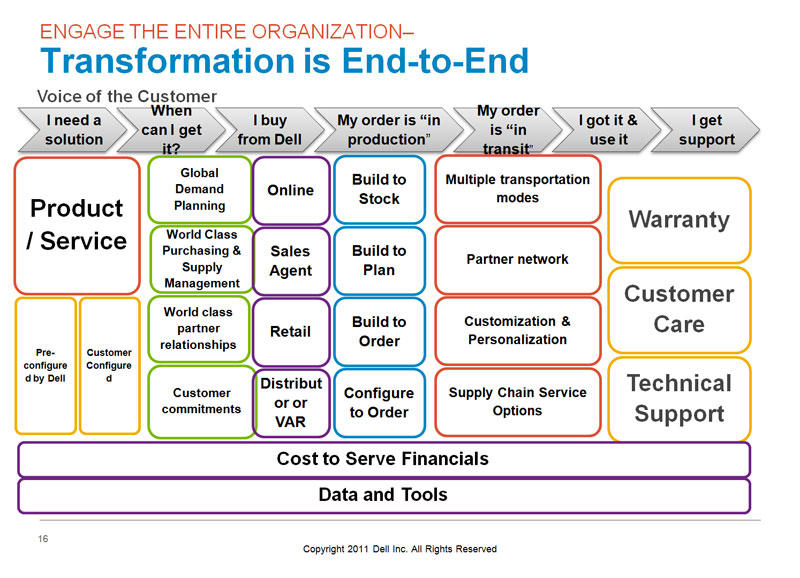
Dell has adopted a direct model supply chain system where customers get products directly from the company. As such, the system has various levels of operations that enable customers to have the best experience. From the diagram above, the customers can either order for a pre-configured product or a customer-configured product. The customer configured product is built in tandem with specifications of the customer provided during the ordering stage. The orders are made directly to the company through the use of online means. During this stage, orders can be done following the Build-to-Stock (BTS), Build-to-Plan (BTP), Build-to-Order (BTO) and Configure-to-Order (CTO). The most applied ordering provisions include BTO and CTO
Apple supply chain framework appears below. BTO enables customers to order the products with their desired features before assembly and shipping is done. The CTO provision requires the company to configure the products in tandem with the customer’s desired performance and capabilities.
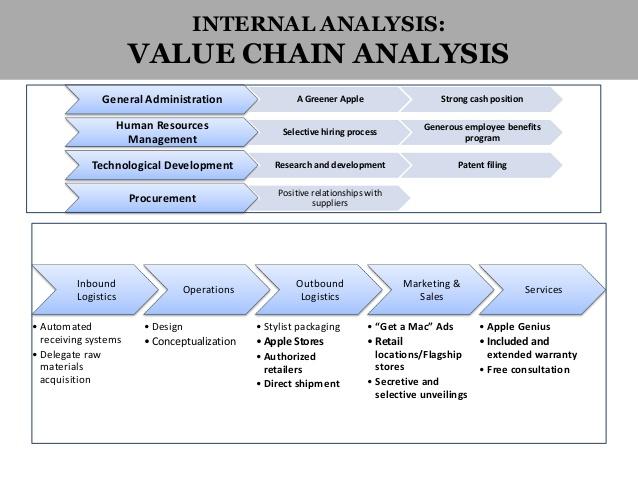
Similarly, Apple applies a direct supply chain model when it comes to the distribution of its products. The automated receiving systems are installed to receive and record customers’ orders from the market. The orders are evaluated later and the design of the product is done following the requirements of the customer. After that, a direct shipment is made to deliver the product to the customer. Alternatively, the customer can get the predesigned product from the Apple stores. Although the company has applied a direct model, it has authorized agents operating in the market to distribute the products. Importantly, the company considers marketing and sales as an important part of their successful business venture considering that the products are of high value. Lastly, they offer services such as the warranties and free consultation to provide the customers with an opportunity to get the required information concerning maintenance.
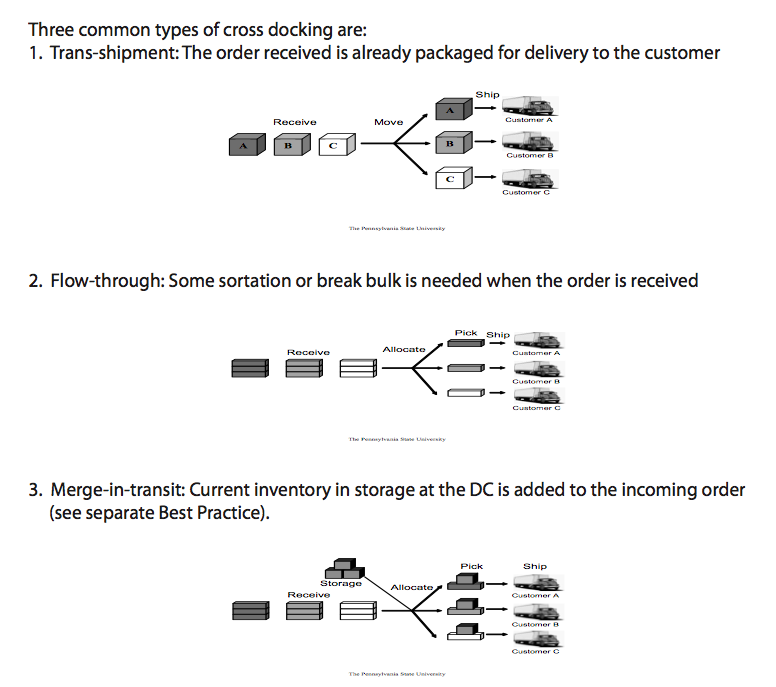
Advantages and Disadvantages
The direct model supply chain is essentially advantageous when it comes to both the operational aspects and the customers’ engagement. First, the direct model enables the company/manufacturer to have a direct relationship with the customers. As a result, the company eliminates retailers who are fond of increasing the price by high margins (Ho & Fan, 2011). Understandably, the increased margins of prices create the impression that Dell sells its products at high prices. However, Dell produces products of essentially high performance at relatively low prices than most of the companies. In this regard, therefore, the elimination of retailers enables the customers to purchase the Dell products at relatively low prices than the ones offered by retailers. In addition to this, the customers get a direct connection with the manufacturer such that their issues can be addressed directly by Dell’s specialists. This plays a fundamental role when it comes to the improvement of quality. Indeed, the customers are also at liberty to provide suggestions and complaints that can form the basis of improving the quality of Dell’s products all over the world. Generally, the system eliminates any fouls that might be caused by retailers (Finch, 2009).
These fouls need to be eliminated to prevent the disparaging of the company’s integrity in the process of the retailers’ pursuit to make a profit. In addition to the direct customer relationship, the system enables the company to collect reliable data on the purchases made. In this case, it is essentially difficult and unreliable to access and use data from the retailers since it might not be accurate. On the other hand, when the customers make the orders and the deliveries are made, the company can project the future to determine the expected sales. Furthermore, the company has integrated a unique feature in its direct model. This feature is known as the Build-To-Order system. The customers are allowed to order the products so that the company starts to manufacturer the product. When the information containing the order details is received, it is sent to the customers’ floor and the assemble starts following the specifications. Once the assembly is over, the products are transported through 3PL. This enables the company to regulate and manage its inventory effectively. The effective management of the inventory is occasioned by the fast responses to demand rather than manufacturing and waiting for the customers to order. Also, the customers pay for the products before the assembly is done. This implies that the customers pay for the products even before the company pays the suppliers. As such, this system enables the running of the business in a financially sustainable manner. The fact that it pays the suppliers after the customers have paid for the products allows it to use negative working capital. Indeed, the company can use a lean production system while using manufacturing as a source of profits even before delivery is made.
However, although the direct model has been identified as one of the most efficient and favorable mechanism when it comes to the manufacturing side. The model is essentially disadvantageous to the provision of support. In this case, the inclusion of resellers in the supply chain enables a company to offload the support cost to them as opposed to a direct model where the service cost goes to the Dell company. In that regard, therefore, it meant that the cost of support can be tragic is it outweighs the money saved by the direct model during production. Dell is facing that threat because it has increased its market share tremendously. This implies that the use of the direct model to reduce the cost of production might be outweighed by the cost of support.
Recommendations and Conclusions
Indeed, the above analysis has presented informative details on the operation of the Dell’s supply chain. Dell uses a direct model where the company delivers its products directly to the customers. As such, the company has direct contact with customers around the world. Indeed, it was indicated that this is very advantageous because it helps the company to cut on the production cost and use negative capital. After all, they pay the suppliers after the customers have paid. However, it evokes a critical problem because, in this model, the company has to incur the support cost. After all, it relates directly to the customers (Kim, 2011). As such, the company should ensure that the support cost remains far below the cost cut by the production process. As a result, the company should work on the following recommendations.
- The support services should be automated so that the customers can get help from online platforms and inbuilt software.
- The company should work to keep the support cost below the cost saved by the production process as a result of using the direct model.
- The company should consider using franchise systems to serve foreign countries. This will help the company to offload some of the support cost to the resellers in the franchising system
- The company should use the retailers when distributing the products to foreign countries because this will further reduce the support price. However, the use of retailers should be used with regulations and restraints to ensure that it just helps to cut the support cost and balance with the cost cut during production.
System Operation and Context
Life Cycle Cost Analysis Indeed, there are various measures that Dell has implemented to ensure that the cost of the life cycle has been reduced. First, the company has implemented the use of the Build-To-Order system (Mendelson & Ziegler, 2009). This system has played a significant role to ensure that the cost of production is reduced significantly. As a result of prior payment, the company pays the suppliers after the customers have paid for their products. This is one of the fundamental changes that Dell has used to ensure there is sustainability in production.
The second technique used by Dell to reduce the cost of the logistics and life cycle is known as the Configure-To-Order system. In this system, the company configures the product according to the needs of the customer. Indeed, this helps to cut the cost of support services required after the products are delivered. Indeed, if customers want to configure their products according to their needs, they require support services from the company. To ensure that the customers do not seek this service and thereby increase the cost of operation, Dell configures the computers upon an order. This implies that the customers will probably become satisfied because the device is already customized.
In addition to BTO and CTO strategies of reducing cost, the company seeks to cut the cost of support by integrating it into the cost of production. In this case, the company uses the Cost of Quality (COQ). The COQ is the cost used to eliminate or reduce the products’ defects which reach the customers’ end (Neto, Fusco & Machado, 2014). In this case, the company seeks to use high-quality supplies to assemble and make resilient products. As such, it ensures that very little defects reach the customers after delivery. As a result, the customers have a very low probability of seeking customer support services from the company. As such, the company is capable of cutting the cost of the operation and life cycle in general.
Life Cycle Cost Analysis
Net Present Value Analysis
Taking revenue as the cash flow for the five years, the net present value of the project the NPV is $91.97. This implies that the present value of the project is higher than the initial cost. As such, it is concluded that the cost of the investment of this project is optimal and profitable.
Internal Rate of Return
Taking the respective cash flows in revenue, the rate of return is measured at 17.804. This implies that the IRR is essentially high above the interest rates which are just 0.25 %. As such, the project is profitable and viable for the company to continue producing its products.
Corrective Action
Mean Time= (17+14+13+15+16)/5=75/5=15 minutes
- In the case of collective maintenance is required, the identification and documentation must indicate all the possible failures.
- The personnel should then conduct routine monitoring to test the performance using the intelligent terminal cable
- The personnel should then refer to the faulty dictionary to identify the implications of various measurements and suitable responses.
- Instructions concerning the isolation of parts and precautions should be made to prevent secondary failures
Preventive Maintenance
Regarding the timelines of repair, the following shows the period used by the company.
- Single Inspection of a Dell computer=35 Minutes
- Single inspection of Dell inbuilt software=47 Minutes
- Trouble Shooting=20
- Mean Preventive Time= (35+47+20)/3=34Minutes
To ensure the quality maintenance of Dell products, the company has developed an internal capability to ensure that there is real-time monitoring. This inbuilt capability captures the users’ experience when interacting with various applications in the computer and identifies the causes of failures in the system. As such, the system enables the users to fix the problems causing the incidents of failure in the system. It enables the user to diagnose the malfunctions and fix them to attain the required satisfactions.
When it comes to the database, the Dell system enables a simplified and real-time monitoring of the database. This monitoring helps the users to optimize their performance and keep any malware from affecting the performance of the database negatively. In essence, the monitoring services help the customers to increase performance and reduce the administrative cost at the same time. This is fulfilled by setting the database in a manner that all its components are operating within their capacity. Importantly, the company has enables the users to use an automated system that notifies them when the limits are extended beyond limits. As such, the users cannot reduce the performance by extending the limits of the various functionalities.
In summary, therefore, Dell engages in various preventative undertakings that include the following.
- It selects hardware from suppliers to prevent passing on the inherent defects to customers
- It uses real-time monitoring to detect possible threats to both the hardware and software besides recommending the required action.
Enabling Maintainability
Enabling maintenance is an undertaking that supports the customers and employees to understand the practice of maintenance and do it practically with essential ease. Dell has availed many provisions to ensure the employees can maintain their devices by themselves without even seeking consultation from the company.
First, the company involves the employees when undertaking the designing phase. This implies that the employees understand the entire design of the products. This understanding provides the employees with the rationale of installing every part in the pursuit of avoiding defects and promoting maintenance.
Second, the company undertakes a careful and thorough selection of hardware before the assembly of the products. In this regard, the quality of the assembly parts is a fundamental determinant of maintainability. To enable maintainability, the products must be less of defects and resilient to destructions. The selection of hardware and use of quality assembly parts makes sure that the clients incur minimum defects and requirements to diagnose the devices. If the defects are too many, the customer might be overloaded by the diagnoses. Some of the users might develop more problems on the devices in the process of diagnosing because they have minimal skills in maintenance (Vieites & Gonzal, 2012).
Dell has also implemented a highly technological troubleshooting mechanism that enables users to detect any issues that might reduce performance. In case of any malfunction, the users can troubleshoot to get the various suggestions on the possible solutions for the noted problem. As such, the company makes it easy for the clients to diagnose the computers by themselves rather than seeking consultations from the company support services. Also, it enables users to make the necessary corrections before the defects cause subsequent problems.
Significant Changes that Occur in Operational Scenario
One of the critical changes that occur in the operational scenarios is the reorganization of transport systems. For example, Dell has shifted to a green transportation program that is steered towards ensuring environmentally friendly operations. In their changes, they seek to implement a decision-making platform that determines the type and amount of goods that should use a given transport system. As a result, they have adopted all the transportation systems including air, road, and water. This aimed at minimum pollution of air and the environment following the directive of the government which requires companies to participate in the prevention of global warming in the country (Yang, 2012). Another crucial change that occurs in the operational scenario involved the reduction or increment of supply chain components. For instance, Dell shifted from a retail-based supply chain system to a direct model where the customers receive products from the company directly. In this case, this was aimed to increase the customer-company interaction and strengthen the relationship.
These two changes require the company to adopt flexibility to absorb the transformation. For example, green transportation requires the company to explore new transportation ways which reduce the cost and pollution of the environment. When it comes to the reduction of the supply chain components under the direct model, the company needs to have flexibility. In this case, the company requires installing an online ordering system for customers to facilitate the Build-to-Order and Configure-to-Order systems. However, some other changes require robust changes in the company. One of those changes is the emergence of a competent product from a competitor. In this case, when a company is confronted by a new innovative product, it seeks to reorganize its staff to develop another competitive product that can stand up to the merging one. Also, the company requires a turn-around strategy which enables it to increase its research and development capacity. This may call for increased funds for research and exploration of the market needs.
Risks Associated with Dell Logistics Systems and Mitigations
The logistic system of Dell is being confronted by one critical risk that might affect the profitability of the company. Previously, it was stated that the Direct Model requires the company to take the responsibility of providing the support services. If the retailers were involved the repairing services are left to them and they incur the cost. Now, with the rising customer base, Dell might be confronted with a situation where the customers’ base demand high support services. In this case, it is important to remember that the direct model cuts the cost of production but increases the cost of production to the company. If the customer base grows rapidly, the company will find itself in a situation where it incurs higher service costs than the savings it makes during production. The overall effect will be insolvency that might see the financial downfall of the company over time.
To mitigate this situation, the company must ensure that the service cost is lower than the amount of money saved during production. As a result, it must increase the quality of the devices by procuring high quality and resilient assembly parts. This will reduce the cost of quality and cut on the cost that goes to the warranty providers as well as the support services. Also, they should develop an automatic service provision where the customers can access the required information. Also, real-time monitoring services should be universal and far-reaching. The company should also implement the franchise systems to offload the support service costs on the basis that the owners of those franchises will incur such costs. Lastly, the company should also consider using the retailers in a regulated manner to ensure that the support service cost is balanced. Indeed, retailers can be used in foreign countries where the company finds it difficult to reach with ease.
Availability
To maintain a competitive edge, Dell must ensure that it is available on a real-time basis. This is based on the fact that clients require instant and fast responses to demand, orders and inquiries. Importantly, it should ensure that its customer ordering system is responsive enough. This implies that customers can reach the company when they want and place the order within their schedules. Also, the company should ensure that the customer support services operate on a 24/7 basis to facilitate their availability to the clients. In case the support services are poor, the competitors can take advantage and strike the company based on availability.
Reliability
The company has ensured vast and effective systems to ensure the reliability of their products. Importantly, they have implemented the parallel system whereby various processes of each step are independent of each other. This implies that when one of the processes breaks down, the other one can be used to execute the same task within the required schedule. The figure below shows the illustration of the parallel system diagrammatically. In the diagram, there are four systems names 1, 2, 3 and 4. The systems operate independently but they execute the same functionality. It is evident that the start point, as well as the endpoint, is the same by the processes to execute the entire task are different. As a result, for instance, if 1 breakdown, the company can use 2, 3 or 4 to ensure that the customers are served.
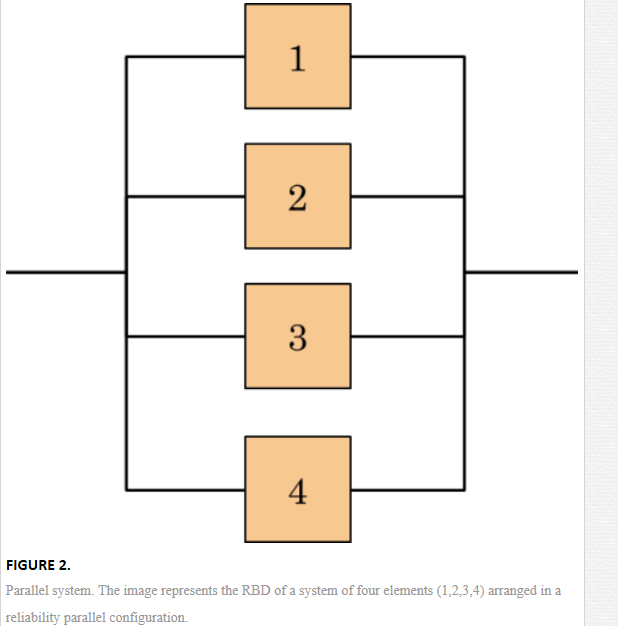
The parallel system is used during the ordering process whereby the company uses BTO, CTO or pre-assembled products. As a result, if the BTO system breaks down, the customers can take the pre-assembled products. When it comes to transportation, the company uses the various mean of transportation including air, water and road transport. As a result, if the shipping is affected by logistical problems, the company can use air to transport their products.
Problems in Operations Capabilities
Increased Service Support Cost
Due to the use of the direct model, the company requires to provide full support to its customers around the world. As a result, they will be incurring additional cost which was otherwise catered by the retailers. Shortly, the cost avoided during production due to the application of the direct model might become insignificant because of the rising demand for support services. Of course, the support services requirement is increasing because of the growing customers’ base.
Cost of Quality
Dell incurs a cost of quality which can hurt the solvency of the company. In most cases, the suppliers can provide parts that are not up to standards. As a result, the company is incurring costs that are not as a result of its poor assembly techniques or substandard services. As a result, the company should take some fast and tactical measures to retain this problem.
Competitive Market
Indeed, Dell is confronted by the competition in the computer industry where many companies are coming up. In this case, companies such as Apple are well organized when it comes to innovation and the development of new products (Huy, 2012). This implies that the company will incur a high cost of production to invest in research and development. This comes amidst a time when the company is trying to reorganize itself and eliminate its financial constraints. As such, it cannot take its time to change and transform its operational mechanism because the competitors might achieve an advantage.
Lack of Competitive Innovation
From a comparative perspective, Dell has been very static as far as innovation and development of new products are concerned. In this regard, companies such as Apple have developed very important and crucial products that have changed the world dramatically. In particular, the Apple personal computer has been highly regarded due to its quality and friendliness to the users. As such, Dell cannot maintain its customers if the level of innovation remains at the current level.
Redesigning of Logistics Operation
Various changes should be made to ensure that the company operates efficiently, sustains the trust of customers, and increases its profitability.
Use of Six Sigma
Dell should use Six sigma to evaluate and improve its quality to maintain its customer base and attain a competitive advantage. The DMAIC steps include five steps which are procedural as follows:
- D – Define Phase
- M – Measure Phase
- A – Analyze Phase
- I – Improve Phase
- C – Control Phase
The method uses data to identify defects in a system and then identify ways of correcting those malfunctions. Importantly, Dell has vast data that can be used in this undertaking since it participates in the direct model of distribution. Importantly, the Six Sigma method will reduce variations, increase stability and facilitate accuracy.
Use of the SCOR Model
Top-Down Analysis Benchmarking
Using the SCOR Metrics, Dell should benchmark on various issues revolving around the computer industry. Some of the critical factors that should be benchmarked are as follows.
- Regional performance of the competitors in terms of their profitability and production.
- The trend of the computer industry for the last 10 years to help in projecting the next possible changes in the market.
- The supply chain performance and innovations embraced by competitors to ease delivery.
End-to-End View
The End-to-End visibility of the supply chain enables the tracking of product status all along the supply chain. It allows the entering of data into a cloud storage database. Also, it allows the actors to import data directly from the system for use. This implies that a supply chain actor can transfer the data from the system into the business system. As such, the reception and sending of data from the Dell database become easy such that communication is efficient. Diagrammatically, this view can be expressed in the flow chart below.
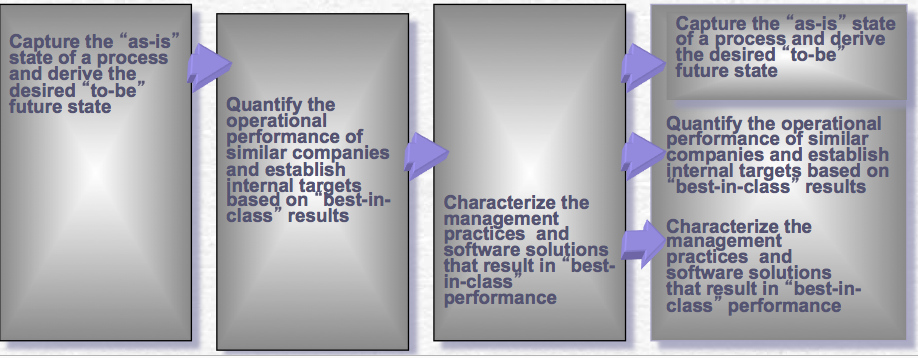
Use of duplication or replication system
The company should introduce a duplication or replication system. This requires the company to use additional parts in the devices such that a single malfunction in the system does not cause the breakdown of the entire product. Indeed, this will be an additional aspect when it comes to the use of the parallel system to ensure reliability. However, this will require additional cost when it comes to the capital required, the weight to the product, and the design of the device to accommodate the changes. Also, the improvement of reliability in the system might cause further problems especially when one kind of malfunction impacts one failure type at the expense of another malfunction.
Use of combined system with both the CTO and BTO
The company should introduce a combined system that includes both the CTO and BTO. The BTO will provide customers with an opportunity to order the desired features. The company should enable the customers to order and get the orders within 24 hours. The combination of the CTO and BTO will enable the company to offer more options to choose from. This will play a fundamental role to ensure that the supply chain changes. It will increase the warehouse capacity unlike the use of the BTO which essentially helps to maintain a small inventory.
Supply and Parts Selection
The company should embark on a serious and careful selection of the suppliers before procuring the assembly parts. In this case, the company should ensure that the parts are validated to prevent transferring inherent defects to the customers. The evaluation of the suppliers will also help to ensure that the companies are credible and have a reputation when it comes to the supply of quality products in the market.
Use of RFID during transportation
In addition to validation, the proposed system ensures the use of RFID during transportation. As such, the RFID system offers a quick and responsive solution for the customers to track their products during transportation. As a result, the RFID-enabled system will increase the availability of the company’s services and reliability during transportation. Importantly, the RFID reduced cost builds trust and increases responsiveness when it comes to the automation of transportation progress.
Advantages of the Proposed Solution
Cost
The proposed solution will help to reduce the Cost of Quality and the support services required by the customers. In this light, the validation of the supplies will ensure that the customers do not get substandard products after the assembly. In other words, the probability of passing on the defects that are originally inherent on the supplies will be very low in case validation is conducted.
Time
The validation of the products will ensure that the assembly is fast and efficient. As a result, the effective coordination of the assembly using fine assembly parts will reduce the time required to sort and fix the parts to make the machines.
Maintainability
Due to the validation of services, the company will ensure the increased quality of the Dell products. As a result, the computer will have very few defects and possible malfunctions. This implies that the current automated real-time monitoring systems will be sufficient to maintain the products from the customers’ side without even seeking the warranties.
Reliability
The use of the RFID tracking system will be a critical breakthrough when it comes to the reliability of the supply chain. Using this system, the customer can track the progress of transportation is a very responsive and fast manner. As a result, the trust of the clients will increase significantly and hence the creation of a good corporate image.
Discussion
Following the analysis that has been provided above, this paper presents the following findings. First, it indicates that Dell uses a direct model of the supply chain where products are delivered to the customer directly. This helps the company to use negative capital and reduce the cost of production besides cutting the inventory. However, it also increases the service cost that may outweigh the cost avoided by the Build-to-Order system. Nonetheless, validation of supplies and the use of franchise can reduce the service cost and the COQ.
Whereas the company has afforded to reduce the cost of operation significantly, it is important to make various changes in the company. The paper proposes that the company should use the duplication system that improves the reliability of the devices. In this regard, it ensures that one failure does not lead to the malfunction of the entire device because other functionalities can operate as an alternative. Second, the company should embark on careful and thorough evaluation of the suppliers as well as their supply parts to prevent incumbent defects which may come with substandard assembly parts. In addition to this, the company should use a virtual integration system to ease the ordering system, facilitate the tracking of product’s transportation and communication with suppliers. Also, Dell should combine the CTO and BTO systems to increase the warehouse operation as they still reduce the inventory. Lastly, it was evident that the company should implement the RFID system which facilitates efficient ordering and traceable transportation. These proposals will go a long way to ensure the increase of sales, add profitability and expand market share. In summary, there are critical solutions that have been proposed according to the table below.
Conclusion
It cannot be disputed that Dell uses a direct model of supply chain management where the company has direct contact with the customers. The use of the direct model has also been integrated with the BTO system where the customers are allowed to order before the assembly and the delivery of the products. As such, the company can reduce the cost of production and inventory to zero. However, the cost of support services is quite alarming because direct delivery necessitates the company to provide the service which would otherwise be provided by the retailers. However, this service cost can be reduced by the validation of assembly parts and the use of the franchise.
References
Arthur, C. (2012). Inside Apple and How America’s Most Admired and Secretive Company Really Works. Choice Reviews Online, 49(11), 231-247.
Balakrishnan, A., & Geunes, J. (2010). Collaboration and Coordination in Supply Chain Management and Ecommerce. Production and Operations Management,13(1), 1-2.
Carls, P. (2011). Order Management in a Case Study in Technological Companies. American Journal of Engineering and Applied Sciences, 6(27), 372-379.
Chang, K., & Graham, G. (2012). An Empirical Study of Supply Chain Management in Ecommerce Project in USA. International Journal of Electronic Business Management, 10 (2), 101-112.
Du, L. (2007). Acquiring Competitive Advantage in Industry Through Supply Chain Integration. Journal of Enterprise Information Management, 20 (5), 527-543.
Dura, C., & Isac, C. (2012). Overview of Performances Achieved by Multinational Companies in the Globalization Era. International Journal of Future Computer and Communication, 15(23), 209-212.
Finch, P. (2009). Supply Chain Risk Management. Supply Chain International Journal, 12(27), 183-196.
Ho, Y., & Fan, L. (2011). Achieving Quality Performance and Environmental Sustainability by the Genius Loci of Quality Management Systems. International Journal of Quality and Reliability Management, 12(56), 144-165.
Huy, P. (2012). Steve Jobs Post Scriptum. Medium Journal, 30(1), 17.
Kim, K. (2011). A Study on Effects of Internal Marketing on Secretaries Job Satisfaction and Organizational Commitment in IT Companies. Journal of the Korea Society of Computer and Information, 12(34)187-194.
Mendelson, H., & Ziegler, J. (2009). Survival of the Smartest and Managing Information for Rapid World Class Performance. California: Wiley & Sons Publications
Neto, P., Fusco, J., & Machado, S. (2014). Supply Chain Strategies in the Context of Ecommerce Chain. Independent Journal of Management and Production, 5 (2), 438-459.
Trites, G., & Boritz, E. (2012). A Canadian Perspective for Networked World. Toronto: Pearson Prentice Hall.
Vieites, A., & Gonzal, C. (2012). A Study of Innovation Activities in Software and Computer Services Companies. Management Journal, 19(34), 49-58.
Yang, M. (2012). Supply Chain Management Under Ecommerce Environment. International Journal of Innovation, 3(3), 210-213