Integrated Logistics for DEP/GARD
The following stages add value:
- The DEP’s seven-day delivery and the flexibility of the company: it can change the kind and quantity of the produced polymers;
- The interactive system which becomes a helpful instrument since it connects different departments and reduces the number of errors;
- Verifying orders for correctness (quantities and end items) (Hoorn 55).
The following stages do not add value:
- Moving goods to other warehouses to verify them;
- Time losses associated with the order and paperwork which ideally should be kept together (Waters and Rinsler 45).
Using the primary DEP suppliers (60 percent of the business), one can receive the following results:
- Minimum Order Cycle = Timely Performance + Time Adjustments = 6 + 2 = 8 days.
- Maximum Order Cycle = 6 + 6 + 5 + 4 + 4 = 25 days.
Yes, the performance can be improved on condition the given percentages are relevant. The new suppliers must be credible and accurate. Although small deviations can bring more trouble, the long-term advantages are potentially worth the effort.
W‐G‐P Chemical Company
First of all, one should calculate the carrying costs. According to Table 4, the inventory carrying cost rate equals 18 %. This formula should be used:

Annual carrying cost = 90×0.18 = 16.2 million.
Total distribution cost = all costs represented in the table without the average inventory level = Storage + Handling + Ordering + Transportation to warehouse + Transportation transfer between centers + Transportation to customers = 33.2 million.
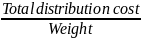

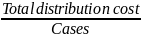

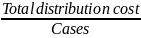

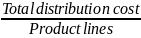

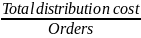

These measures can help the company identify possible areas of cost reduction, and benchmarking these measures against those of their rivals will give the chance to find strengths and weaknesses (Rushton, Croucher, and Baker 106).
Location is one of the most significant characteristics (Yu, Normasari, and Luong 6). One can see that the majority of distribution centers and other facilities are close to agricultural regions; besides, the transportation conditions are favorable since railroads, highways, waterways, and canals are nearby. Because farmers start buying the products prior to the beginning of field works, this location becomes advantageous. Bulky containers make the delivery process optimal.
Some alternatives are probable:
- To create more distribution models, this issue may be open for the discussion;
- The locations of the warehouse may be considered: although the large number can be justified, it is possible to view how the quantity reduction will influence the whole process. For instance, one facility may serve two states.
The early order program may be beneficial to project future demand and allocate the resources accordingly. If this information is collected, more cost-effective measures will be chosen. The customer pickup policies are associated with dealers who want to use their equipment to the fullest extent. Moreover, the company will not have to schedule common carriers for pickup at the warehouse and delivery to dealers (Holcomb, Liao-Troth, and Manrodt 518). Finally, public warehouses are likely to help reduce costs because private warehousing is connected with full employment expenditures and supervision. In other words, public houses are more cost-effective in terms of seasonal issues (Myerson 25).
Designing the Distribution Network for Michael’s Hardware
The following indexes are relevant:
- Batch size = 10 000
- Average inventory at store = 50 000
- Number of shipments per year = 5
- Truck cost / retail store / supplier = $ 2 250
- Total truck cost = $ 576 000
- Holding cost / retail store / supplier = $ 50 000
- Total holding cost = $ 1 280 000
- Total holding and truck cost = $ 13 376 000
The Annual Distribution Cost of the current distribution network is calculated:
- Total transportation cost = 8 × 32 × 10 000 × 0.5 = $1 280 000
- Holding cost = (500/2) × 8 × 32 = $64 000.
- The total annual cost = 1 280 000 + 64 000 = $1 344 000.
Milk Run Using Small Trucks seems to be an optimal solution since it can decrease the transportation cost to a larger extent.
- Number of stops/truck 4 Batch size/product/store =10000/4=2 500.
- Average inventory at store/product=2500/2=1 250
- Number of shipments/store/year =20
- Truck cost/retail store/supplier/year=3000
- Total truck cost/year=768 000
- Holding cost/retail store/supplier=250
- Total holding cost/year=320 000
- Total holding and truck cost=1 088 000
- Savings=1088000–320000=768 000
Milk Run Using Small Trucks (full) is more advantageous. The same calculations model will demonstrate that the cost savings will equal $576000.
If Ontario grows, the number of stores aggregated on one truck will be reduced. The number of stores per milk run will change from four to two. If Albertina grows, the necessity for facilities will diminish. The increase in demand is expected. Thus, the facility will be appropriate until the demand in Albertina increases by a factor of four relative to current levels.
Works Cited
Holcomb, Mary C., Sara Liao-Troth, and Karl B. Manrodt. “A Shift in Fundamentals: The Changing Direction in Logistics and Transportation Management.” Transportation Journal 53.4 (2014): 516-533. Print.
Hoorn, Johan F. “Stakeholder Logistics of an Interactive System.” Journal of Systems and Software 95.1 (2014): 52-69. Print.
Myerson, Paul. Lean Supply Chain and Logistics Management. New York: McGraw Hill Professional, 2012. Print.
Rushton, Alan, Phil Croucher, and Peter Baker. The Handbook of Logistics and Distribution Management: Understanding the Supply Chain. London: Kogan Page Publishers, 2014. Print.
Waters, Donald, and Stephen Rinsler. Global Logistics: New Directions in Supply Chain Management. London: Kogan Page Publishers, 2014. Print.
Yu, Vincent F., Nur Mayke Eka Normasari, and Huynh Trung Luong. “Integrated Location-Production-Distribution Planning in a Multiproducts Supply Chain Network Design Model.” Mathematical Problems in Engineering 1.1 (2015): 1-14. Print.