FMEA
Failure Modes and Effects Analysis is a framework typically used to determine the existing risks and evaluate the potential harm that they may cause to a company or a project (Kubiak & Benbow, 2014a). The areas that FMEA embraces include the manufacturing process, the design, the promotion of a particular product, the quality assurance stage, etc. FMEA helps rank the risks according to their severity and, thus, single out the ones that are the most dangerous (Kubiak & Benbow, 2014b). A table below is an example of FMEA in QA.
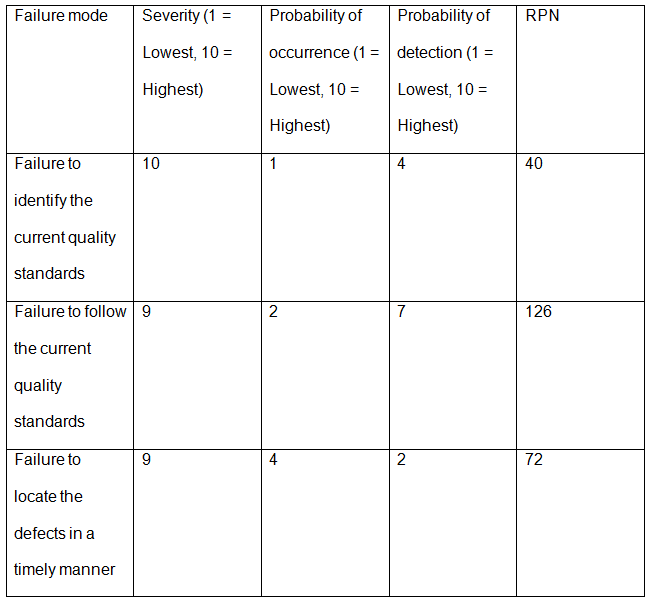
FMEA may serve to help identify the threats of entering a new market (see the table below).
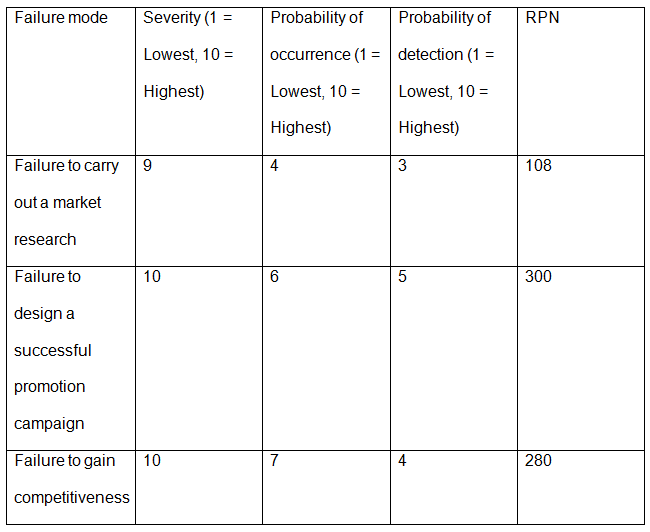
Pilot Testing
Pilot testing is a small-scale test that helps figure out whether a certain product, strategy, or tool will be viable in the real-world environment (Kubiak & Benbow, 2014c). Traditionally, pilot testing implies that the item in question should be tested on several people prior to using it to its full potential. In the course of a pilot test, essential flaws of the item can be identified and addressed.
For example, a survey designed to collect data about the popularity of a particular movie genre can be pilot-tested by offering it to a small group of people (i.e., 2-10 participants) (Kubiak & Benbow, 2014d). Similarly, a new recipe may undergo a pilot test once its creator makes a small portion and offers it to the neighbors before introducing it to a large market. Finally, the notion of a pilot test can be applied to a new quality assurance framework by selecting a group of people for an experiment and suggesting them to follow the new framework.
Talk Time
As a rule, the concept of the talk time is rendered as the amount of time that an agent of a call center spends with the customer during the conversation. For example, when a customer of a service provider has issues with the Internet connection and contacts the corresponding call center, the time spent on conversing with the representative of the organization and addressing the issue can be defined as call time. The waiting time that the customer spends in line, however, is not included in the definition (Kubiak & Benbow, 2014e).
Similarly, when contacting the hotel reception staff by phone in order to book a room and mention essential details, the amount of time that one spends when communicating with the receptionist is viewed as the talk time. The time that the customer spends when arriving at the hotel and talking to the receptionist directly is not included in the definition, though.
Cycle Time
The cycle time is typically defined as the time that a stage of a process requires to be completed (Kubiak & Benbow, 2014g). The phenomenon of the cycle time applies to not only minor stages but also to grand processes. Therefore, the time-lapse may vary from a couple of minutes to several hours, days, or even months. With the help of the cycle time, a line is drawn between the run time of a process and its duration (Kubiak & Benbow, 2014f).
For example, the time taken to complete every single stage of the product promotion process in a food manufacturing company is an example of the cycle time. The time-lapse between the beginning of the first stage of the QA process and the end of the final one (i.e., the identification of the standards and the submission of a report) is also an example of the cycle time.
Reference List
Kubiak, T. M., & Benbow, D. W. (2014a). Chapter 28: Design of experiments. In The Certified Six Sigma Black Belt handbook (2nd ed.) (pp. 294-331). Milwaukee, WI: ASQ Press.
Kubiak, T. M., & Benbow, D. W. (2014b). Chapter 29: Waste elimination. In The Certified Six Sigma Black Belt handbook (2nd ed.) (pp. 333632-). Milwaukee, WI: ASQ Press.
Kubiak, T. M., & Benbow, D. W. (2014c). Chapter 30: Cycle-time reduction. In The Certified Six Sigma Black Belt handbook (2nd ed.) (pp. 337-341). Milwaukee, WI: ASQ Press.
Kubiak, T. M., & Benbow, D. W. (2014d). Chapter 31: Kaizen and Kaizen Blitz. In The Certified Six Sigma Black Belt handbook (2nd ed.) (pp. 342-343). Milwaukee, WI: ASQ Press.
Kubiak, T. M., & Benbow, D. W. (2014e). Chapter 32: Theory of constraints. In The Certified Six Sigma Black Belt handbook (2nd ed.) (pp. 344-346). Milwaukee, WI: ASQ Press.
Kubiak, T. M., & Benbow, D. W. (2014f). Chapter 33: Implementation. In The Certified Six Sigma Black Belt handbook (2nd ed.) (pp. 347-350). Milwaukee, WI: ASQ Press.
Kubiak, T. M., & Benbow, D. W. (2014g). Chapter 34: Risk analysis and mitigation. In The Certified Six Sigma Black Belt handbook (2nd ed.) (pp. 351-356). Milwaukee, WI: ASQ Press.