Process Evaluation
The Toyota Production System gave rise to the lean approach, now a mainstay for businesses looking to reduce waste and improve operational effectiveness. The main goal of applying the Lean concept to evaluating a process is to find and remove any waste that might obstruct its flow and result in inefficiencies and worse overall performance. Fundamentally, Lean is based on the understanding that processes generate value and that every action or stage that does not add to this value is wasteful. Lean thinking has discovered that motion, inventory, waiting, defects, overproduction, overprocessing, and transportation are the seven categories of waste. Within a business, this waste may take many forms that impede customer satisfaction and production.
Finding customer value is the first step in using Lean for process assessment. It is essential to comprehend which process elements directly affect customer satisfaction and to match activities with these principles. Process improvements are closely related to meeting or exceeding customer expectations because of this customer-centric approach. One essential tool in the Lean toolbox is process mapping. This workflow’s graphic depiction gives an in-depth synopsis of the whole procedure. It enables businesses to identify waste, redundancy, and bottlenecks. Process mapping helps businesses see the flow of work by emphasizing the connections between different processes and sets the groundwork for targeted changes.
Once the process has been mapped out, its main objective becomes to streamline it. Streamlining entails removing unnecessary stages, streamlining workflows, and ensuring that every stage of the process contributes significantly to the conclusion. Organizations may improve the overall efficiency of their operations by eliminating non-value-added tasks and redundancies. Making just what consumers need is another essential Lean concept. In addition to creating surplus inventory, overproduction wastes resources. Lean promotes businesses to match their output to actual demand from customers in order to minimize the danger of overproduction and guarantee effective use of resources.
Lean thinking’s core principle is to strive for excellence. Continuous improvement is an organizational philosophy rather than a one-time project. Organizations strive for process excellence by consistently detecting and eliminating waste. This dedication to continuous improvement ensures that the company stays flexible, adapts to changes in the market, and continuously provides high-quality goods and services.
Evaluation of Control Chart and Process Metrics
In statistical process control (SPC), understanding the causes of process variation is crucial for assessing control charts and process metrics. Variations can be classified as a common cause or a particular cause, with common cause variations being a natural byproduct of the process and particular cause variations being the outcome of identified causes. Process capacity is an essential indicator in SPC, providing information on the process’s long-term performance.
Differentiating between discrete and continuous data is essential for evaluating process capacity in Six Sigma. The Individuals and Moving Range (I-MR) control chart is vital for assessing process stability. It displays data changes chronologically, identifying variation causes and determining if deviations are within allowable limits. Excel’s control chart and process metrics visually represent process performance, allowing organizations to understand the efficacy of their processes. A graph depicting a control chart from the computations is shown in figure 1.
A thorough examination of these charts and metrics is necessary to determine if the process could benefit from Six Sigma, Lean, or other techniques. Stability can be achieved if the control chart shows regular, predictable fluctuation within allowable limits, while substantial deviations beyond allowable limits indicate unique reasons that require further research. Lean tools may be more suitable for reducing waste if the process shows common cause variation, while Six Sigma techniques can be used for focused improvement.
Table 1 – Statistical Data.
In calculation of the variation of the process, the standard deviation formula should be used:
Where s is the standard deviation, x is each data point, x̄ is the mean of the data, and n is the number of data points.
s = 4.903616
So, the variation of the process is 4.903616.
To calculate the process capability, the process capability index formula is used:
Cp = (USL – LSL) / 6s
Where Cp is the process capability index, USL is the upper specification limit, LSL is the lower specification limit, and s is the standard deviation. The specification limits are the acceptable range of values for the process output.
Cp = (22 – 18) / 6 * 4.903616
Cp = 0.13595
So, the process capability is 0.13595.
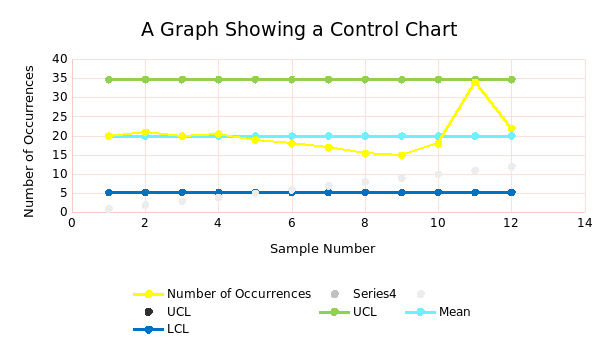
Executive Summary
Process Evaluation Using Lean Methodology
Lean methodology for process assessment is a strategic approach to process improvement in management, emphasizing efficiency gains and process error correction. Lean uses ideas, techniques, and procedures to eliminate waste in operational processes that take up time and money. Lean seeks to improve resource efficiency by focusing on motion, inventory, waiting, defects, overproduction, overprocessing, and transportation. This approach leads to higher-quality production and more total outputs by optimizing statistical control procedures and increasing efficiency. Lean helps to ensure process consistency by methodically eliminating waste, which helps to match operations with customer value and market expectations. Process mapping is a crucial Lean tool that helps visualize and optimize operations and offers a path forward for waste reduction and ongoing development.
Evaluation of Control Chart and Process Metrics Using SPC
The control chart and process metrics were assessed using Statistical Process Control (SPC) techniques, which gave rise to a solid knowledge of the process’s capacity and stability. SPC is a data-driven technique for quality improvement and analysis that tries to stop issues from arising in internal systems. In this review, the I-MR control chart is used to identify out-of-control signals, such as persistent runs that indicate anomalous data patterns, patterns on one side of the mean line, or points outside of control boundaries.
Production companies can follow and identify irregularities in the production process thanks to the real-time visual information provided by control charts, which is made possible by statistical process control software solutions. SPC’s suggestions strongly emphasize the value of real-time data, high-quality work, and data supply to deter excessive manipulation, simple data access, and elevated visibility levels. Control charts help to provide a thorough grasp of the dynamics of the process by serving as operational insights for essential stakeholders.
Evaluation of the Need for Six Sigma, Lean, or Other Tools
The examination of the control chart and process metrics drove the assessment of whether Six Sigma, Lean, or other methods may be beneficial for the process. Because lean approaches prioritize efficiency improvement and waste reduction, they are well-suited for processes with common cause variations. Businesses may improve overall productivity and simplify processes by using Lean techniques like value stream mapping and 5S methodology.
On the other hand, Six Sigma techniques are necessary for targeted defect reduction if the control chart shows notable variations beyond permissible bounds and points to unique cause variations. Enhancing process quality and uniformity using statistical methodologies, Six Sigma focuses on making procedures transparent and consistent. Depending on the kind and degree of variations found, Six Sigma or Lean techniques may be integrated to provide a customized and all-encompassing approach to process optimization. To optimize processes effectively, evaluating additional tools like process automation, advanced analytics and tailored technology is crucial.
Description of the SPC Project and Recommendations for Improvement
Using the I-MR control chart and SPC techniques, the Statistical Process Control (SPC) project included a thorough investigation of process capacity and stability. Atalan and Atalan (2023) suggest using statistical process control (SPC) methods with the I-MR control chart to verify the accuracy of machine learning models for solar energy generation. This method offers a two-way validation mechanism, confirming system control.
Integrating machine learning with SPC can improve power plant efficiency, energy demand management, and resource use, offering several advantages. Depending on the kind of alterations found, targeted actions are among the improvement suggestions. Using Lean tools like value stream mapping and the 5S approach helps further improve operations and cut waste for frequent cause variations.
Using the DMAIC (Define, Measure, Analyze, Improve, Control) approach, Six Sigma techniques may be used to systematically identify and remove the root causes of defects, including unique cause variants. Process improvement requires regular evaluations of the control chart, process metrics, and ongoing monitoring. Employee upskilling and training in Six Sigma and Lean techniques promote an ongoing improvement culture within the company. Additionally, the organization’s ability to react quickly to new trends or changes is improved by integrating technology for real-time data collection and analysis. This focus on technology aligns with SPC’s suggestions for higher visibility levels and real-time data provision. Organizations may create a complete framework for continuous improvement and guarantee effective and superior operational processes by integrating Lean, SPC, and Six Sigma approaches.
Reference
Atalan, Y. A., & Atalan, A. (2023). Integration of the machine learning algorithms and I-MR statistical process control for solar energy. Sustainability, 15(18). Web.