Maintaining Current Partnerships
Due to the increase in market demand and the company’s expansion to other markets, VASA faces various challenges and can consider several solutions. First, it is possible to focus on the solutions associated with the maintenance of the partnerships with the two transportation companies. This option can be viable as it is rather difficult to find a delivery company that could provide high-quality services in the glass industry due to the specifics of the delivery process (Sanchez Loppacher, Pancotto, & Vera, 2013). CristaLog Hnos. and Transfer S.A. has sufficient float to cover the demand of VASA. It is noteworthy that the trucks have trestle and modular technology that are specifically valuable in the process of delivery. The two transportation firms have different areas, so their interests do not overlap, which contributes to the development of appropriate relationships between the contractor and delivery services.
Moreover, VASA has collaborated with these organizations for over two decades, so they managed to establish proper relationships that have a positive impact on their business development. Morana (2013) claims that sustainable supply chain management involves the development of effective relationships with partners and maintaining these links. Sanchez Loppacher et al. (2013) also claim that customers also have a positive attitude towards such lasting partnerships and develop good relationships with delivery companies as well. Maintaining current transportation companies will also help VASA avoid additional costs associated with contracting new firms.
Existing Issues and Available Solutions to Maintain Current Partnerships and Improve Delivery Quality
The Use of Technology
To improve the delivery service and keep current partnerships, VASA has to focus on such areas as effective inventory management, strict scheduling, effective dispatch teamwork, and penalties for delays, as well as closer cooperation with the transportation companies. To start with, the company should address one of the key issues it is facing at the moment. The growing number of customers and deliveries makes supply chain management more complex. Sanchez Loppacher et al. (2013) note that ordered items are not always available for dispatch at the time of the truck’s arrival. Although the company uses certain information systems to conduct its operations, they have proved to be ineffective.
The use of sophisticated technology such as cloud computing, service-oriented software, and the Internet of Things can ensure the improvement of supply chain management (Helo, Shamsuzzoha, & Sandhu, 2016). A certain level of connectivity between VASA and transportation companies can help them control arrival and dispatch times more effectively. The use of technology will ensure the elimination of 4- and 5-level delays that disrupt the entire delivery process. It is essential to make sure that the dispatch team is completely ready when the truck arrives. Loading should start upon the truck’s arrival, and no delays can be tolerated. VASA should consider investing in additional equipment that could improve the dispatch process.
The development of schedules and strict adherence to them can be possible if appropriate information systems are utilized, certain training is provided to employees, and some HR policies are introduced. The review of the company’s documentation shows that schedules are extensively used, but the number of delays indicates that the process is characterized by low compliance with the planned time. One of the major reasons is the flaws of the information systems utilized as some items can be unavailable even during the process of dispatch. The introduction of the new information systems (which was discussed above) should be accompanied by extensive training provided to the dispatch teams (Ross, 2016). Employees should have the necessary skills to use the new technology. In addition, it can be beneficial to use some rewards for the most effective teams. To trace the employees’ performance, it is possible to use the system of self-reporting and scoring.
When introducing new software, the company will have to address some challenges. First, this process is rather lasting and costly, which may lead to certain financial constraints. However, a more serious issue will be associated with the collaborations with VASA’s partners. The transportation companies in question may be reluctant to invest in the use of new technology they might need to improve information sharing with VASA. The implementation of any information system requires the provision of extensive training to employees, which results in additional costs (Helo et al., 2016). Transfer S.A. and CristaLog Hnos. maybe reluctant to allocate additional funds due to scarcity of resources and increasing competition in the market. Confidentiality and data security problems can also make companies unwilling to share information to the extent necessary for their mutual benefit.
Collaboration with Partners
As far as the collaboration with the transportation companies is concerned, it should become more effective. One of the most urgent issues to address is associated with a company’s policy regarding customer service. The representatives of Transfer S.A. claim that they tend to assign similar drivers to deliver loads to certain customers (Sanchez Loppacher et al., 2013). They stress that such a strategy enables them to maintain good relationships with their customers although it is not always convenient for logistics. This delivery company operates throughout the entire country, and it covers 35% of VASA’s customers, which is a considerable amount (see Chart 1). It is possible to assume that Transfer S. A. can contribute to VASA’s loss of a third of its customers.
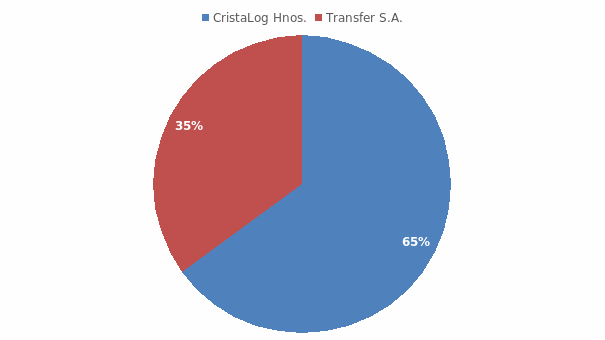
VASA should negotiate with the company ensuring that they will abandon their customer loyalty policy that results in delays and some customers’ overall dissatisfaction. Addo-Tenkorang, Helo, and Kantola (2016) emphasize that the development of value-added partnerships is essential for the creation of a sustainable supply chain network that, in its turn, is critical for companies’ competitiveness. Such relationships can be developed through effective information sharing and cooperation within cross-sectional teams. Therefore, VASA can try to achieve deeper cooperation and become involved in the development of routes.
For example, instead of assigning drivers to deliver cargo to certain customers, trucks will be assigned to follow some routes. One of the arguments for such an approach can be the results of a survey that would involve evaluating customers’ satisfaction. This process is also associated with some challenges as companies are reluctant to tolerate any interference with their internal policies. For instance, Transfer S. A. boasts its long history and the ability to maintain friendly relationships with its customers. Therefore, the organization will try to keep the practice that is regarded as one of its advantages (Sanchez Loppacher et al., 2013). Additionally, the companies may have other reasons (certain interests, additional profit or costs, and others) to maintain their operations without any changes.
Penalties and No-Delays Policy at Warehouses
VASA can also introduce a system of penalties for delays. The transportation companies pay their drivers if they have to work overtime, which happens quite often due to dispatch and unloading delays. The two transportation companies note that they often have difficulties with the provision of trucks on VASA’s demand due to the shortage of vehicles (Sanchez Loppacher et al., 2013). They stress that the delays at warehouses tend to lead to delays with other deliveries. VASA should ensure timely dispatch, but it should also negotiate the use of penalties for delays at warehouses. The company should discuss the need to unload trucks timely as this affects other deliveries. VASA should discuss the specific periods of deliveries with its partners, which will help them adhere to their schedules.
The barriers to effective implementation of these solutions are associated with companies’ focus on their cultures and interests. For example, the introduction of penalties may be seen as unacceptable at CristaLog Hnos. and Transfer S. A. that have full- and part-time drivers as well as contract additional drivers when necessary. The transportation companies may concentrate on their potential lack of labor force as drivers will simply avoid cooperating with them. Furthermore, customers may be reluctant to improve their own processes related to unloading, so the shortage of trucks and delays caused by the ineffectiveness of warehouses’ operations will remain a burning issue. Nevertheless, VASA should try to undertake the steps mentioned above if it wants to keep its partnerships with Transfer S. A. and CristaLog Hnos. The glass manufacturer should be ready to invest additional time and funds to improve its supply chain management and relationships with the transportation companies in question.
References
Addo-Tenkorang, R., Helo, P., & Kantola, J. (2016). Concurrent enterprise: A conceptual framework for enterprise supply-chain network activities. Enterprise Information Systems, 11(4), 474-511. Web.
Helo, P., Shamsuzzoha, M., & Sandhu, M. (2016). Cloud-based virtual supply chain. In Proceedings of the 2016 International Conference on Industrial Engineering and Operations Management (pp. 150-155). Detroit, MI: IEOM Society International.
Morana, J. (2013). Sustainable supply chain management. Hoboken, NJ: John Wiley & Sons.
Ross, D. F. (2016). Introduction to supply chain management technologies (2nd ed.). Boca Raton, FL: CRC Press.
Sanchez Loppacher, J., Pancotto, M., & Vera, M. F. (2013). Rethinking distribution logistics at VASA, Pilkington. Harvard Business Review, NA0247, 1-25.