It is amazing when one considers the number of plastics that are produced and consumed annually. Plastic bags contribute greatly to this increasing number of plastics because people are always buying things. Plastic bugs provide the immediate and available material in which shopping can be loaded into.
The large number of waste that is produced by the use of these bags cause such a nuisance during disposal that the life cycle assessment was initiated in plastic bag production to check the use and recycling of plastic bags due to the environmental degradation that is caused by these large numbers of plastic bag waste. The essay that follows intends to focus on the life cycle assessment and its relationship with the recycling and recuperation of plastic.
Plastics contribute greatly to the high numbers of waste, and what is worse, they provide a great contribution to environmental degradation, and therefore, life cycle assessment is a good approach at reducing the numbers of plastic waste in the environment (Dodhiba, Takahashi, Sadaki, and Fujita 2008).
The concept behind the Life cycle assessment is that it is an assessment that looks at the broader picture concerning a product’s life from the time it starts as a raw material to the point where it becomes waste material, including the impact that the particular product has on the environment. That is, whether the environment is negatively or positively affected by the product.
The life cycle assessment consists of a comprehensive analysis of a product from the time when it was a raw material, the period when it was being manufactured, and the purpose of the product, including how it is put to use and finally how it is disposed of.
The use of the life cycle assessment (LCA) is something that businesses that engage in the production of products should put to mind because it ensures that all the products being produced in the market for consumption are environmentally friendly and this goes a long way in ensuring that the environment is protected from environmental degradation.
This situation is threatening to affect the survival of living beings on the earth’s surface due to the greenhouse effect that is brought about as a result of environmental degradation (Astrup, Christensen, and Fruergaard 2009).
Consumers are becoming more and more aware of the fact that there is a higher risk of environmental degradation that is caused by the methods of production being employed by manufacturers in addition to the products that are being produced into the market for consumption.
Because of this consumer awareness, it becomes important for manufacturers to evaluate their methods of production and their products to ensure that they are ecologically friendly. Consumers are therefore demanding the production of products in the market that has a combination of goods that are cost-friendly and are at the same time environmentally friendly and sensitive.
For a knowledgeable and smart manager, this is an opportunity to cease. To ensure that they produce products that are eco-friendly, thus achieving strong grounds for competition in the market against their competitors by ensuring that they market products that are environmentally sensitive.
Various benefits are associated with the LCA apart from the fact that an intelligent manager can use it as a strategy for gaining good grounds against their competitors. Another benefit that is accompanied by the LCA is that it enables a producer to assess the effect that the production of a certain product has on the environment.
This will hence encourage the management to analyze the performance of their product production into the market and to devise measures that would ensure that less damage is being caused to the environment.
However, it should be noted that the LCA is not an instrument responsible for making decisions regarding production, but rather, it should be used to reach a conclusion towards a production method that will ensure that environmentally friendly goods are being produced into the market.
The LCA was initiated in the early 1960s at a period when scientists realized the potential depletion of fossil fuels. The LCA was a strategy that was developed by the scientist with the aim of understanding and finding solutions to the impact that energy consumption has on the environment.
The strategy was later on put to use regarding environmental degradation in the 1980s when the numbers of solid waste were becoming a major concern (Finkbeiner, Wiedemann, and Saur 1998). The strategy was implemented in 1990 in a study that intended to analyze the benefits of using paper grocery bags against plastic paper bags.
LCA utilizes certain principles in ensuring that it covers the life cycle of a product comprehensively. One of the principles that are used by LCA is the life cycle. As mentioned earlier, LCA covers the life of a product comprehensively. This goes back into the extraction of the raw materials that are used in production and the environmental risk that is associated with the extraction of the raw material.
After the assessment of the raw material is done, the energy that is utilized during the manufacture of the product is also analyzed, followed by the use to which the product is put to and lastly, the disposal of the product after use once it becomes a waste product. Another principle that is used by the LCA is the environmental focus.
The product’s impact is evaluated to determine the effect it has created on the environment. The use of the LCA relative and its cause revolves around a functional unit. This forms an integral position in the LCA because all other procedures that follow the use of the information that has been generated relating to the functional unit.
The LCA is an iterative procedure meaning that one phase that was used in the LCA will be used subsequently by another phase. The process continues since information collected at one point is used in the analysis of the next process. This contributes greatly to ensuring that the results obtained at the end of the procedure are reliable and consistent.
Transparency of the whole LCA procedure is important as it provides assurity that the interpretation of the collected data is sufficient and efficient thus making it reliable in reaching a decision that will enable manufacturers to produce something into the market that has low environmental degradation in the extraction of the raw materials, its use and disposal.
The LCA procedures are complex as they consider a number of things such as the impact of the product ecologically, its effects on human health in addition to the natural resources that are used during the production of a particular product.
In the study of LCA, plastics are the most the products that are being put to use the most in the current world. The discovery of plastics has opened a completely new direction and has taken place for the production of many materials.
This is due to the fact that it has many advantages over this other product, such as the fact that it is economical, can be put into many varied uses, its resistance to moisture and another chemical, it has its own negative effects in the environment.
The use of plastics has become so enormous that plastics are currently the tools of environmental degradation when the fact that the product is resistant to decay is brought into mind. The fact that plastic does not decay is enough reason to worry about the companies being produced since many people use their plastics only once, and if these products do not decompose, then where dare they supposed to go.
Most of the plastics that are used by people are prepared by using simple molecules of hydrocarbons and result in the formation of two wide varieties of plastics, which are thermoplastics and the thermosets. Some people might think that the fact that plastics are stable; therefore, there is no risk of poisonous gases being produced in landfills once the plastics are disposed of.
However, considering that plastics do not disintegrate and they are produced in large quantities of almost 100 million every single year, where is this entire heap supposed to go to? (Reap, Roman, Duncan, and Bras 2008).
In addition to the fact that plastics are produced in great numbers, there are many companies that rely on plastic products for the packaging of their finished products. The thermoplastics are the kind of plastics that harden under cool conditions and melt when exposed to high temperatures. Due to this nature, they are the most common plastics that are used as compared to the thermosets.
The thermoplastic is used in the manufacture of both high density and low-density polythene bags. They high-density polythenes are used for a couple of reasons, such as in the formation of bottles that are used to store detergents, other are used to store food products in addition to the production of toys. The low-density polythenes are employed in the manufacture of flexible products and bin liners.
The thermosets are the worst forms of plastics because this has no chance at any form of decomposition because once they are manufactured, there is no method that can be used to either remelt them or remold them. These sorts of plastics are used in making coatings, mattresses, and adhesives among a list of other things.
Due to the realization that people have made regarding the negative effects of these plastics on the environment, a version of degradable plastics has been developed. These are manufactured from the use of plant resources and bacteria. The products are called bioplastics.
Oil is used during the manufacture of plastics, and these accounts for about 4% use of oil for the world stock. Gas and biomass can also be used, but biomass is not commonly used because it is expensive to be used in the production of plastics. However, as much as plastic production uses up a considerable quantity of oil, its corresponding use indicates that more oil is saved than the amount that was used during the manufacturing process.
This can be reflected in the packaging process whereby little energy is required to pack them as compared to other products. Another advantage is that it utilizes the load for every vehicle, which reduces traffic and, therefore, the resultant fuel that would have been used in addition to the emission of, assumes during the transportation (Toloken 1998).
Since the 1950s, the world’s use of plastic products has increased considerately from 5 million tones a year to an unbelievable amount of 100 million tones each year today.
A survey carried out in 2001 in the UK regarding plastic consumption showed that just about 4.7 million tones of plastic goods were utilized in the various economic sectors. Another survey that was conducted in Western Europe confirmed that approximately 33.6 Mt of plastics were consumed in 1999.
A detailed survey which can be shown by the diagram is below shows that the largest amount of plastics is used in packaging, which represents almost 40% of the total use of plastics; 50 percent of this is used in wrapping the packed goods.
This represents almost more than one-third of the plastics produced. From this data, it is clear that packaging provides a major source of waste plastics. The surprising thing is that a good 65% of these plastic waste products are from the household packaging while the remaining bit originates from the industrial world and commerce (Subramanian 2000).
There are six categories of plastics that are used during the packaging process, and this includes PP, PVC, PET, and Ps, but the omnipresent is polyethylene. It is interesting to note that annually, Americans account for the production of 100 billion waste polythene plastic bags, and out of this large number, only 0.6% of them are recycled.
The average consumer can nevertheless contribute greatly in reducing the number of polythenes present in the environment as waste by taking action in the eradication of plastic bags as the only means of carrying shopping (Waste Online 2006).
The building and construction industry utilizes about one-quarter of the plastic produced and in effect, is the second sector with the highest consumption of plastics after packaging. Of this amount, a good 30% is used for insulation purposes while almost half of the plastics are employed in pipelines and ducts; the rest is utilized in the installation of windows and floor covers — the common type of plastic used in the construction industry id the PVD.
The electrical and electronic sector is the third in this category, it uses plastics mainly for cable insulation, and even though the percentage is a bit low, it is expected to increase in the near future (Heyde, Kremer, Holley, 1999). However, as much as the plastics used in the electrical industry is on the increase, the total weight of these plastics used decreases with every unit.
The agriculture sector is another one in which plastic use is employed in horticulture and in the livestock activities. The problem with farm plastics is that they are contaminated with soil and therefore prove to be quite expensive to do away with. Most of the plastics used on farms are mainly PP and PE.
In the Automotive sector, plastics account for about 10% of the total materials used in cars and of this only 3% is recycled. Most of this waste was from PP mostly from battery casings, but the general use of PPs is expected to increase in the near future for use in car interiors.
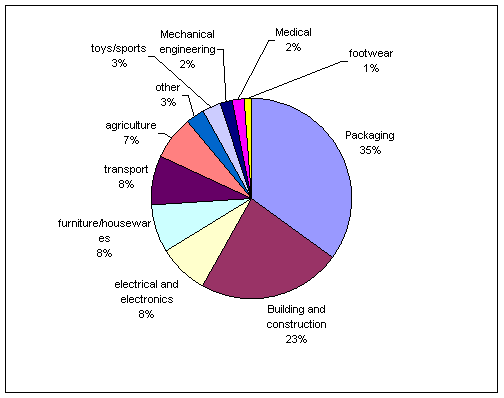
Plastics have environmental impacts, which have varying effects depending on the type of plastic that is being produced and used.
During the manufacture of plastics, considerable amounts of fossil fuels are used. In addition to this, there are a lot of chemicals that are used during manufacture, and as a result, there is a considerable amount of fumes that are emitted into the air, not to mention water and the waste products generated in the production process.
The transportation of the raw materials that are used in the production of plastics also contributes to environmental degradation, but as mentioned earlier, the transportation of the finished products does not result in a lot of fume emission (Meadows, Meadows, and Randers 1972).
Plastics are manufactured by the formation of polymers, which are a group of hydrocarbons. During the manufacture of these polymers, there are large emissions of chemicals that have a high potential for environmental degradation (Goldsmith and Allen 1972).
Most of the emissions that are not eco-friendly are organic products, which are volatile in nature, such as benzene, some of which are toxic substances. However, there have EU VOC emissions in polymerization now account for about 0.5% of the total emissions.
Although plastics are in high demand in almost all sectors, their weight is considerably small as compared to the total waste produced by other non-plastic products. Plastics account for only 1% total by weight of the total waste. In research conducted in Western Europe in 1999, 32% of the total plastic waste was recycled while the rest was landfilled.
In the other parts of the world, such as the US, a number exceeding 80% of the total population in 1999 had access to the facilities that deal with plastic recycling. In the United States, the average plastic recycling rate has stabilized at 23%, and as a result, the American market has more than 1,300 plastic products whose contents are recycled. This is a good move that supports the life cycle analysis.
This mechanical recycling method is most suitable for those plastic materials that are relatively clean and readily available at the same time. Europe utilized the mechanical recycling method, and in the process, they recovered about 9.4% of the plastic that had been previously used. Germany was the leading country as they recovered about 18% of the total plastic waste they had used in 1999 (Tukker 2002).
There are two types of plastic collection methods for the recycling of used plastic, and this is the kerbside or the bring-bank. Irrespective of either method, mechanical recycling is of great benefit only if the recyclate in use substitutes the virgin polymers.
The collection scheme design is the main determinant of the level of impurities present in the polymers. Feedstock recycling has similar benefits to the environment as that of energy recovery, but the difference is that it is more costly than energy recovery.
However, despite the fact that they are clean and relatively efficient, modern energy recovery is environmentally friendly than either the mechanical or feedstock recycling methods. Modern plants offer better energy recovery advantages over the use of landfills. The diversion that was brought about by eradicating the use of landfills has a positive influence in the direction of plastic waste recovery.
The plastic industries in North America utilized the concept of plastic recycling, and there was a remarkable increase in demand for recycled plastic products. The plastic products generated from this recycling include fleece clothing, garden equipment, and equipment used in the playgrounds. The consumers in this part of the world have encouraged the production of outdoor furniture that has been made by using recycled plastic materials.
Feedstock recycling is a method whereby plastic waste is converted back to raw materials that can be utilized as secondary feedstock in plastic industries such as processing plants, petrochemical plants, and chemical reactors.
Another use for this plastic is that it can be used as a monomer for the manufacture of other new plastics such as the PMMA and PET that are depolymerized and converted back to monomers that are made to go back through the polymerization loop.
Other methods of recycling, such as the gasification can be used. This method uses synthetic gas that is produced in the blurts furnaces in the process of steel production or another way in which the synthetic gas can be obtained is as a raw material for the production of methanol, which leads to the subsequent production of a new polymer.
Another option that can be used in this case is the pyrolysis in which oxygen is not used while heating plastics. This results in ton the breakdown of long-chain polymers into reduced molecules (Umberto, Mastellone, and Perugini 2003).
Instead of burning up the plastics in landfills, they can be put into good use because they have a high calorific content, which can be recovered most of the time and become a useful source of heat. In respect to these, cement kilns sometimes utilize waste elastics as a fuel resource. In the diagram below, plastic waste obtained after use is shredded, and after this, a solvent is added in order to recover the useful plastic.
The other waste that remains in the system has a high calorific level since plastics are manufactured oil, which has a high calorific level. The recovery process helps in saving energy that would otherwise have been wasted.
In this system, the solvent that was used could be recovered, and since the recovery requires a lot of energy, the energy is obtained from the waste plastic that was not used in the system. In this way, the energy that as used to make the plastics are recovered instead of being wasted while making new plastics instead of recycling the already existing ones. This method considerably reduces the amount of plastic waste found in landfills by about 5.4%.
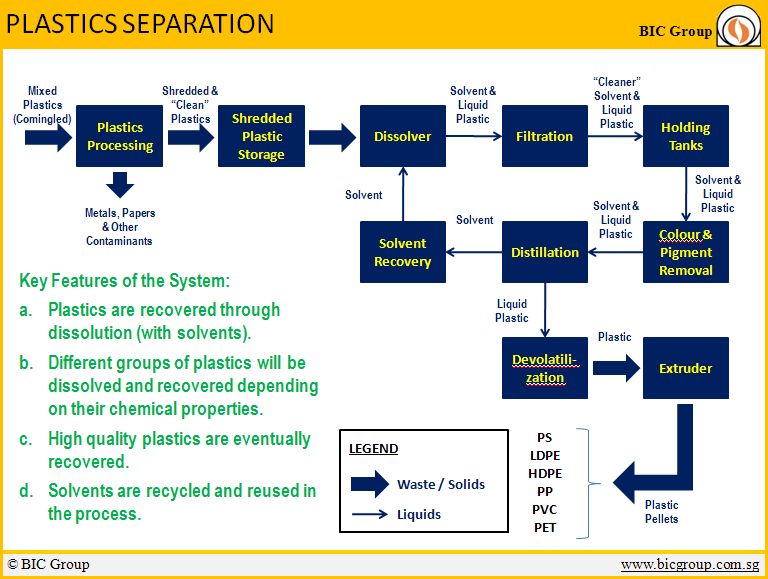
Environmental concern has been raised over the incineration of particular plastic waste products. These concerns have been raised especially about the PVC, which results to the generation of dioxins, which are enduring forms of organic materials that have a high potential of being toxic, and at the same time, they are perceived to have carcinogenic effects in addition to the fact that they are bio-accumulators.
In other processes such as MCW incineration, the fact that chlorine is present leads to the formation of dioxin (Dilli 2007).
However, there has been a remarkable reduction in the percentage of dioxin being released into the atmosphere, and they currently account for only about 3% of the dioxin emissions being experienced in the United Kingdom.
The current emission of dioxins being emitted in the atmosphere has greatly reduced such that a direct correlation cannot be found between emissions and chlorine contents.
Policies are being devised worldwide that demand the use of better ways to ensure that raw materials do not get depleted and at the same time, the environment to be considered as a vital part during the production process. This is where the life cycle assessment comes in.
Once the LCA is incorporated in the decision-making process, a good understanding in regard to human health requirements will be achieved in addition to the different environmental impacts of different production processes that are utilized by managers.
Previously, the methods of production and the consequences they have on the environment were not considered as part of the decision-making process since individuals were not aware of the detrimental effects of the emissions that result from industries (Ackerman 1997).
The life cycle assessment provides valuable information to producers and manufacturers that would help them in fully analyzing the impacts that are brought about when making decisions that concern their products and the effects these products have on the environment after their production in the processing firms.
Production managers should remember that LCA one of the tools that should be used in the decision-making process. They should, therefore, be utilized in the decision making process together with other criteria used during decision making e.g., expenditure and performance. The use of the life cycle assessment will enable the production managers to make informed decisions that are well balanced (Worldwatch Institute 2008).
The use of plastics generally reduces the materials that are needed by the many sectors in the market. The advanced procedures used in the manufacture of plastic materials such as engineering and differentiation reduces the chances that plastics would be recycled mechanically, which reduces the incidences of recycling plastics mechanically, thus causing little or no environmental degradation.
Other methods of plastic recovery methods do not pose grave dangers to the environment as much as the mechanical method does. It is currently the general rule that waste management has become the top objective above other alternatives because it ensures that there is waste minimization.
The creation of secondary raw materials through the use of the feedstock recycling method is one of the best methods to be used where appropriate, as it proves to be one of the best ways of managing plastic waste products in an eco-efficient manner.
This, together with the incorporation of the life assessment strategy, will ensure that there are fewer emissions in the air that result in environmental degeneration due to the large numbers of plastics waste products in the environment.
List of Reference
Ackerman, F., 1997. Why Do We Recycle?: Markets, Values, and Public Policy. San Rafael, California Island Press.
Astrup, T., Christensen, H.T., and Fruergaard, T., 2009. Recycling of plastic: accounting of greenhouse gases and global warming. Waste Management & Research, 27 (8), pp. 763-772
Bicgroup. Incineration and plastic recovery.
Dilli, R. 2007. Comparison of existing life cycle analysis of shopping bag alternatives. Final report. Melbourne, Australia: Hyder Consultancy Pty Ltd.
Dodhiba,G., Takahashi,K., Sadaki, J., and Fujita, T., 2008. The recycling of plastic wastes from discarded TV sets: comparing energy recovery with mechanical recycling in the context of life cycle assessment. Journal of Cleaner Production, 16, pp. 458-470
Umberto, A., Mastellone, M. and Perugini, F., 2003. Life Cycle assessment of a plastic packaging recycling system. The international journal of life cycle assessment, 8 (2), pp. 92-98
Finkbeiner M, Wiedemann M, and Saur, K.,1998. A Comprehensive Approach Towards Product and Organisation Related Environmental
Management Tools. Life Cycle Assessment (ISO 14040) and Environmental Management Systems (ISO 14001). Int J LCA 3 (3), pp. 169–178
Goldsmith, E., and Allen, R., 1972. “A Blueprint for Survival.” The Economist 2(1).
Heyde, M., Kremer, M., Holley, W., 1999. Recycling and Recovery of Plastics from Packagings in Domestic Waste. LCA-Type Analysis of Different Strategies. Bayreuth: Eco- Informa Press.
Reap, J., Roman, F., Duncan, S., and Bras, B., 2008.A survey of unresolved problems in life cycle assessment. Part 2: impact assessment and interpretation. Int J Life Cycle Assess, 13, pp. 374-388
Meadows, D., Meadows, D., and Randers, J., 1972. Limits to Growth. New York: Universe Books.
Subramanian, P.M., 2000. Plastics recycling and waste management in the US. Resource, Conservation and Recycling, 28, pp. 253-263
Toloken, S., 1998. Plastic bottle recycling rate keeps sliding. In: Plastics News, August 24, 1998, p 1.
Tukker, A., 2002. Plastics Waste – Feedstock Recycling, Chemical Recycling and Incineration. Rapra Review reports, 13 (4)
Waste Online. 2006. Packaging recycling information sheet.
Worldwatch Institute., 2008. Plastic bags.