Although manufacturing and service companies are different in their purpose, both manufacturing and service environments prompt companies to rely on established processes to deliver their products or services to customers in the most efficient way possible. The concept of operations management describes the processes which are included in the production of a product and its delivery to the customer (Boyer and Verma xvii).
The concept of service operations management addresses the same processes in the service environment (Boyer and Verma xvii). These processes can be visualized through process maps or flowcharts to help managers to achieve greater supply chain integration with suppliers and customers. In this paper, the manufacturing and service processes are outlined for two companies, the smartphone division of Lenovo Group Ltd., and logistics services company DHL Express. Also, differences and similarities between manufacturing and service environments are described.
Lenovo is a Chinese technology company, one of the biggest personal computer vendors. In addition to personal computers, Lenovo produces servers, smart televisions and mobile devices such as smartphones and tablets. The smartphone division of Lenovo Group Ltd. primarily manufactures Android smartphones under brands Lenovo and Motorola (“Motorola Mobility LLC” par. 3). The manufacturing process of Lenovo smartphones is done by a traditional method of the production line and includes the following steps: production and quality testing of motherboards, assembly and testing of smartphones, packaging and storage (Murray par. 2; Schooter pars. 12-15; “Inside Lenovo – HQ & Factory Tour”).
DHL Express is a global provider of logistics and transportation services. In its essence, the business of DHL Express is built around the delivery of goods from one place to another through its network of logistics facilities. Currently, DHL offers international express delivery services, freight forwarding, logistics, and supply chain services. DHL operates in more than 220 countries worldwide and encompasses “the business units DHL Express, DHL Parcel, DHL eCommerce, DHL Global Forwarding, DHL Freight, and DHL Supply Chain” (“Company Portrait” par. 1).
The service process of DHL includes order transmission, order preparation, and execution, shipment consolidation, dispatch and delivery (“Information flow from the order to delivery” par. 1; Zhu 18;). Other elements might be included if customs services or other value-added services are required by the customer (“Value Added Services” par. 2).
There are differences and similarities between the manufacturing and service industries. The main difference is in the output: manufacturing companies produce tangible goods, while service companies provide services. For example, the mobile division of Lenovo produces smartphones, and as such, it has to establish a supply chain to purchase necessary components and create and maintain facilities where goods are produced. Because manufacturing firms are making profits by selling goods, they have to produce them in advance and maintain warehouses where the supply of goods can be stored.
Service industries do not have to produce anything other than service, and therefore, only the infrastructure to support service operations is required. In the case of DHL, this infrastructure is the global network of logistics facilities and warehouses, as well as the IT network for parcel tracking. Another difference is the fact that in the manufacturing environment, a company’s management has to forecast the demand for goods and adjust production volumes accordingly. In a service environment, services are offered in response to demand. Some forecasting is required to predict the demand to build the necessary infrastructure and allocate an adequate amount of personnel, but if the infrastructure to support service operations is established, other variables can be adjusted on the fly.
There are similarities between the two industries. Generally speaking, customer-induced variability has an effect on the performance of both the manufacturing operations and service operations performance, albeit in different ways. If customers do not buy Lenovo smartphones, the company will have to cease production to limit financial losses. If customers buy the company’s smartphones but are not satisfied with their quality, they are likely to penalize the company and Lenovo will have to make some changes to its production pipeline.
In the case of DHL, the company is affected the same way, if customers are not satisfied with delivery times, they are likely to choose another courier company and DHL will have to change its service operations to meet customers’ demands. Also, within the service industry customer-induced variability has an immediate effect on the company’s service operations, and certain measures are to be implemented to compensate for it. For example, a DHL courier might not be able to deliver a parcel because the recipient does not answer the phone. If this is the case, the company’s service operations process has to include a regulation that will outline what the courier has to do in such cases.
As a manager, I must have a thorough understanding of both manufacturing and service environments. For example, the management of the company is responsible for developing operations strategy and an efficient supply chain strategy to achieve certain strategic or competitive priorities. Both manufacturing and service companies rely on efficient operations management to deliver their products or services to customers at the lowest cost possible. If I am in charge of developing an operations strategy for a service company, I have to understand the specifics of the service environment, and vice-versa for the manufacturing environment.
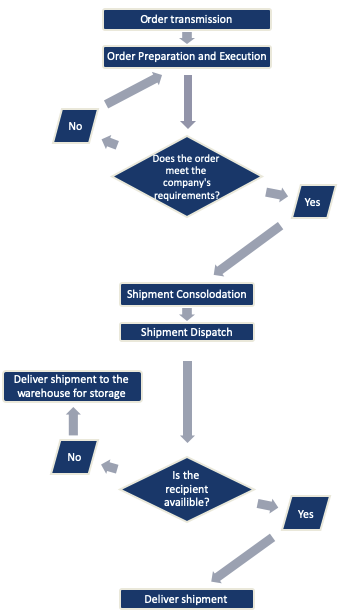
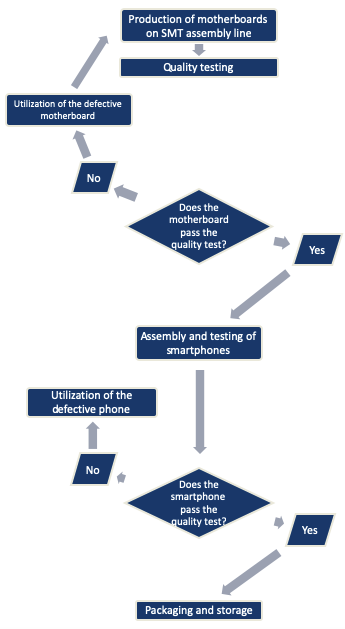
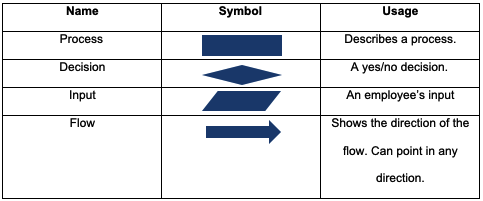
Works Cited
Boyer, Ken, and Rohit Verma. Operations and Supply Chain Management for the 21st Century, Boston: Cengage Learning, 2009. Print.
Scooter, Nicole. Behind the Scenes at Lenovo – How a Smartphone is Made. 2014. Web.
Zhu, Hanzheng. Logistics System and Process in Express Delivery Service Companies. 2010.
Inside Lenovo – HQ & Factory Tour 2014.
Company Portrait n.d.
Information flow from the order to delivery n.d.
Value Added Services n.d.
Murray, Martin. Manufacturing Process. 2016.