Introduction
Creating the environment in which employees will be able to excel in their performance is an absolute necessity for an organization to exist and, in the best-case scenario, thrive in the context of the contemporary global economy. Therefore, the introduction of a cohesive and efficient measurement system must be viewed as an absolute necessity. For these purposes, a deep understanding of the essential concepts and phenomena related to the subject matter is required.
Gage Repeatability
Gage repeatability is the measurement element that indicates whether inspectors are consistent when evaluating the same parts of the performance. For example, the difference in measurements of a set of identical items, such as the length of certain parts of details in the toy factory, can be viewed as a gage repeatability evaluation. Similarly, the variations in the assessment of the number of fats in produced meals can be considered an example of gage repeatability. The gaps between measurements of the number of lags in video games can also be interpreted as an instance of gage repeatability (Kubiak & Benbow, 2009a).
Gage Reproducibility
Gage reproducibility is another part of ANOVA that indicates differences between the measurements of the same items performed with the help of a specific device. For instance, the gap between the measurement results performed by the same speed gun on the same vehicle running on a specific speed (e.g., 60 mph) should be viewed as an example of gage reproducibility. The difference between the measurements of the length of a particular detail with the help of different tools (e.g., a tape and a ruler) due to the imperfections in the design thereof can be considered another example of gage reproducibility (Kubiak & Benbow, 2009b).
SIPOC Diagram
The SIPOC Diagram, in its turn, translates to Suppliers, Inputs, Process, Outputs, and Customers (Kubiak & Benbow, 2009c). The diagram is used to map the essential stages of the quality improvement process and identify its components successfully. As Figure 1 below shows, the SIPOC Diagram can be used to improve the quality of a food manufacturer.
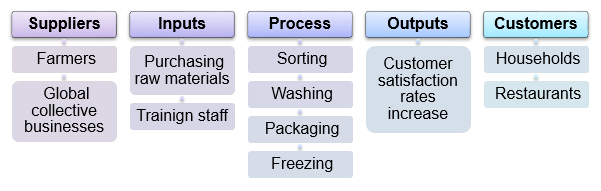
Similarly, the SIPOC Diagram can be applied to other environments, such as the area of healthcare. Figure 2 below provides an example of locating the crucial stages of improving service quality in a nursing facility.
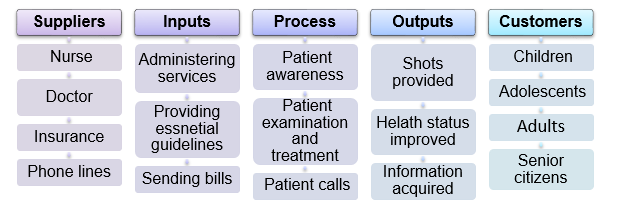
Finally, the diagram can be applied to promote quality improvement in a household. For example, feeding a cat can be considered from the SIPOC perspective. The premise might be viewed as grotesque, yet it still follows the essential principles of the SIPOC quality improvement (see Fig. 3).
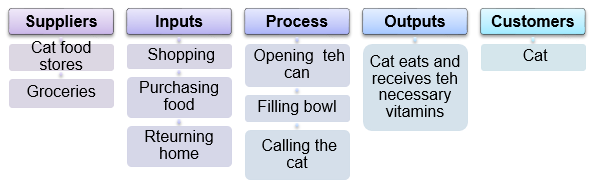
Discrete Distributions
A discrete distribution is a statistical tool that helps identify the probability of occurrence of the values related to the discrete random variable (Kubiak & Benbow, 2009d). For example, supposing, there is a box with twenty pairs of black socks in it (left labeled as L, right labeled as R). Supposing, one pulls a sock out of the box two times. The possible outcomes include LL, RR, RL, and LR. The random variable X can only take the form of 0, 1, or 2 and, therefore, is discrete (Kubiak & Benbow, 2009e). Thus, the probability distribution is discrete. A similar experiment can be done with candies of two colors (e.g., red and white ones), etc.
Continuous Distributions
A continuous distribution implies the use of variables that can be characterized as continuous and, therefore, can be represented by any value (Kubiak & Benbow, 2009f). For instance, identifying the possibility of a vehicle fracture occurring at a particular temperature can be deemed as a continuous distribution.
Conclusion
By focusing on the identification of the crucial factors that define the success of product quality measurement, one is likely to create prerequisites for the rapid progress of the organization. Removing effects and enhancing the QA processes is imperative for increasing product quality and, thus, developing a competitive advantage that will propel the firm to the top of the global market. As soon as the quality-related issues are addressed, the staff’s performance rates can be increased significantly.
Reference List
Kubiak, T. M., & Benbow, D. W. (2009a). Chapter 18: Process characteristics. In The Certified Six Sigma Black Belt handbook (2nd ed.) (pp. 80-89). Milwaukee, WI: ASQ.
Kubiak, T. M., & Benbow, D. W. (2009b). Chapter 19: Data collection. In The Certified Six Sigma Black Belt handbook (2nd ed.) (pp. 90-94). Milwaukee, WI: ASQ.
Kubiak, T. M., & Benbow, D. W. (2009c). Chapter 20: Measurement systems. In The Certified Six Sigma Black Belt handbook (2nd ed.) (pp. pp. 95-121). Milwaukee, WI: ASQ.
Kubiak, T. M., & Benbow, D. W. (2009d). Chapter 21: Basic statistics. In The Certified Six Sigma Black Belt handbook (2nd ed.) (pp. 122-137). Milwaukee, WI: ASQ.
Kubiak, T. M., & Benbow, D. W. (2009e). Chapter 22: Probability. In The Certified Six Sigma Black Belt handbook (2nd ed.) (pp. 138-166). Milwaukee, WI: ASQ.
Kubiak, T. M., & Benbow, D. W. (2009f). Chapter 23: Process capability. In The Certified Six Sigma Black Belt handbook (2nd ed.) (pp. 167-182). Milwaukee, WI: ASQ.