Introduction
The world of business in the twenty first century is getting more and more competitive as time goes by. The concept of globalization and free trade has only increased the issue further. This is true for any sector in the market which includes manufacturers, retailers, wholesalers, and service providers. In such a scenario, organizations have to become very efficient and competitive in order to survive and grow. One of the key elements that contribute to this is the management of its supply chain. This paper is a review of the supply chain management process in a shoelace manufacturing company. The assignment will draw out a supply chain process map for the product. In the process, the following factors like key problems faced, the background of the situation, the concept, the relent statistics and possible solutions will be given.
Supply chain management
All well managed organizations take the concept of supply chain management very seriously. The level of complication will vary depending upon the type of activity and the size of operations for a company. The concept of supply chain management as a discipline is not very old. This concept was first thought of by a person called Forrester way back in 1958, even though the name of supply chain management came about only later. This visionary wrote that “Management is on the verge of a major breakthrough in understanding how industrial company success depends on the interactions between the flows of information, materials, money, manpower, and capital equipment.” (John et al 2001, p.1). The study of the above concept as a discipline in itself called supply chain management came about only in the last ten years or so. The journal article in which the above statement by Forrester was given also states that supply chain management is viewed as a process, a management philosophy or just a management of the movement of goods and services by different people. As a process, the Council of Logistics Management has defined supply chain management as “The process of planning, implementing, and controlling the efficient, cost-effective flow and storage of raw materials, in-process inventory, finished good, and related information from point of origin to point of consumption for the purpose of conforming to customer requirements.” (Levi and Kaminsky 2004, p.3). A simple supply chain diagram is given below:
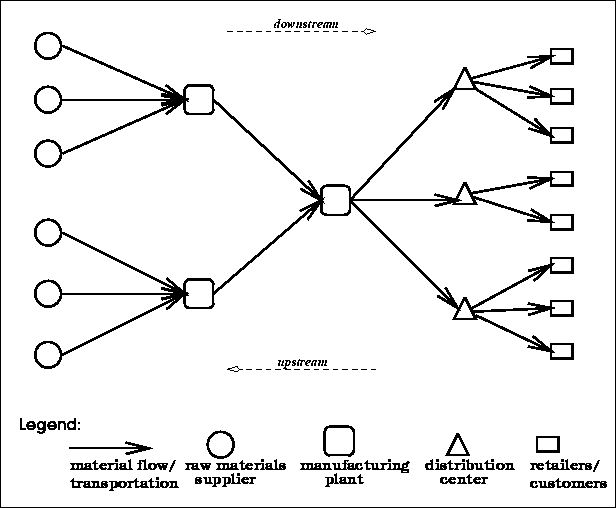
The Shoelace Company: The Company in question is a shoe lace manufacturing concern located in the United States. The company has a single manufacturing base, situated alongside its administrative and head office. There is no retail marketing for the company and its only customers are two major shoe manufacturers. The manufacturing process is fairly simple. Three types of yarn are used namely cotton, polyester (both textured and spun), and polypropylene. The piece at each end which allows easy insertion into the hole (eyelet) in the shoe is called aglet and is usually made of plastic (metal was used earlier). The gum acetone is used to bind the aglet to the lace. Several types of machinery are needed to finish the whole process. The braiding machine will braid the yarn first. Then a machine will apply the glue and another will cut the long lace into the requisite size. Next a machine will fix the aglet at each end, after which they are paired and packaged as a unit (two laces). Finally each unit is bundled and packed into boxes which are now ready to be shipped. (Bryk 1998, p.2).
Each box contains 100 pairs. The supply chain consists of the following players apart from the company itself. They are the yarn supplier, dye suppliers, the aglet suppliers, transportation and logistics service providers, the customers, acetone suppliers, and packing material suppliers. The retailer and the end customer are beyond the control of the company and hence not considered a part of the supply chain in this case. The machine has the capability to manufacture 150 individual laced every thirty minutes. In an hour, 150 pairs (one set) can be manufactured. The company works for only one shift and hence the daily production will come to approximately 1,500 pairs. The internal and external supply chain maps of the company are given in the appendix.
The problem: The Company supplies laces to two major manufacturers. It is to be noted that the manufacturers also use other lace suppliers since the current capacity is not enough to cater to the completed needs. Approximately 44,000 pairs are shipped out at the end of every month in rented trucks to the shoe (both) manufacture’s premises which lies in a radius of 25 miles from the company’s plant. Both shoe manufacturers buy around half each of the monthly production. In such a scenario, the company does not have any excess stock at the end of each month apart from 1000 pairs that are damaged during the production process. The problem occurred when the company received an emergency order for 45,000 pairs. The increase resulted due to the holding of two mass marathons in the country, the New York marathon, and the Boston marathon. About 100,000 and 22,000 people participate in the New York and Boston Marathons respectively. The shoe manufactures calculated that an additional 75,000 pairs would be needed in total. They faced an emergency because one of their regular suppliers had gone out of business and another company agreed to supply only 25,000 pairs. They contacted the company about 45 days in advance of their requirements and it was agreed that the supply could be produced and delivered if an additional shift with temporary workers were taken for 45 days. An unexpected flooding damaged the plant of the yarn manufacturer and they expressed their inability to supply the additional yarn required for production. The normal supply was supplied by the yarn company out of existing stock and outside purchases.
The background of the supply chain management system in the Shoelace Company
All raw materials are delivered to the company by suppliers themselves and hence transportation and insurance is included in their selling price. After the manufacturing process is complete, the company delivers the product to the two shoe manufacturers in rented vehicles. The cost of transportation and insurance is included in the price of the laces. Both supplies (of raw materials) and deliveries (of finished products) happen every month and are fixed. In normal circumstances, the quantities are fixed in both cases and do not vary from month to month.
The concept
The supply chain management system within the company is based on the concepts discussed below.
Supply chain decisions
The first step in planning a supply chain management system is the decision to set up a particular system that will ensure the smooth flow of raw material and finished products at minimum cost. The whole supply chain process for the Shoelace Company is simple and uncomplicated since it is a single product firm. There are two categories into which this decision process can be divided, namely strategic and operational. (Ganeshan and Harrison 1995). As the name suggests, strategic decisions are taken over a long period of time. “Beginning at the strategic level, a company must address such key issues as overall corporate objectives, market share and profitability goals, business and product mix, etc.” (Framework for Continuous Distribution and Supply Chain Performance Improvement: A Supply Chaining Framework. 2007).
Strategic decisions are usually taken for a period of three to five years in advance and will not change unless absolutely necessary. Of course, minor adjustments can be made. It could also change if some technology or other factor that can have impact on the cost comes about. Production level planning, the required raw material, the logistics involved, delivery of finished products etc must be taken into consideration. In the case of the Shoelace Company, the decision was to ask the suppliers (of raw materials) to handle the issue of transportation themselves. It would have entailed a slightly higher cost, but it can be offset by reduction of at least one personnel for the company. The suppliers were decided on by assessing their reliability, quality and cost of products. Operational decisions are more related to the day to day activities of the company and may change occasionally. For example, the time of delivery may be changed for raw materials. Another example would be changing of the transportation provider in favor of another company. All supply chain decisions are divided into four distinct areas namely, location, production, inventory and transportation. (Logistics Management: An Introduction to Supply Chain Management. 2008). The location of the plant of the Shoelace Company was decided on due to its proximity to suppliers and customers. The production capacity was planned according to the demands from customers. A change in strategic decision may come about because the company is now nearing full capacity production. Inventory is minimized and is delivered every month. Practically no inventory of raw materials and finished goods exist at the end of each month. Transportation is fairly simple and only requires one mode of transport both from the suppliers and to the customers.
Risk factors
Certain risk factors also exist within a supply chain management system. They can be classified into external and internal risks. (Supply Chain Risk Management. 2005). External drivers of risk can be due to demand, supply or the environment. In demand and supply, availability of raw materials, unexpected price increase, shipment delays etc can occur. (Aberdeen et al. 2008).
In the present scenario, both demand and supply risks have been present. In a way, environmental risk is also there because the conducting of the marathon is something beyond control of the company. Internal risk drivers are processes and controls. In this case there no risk in both cases since the problem is totally external. If the company had the required raw materials, the order would have been completed without much of a problem.
Table 1. Statistics
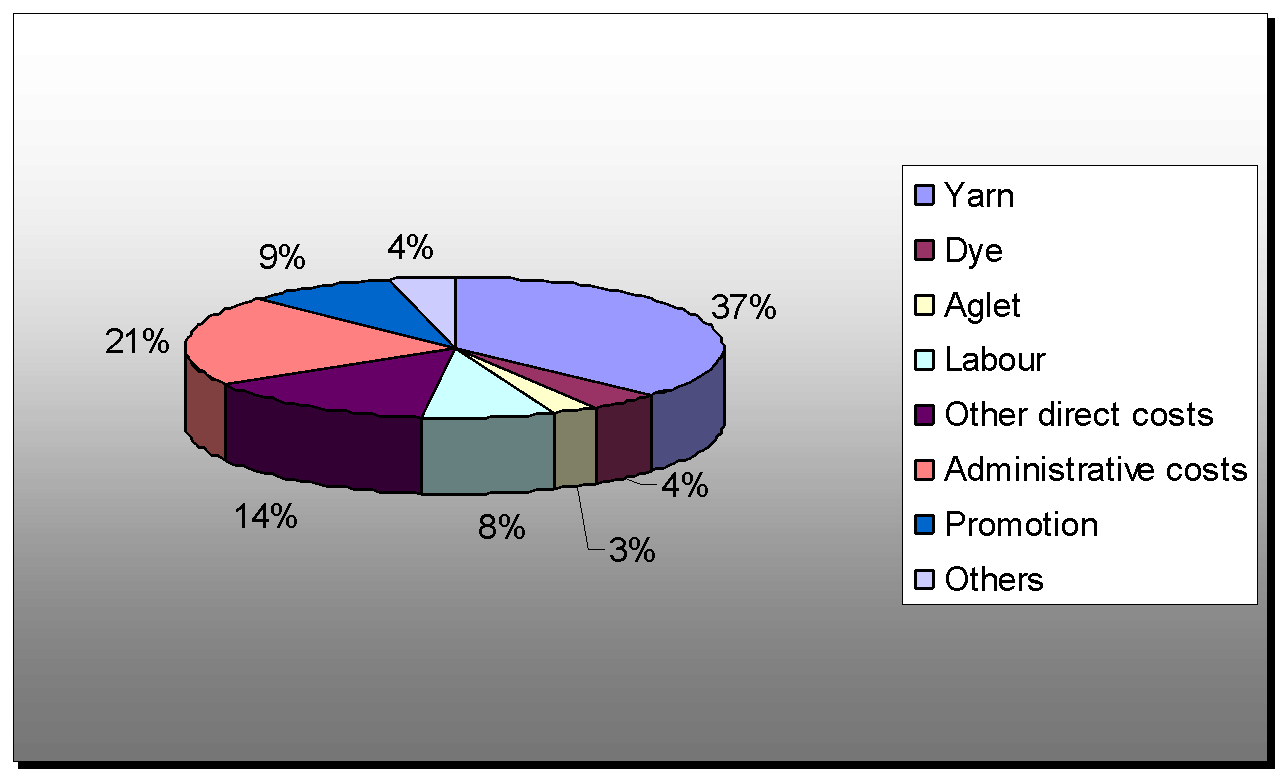
Table 2. Chart showing cost components of 100 pairs of laces
(Normal profit)
The solution
The only solution in this case was to find a new supplier of yarn. This was done, but at additional cost in the price of yarn. The company had to pay 25% over the usual price enjoyed by the company.
(Profit in current scenario)
Net reduction in profits: 13,500 – 8,505 = 4,995
% reduction in profits: 4,995/13,500 x 100 = 37%
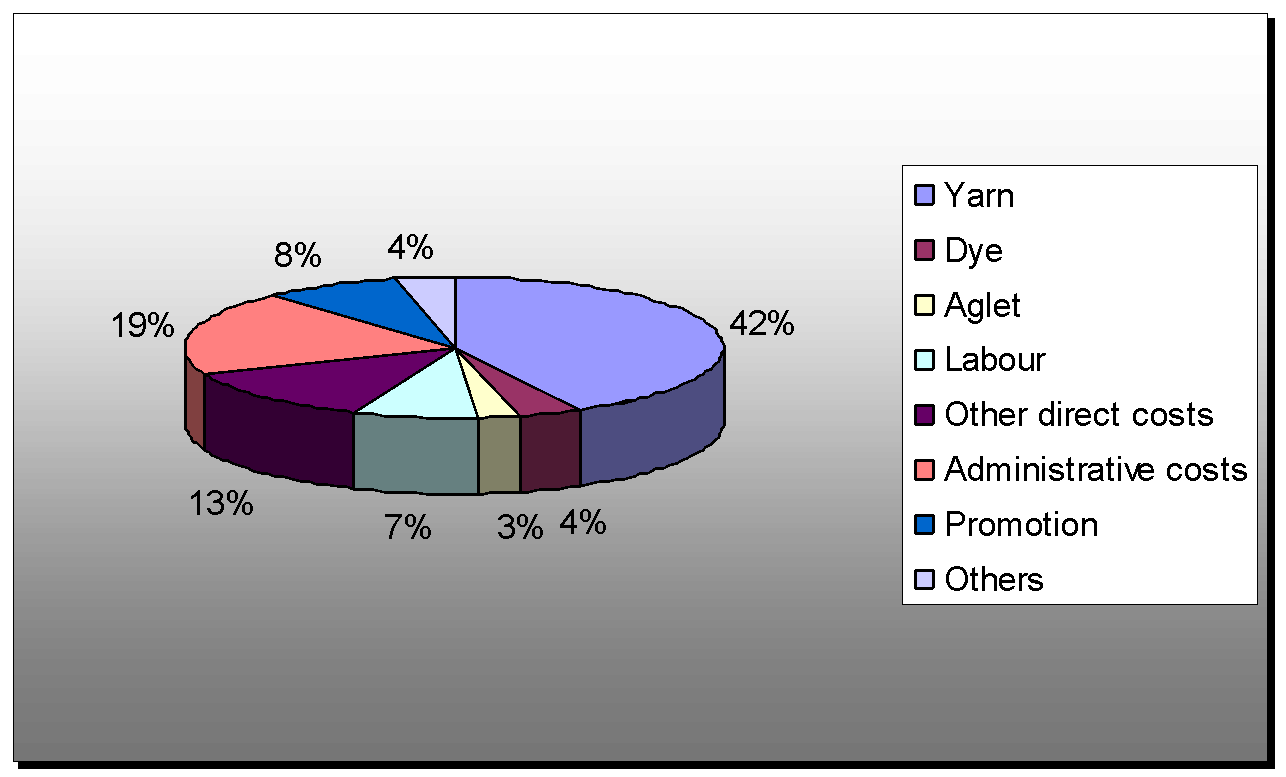
Appendix
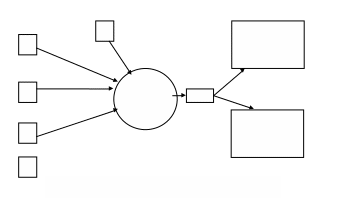
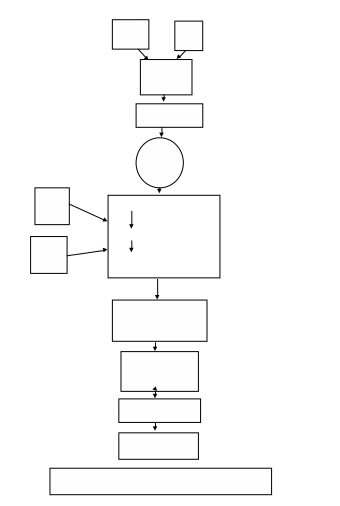
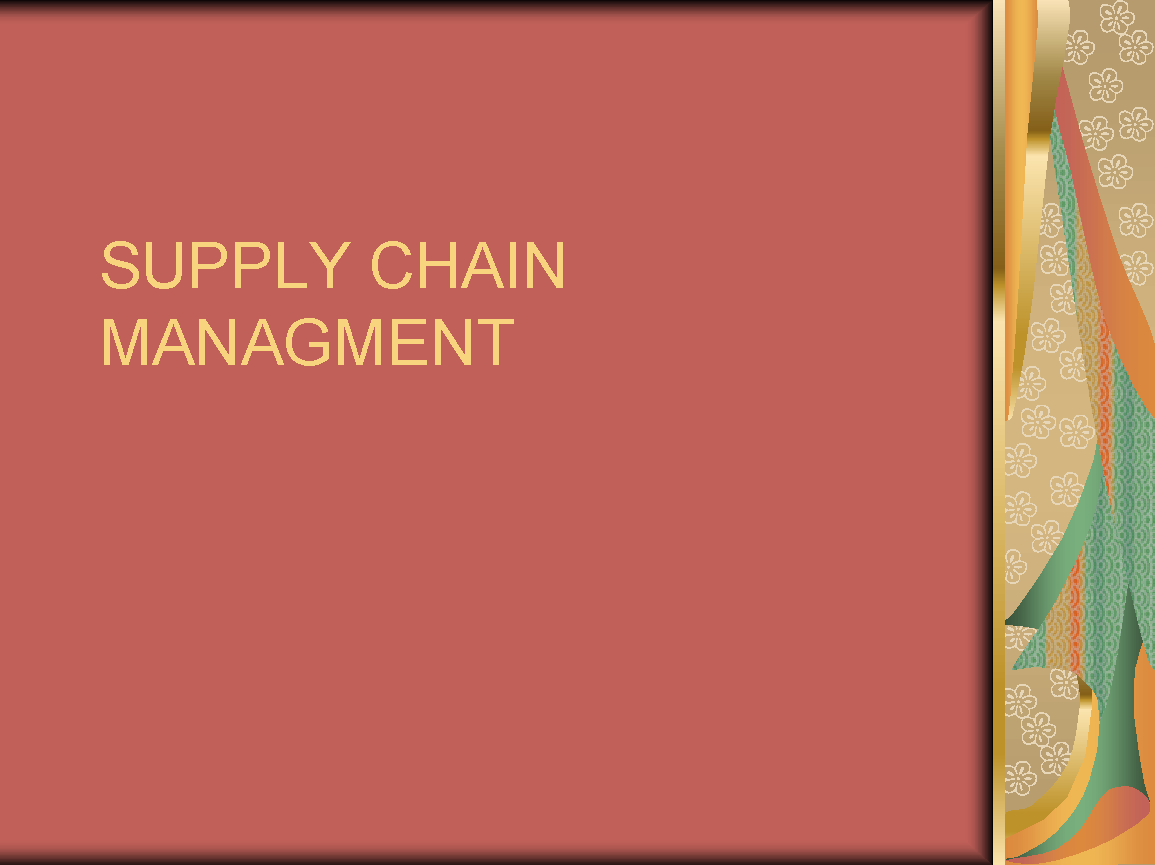
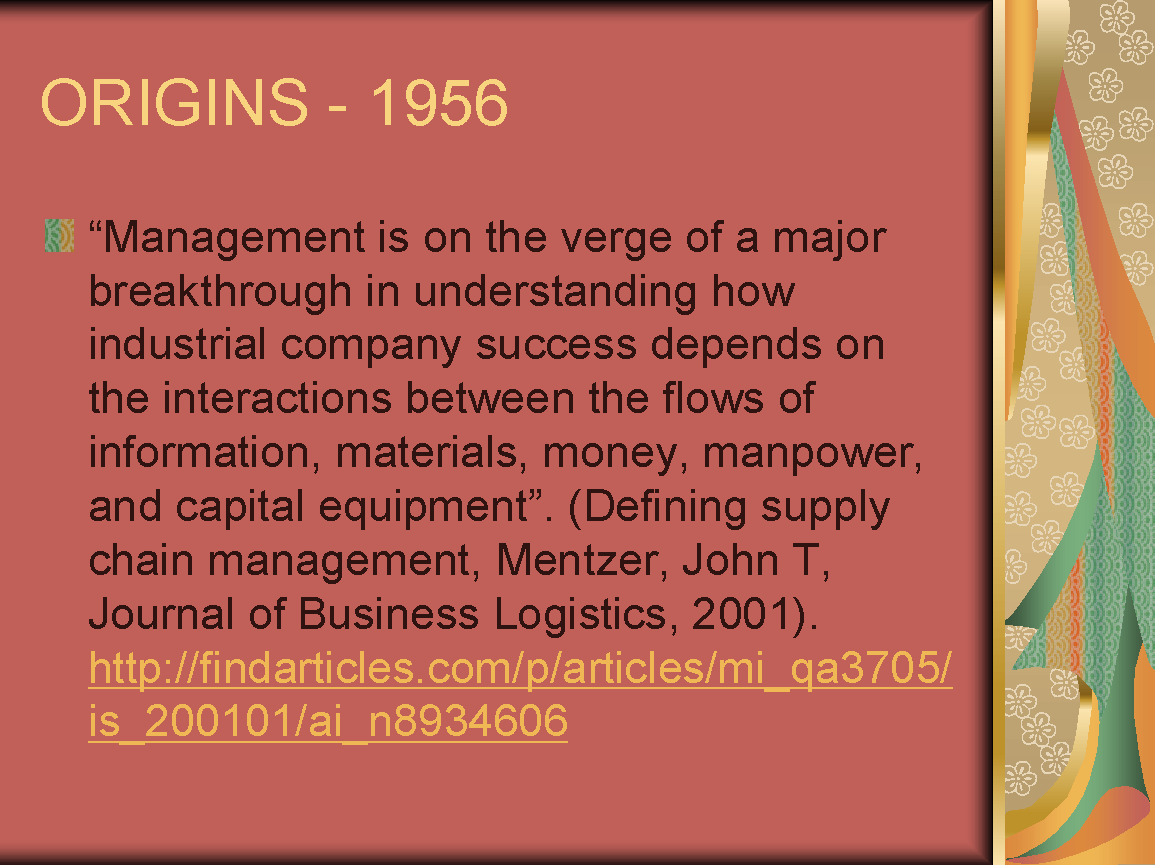
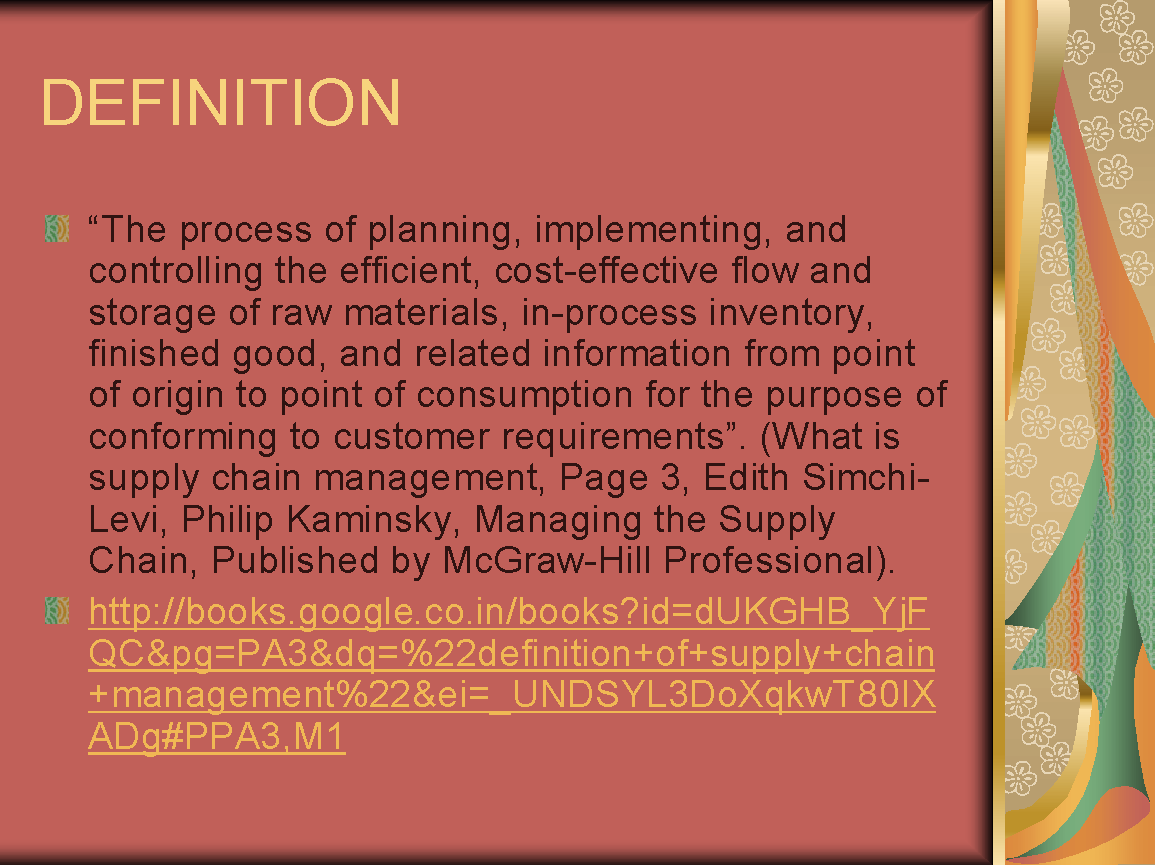
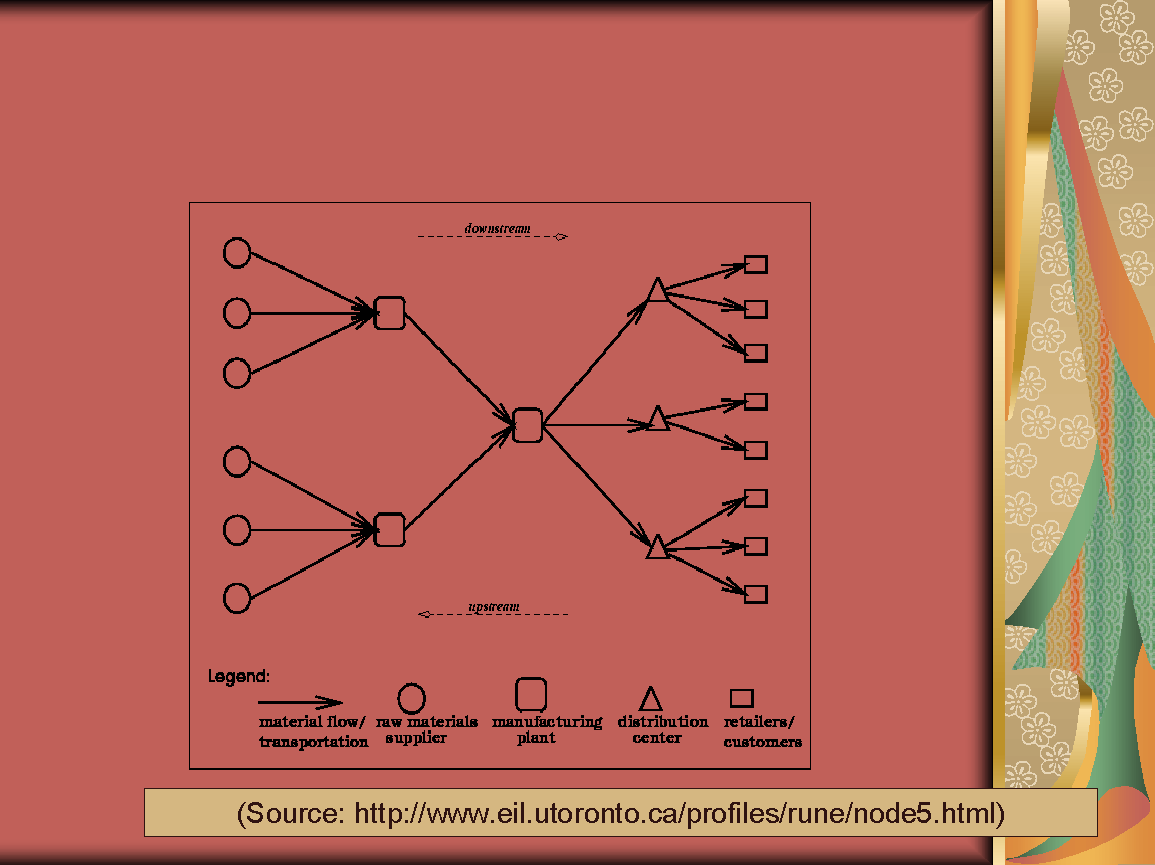
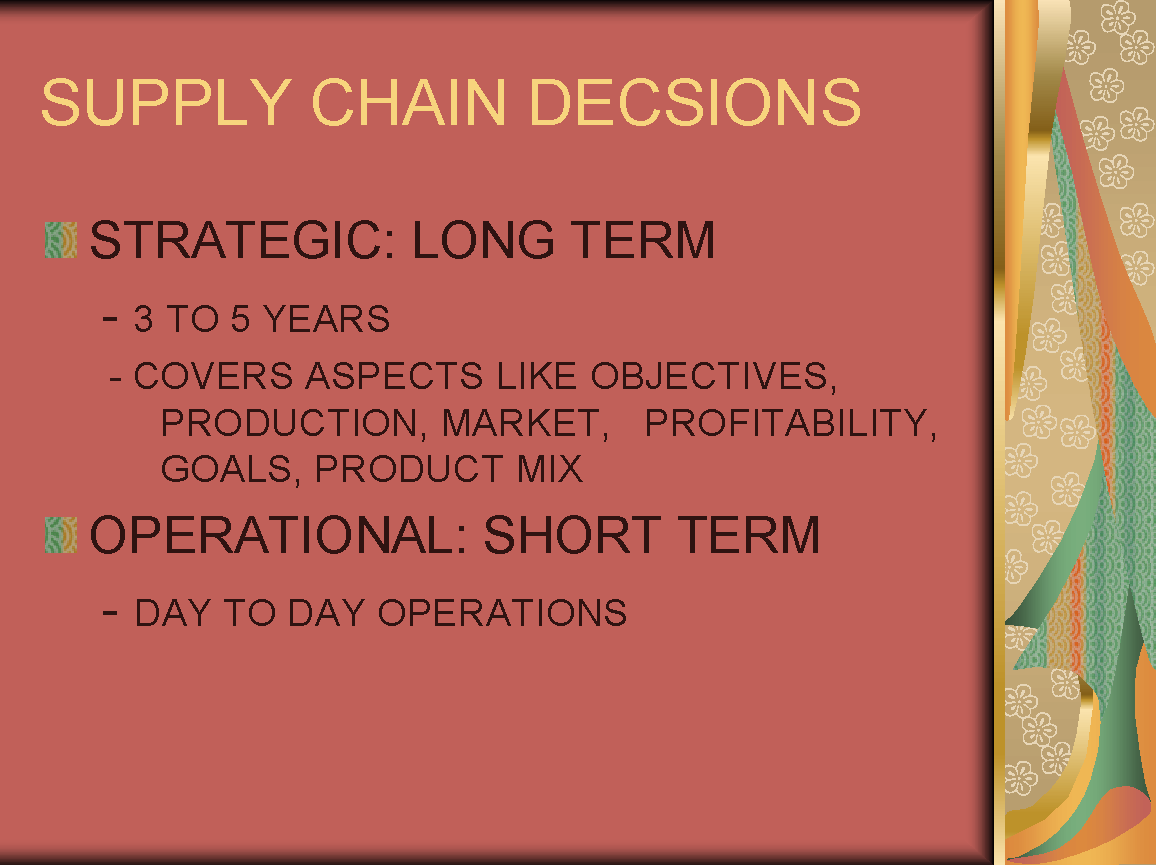
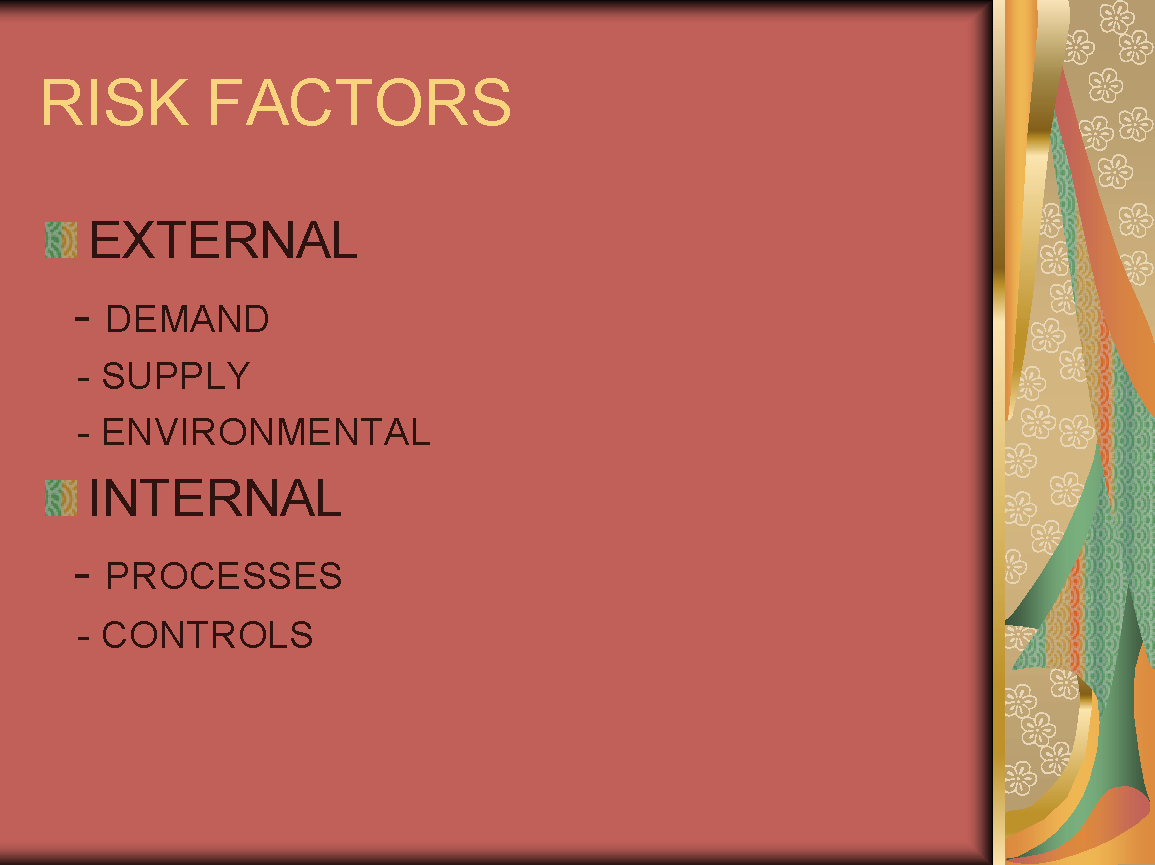
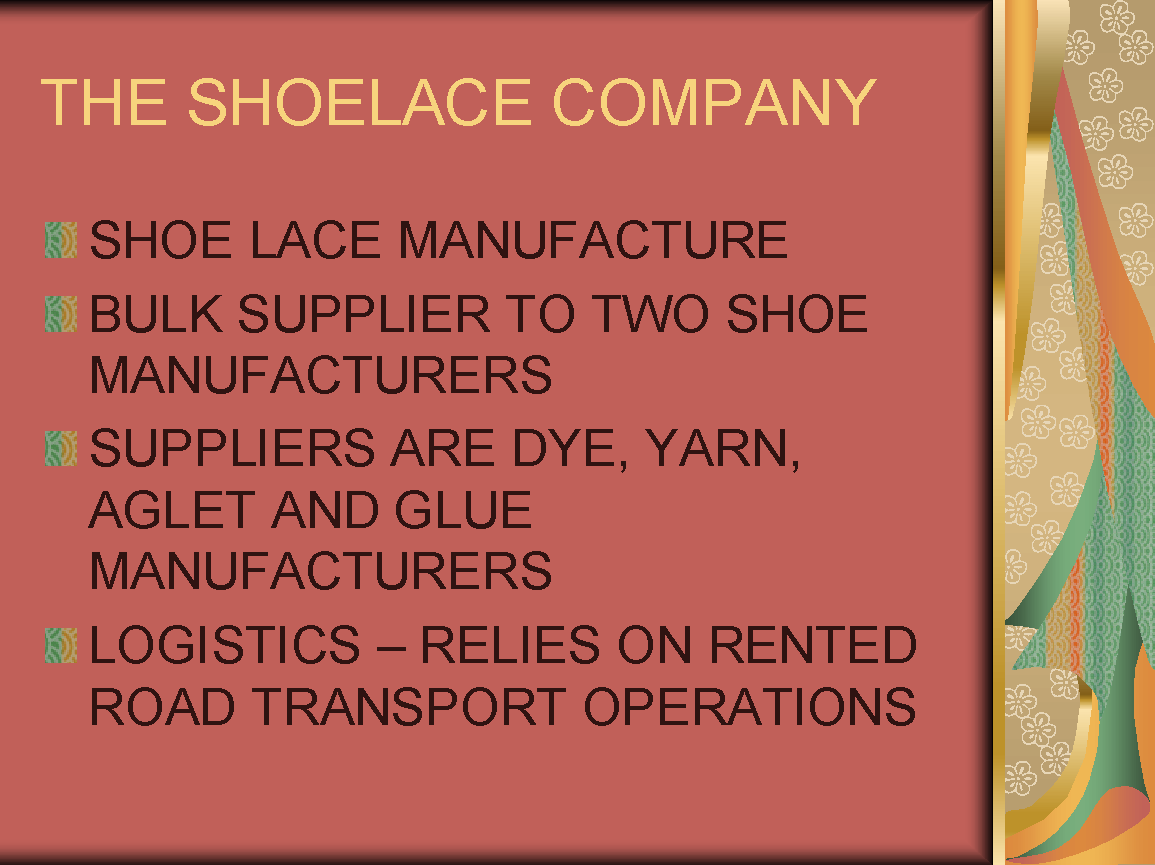
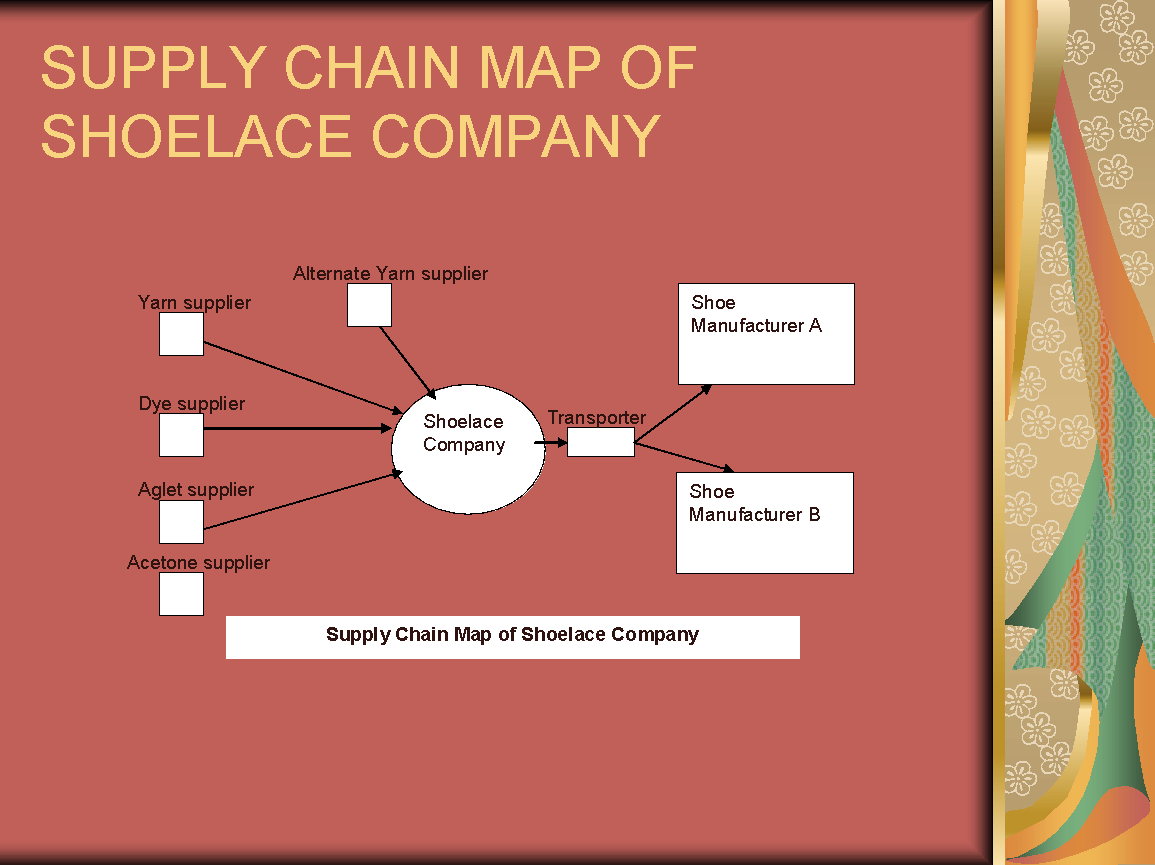
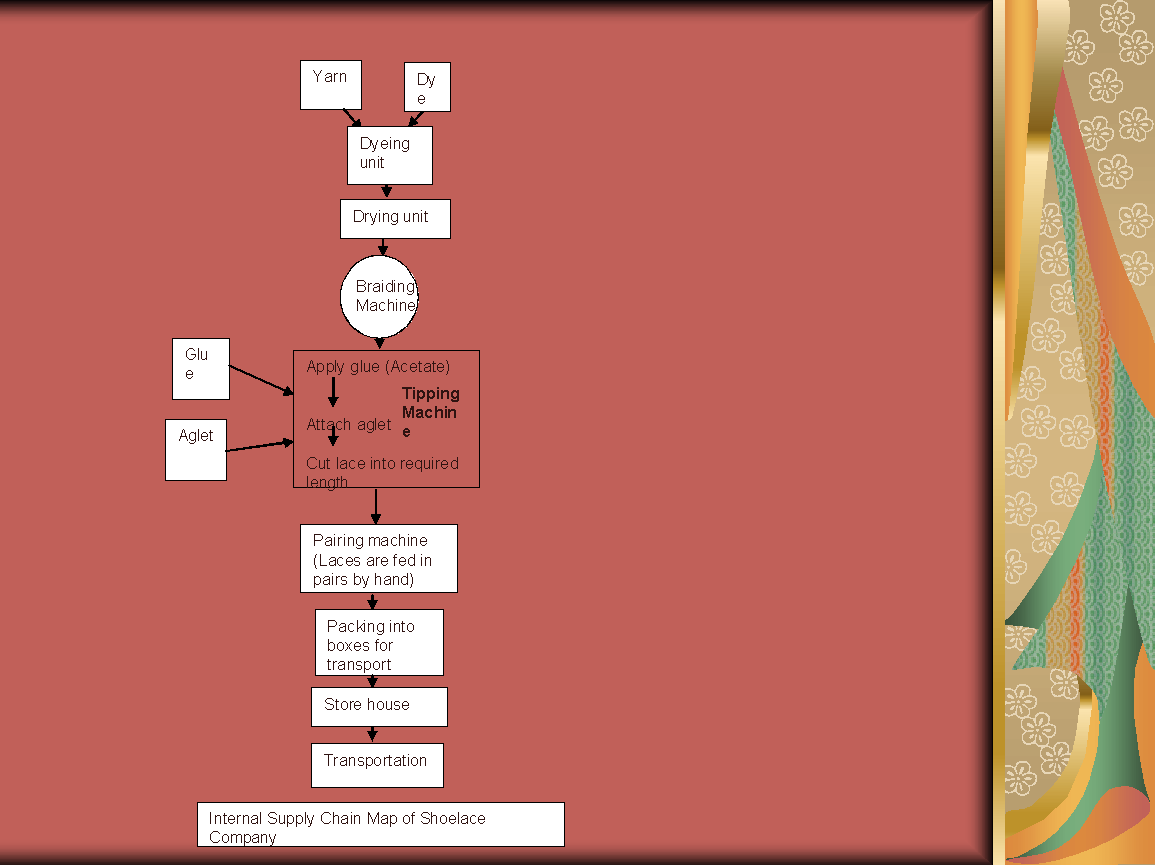
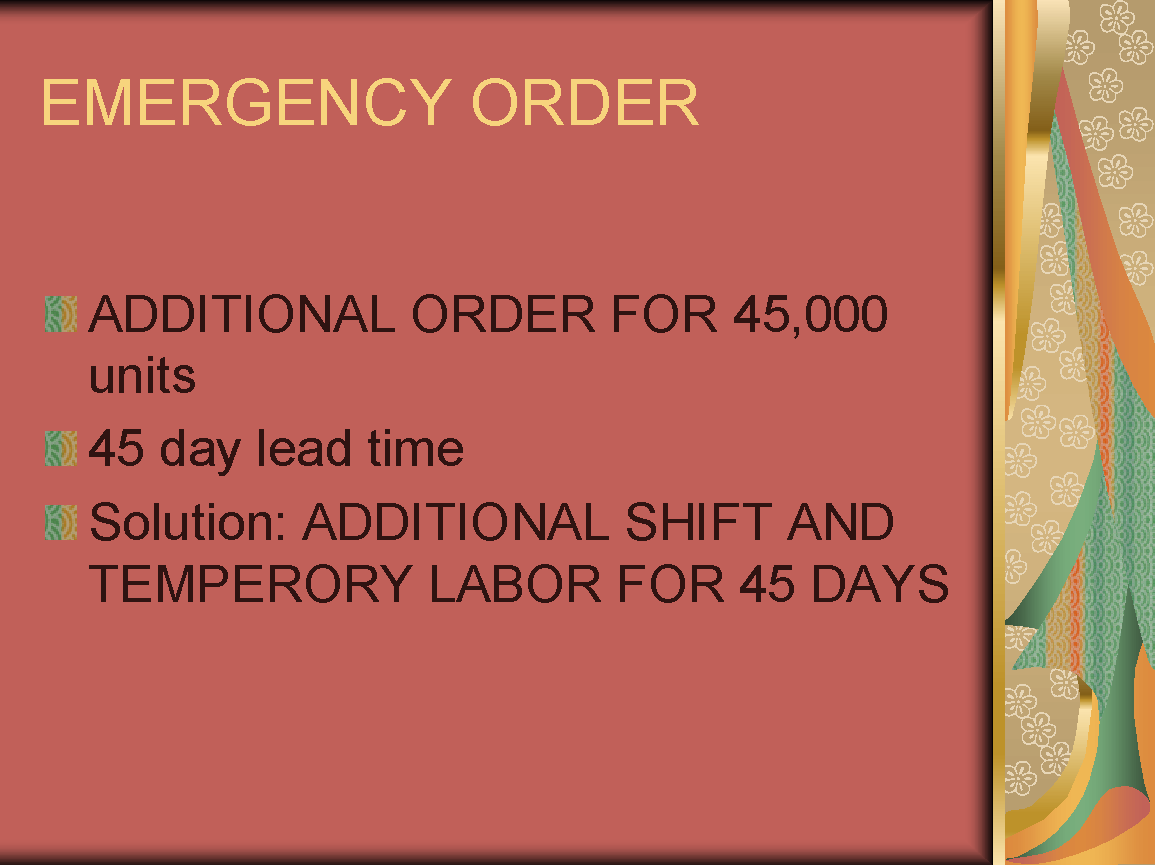
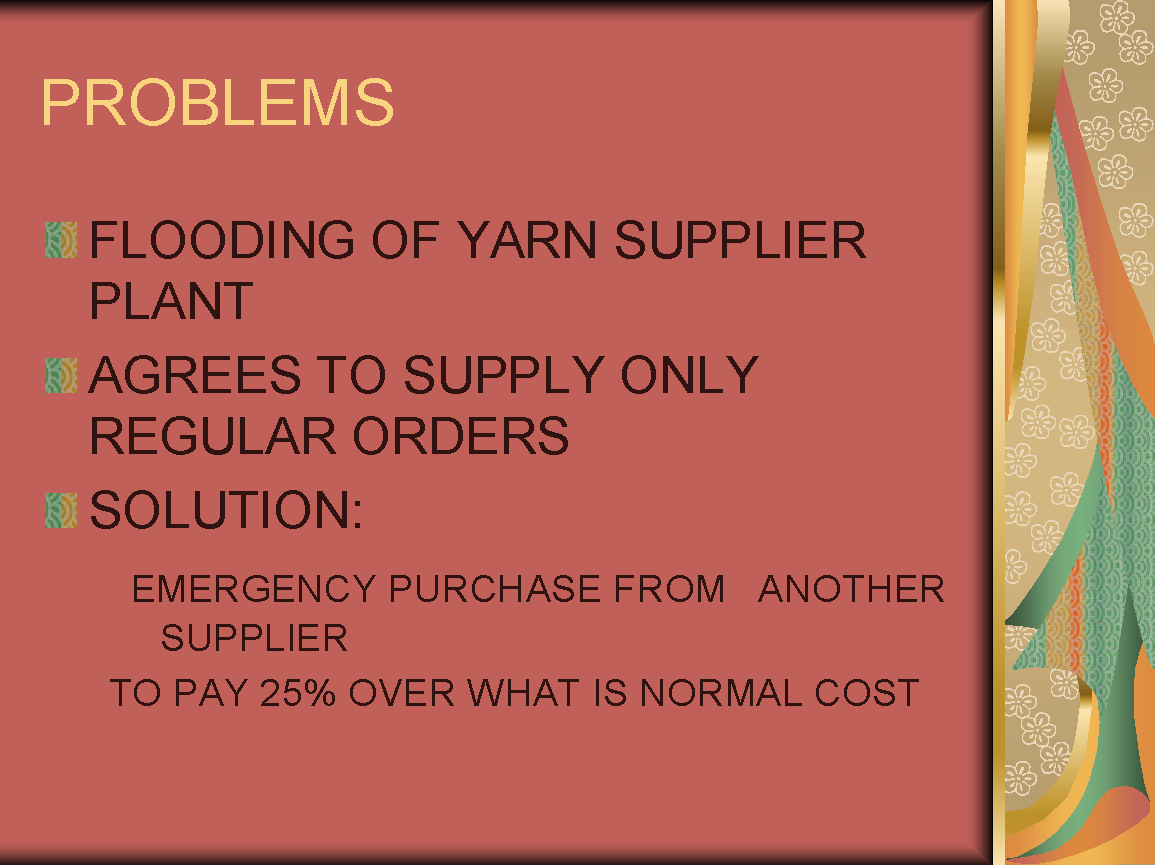
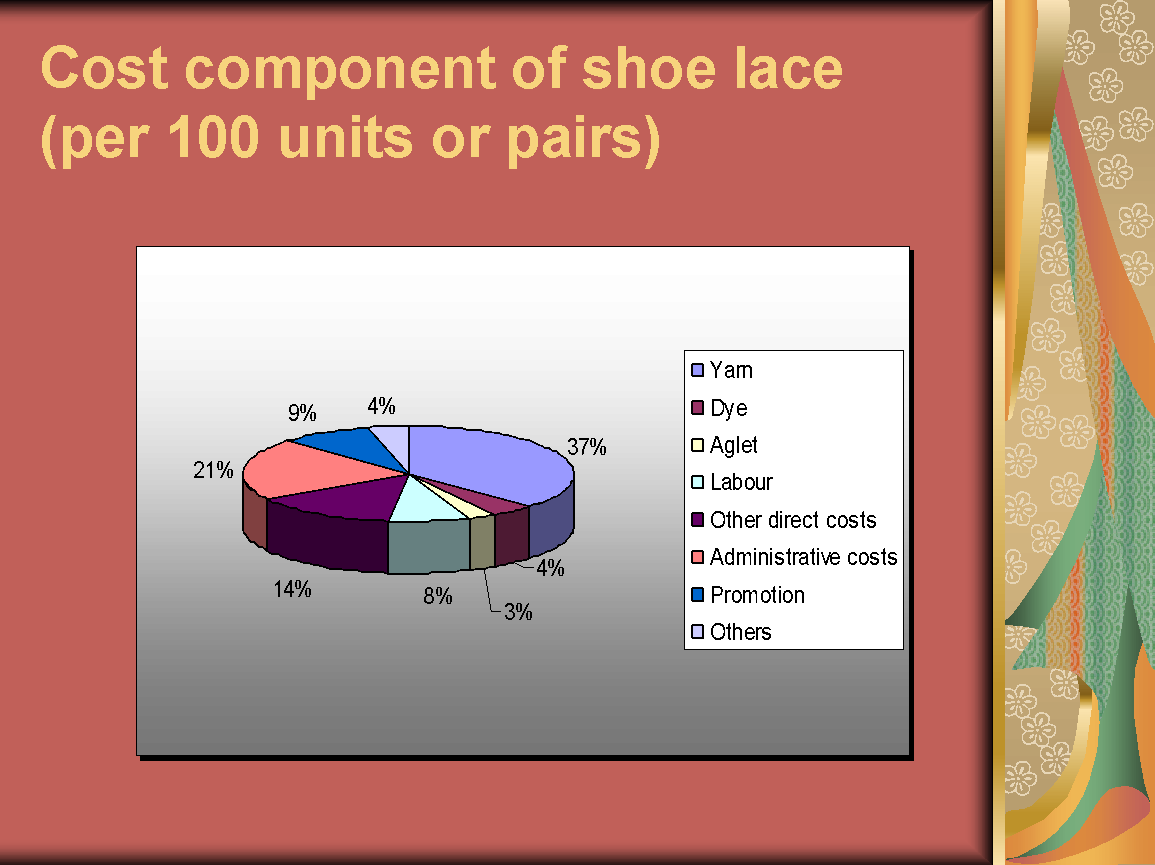
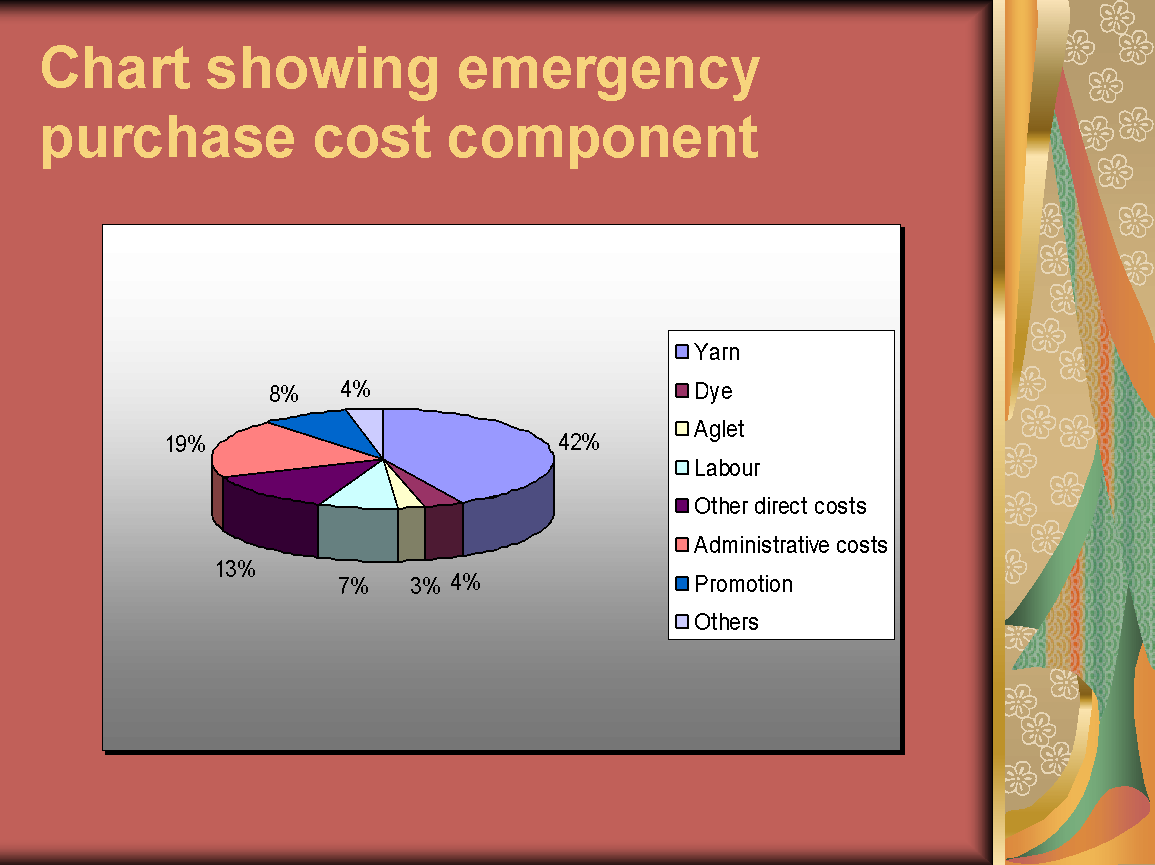
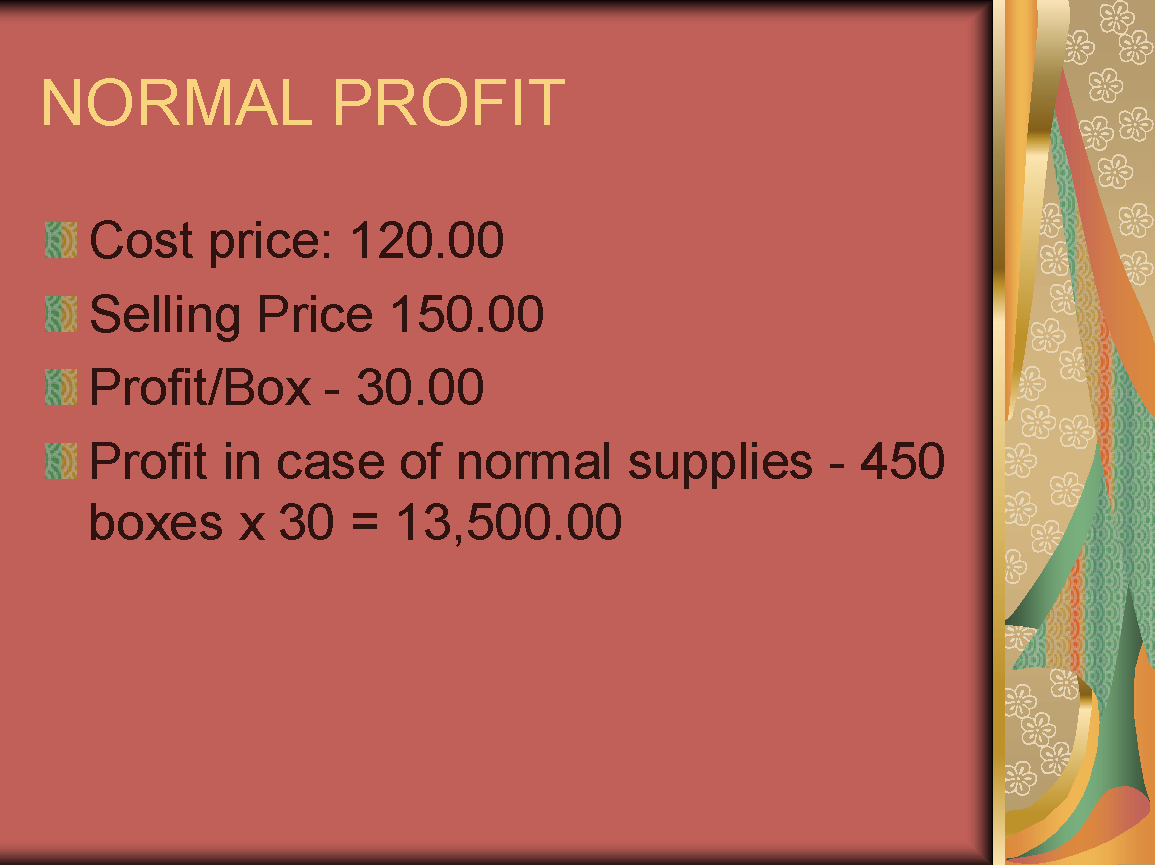
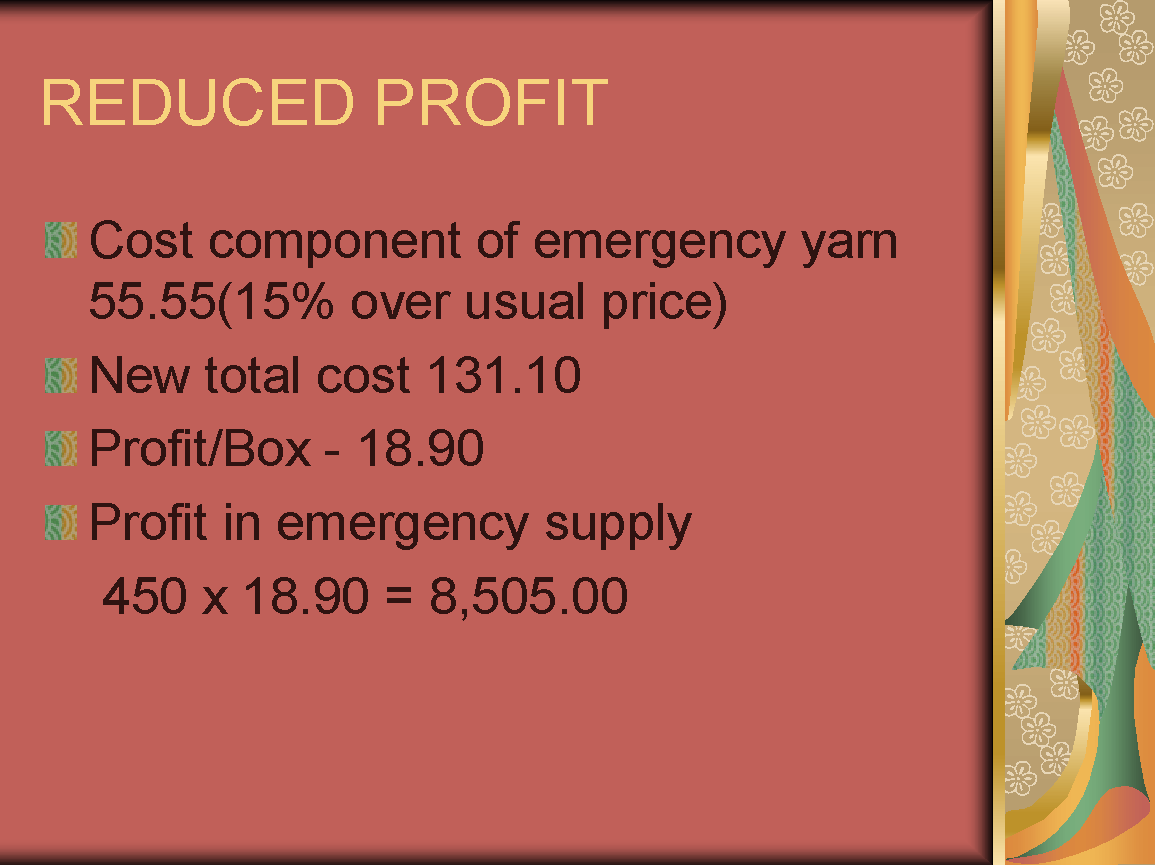
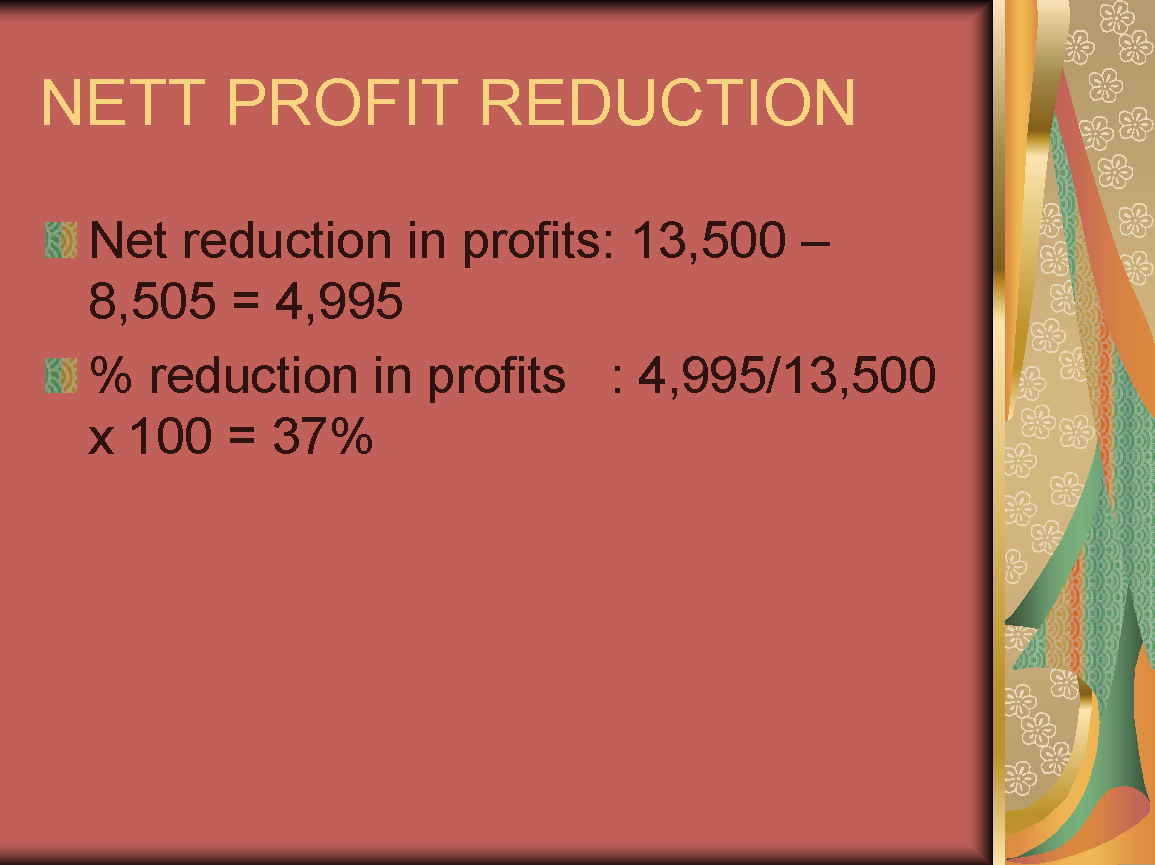
Bibliography
Aberdeen., et al. (2008). Supply Chain Risk Management: Building a Resilient Global Supply Chain. [online]. SupplyChainBrain. Com.
BRYK, Nancy. (1998). Shoelace: How Products are Made. [online]. BNET: The Go To Place for Management. 9. 2.
Framework for Continuous Distribution and Supply Chain Performance Improvement: A Supply Chaining Framework. (2007). [online]. Future Pharmaceuticals.
GANESHAN, Ram., and HARRISON, Terry p. (1995). An Introduction to Supply Chain Management.
JOHN T, Mentzer., et al. (2001). Defining Supply Chain Management. [online]. Journal of Business Logisitics. 1.
LEVI, Edith Simchi., and KAMINSKY, Philip. (2004). What is Supply Chain Management. [online]. Managing the Supply Chain. 3.
Logistics Management: An Introduction to Supply Chain Management. (2008). [online]. NSL World: Narayan Shipping and Logistics.
Supply Chain Risk Management. (2005). [online]. The Decision Makers Direct.
TEIGEN, Rune. (1997). Definition: An Example of a Supply Chain.