Abstract
This research paper covers the definition, strategic effect, and stages of the product design process. This paper also discusses four steps of Vs. Model and the stages involved in their design and selection of product design process. Planning is the essential phase in designing any product. A series of plans are established then the most appropriate one is selected for completing up the product. The best plan selected for product design is then executed. However, other alternative plans must also work if anything in the original plan requires amendment or gets failed or error red.
It shows a flowchart of the process and the influence of technical improvements on process design. With the right design techniques and approaches, you may get double the outcome with half the effort. Choosing the correct techniques and methodology in product design is necessary to execute a perfect product design. The results get better off when the proper methodology is selected. First of all, it is better to understand the product’s design; by getting the design know-how, it will know what things are needed to improve it further. After that product requirements are gathered, there are many conceptual phases; analytical and investigation are done to complete the product. It is a long and detailed process of designing any product.
Introduction
The design method guarantees that the design process is established effectively and that its quality is increased. In contrast, the design procedure serves as the foundation for guiding the phases of the design process. A clear and logical method may lead to a high-quality and straightforward design process. At the same time, the proper use of manufacturing strategies can help the manufacturer discover a reasonable solution to a wide variety of challenges, allowing the manufacturer to construct and manufacture a high-quality product (Pessoa, 2020). The advancements in computing, intelligent machine learning, and network advancements aid in developing smart products and allow for drastic transformations of developments in other fields.
Understanding of Product Design Process
Sustainable product creation and design seek to limit negative environmental consequences while maximizing long-term value across the brand’s, building’s, or service’s life span. Inventing new technologies that add to, rather than endanger, sustainability is the key to solving many sustainability concerns (Ahmad and Wong, 2018). It is a series of design tasks that accompany a product from idea to completion. A well-structured process with clearly defined planning and integration phases is essential from concept to the final product, ready for sale. The product design process is a time taking and complex task. This is accomplished through the development of a Product Design Process for the target market. It is challenging to create a universal design approach that works for all things, tangible and immaterial. However, a set of phases that should be present in every product design process may be described:
- Product Requirement Gathering;
- Defining Product Scope and Requirement Analysis;
- Action Plan or Process Selection;
- Plan Execution;
- Prototyping;
- Validation and Verification of All Steps in the Process;
- Maintenance for a Product.
Product Requirement Gathering
A requirement gathering is a comprehensive phrase that is used across a wide range of businesses. It expresses an essential function, trait, or quality for a system, whether in law, engineering, or general business. It is a collection of criteria or actions that must be satisfied for a project to be considered successful (Mohammad, 2017). Consider automobile tires; certain automobile tires have size and air pressure specifications to match the specific kind of car they are going on.
With the introduction of data mining tools, several new prospects for improving the requirement gathering procedure have emerged, just using recommender systems. Recommendation systems for requirements elicitation can offer the correct information to demand engineers at the right moment. Teams have decided how large and thick a tire should be for a truck, how much air should be in the tire, the type of material used, and other factors. The need component includes everything related to the specifications of ensuring the tire fits the automobile appropriately. A requirement is a precise documented functional need that a design, product, or feature is intended to address during the product development process (Uhlar and Heyder, 2021).
Requirements are divided into two main categories:
- Functional Requirements – Which state what products have to do and what does not have to do.
- Non-Functional Requirements – It related to the product reliability and performance.
Defining Product Scope and Requirement Analysis
During this phase, a series of barriers, challenges, and model concepts will be provided, analyzed to steer our future offers. To research our product, learn about the market and potential buyers, and obtain vital knowledge about the many features, we must first discover the main point. As shown in the picture, we also need to manage the entire development and design process and keep track of the associated costs.
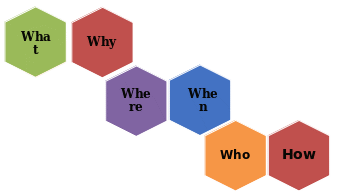
In this step, we define the product’s scope, which states what the product has to do and what the product does not have to, and provides the target audience’s information. To ensure this, the team performs requirements analysis, including 5Ws (What, Why, Where, When, and who) and 1H (How).
- What – what we have to design
- Why – why we have to design this product
- Where – Where we can use this product
- When – In which situations this product is helpful
- Who – For whom we are designing this product
- How – What process do we follow to design this product.
Action Plan or Process Selection
The design process refers to the progression of a design and how design tasks are completed. According to how the procedure is set up, it may be categorized as linear, parallel, or sophisticated. It is a natural combination of identifying, assessing, and finding solutions. As technology advances, computer-aided design and manufacturing (CAD/CAM) have become extremely prevalent in the design phase (Herzberger and Sirrine, 2019). Consequently, the design process illustrated in the above image may be reduced to the modern digital design approach depicted in the graphic below.
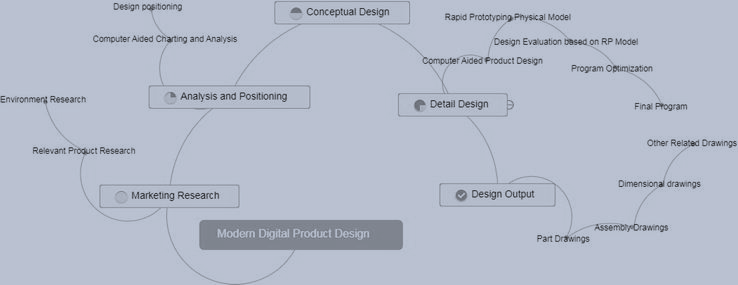
Product design is generally divided into four phases: investigation, analytics and orientation, conceptual design, design specifications, and design output. The particular concerns at each step change slightly and are more difficult depending on distinct design elements.
Investigation Phase
The design process begins with design and research. It is recognizing what we already have, what we need and, and where to get as well as how to get the required information from segments and sub to recognize the importance, using existing data as a preliminary step, using evaluation and synthesis methods, and so on, to combine the significant contributing factors of the products in order to get objective of business (Zhang and Huang, 2018). As indicated in Figure, the research phase primarily focuses on the target audience, technology, and surroundings.
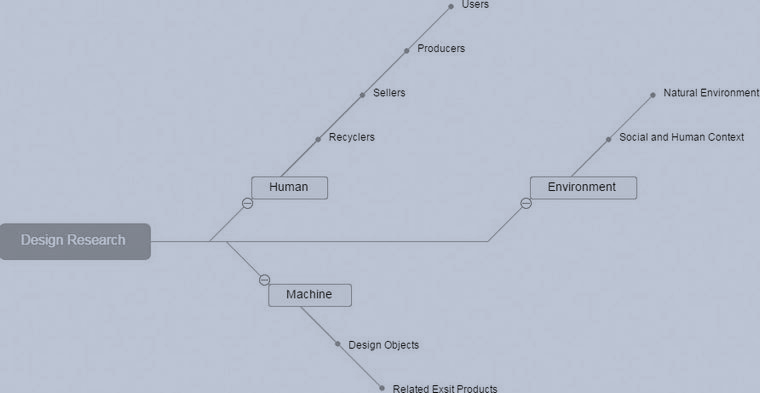
Analytics and Orientation Phase
The investigation mentioned above material is mostly used in the analysis and positioning stages. Second, machine analysis may be intuitive and successful in identifying market development prospects. On the one hand, market agglomeration indicates that a product’s status is well-suited to the present trend and can fulfill the wants of the majority of users. It may be used as a product development follow-up (Valle and Antonenko, 2020). On the other hand, the problem of a different approach of treating challenges with revolutionary thinking and the employment of unique methods to creatively finish the development of brand-new things may be reversed in the case of the market’s adverse outcomes.
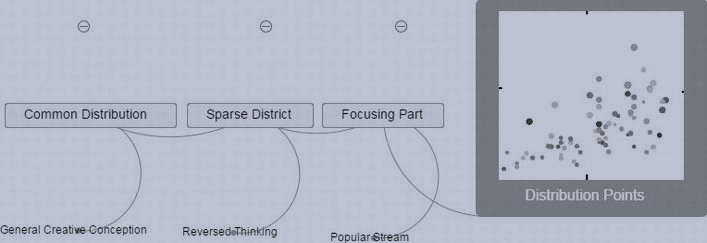
Conceptual Design
Based on historical market requirements and user demands, conceptual design is a series of structured and focused brief design concepts. It takes the form of a gradual progression from large to fine, from hazy to clearer, and from abstraction to definite, which serves as a prelude to the visualization of design concepts after the design above positioning has been decided (Renzi and Leali, 2017). The fundamental goal and development path of a new product are determined by conceptual design, which allows us to conserve as many resource professionals as feasible, assist subsequent manufacturing and sales, increase profit margins, and efficiently estimate and steer late recycling difficulties.
Detailed Design
The comprehensive design process is a visual representation of previous design ideas. It is gradually building a clear graphical plan, extending and deviating following design concepts. This is the foundation for the design and testing process, programmed selection and optimization, and product expressions. Focusing on the abstraction design concept, creativeness, and extension, the ideal notion is increasingly related to tangible things, and the methodology is gradually clarified and extended. The design specifications for modern automatic vehicles pose additional considerations. One of the major remaining research difficulties in software-intensive systems is the convergence of safety and security requirements (Bertolino and Calabro, 2018). Aspects of these requirements should be established early in the design, as they can significantly affect the functional characteristics of a product.
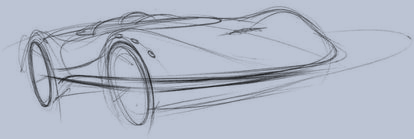
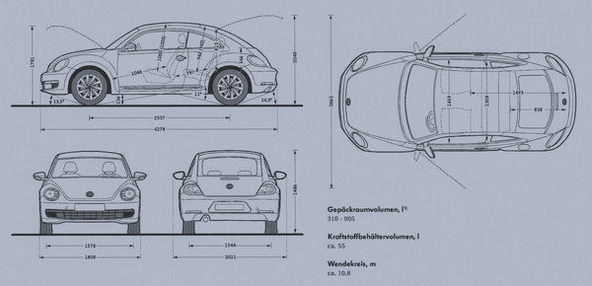
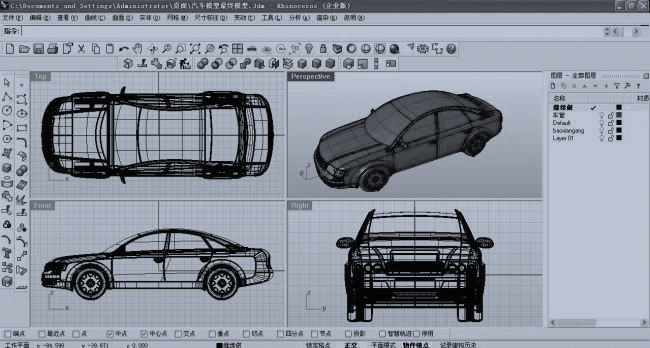
Plan Execution
In the plan execution stage, we put our plan into action. Based on the To-do list which we create in the second phase, we perform the steps in sequence to accomplish our task to add value to the customer experience. Customer satisfaction is the objective of every business. We try to perform every step according to schedule so we can deliver the product before the deadline.
Prototyping
Computer-aided design and production techniques can be fully utilized for planning and evaluation, program choice, and advancement based on the progression and commercialization of advanced technology. Virtual models can be built with design sketches, and even three-dimensional models can be obtained using computer-aided design technology. Product functioning, architectural engineering, color design, and human-machine interface design are just a few of the model’s roles. Simultaneously, the 3D or theoretical model is improved and enhanced based on the assessment findings, employing computer-aided design tools and reverse engineering methods.
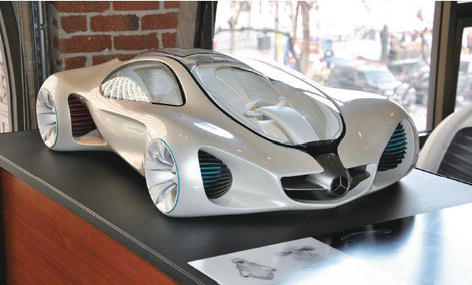
With the rising use of the Arduino platform, prototyping with Arduino has gained in popularity. However, for the nonprogrammers, it could not be easy to perform (Imottesjo and Kain, 2018). Therefore, in today’s world, programming in the design and manufacturing of products plays a key role in an efficient process.
Validation and Verification of All Steps in the Process (Design Evaluation)
Design evaluation is a step in the design process that involves comparing and assessing the issue solution, calculating the value of each program, and examining its benefits and drawbacks to select the best design. In this context, the term “programs” has a broad definition and may apply to a range of things, such as main programs, structural programs, modeling programs, and so on. From the recipient’s perspective, it may be a single component or a whole design, a model, a prototype, a product, or anything else.
In actuality, the “programs” indicated in the evaluation solve the design’s problems. The relevance of design assessment is to manage the design process consciously, target the design’s direction, and review the design plan using precise analysis rather than perception, which provides designers with a platform for evaluating design concepts. Design evaluation may successfully ensure the quality of a design, and the best solution, in which all performance factors meet the aim goals, can be selected from numerous design programs. Second, proper design evaluation may help to reduce design blindness while also improving design quality.
Different assessment targets for different design items and stages of the design process are defined, and the most relevant content is picked to construct the evaluation target system.
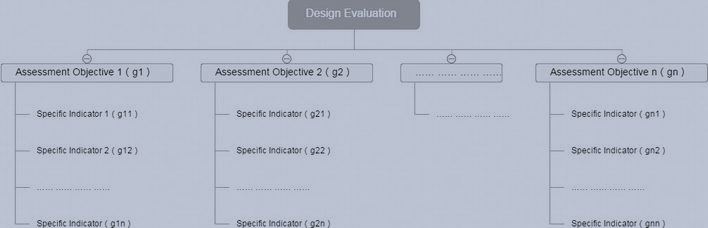
Supports and Maintenance
Every firm additionally supports its clients by providing a wide range of support and maintenance services to guarantee that the given product functions smoothly and completely meet its customer’s needs. Bug fixes, troubleshooting, application updates and additions, training, product performance assistance, and more are all part of the company’s entire spectrum of support and maintenance services.
Operational Management
Any corporate function involved in controlling producing products and services is known as operations management (O.M.). Operations management is a business department concerned with the production of products and services, and it comprises ensuring that company units are both efficient and effective in meeting customer demands. It is critical in converting raw materials into products.
4Vs Model
The four Vs. Model assist a company in making the most use of its resources:
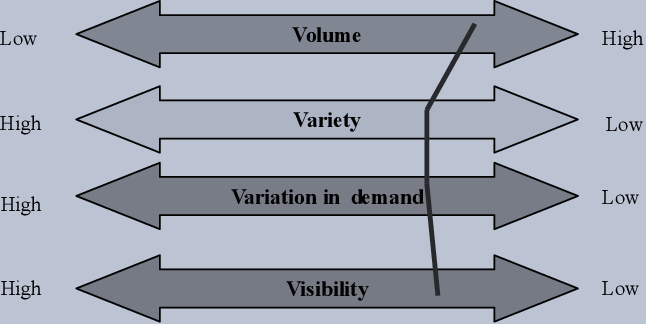
- Volume – Contain high levels of a standardized product.
- Variety – A wide range of items (output).
- Variation – Such as the degree of product customization.
- Visibility – Customers’ ability to view and experience operations.
Volume
A fast-food restaurant like Domino’s may be able to deliver superior business service. Every day, they sell many pizzas and other food items worldwide, and one of Dominos’ most distinguishing traits is their continuous supply of goods and services. They are one-of-a-kind, will take a long time to create, and will be difficult, if not impossible, to replicate exactly. Volume is the amount of inventory that must be generated in order to keep up with the market’s total competitiveness—the total number of units or things produced (Saliji, 2021). This is a lengthy operation that demands a large number of resources. Scarcity is often utilized to raise sales, but it may also be used to increase brand recognition. It takes advantage of a gap in the current market (Hawkins and Habib, 2018). Thus, adjusting production volumes can be a useful tool to maintain a competitive advantage.
Variety
Companies that sell a wide range of products or services could increase their sales and profits while limiting their concentration on one or two items, leading to market closing if the quantity demanded declines. Global competition has forced customers to select application-specific bespoke goods or services. When the market requires low volume and a wide range of items (LVHVs), in this day and age, the lean manufacturing (L.M.) technique is gaining popularity since it minimizes or eliminates waste while also increasing a company’s competitiveness (Shigeta and Hosseini, 2020). For people from all areas of life, HUL has a product. It has maintained diversity within a single product category. It is simpler to supply goods and services that meet the needs of clients because of this diversity.
Variation
This is the change in demand over time caused by external forces. Variation is difficult to predict for a variety of reasons. A natural calamity, like the COVID-19 epidemic, is one example. Wreaked havoc on the earth, flipping life on its head in every way (Greene and Ogden, 2020). Most business operations are made up of several different versions that must all be managed together. The bulk of these algorithms work assuming that the variance spots and parameters are given as inputs. The control variable has received very little attention in terms of how it is originally sketched and imagined. When activities do not follow a fixed pattern, quality concerns can arise in transactional and manufacturing processes.
Visibility
This term refers to a company’s whole value chain, which includes all processes. Customers must be able to inspect the company’s products or services before making a purchase. Industrial firms have a lower level of Visibility than service industries. At some time in our lives, the vast majority of us have become disoriented. It is frustrating to find a client’s preferred location, whether the firm’s workplace, factory, retail outlet, office, or customer support center.
Visitors must be able to discover organizations quickly if their signage is both clear and conspicuous. Otherwise, the encounter might be unpleasant. Returning customers have already found it simpler to find, thanks to high-visibility signs. The four Vs. are critical to high productivity in the global corporation, and operations management keeps them that way. Operations managers provide procedures and processes to assist the organization in getting a good level of amount, diversity, volatility (Somapa and Cools, 2018). Unilever’s production team contributes to the success of marketing, sales, finance, and human resources.
Lean Principle
Lean is a strong technique that may significantly improve industrial sectors by reducing waste and producing value. The lean methodology has grown in popularity in widespread companies such as the automobile industry; it has lately been implemented in the various progression of steps and service industries. Numerous research studies have shown a huge prospect of efficiency improvement in the automobile sector while implementing lean management (Ismail, 2018). Corporations are now focused on sustainable development with increasing environmental concerns to respect current and future advancements (Bouazza and Lajjam, 2021). Lean manufacturing has allowed manufacturers to effectively reduce wastes and increase profitability.
Just-In-Time
Just-in-time (JIT) management is a processing technique in which goods and services are made to meet exact demand instead of surplus, deficit, or ahead of actual need. In business, just-in-time management aim to reduce waste caused by overproduction, holding inventories, and excess inventory by assisting producers in controlling variation and improving efficiency while cutting costs (Delic and Knezevic, 2017). Just-in-time production attempts to lower overall supply chain costs while also improving operations. Just in time, (JIT) manufacturing may assist with improved inventory control by up to 75 percent, from minimizing inventory losses to lowering inventory and supply chain expenses. A just-in-time production system also delivers substantial value in quality control, with productivity gains of over 25%.
Conclusion
A clear and logical method may lead to a simple and high-quality design process. At the same time, the proper use of manufacturing strategies can help the manufacturer discover a reasonable solution to a wide variety of challenges, allowing the manufacturer to construct and manufacture a high-quality product. Challenges are there to be faced in the designing process of a product, but one needs to have a clear and high-quality design procedure so that the product can easily be designed to get executed. Many advanced techniques are also devised that can aid in designing products.
For the manufacturing process, it is highly recommended to follow all 4Vs of product design plus following the peculiar methodology of product design. The just in time (JIT) manufacturing method ensures good inventory control and quality of products, minimizes material losses, and reduces stock-related losses. Whenever anything needs to be designed, it goes through several phases of planning, plotting, investigation, inspection, technical, analytical, and finally to execution level. Alternatives must be made part of product design because it is often needed to amend the product design or some parts of the plan.
Reference List
Ahmad, S. and Wong, K. Y. 2018. ‘Sustainable product design and development: a review of tools, applications, and research prospects’, Resources, Conservation & Recycling, 132, pp. 49-61.
Bertolino, C.G. and Calabro, A. 2018. ‘A tour of secure software engineering solutions for connected vehicles’, Software Quality Journal, 26, pp. 1223–1256.
Bouazza, D. and Lajjam, A. 2021. ‘The impact of lean manufacturing on environmental performance in Morrocan automotive industry’, Management Systems in Production Engineering, 29(3), pp. 184-92.
Delic, K.S. and Knezevic, B. 2017. ‘Additive manufacturing technologies adoption in automotive supply chains – the theoretical review’, Business Logistics in Modern Management, 17, pp. 421-436.
Greene, D. L. and Ogden, J. M. 2020. ‘Challenges in the designing, planning, and deployment of hydrogen refueling infrastructure for fuel cell electric vehicles’, eTransportation, 6, pp. 1-16.
Hawkins, H. and Habib, K. N. 2018. ‘Integrated models of land use and transportation for the autonomous vehicle revolution’, Transport Reviews, 6.
Herzberger, J. and Sirrine, J. M. 2019. ‘Polymer design for 3D printing Elastomers: Recent advances in structure, properties, and printing’, Progress in Polymer Science, 97.
Imottesjo, H. and Kain, J. H. 2018. ‘The urban co-builder – mobile augmented reality tool for crowd-sourced simulation of emergent urban development patterns: requirements, prototyping, and assessment’, Computer, Environment and Urban Systems, 71, pp. 120-130.
Ismail, Z.K.M., 2018. ‘Amini review: Lean management tools in assembly line automotive industry’, IOP Science.
Mohammad, H.Z., 2017. ‘Analysis for determining factors that make good design process in Automotive Manufacturing Organization’, Journal of Mechanical and Civil Engineering, 14(3).
Pessoa, B., 2020. Smart Design Engineering: a literature review of the impact of the fourth industry trial revolution on product design and development. Research in Engineering Design.
Renzi, L.A. and Leali, F. 2017. ‘A review on decision-making methods in engineering design for the automotive industry’, Journal of Engineering Design, 28.
Shigeta, N. and Hosseini, S. E. 2020. ‘Sustainable development of the automobile industry in the United States, Europe, and Japan with special focus on the vehicles power sources’, Energies, 14(1).
Somapa, S. and Cools, M. 2018. ‘Characterizing supply chain visibility – a literature review’, The International Journal of Logistics Management, 29(1), pp. 308-339.
Uhlar, H.K. and Heyder, F. 2021. ‘Assessment of two physical tire models concerning their NVH performance up to 300 HZ’, International Journal of Vehicle Mechanics and Mobility, 59(3), pp. 331-51.
Valle, N. and Antonenko, P. 2020. ‘Staying on target: a systematic literature review on learner-facing learning analytics dashboards’, British Journal of Educational Technology, 52(4), pp. 1724-1748.
Zhang, T. and Huang, W. 2018. ‘A review of parametric approaches specific to the aerodynamic design process’, Acta Astronautica, 145.