Push and Pull management philosophies
The origin of the term push and pull can be traced back to supply chain and logistics management (Hugos 214). However, according to Nigel, the term is also used in marketing (76). The term describes the flow of information or products from one subject to another. Consumer of goods and services usually “pulls” information or goods in the market to meet their needs. On the other hand, suppliers “push” goods or information required by the customers to the market. The logistic and supply chain operates through a push and pulls system. The inter-boundary between a pull and push stage is referred to as decoupling point (Ballou 56). He adds that the Push and pull strategy is either non-interactive or interactive (86).
The sandwich manufacturing company is a production-driven company, which produces sandwiches and wait for demand to arise. The future anticipation of growth opportunity to the production of 12,000 items up from 3,000 a week will convert the company from a manufacturing to a marketing-oriented company. This is because the company will now manufacture sandwiches to meet the needs of the built-up demand. Sandwich, therefore, will sell fast hence pushing to customers to meet their demand other than wait for the consumers to pull the commodity. This will result to higher returns by the company and ensure instant demand for the highly perishable sandwich.
On the other hand, the sandwich manufacturing company will result in to pull strategy in demand for supplies of the ingredients used to manufacture sandwiches. The supplies will be pulled from them to meet the expected demand for a sandwich. Because of the increase in the scale of production, the company will, however, be faced with a dire need to scale its operations. More production will call for more labor and resources. The services of the workers and employees will, therefore, be pulled more into the company to meet the expected output. More effort will be pulled from the business improvement manager to ensure that the production process is effectively carried out to meet the customers’ needs. This would be by ensuring that time and place utility is observed. More effort will also be required to ensure that quality is observed.
The resulting increase in the scale of production will call for a more effective control system. The services of the control system will therefore be pulled more to meet expected output. This may, therefore, call for an upgrade of the systems to ensure that control is not compromised. As the company pulls more supplies, more facilities including storage facilities, transport, processing, and communication will be required. More workforces and more working hours will also be necessitated by the company’s pull for labor. This will therefore lead to huge costs and the company may therefore be compelled to pull the services of financial institutions. Communication costs will escalate, as the company from the various parts of the supply chain pulls more information.
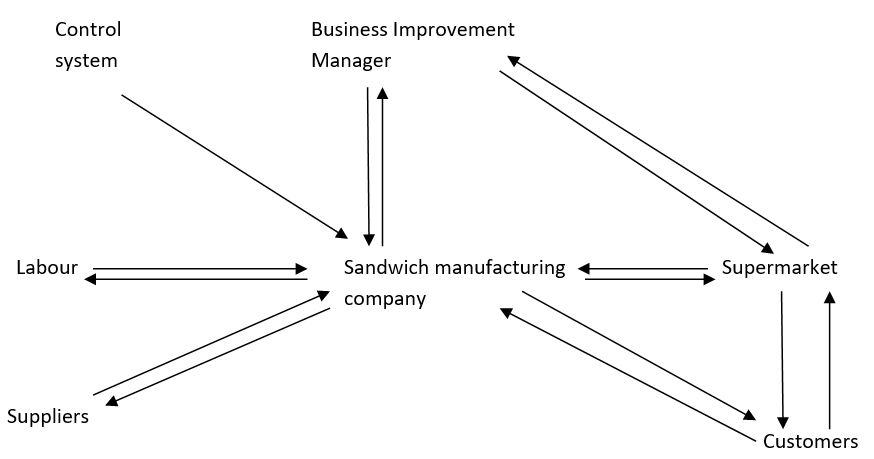
The business improvement manager will offer advice to the company on how to deal with the expected increase in demand for sandwich. He will therefore provide his know how to the company. The company will in return offer him wages for his services. The Business development manager will also exchange information with the customers especially the supermarket outlet to secure orders and feedback from them, since they will have a direct contact with the company’s customers.
The supermarket will obtain and place orders for sandwich from the sandwich manufacturing company. The company will provide feedback in form of information to the supermarket. Once the products are ready, the company will distribute them to the supermarket, ensure time, and place utility. Since the products are perishable, the company will provide the best means of transport for example refrigerated vans to transport the products. The supermarket will in return offer payments to the company on order. The company will take expired products from the supermarket and replacement done.
Because of a pull in labour by the company, more services in form of working hours will b required from the workers. This will be per with the company’s regulations to ensure that quality of production is not compromised. The labour force will in return expect a pay for their service for normal and extra working hours. Information will also be exchanged between the labour force and the company to ensure that the expected output is met. This will also be critical in understanding the working condition of the workers to ensure that they are not overworked to maximize output. To ensure effective allocation of working hours between the various employees a more advanced system will have to be incorporated into the company. The system may in turn call for employment of expert staff to run and manage the system.
The company’s suppliers will require information from the company on the quantity of supplies required. Time for delivery of the products will also be communicated because most of the products are perishable. This will ensure that the correct quantity and quality of products is supplied to the company in time for production and in the right quality so as not to comprise on the quality of the final product. The suppliers will also need to be communicated on increase in scale of production in order to communicate the same to their source of the products. The same will be also important since it may call for more investment on suppliers especially on transport facilities. The suppliers will in return receive payments on procurements delivered to the company.
The control system of the company monitors the operations of the company to ensure that the manufacturing process runs effectively as planned. The control system also allows the company to identify any discrepancies in the production process. It also provides interventions in case a discrepancy occurs. For an effective production process, an effective control system is therefore critical. A company should therefore, consider an effective control system probably in software form rather than manual. The company however, provide the expertise and resources for effective running of the system in return of the benefits it offer to the company.
SCOR Model
A SCOR model is used by an organization to assists an organization to measure their rate of success in their target market (Hugos 301). The model performs the task by forming a framework that forms a link between a firm’s processes, technology, best practices, and metrics. The model also provides common language and metrics, which accelerate change within a business. SCOR model improves, reorganize, measure, and identify the processes of a supply chain (Hugos 305). The cyclic cycle of a SCOR model, include configuration and capturing of the supply chain. The configuration of a supply chain is motivated by a plan of the levels of sources of information, their integration, their source, make method used, site, delivery methods used and return methods and locations (Hugos 310).
The model also encompasses measurements of the supply chain performance through comparison between external and internal goals of the company. This is through focus on assets, costs, agility, responsiveness, and reliability of the supply chain. It also re-aligns the best practices and processes of a supply chain by reviewing the set objectives. This is achieved through bench marking, ISO- 9000, Constraints Theory, Six-sigma, Lean Manufacturing, and Reengineering (Hugos 315).
Level 1 is the top-level top level of a SCOR diagram. Level 1 SCOR Diagram for the sandwich manufacturing company can therefore, be illustrated as shown below:
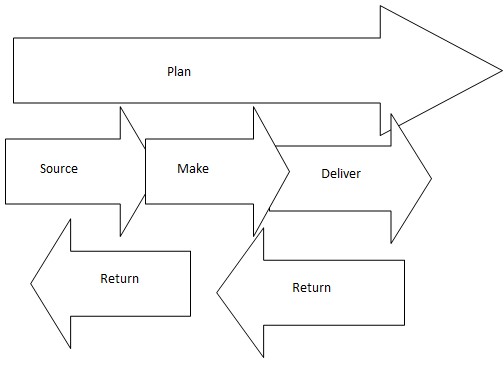
The plan process will involve an identification of the requirements for the supply chain management; these will then be prioritized and aggregated. This will be followed by an identification of the production, delivery and return requirements and their prior prioritization and aggregation.
The sandwich company supplies comprise the perishable and non-perishable products. Non-perishable products will be supplied fast before the perishable products. This is because they can be stored within the company’s facilities for some days before actual production takes course. On the other hand the perishable products used for making sandwich will be supplied a day before production process. Production process for sandwich will be done during the night when temperatures are low. This will enable the products to have a longer shelf life. The returns from the customers and the supermarket will be received fast on delivery of the products. This will allow the company meet costs for supplies acquired by the company together with other costs for example labour and transport costs.
Conclusion
The supply chain of the sandwich manufacturing company can be supported through automation of the supply chain through use of a software application system. This will allow the company to identify the profitable channels through which the company can dispatch its products. This will also allow the company to track all costs arising from its operations, allow invoicing of supplies, and allow a connection between the supply chains for effective management.
Works cited
Ballou, Ronald. Business Logistics: Supply Chain Management. London: Prentice Hall, 2003. Print.
Hugos, Michael. Essentials of Supply Chain Management. San Francisco: Wiley, 2006. Print.
Nigel, Slack. Operations Management. London: prentice Hall, 2004. Print.