Introduction
The role of welding in everyday human life cannot be estimated. Within anybody’s vicinity, half of the items have undergone a form of welding. These start from the automobile bodies and the railings on the staircase to the functional and decorative items like patio chairs, candle holders, baker’s shelves, wine racks et cetera. However, a large number of people have no idea of even the basic fundamentals of this profession. This paper will therefore highlight the basic principles of welding. It will identify the major types of welding, what they entail and the safety precautions necessary for these processes.
To ascertain an understanding of the process, we might want to ask ourselves what welding entails. As Ruth ( p. 8) simplifies the whole process, welding is all about “…using heat to melt separate pieces of metal so they will flow together and fuse to form a single, seamless piece.” Therefore, heat marks the basis of welding. Accordingly, the whole process of welding depends on the welder’s ability to control the heat in order to deliver quality results. In this profession, there are terms used to refer to certain objects that are specific to the job. The parts that are being welded are referred to as the base metal. When welding, some additional metals are added to the part being welded and are referred to as the filler metal. While creating the weld, there is an area that is maintained by the welder which is composed of the filler metal and the base metal and is referred to as the molten puddle. What really distinguishes welding from soldering, braze welding and brazing is the composition of the metals being welded. In welding, the metal composition must be similar as opposed to the other methods. The following are the safety rules in welding (Pender 7: Finch 9).
Safety Rules in Welding
As mentioned above, welding is all about heat. Accordingly, welding can be a dangerous activity. In the process of welding, one can sustain cuts, burns, electrocution or can simply cause fires which can cause loss of property or even loss of life. The dangerous part of welding is not only during welding but also during other processes of welding preparation like sawing, grinding and burnishing. It is therefore important that great precaution be taken whenever undertaking any process of welding. The following are some of the major precautions to be considered.
Fumes
In the process of welding, the fumes produced are usually dangerous to human health. Therefore, a welder must ensure that his face is not within the weld plume. If the welding is being done indoors, there has to be a ventilation fan, fume extractor or exhaust hood. In addition, the welder should wear a particle mask or a respirator that has been approved by OSHA. In the event of pregnancy, a respirator is obligatory.
Burns
The whole body including the hands and head should be protected using natural fibers. This protects the body from sustaining burns from hot sparks and slag that fly around. Natural fibers are recommended because synthetic ones like nylon could melt when subjected to ignition. This could cause burns of a serious nature.
Arc Burn
Infrared and ultraviolet lights produced by welding arcs could be detrimental to the eyes, and skin. They can cause blindness, burns or skin cancer. As a precaution, a welder should wear a welding helmet that is fitted with a lens for eyes and also facial protection. Long pants and long-sleeved clothes are recommended for the protection of the skin. Welding screens should also be available to protect the eyes of passers-by and pets. There should be an extra helmet for any interested observer.
Fire
Matches, cigarette lighters, rugs and any other flammable substances should not be within the welding area. The workshop should also be sawdust-free. To further the precautions, there always should be an ABC-rated fire extinguisher. Together with the fire extinguisher should be a first aid kit. Also, the welder should look around an hour after welding to ensure that welding sparks are not smoldering at a place.
Explosions
In the workshop, gas cylinders including non-flammable ones should be kept in chains or strapped at all times. This is a precaution because the pressure by which these cylinders are packed can make them dangerous missiles. In addition, cylinders should not be double tasked as rollers or supporters. Neither should any welding be performed on them. If one is to be away for more than ten minutes, all cylinder valves should be turned off. During transportation, ensure that cylinders are right side up and chained. This routine should be observed even when they are empty.
Fundamental Welding Techniques
There are several techniques used in welding. These are determined by the different characters of the metal to be welded. For instance, metals with different shapes, compositions, positions and thicknesses will call for different welding techniques. This part of the paper will discuss these techniques one by one.
Holding the torch
This is usually determined by the thickness of the metal in question. In light gauge metals, the horse should be held in a position where the horse is draped over the wrist. The holding methods are shown in figures 1 and 2 below. While welding, the tip should be aligned with the joint that is supposed to be welded. The tip should be held at an inclination angle of 30 to 60 degrees from the perpendicular. However, ascertaining precisely the angle depends on the expected weld, the degree of necessary preheating, and the thickness of the metal. Thicker metals call for more vertical angles which facilitate penetration. The distance from the base metal’s surface to the white cone of the flame should be approximately 1/8 inches. With the correct position of the horse, the puddle formed should have equal amounts of the metals being welded. The movement of the tip should be begun in a circular or semicircular movement. This facilitates an equitable heat distribution on both metals (Giachino 23).
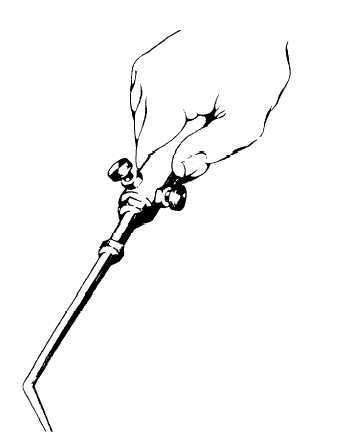
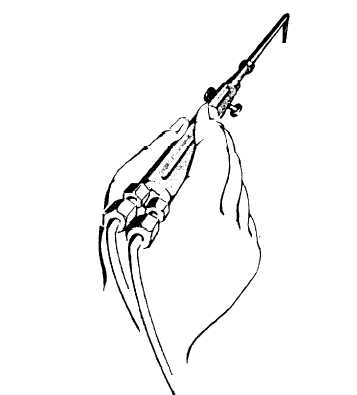
Forehand Welding
This is also referred to as puddle or ripple welding. In this form of welding, also said to be the oldest method of welding, the rod is put in front of the tip in the weld’s direction. The flames are pointed towards the weld with the tip inclining at an angle of 45 to 60 degrees from the plates. This assists in the preheating of the edges being welded just before the molten puddle. The tip is moved back and forth in a semicircular position hence having a balance of heat between the rod and the walls of the base metal. This method is usually recommended for lighter tubing and sheet metals that do not exceed a thickness of 1/8 inch. Due to the nature of its ability to control the puddle, it results in a smooth weld and that is why it is recommended for the mentioned metals. However, it cannot perform well in heavy metals (Griffin 30).
Backhand Welding
In this method, the tip of the torch is placed in precedence of the rod towards the weld. The welder places the rod’s end between the puddle and the torch tip. Like the forehand welding, the angle remains between 45 and 60 from the joint being welded or the plates. Comparatively, the motion required in this method is less than that required in forehand welding. In the case of a straight rod, it should be rolled over and over again for an even distribution of heat. Otherwise the rod could be bent and moved together with the torch back and forth rapidly. This method calls for a back and forth movement of the torch across the weld while at the same time slowly advancing it in a uniform manner towards the weld’s direction. This method provides for a narrower “V” as compared to forehand welding. It is more recommended for thick metals that exceed 1/8 inch. In addition, it requires less puddle and rod as compared to forehand (Griffin 30).
Welding Positions
Whenever possible, the most appropriate position for welding in the flat position. At this position, it is easier to control the puddle and also it is less tedious. This position is however appropriate if the material is to be welded on the top side while it’s lain flat or near flat. On the other part, it is appropriate to apply for an overhead position if the material needs underside welding. It happens with the torch being pointed upward towards the joint. If the puddle is left to get too large, it might sag or assume a large drop-like shape. It is therefore the role of the rod to ensure that the puddle is put under control. In addition, this position requires less heat because heat tends to rise naturally (Finch 43).
When the work requires a horizontal line weld, a horizontal position is assumed. In this position, the torch assumes a horizontal direction towards the material being welded. While working, the weld should start from the right going to the left. Also, the welder should assume an upward inclination of the flame at an angle of about 45 to 65 degrees. It is appropriate with the forehand technique. As in the overhead position, the rod should be used for controlling the puddle from sagging towards the bead’s lower edge. The puddle should not be allowed to get overheated because this reduces its cohesive power (Finch 44).
Finally, there is the vertical position where the puddle greatly relies upon the pressure from the torch flame for support. In this position, the welder should ensure that he maintains a standard degree of heat and that the hot iron is not allowed to escape from the puddle. From time to time removal of the flame from the puddle is necessary because it prevents instances of overheating. In this position, the welds are begun from the bottom with an upward pushing of the puddle. This should be done with a forehand motion. The tip’s angle of inclination is 45 to 60 degrees. Rod addition is done from the top just in front of the flame (Finch 43).
Purposes of the different types of welding
There are several types of welding. Each type serves a specific function that suits it (Jeffus 29).
Electroslag welding
Also known as ESW, this type of welding allows for the depositing of weld metal within the cavity of the weld between the two metals being joined. To prevent puddles from running off, the joint is fitted with water-cooled copper dams. This method is recommended for horizontal welds on metals exceeding 36 inches.
Fluxed- core arc-welding
Also referred to as FCAW, this method uses flux-filled tube electrodes. In comparison with the SMAW coatings, this flux is less brittle. It is recommended for joining 1” metal sections or thicker. This is favorable because of its compliance with technology.
Gas metal-arc welding
Also referred to as metal inert gas, this method involves using an outside gas to shield the weld zone. The gases could be helium, argon, carbon dioxide or a medley of these. Due to its deoxidation ability, it can allow for multiple weld layers at the joint. This method employs low temperatures and is hence recommended for thin metals that are less than a quarter inch.
Plasma arc welding
This method employs the use of a very hot plasma jet generated from ionized gas and electrodes. This use of high energy concentration makes it a favorite for deep joints and narrow welds.
Gas tungsten arc welding
It is also referred to as tungsten inert gas. This method involves the generation of heat from tungsten electrodes as one pole of the arc. Where necessary, the molten material is provided by a filler wire. It is mostly recommended for thin welds that require excellent quality and a beautiful surface finish.
Current issues and Technological Changes
In the recent years, there have been witnessed various deaths and destruction of property as a result of collapsed buildings. The blame was laid on welding. Many analysts blamed the welders for doing shoddy work that could not sustain any pressure. This has resulted in the advancement of welding techniques to embrace the advancing technology to avert the recurrence of such cases. One of the notable improvements in the industry is the inclusion of the computer to predetermine the relative motion between the base metal and the heat source. This leads to a more secure and reliable weld. In addition to the use of computers, the industry has also witnessed the inclusion of robots that are “capable of multi-axial motion” to facilitate the motion (David & DebRoy 497).
In addition to this, the weld pool and other essential parameters’ location and size can be tracked. This is facilitated by a tracking system powered by infrared and other optical emissions. These assist in the determination of a precise weld. Due to the intensity of the heat, there is a formation of gas plasma that is electrically conducting around the weld pool. With the improvement of technology, the plasma pool is used as a monitor of the emissions of metal vapor by the weld pool (David & DebRoy 497). This becomes an important step towards the environment and health safety of the welders. This is also useful in laser welding as it gives an estimation of energy that is reaching the workpiece and estimating the arc’s electrical conductivity in gas-tungsten arc welding.
Conclusion
In conclusion, the role of welding in human society is indispensable. It therefore calls for more and more technological advances to improve the quality and reliability of the welding products. In addition, more and more research should be done to ensure the environmental and health safety of the welders. With all these observed, the profession will continue serving its important role to the community with ease.
Works Cited
Ares, Josa. Metal: forming, forging, and welding techniques. Hauppauge, NY: Barron’s Educational Services, 2006.
Austin, John. Electric arc welding. Chicago: American Technical Society, 1952.
Cary, Howard. Modern welding technology. Englewood Cliffs, NJ: Prentice-Hall, 1979.
David, A and DebRoy, T. Current Issues and Problems in Welding Science. Journal of Science. 257: 497-501. 1992. 2009. Web.
Finch, Richard. Performance welding handbook. St. Paul, MN : Motorbooks International, 2005.
Giachino, William. Welding technology. Chicago: American Technical Society, 1973.
Griffin, Ivan. Welding processes. Albany, NY: Delmar Publishers, 1978.
Jeffus, L. Welding: Principles and applications. Stamford, CT: Cengage Learning, 2002.
Pender, Angus. Welding. Toronto: McGraw-Hill Co. of Canada, 1968.
Ruth, K. Welding Basics: An introduction to practical & ornamental welding. New York: Creative Publishing International, 2003.