OM Forecasting
Apple’s OM forecasting is based on the bottom-up approach because the organization is focused on providing the best quality products. The inventory control department details the number of supplies that will be needed. Hence, the basis of Apple’s forecasting is qualitative techniques, such as time series analysis and projections because the company’s management assesses the type of products they will produce, their quantity, the quality, and the potential demand from the customer, after which the inventory department, using the history of the previous supplies creates the forecasts for the future.
Since Apple’s operational management strategy is focused on differentiation, the first step under the Seven Steps approach is the determination of which new product the forecast will be designed for; for example, a long-term forecast of the demand for the new iPhone. Next, the key KPIs must be set, such as product quality or quantity of sales for the new smartphone. Based on the previous metrics, the management can choose the accuracy of data they will require; for example, it is essential not to underestimate the demand for the new phone as this will result in financial losses and delays with deliveries. At the final stages, the management collects the data, for example, from its past smartphone releases and from its suppliers, to make a forecast model. The ethical considerations with this approach may be linked to Apple’s sourcing strategy, as the majority of their products are manufactured in China.
Quality Management
Common OM quality management best practices include quality management planning, Six Sigma, and Lean practices, among others. Apple appears to be using the Six Sigma approach as its primary quality management tool. Figure 1 in the Appendix shows the house of quality chart for Apple’s new packaging. The main characteristics that are important in this case are the design, capacity, strength, and resistance. The product characteristics were selected based on Apple’s current packaging design because the company focuses on minimizing waste and using the least amount of materials for its packaging while ensuring it is durable. These characteristics are met by creating ergonomic packaging from premium materials.
Supply Chain Management
Apple’s supply chain management strategy is based on the diversification of suppliers, as the company cooperates with hundreds of suppliers globally. The basis for the determination is the cost of inventory and quality. Apple uses advanced technology to manage its inventory and supply chains, such as tracking devices for warehouses and data management systems (Pulungan et al., 2018). The main SCM risk for Apple is the growing cost of production in China and rates of freight shipping, which increased during the pandemic and the disruption of the global supply chains. Ethical considerations related to work practices and fair wages are the main problems in developing countries, where most of Apple’s suppliers are.
Inventory Management
The process of ordering, storing, using, and selling a company’s inventory is referred to as inventory management. This comprises the storage and processing of raw materials, components, and completed products, as well as the administration of raw materials, components, and final products (Hayes, 2022). Inventory management is important because it allows the organizations to maintain the stock they need for manufacturing at the moment. Common inventory models include Just-in-Time, Materials requirement planning, Economic Order Quantity, and days sales of inventory (Hayes, 2022). Apple uses the Just-in_time approach, which helps the organization minimize waste and maintain the low cost of the working capital. However, from an ethical perspective, this approach makes Apple highly reliant on its suppliers, and any disruptions, such as lack of raw materials or high cost, would directly affect the production.
References
Hayes, A. (2022). Inventory management. Web.
Pulungan, M. D., Nadira, N., & Dewi, I. A. (2018). Re-design of apple pia packaging using quality function deployment method. International Conference on Green Agro-industry and Bioeconomy. Web.
Appendix
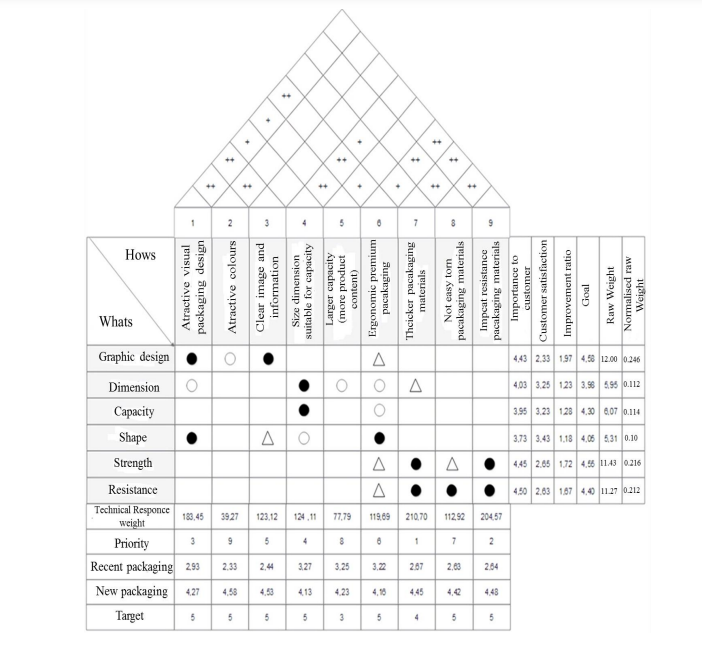