Apple iPhone Supply Chain: Introduction
Supply Chain Management (SCM) is the design and implementation of processes to manage movement and storage of raw materials, work in progress, finished goods, and consumables, from various points of origins to their destination. Modern firms procure raw materials and components from vendors that are further processed and sold as finished goods. A car will have hundreds of components while smart phones would have large number of parts and sub assemblies. Scale of economies, product specialization, and cost saving, allows vendors to take up dedicated manufacturing and assembly of these components. Original Equipment Manufacturers (OEMs) such as Apple Inc., Ford, Dell, and other firms procure these components from low cost manufacturing countries such as China and India, assemble and sell products under their own brand name. Considering the huge distance involved in moving components from across continents, SCM facilitates OEMs to manage their supply chains. The challenge is to add value to each step in the supply chain, obtain deliveries of the right quality of goods, in required quantities, at the right time, and at the right costs (Christopher, 2016). This paper analyzes SCM practices for Apple iPhone.
Supply chain of iPhone
Apple iPhones are very popular and considered as status symbols. Apple sells more than 250 million units per year. It is interesting to note that 100% of components are outsourced, and the devices are assembled in China by Foxconn and Pegatron at their plants in Guangdon, Henan, Shanxi, and Shanghai. An iPhone 7 that retails at more than $700/ unit has direct material costs of $215 and conversion costs of $5 per unit, yielding a gross profit of $480/ unit. An efficient supply chain with dedicated and disciplined suppliers, high security with no supply disruptions, has allowed Apple to gain a huge competitive advantage. Interestingly, Apple has managed to replicate the supply chain for all iPhone models (Barker, 2014).
Apple has more than 1180 part suppliers, spread across 31 countries. China has 349 suppliers, followed by 139 in Japan, 60 in USA, 30 in Korea, and the rest spread across Hungary, Malta, Germany, Italy, Mexico, and other countries. These vendors supply components such as display, camera, battery, processor, RAM chips, touch screen, and many other components, to assembly centers in China. Robots are used for assembly of critical processes such as mother boards, soldering of circuits, and other operations, while workers assemble RAM, batteries, and carry out manual testing, inspection, and packing. Use of automation for critical processes increases speed and reduces defects (24/7 Staff, 2016).
Packed iPhones along with chargers, headphones, booklets, etc. are dispatched to distribution centers across the world. The whole operation of SCM is controlled with powerful SCM software that controls scheduling, arranges for pickup and delivery up to dealers. A reverse SCM collects defective items, items under warranty, and units that can be repaired for further actions (Quarterman, 2012). Following figure illustrates the forward supply chain for two critical components, touch screen display supplied by LG of Korea (Smith, 2017) and Camera supplied by Sony, Japan (Cole, 2013; Wuerthele, 2017).
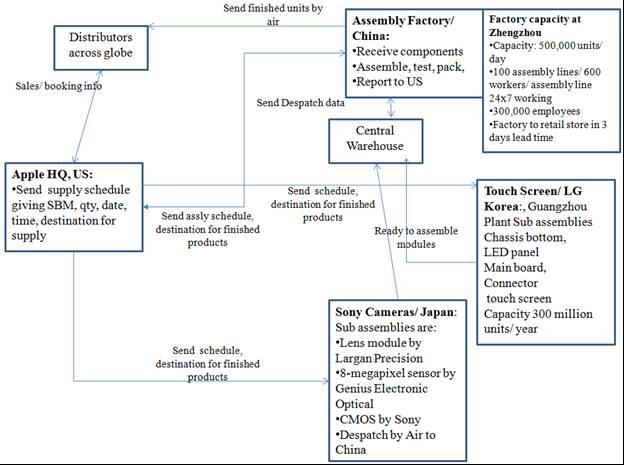
Elements of the forward supply chain are explained as below.
Supply Chain of iPhone: Apple HQ, USA
The headquarters and its branches provide the design with the summary bill of materials giving specification for the iPhone model. The SBM details component specifications, quantity required per unit and performance requirements. The vendor development and purchase department have a list of preferred vendors for all parts. Confidentially agreements, purchase orders, part drawings, specifications, quality and performance requirements and daily, weekly schedule are sent to vendors such as Sony and LG Display. These vendors procure raw materials, contact their suppliers, obtain deliveries, and assemble the components.
Supply Chain of iPhone: Assembly Factory, China
Contract assembly vendors such as Foxconn and Pegatron who have large plants in China, arrange for material receipt from vendors, plan the assembly lines as per the required output, and begin assembly. As indicated in Figure 1, the plant has a capacity of 500,000 units/ day, when a new product is launched. A just in time approach is required since idle inventory is a problem and excess or short supply is not allowed. Therefore, the supply chain must ensure the right quantity of parts is delivered at the required time. Finished and packed products are sent to regional headquarters and dealers in different countries (Marshall, McCarthy, McGrath, and Harrigan, 2016).
Supply Chain of iPhone: Sony Cameras and LG Display
Sony manufactures cameras in Japan and LG in South Korea. The vendors receive purchase orders giving the schedule breakup with quantity and delivery dates. Ready to assemble and first time right principles are used. Vendors also send spares to authorized repair centers in different countries, when indents are raised (Marshall et. al 2016).
Reverse iPhone Supply Chain Map
The reverse supply chain is used to send defective products, damaged goods under warranty, and unsold inventory, customer exchange for upgrades, items for recycling, etc. Number of elements is less in the reverse supply chain (Lockamy, 2017). Following figure illustrates the reverse supply chain.
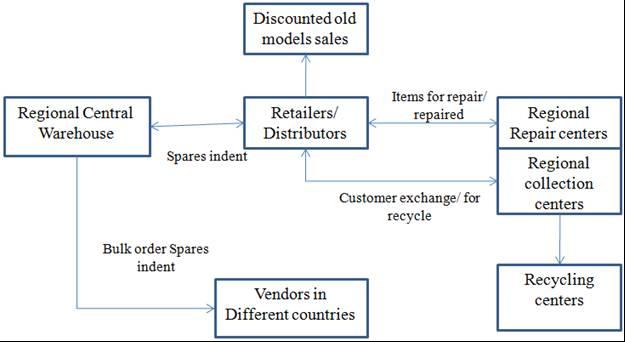
As seen in Figure 2, different elements of the reverse supply chain are illustrated. Customers approach regional repair centers for phone repairs or replacement. The repair center indents spares from retail distributors who contact regional central warehouses. If the item cannot be repaired, then it is recycled. Customers exchange old models with new ones, and the old units are refurbished and sold in the secondary market. Old models and units that cannot be repaired are recycled.
SIPOC Chart for the Supply Chain of iPhone
The suppliers, inputs, process, outputs, and customers (SIPOC) tool is used for process analysis and improvement. The tool is used to chart the forward supply chain of iPhones, illustrated in Figure 1.
Two performance measures at each SIPOC element
The two elements are Sony Camera and LG Display. Performance measures for these two elements are discussed as follows.
Performance measure of Sony Camera: The two performance measures analyzed are: ability to manufacture as per specifications and on time delivery. Cameras of iPhones see regular upgrade and design changes. The design changes may not be major, in the sense that the Mega Pixels would not change. However, internal parts specification, the manner in which image data is gathered and processed may be changed. In such cases, Sony needs to procure parts to meet the requirements and assemble the cameras. If Sony cannot manage these complexities, the assemblies will be rejected. On-time delivery implies that components are of the required quality and specification, and supplied in a ready to use condition. Apple plant does not have the resources to test Sony cameras and see if they work as per specifications. Therefore, quality is implicit (Lockamy, 2017).
Performance measure of LG Display: The two performance measures analyzed are: ability to fulfill orders for multiple models and languages and no errors in packaging and dispatch. LG Display supplies touch screen used to run the menus and options. Users in non English speaking countries such as China, Japan, France, Germany, and others, need a user interface in their language. A person in France will not be able to use a display in Chinese. Hence, labeling and packaging must be exact. Another performance measure is the ability to fulfill orders for different models. Apple still sells the earlier models, and requires spares for these older models. When urgent requirement of spares for older models are raised, then LG must be able to manufacture and dispatch the required parts (Lockamy, 2017).
One risk at each SIPOC element
Incapable of handling and manufacturing as per specifications: Apple iPhones are complex in their design, and each component has a role to play. If the manufacturer is incapable of handling these complexities, omits certain intricate design requirements, then the component and the product will fail (Lockamy, 2017).
Customer faces large failures in testing, product recall, and user complaints: Due to the high volume assembly at rapid speed and limited inspection, the phone is not fully tested. Problems such as battery overheating or exploding can create fear and negative publicity. Even a couple of failed product among millions, create bad publicity (Lockamy, 2017).
Apple iPhone Supply Chain: Conclusions
The paper examined Apple iPhone and analyzed two suppliers, Sony Camera and LG Display. The SIPOC framework was applied for the analysis. Apple maintains a robust supply chain that provides a high value addition. The discussion shows that Apple outsources its parts and assembly of the iPhone to a large number of vendors. These vendors are able to meet the peak demand of 500,000 units per day. The SIPO analysis helped to understand the supply chain performance measures and risks for the five elements. Accepting these risks, Apple has ensured that the suppliers are spread across different countries. This strategy ensures that if a vendor in one country cannot supply the components, other vendors can provide the deliveries.
References
Barker, I. (2014). The global supply chain behind the iPhone 6. Beta News. Web.
Barner, C. (2012). Social media and communication. New York, NY: Sage.
Brownlie, D. (2012). Andragogy. Web.
Christopher, M. (2016). Logistics & supply chain management. Pearson UK.
Cole, S. (2013). Foxconn building 500K iPhone 5s units for Apple per day with nonstop production lines. Apple Insider. Web.
Lockamy, A. (2017). An examination of external risk factors in Apple Inc.’s supply chain. Supply Chain Forum: An International Journal, 18(3), 34-46.
Marshall, D., McCarthy, L., McGrath, P., & Harrigan, F. (2016). What’s Your Strategy for Supply Chain Disclosure?. MIT Sloan Management Review, 57(2), 37-43.
Smith, C. (2015). LG investment adds new fuel to reports that Apple is planning an OLED iPhone. BGR. Web.
Supply Chain 24/7. (2016). Apple’s Supply Chain Cost of Making the iPhone 7. Supply Chain 24/7. Web.
Quarterman, L. (2012). Apple, Foxconn & Manufacturing Strategy. Strategos, Inc. Web.
Wuerthele, M. (2017). Sony prioritizing Apple’s supply of iPhone cameras, cutting back on other vendors. Apple Insider. Web.