Occupational exoskeletons are mechanical constructs worn by humans to improve physical performance and reduce musculoskeletal diseases. Active exoskeletons employ actuators (machine components responsible for physical movement) to drive the system, whereas passive exoskeletons use human activity to power the system. Electric motors, levers, and pneumatic or hydraulic technologies are used as actuators in active devices, whereas materials, springs, and dampers are used to redirect kinetic energy in passive devices. Active and passive systems are offered in joint-specific, body region-specific, and full-body configurations.
Parts and Process
The equipment produced and developed by Ekso Bionics, inc., includes magnetic components, features, and working principles unique to EksoVest. The characteristics and equipment of the bionic EksoVest are described in their manual document (Manualslib.com, n.d.), consisting of a handbook for its use. Each EksoVest includes the hardware, components, and well-balanced, delicate items discussed before. Using the size tables and matrix, each operator chooses the mild things with their vest. The operator sews the light personalized elements onto the vest’s chest, waist, and arm cuff plates. With lifts ranging from 5 to 15 pounds, EksoVest can help. With sizes ranging from 5’2 to 6’4 feet, the vest’s modular construction allows it to fit many body forms.
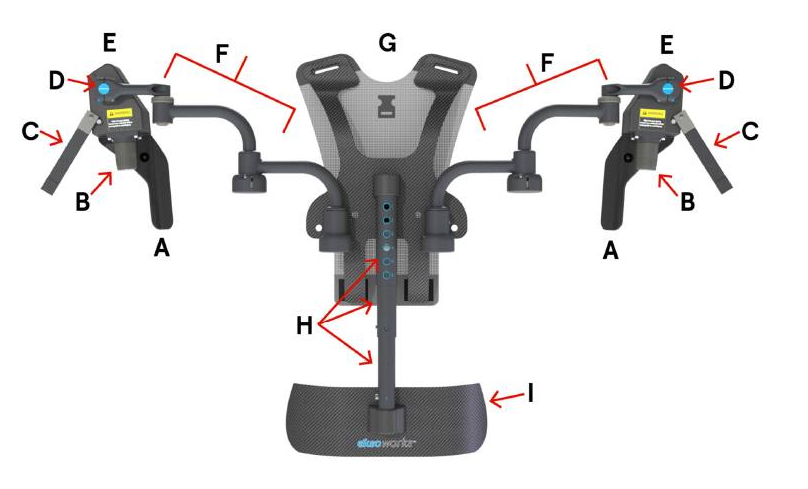
At the same time, Ekso Bionics provided iterations to meet the demands of their employees. The collaboration between the two businesses resulted in developing a lightweight, comfortable upper-body exoskeleton (Jones, 2018). This machine delivers a large amount of lift during overhead movements, lowering the danger of shoulder muscle damage and strain. A passive spring-driven actuator drives the EksoVest at each shoulder during a charge, providing torque to the user’s arms. When the user lifts their arm, the actuator engages, causing tension in both arms and allowing the EksoVest to give 5-15 pounds of movement support, depending on which spring is utilized (McGowan & Beltzman, 2020). The vest’s modular architecture will enable it to accommodate a variety of body shapes, with sizes ranging from 5’2 to 6’4. The EksoVEST is entirely mechanical and does not require any electrical or battery power to perform FES treatment.
The use of the exoskeletons could be viewed from the point of the process. The procedure takes into account four support categories (Hand, Shoulder, Trunk, and Arm), as well as the mode of actuation. Moreover, it might include force sensors, inertial measurement units, strain gauges, and dry EMGS that are used to detect user movement or intention of activity for any given use-case (McGowan & Beltzman, 2020). The four steps of the testing procedure are identifying the appropriate exoskeleton for the specified high-risk use case, laboratory validation, pilot testing, and in-line testing. It may determine how well an exoskeleton’s features meet the user requirements for the specified use case. The selected item’s impact, appropriation, usefulness, usability, and safety on the end-user are currently evaluated factors. Using this technique to design has been demonstrated to enhance user muscle activity, range of motion, and productivity when doing simulated, use-specific activities.
Occupational exoskeletons are used in Ford industry for various purposes. Workers in Ford manufacturing benefit from bionic vests since they improve and facilitate their working circumstances. An illustrative example shown in the CBC video demonstrates that the elements of operation and the benefits and drawbacks of various bionic vests (CBC [CBC News: The National], 2018). According to the information supplied in the movie, vests do not require a specific power source. The procedure is based only on mechanical movement, which allows for a qualitative reduction in the strain on the worker’s body. The questioned gadget operator claims that the vest is quite beneficial to him.
Even when one cycle of industrial activities has a slight constraint, its repeated recurrence might be uncomfortable. The strain on the body merely grows, and tension builds up in the muscles and throughout the body (CBC [CBC News: The National], 2018). In this situation, the bionic vest allows the user to cycle between tasks while the load is transferred to the device. According to the video, despite the benefits mentioned earlier, the gadget is still expensive.
Analysis
Ford’s usage of EksoVest, a device developed and manufactured by Ekso Bionics, inc, is also a compelling illustration of technology application. In what is considered to be the largest deployment of the technology to date, Ford Motor Company is installing 75 upper-body exoskeletons across 15 sites in the United States, Canada, Mexico, Brazil, Romania, and China (Jones, 2018). Ford uses EksoVest technology from Ekso Bionics to provide continuous structural protection for employees performing overhead tasks that need them to reach aloft for long periods of time.
Ekso was investigating application usage when Ford attempted to introduce exoskeletons in its workforce, and the two firms agreed. According to Ekso, the collaboration began when an early prototype received a positive response from Ford, which provided several practical recommendations (Jones, 2018). Moreover, Ford supplied a testing environment and critical comments on design concepts.
Moreover, occupational exoskeletons have progressed from idea to reality during the last few years. They’ve become widely available and are employed in a variety of fields. Their primary goal is to improve human performance. Most suppliers claim that they accomplish so by reducing musculoskeletal diseases or MSDs, enhancing worker stamina, improving job quality while increasing productivity, and keeping the workplace healthy in general. It is possible that there will be unexpected consequences for industry and there aren’t any, and it would seem nonsensical not to use exoskeletons. Until now, there hasn’t been a defined method or set of rules for assessing end-user needs and exoskeleton specificity until now (McGowan & Beltzman, 2020). MSDs can arise when the job, or in this example, the exoskeleton, does not fit the worker. Fortunately, researchers have created a new approach for evaluating occupational exoskeletons under job-specific operating circumstances, complete with defined rules.
Occupational exoskeletons are now being developed to avoid lower back discomfort and shoulder tendon injury by reducing muscular activity in the back and shoulders. Exoskeletons have been shown to lower localized muscle activity in the past. However, there is a risk of injury. Because the entire musculoskeletal system is interrelated, reducing one muscle’s or structure’s work implies moving that task to another muscle or structure (McGowan & Beltzman, 2020). Depending on the action, this might influence the same powers or ultimately cause another group of muscles to respond when doing the same activity differently, all of which could pose new hazards to the system.
Exoskeletons for the workplace have many promises, but they still have issues that need to be improved. In their current condition, these devices minimize localized muscle activity by distributing the stress across the musculoskeletal system (Jones, 2018). Depending on the gadget, the user, and the environment, this mode of action exposes additional locations to unknown and potentially hazardous pressures. Additionally, if a nerve is crushed or a tendon is torn, unnatural motions and forced lengthy postures might result in long-term harm. If the body responds to chronic movement constraints like wrist braces or back belts, there is a risk of muscle disuse atrophy or shrinking, deconditioning, and structural weakness. If the body responds to chronic movement constraints like wrist braces or back belts, there is a risk of muscle disuse atrophy, deconditioning, and structural weakness.
References
CBC [CBC News: The National]. (2018). A bionic vest decreases fatigue and prevents injury | The Fix [Video]. YouTube. Web.
EksoVest. (n.d.). The mechanical and hardware components of EksoVest [Illustration]. ManualsLib. Web.
Jones, D. (2018). Ford rolls out largest adoption of exoskeleton technology to date. Design Engineering. Web.
Manualslib.com. (n.d.). Vest hardware – ekso bionics EksoVest operator’s manual | ManualsLib. ManualsLib. Web.
McGowan, B., & Beltzman, B. (2020). StackPath. EHS Today. Web.