Abstract
Ergonomics is a consideration of several factors within a manufacturing plant, i.e. the environment, the work station, the task, the tool, and the organization itself which bears the culture. This dissertation focused on ergonomics intervention and quality implementation at Kemya chemical manufacturing plant. This company has been in the forefront of ergonomics and quality applications but there have been some errors and defects in the implementation leading to workers’ injuries and a number of shutdowns.
Product quality, employee performance and organizational output are affected by factors such as inappropriate total quality management (TQM), or ergonomics problems. This dissertation will focus on the two factors – quality management and ergonomics interventions. This study conducted a survey on employees of the plant, and recommended ergonomics interventions on the work area and physical environment.
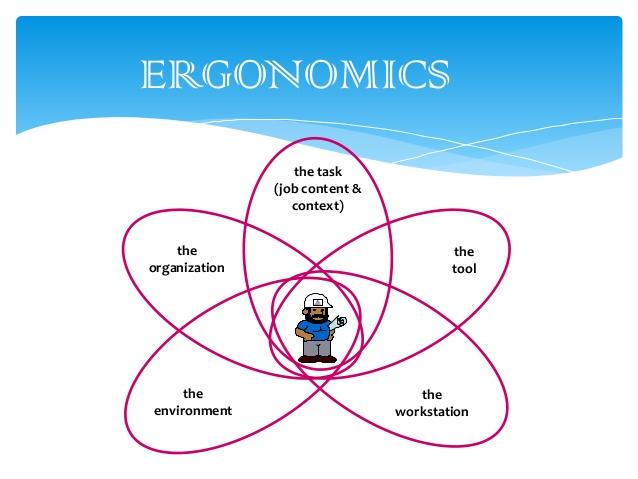
The questionnaire was in the form of open- and closed-ended questions and the results of the survey were analysed by means of descriptive method. Kemya does not have to spend large amounts of money, because the manufacturing plant has continuously applied ergonomics interventions and quality management. The application for QUITE (Quality Improvement through Ergonomics) methodology was recommended for Kemya.
Chapter 1: Introduction
Introduction
Ergonomics should be proactive, in addition to being reactive. Proactive ergonomics reduce injury and enhances coordination between worker and environment. The ultimate aim is for quality production, since successful ergonomics enhance worker performance, organizational output, and reduce absenteeism and turnover rate.
In an ergonomics activity, the ergonomics team has to assess the work area with the aim of providing solution to the reported risks that caused injury and discomfort. The firm could be dealing with financial problems, which has resulted in administrative measures like providing breaks between manufacturing processes, or changing work strategies so that some equipment or parts can be in a neutral position. Such measures are difficult to manage and tolerate over time, and can cause ergonomic problems.
Ergonomics is the science of properly fitting the work environment to a worker; it also refers to adjusting the worker’s to the work environment, ensuring that the workplace and the parts therein are specifically positioned. In a computer room, for instance, the chair, monitor, mouse, and keyboard must be properly positioned so that the user will not acquire backaches or musculoskeletal and cumulative trauma. In the manufacturing sector, ergonomics refers to the different areas in manufacturing that should fit the workers’ physical body, make them safe from injury and allow some comfort while working (Piatt, 2012).
Ergonomics guidelines and company policies should include adequate training and development and installation of appropriate equipment in order to reduce the risk factors related to injury or accident. It is hard to think that repetitive tasks like using the usual equipment for extended amounts of time could cause injuries. Not being in an appropriate position can cause discomfort or musculoskeletal disorder (MSD). MSDs are also referred to as repetitive stress injuries (RSI) and cumulative trauma disorders (CTD) (Stanger, 2002). This is one of the main problems being addressed by ergonomics.
There can be other ergonomic factors in the workplace such as noise, lighting, and safety measures. The objective of using proper ergonomics is to enable a person to perform his or her job in a natural, comfortable position. The body’s natural position is also known as a neutral position. While using instruments or manufacturing parts, the worker is at a safe distance and uses protective clothes and gloves.
This study focused on the operational problems in a manufacturing plant at KEMYA to find out how ergonomics can be properly applied. Currently, the company employs approximately 600 workers, mostly Saudi nationals. The company also answers to the call of environmental preservation by applying a rigorous waste management system and effective safety measures (ExxonMobil, 2016).
Aim and Objectives
This study aims to address the ergonomics problems of a manufacturing plant at Kemya. Particularly, the study examined how QUITE (Quality Improvement Through Ergonomics) methodology could improve workers’ performance.
Objectives
To determine how the company practices quality and ergonomics intervention at the manufacturing plant;
- To investigate how ergonomics intervention can be improved and enhance worker performance;
- To provide recommendations for further ergonomics intervention at Kemya.
Hypothesis
Ergonomics interventions should parallel quality implementation. The Kemya LDPE plant must continuously adopt ergonomics innovations to avoid safety issues and reduce the number of shutdowns and turnover of employees.
Rationale of the study
This is a case study about ergonomics implementation in a manufacturing plant at Kemya. The in-depth analysis of the problems and solutions will help in reducing errors and defects in ergonomics intervention, and encourage other manufacturing plants in Saudi Arabia and the Middle East.
This study has provided a background and application processes for QUITE (Quality Improvement Through Ergonomics) methodology, and has recommended that this be applied to the manufacturing plant. The different methods of QUITE application are explained in the literature and in the methodology.
Businesses have been finding ways to reduce cost of operation, while increasing profits. This runs counter to the principle of good business, and might have negative repercussions in the aspect of organizational performance. Expenditures associated with lower quality and reduced worker performance include: additional expenses for workers’ compensation and insurance premiums, lower productivity and low morale of employees, and additional cost in recruiting new employees as replacement for the sick ones and those who have been forced to stay on the job.
Chapter 2: Literature Review
Introduction
The predominant culture in many Saudi organisations has evolved from a nomadic ethnic community to the comfortable resource rich economy and from the traditional small-time trader to the new businessman influenced by western and other cultures. The Saudi businessman’s concept of TQM is unique from the concept borne of Western culture. TQM, according to the Saudi culture, is attaining total quality by drawing the commitment of every member of the organisation.
The Saudi’s approach to quality management is characterised by the short-term view in contrast to the Japanese and Western’s long-term view; the Saudi’s instant results-expected to the former’s results-oriented; and the Saudi’s contingency style to the Western’s step-by-step building and quick-fix (Al-Darrab, Gulzar, & Ali, 2015).
Saudi Arabia has one of the most unwavering and dynamic economies of the world because of its effective and well-managed use of resources, particularly oil. The reforms initiated have made the country one of the world’s top growing economies. However, to become a truly industrialised country is yet to be achieved (Al-Darrab et al., 2013).
With globalisation, the country is experiencing the influx of foreign products supported by oil-based economy. This continuous economic growth is primarily due to the Saudi leadership’s policy decisions and its shift to focus on international business. Saudi Arabia is heading for industrialisation and this will surely affect the economy and the Saudi people. The oil sector accounts for approximately 80 percent of the budget revenues and almost half of the gross domestic product (GDP) (Al-Darrab et al., 2013).
Kemya was officially established in 1980 with a specific task of manufacturing low-density polyethylene (LDPE) and other chemicals like ethylene and olefin. The plant can produce approximately 700,000 tonnes of ethylene annually and a staggering 1.1 million tonnes of polyethylene serving local and foreign markets (ExxonMobil, 2016). The company has helped boast Saudi Arabia’s economy, which largely depends on oil.
Background
The relationship between the physical body and the workplace has been researched for many years (Piatt, 2012). The first known studies of this phenomenon occurred around the mid-1940s, just when the war ended. At first, ergonomic was often defined as the relationship between man and machine, fitting man to the job or “human factors” (Branton as cited in Piatt, 2012).
As the post-industrial age transformed into the information revolution a new set of challenges arose that possibly put office workers at potential risk of injuries (Murrell as cited in Piatt, 2012). The early studies provided the findings and insights for today’s ergonomists to seek ways to control and change the work environments to fit a person to the job.
The psychologist Bartlett (as cited in Piatt, 2012) was considered one of the founders of ergonomics. In 1962, Bartlett presented a paper on the future of ergonomics at the Ergonomics Research Society, where he predicted that in the future, new technology would bring about isolation of individuals, combining workloads from several individuals to one, increasing mental workload and a decrease in physical workload together with a greater demand on communication via means of advanced technology.
Bartlett predicted the rise of computers and the internet. However, in an earlier paper he discussed the concept of fitting man to the job. For example, instructing or showing people how to place or position themselves in using equipment, allowing one’s body to adapt to its work environment. These concepts are foundations of today’s ergonomics, where office ergonomics best practices fit the workplace environment to the person.
Moreover, the Occupational Safety and Health Act of the United States requires “employers to prepare and maintain records of occupational injuries and illnesses” (Rethaber, 2010). Saudi Arabia has the General Organization for Social Insurance (GOSI) which keeps records of occupational injuries and illnesses. Safety experts, most of whom are private businesses or insurance companies, now have years of data that show patterns in work-related injuries caused by physical repetitive stress.
In 2014, Saudi Arabia reported 69,000 work injuries, with the construction sector having the highest number (Latif, 2016). GOSI reported that the construction and manufacturing industries have the most number of work-related injuries, accounting to approximately 355,000 injuries recorded in 2016, where most of the victims were expatriate workers (Ace Brokers, 2016). The country has increasing development projects which explain the growing number of work-related accidents and injuries.
The significance of ergonomics was established some decades back but what was not known at the time was that musculoskeletal disorders (MSDs) were acquired in the workplace setting. However, the increased awareness of office ergonomics was triggered by the information revolution and longer time in the office.
Definitions and Concepts
Ergonomic is defined as a process for improving manufacturing systems and products by means of careful and orderly study of how they relate with their users (Stanger, 2002). Ergonomic also refers to high technology improvement process. Biomechanics is the decision tool that allows a professional to set exposure limits that can help prevent injuries.
Many companies conduct ergonomics with the aim of solving injury problems, but they become frustrated when their steps prove ineffective. Ergonomic programs fail because of some factors. Common mistakes in ergonomics implementation include: having an incomplete understanding of ergonomics and human characteristics, and non-ergonomic methods are included to control injuries that limit the scope and effectiveness of ergonomic programs (Kelby, 2014).
Ergonomics grew out of the need to better accommodate military personnel during World War II, but in the study of Stanger (2002), he found it interesting that what was developed as a tool to make war winnable is now the preferred technique for preventing musculoskeletal injuries in the workplace.
The advantage of ergonomics is its being proactive, although some organisations conduct reactive applications. In the previous paragraphs, ergonomic evaluations involved the assessment of an existing work area and reduction of risk factors. We need not wait for injuries to occur. A proactive approach to workplace ergonomics permits problems to be addressed right away before an injury occurs (White, 2015). Ergonomic has many other benefits that management fails to see. It can increase activity in the workplace and motivate employees to perform better for up to 10% to 15% enhanced activity (MacLeod as cited in White, 2015).
The company should be able to design a job that can provide comfort for the worker’s environment , with minimum force exertions and fewer motions; this way the work environment becomes more effective. Workers feel more comfortable, perform more efficiently and increase overall job satisfaction and reduce turnover. Quality is improved with an effective ergonomic intervention.
According to White (2015), a study in an assembly plant found that quality defects were three times as common for poorly designed ergonomic tasks compared with the others. The study also found a relationship between employee satisfaction and product quality. Workers become contented with their jobs when they feel they are producing quality product (White, 2015).
With positive features of ergonomics, the benefits are enormous for the company and its employees and the customers as well. Most problems of ergonomics are based around the workplace environment. Therefore, proactive ergonomic eliminates risk factors to not only reduce the risk of injury, but also to attain benefits in the workplace environment.
The design phase is significant because the available resources are seen and there is a high tendency to affect a final setup of the work arrangement (White, 2015). With these ergonomic benefits, one can still ask why many facilities or production plants do not give much attention on ergonomics application. This poses a challenge to policy makers and to managements of organisations as well. Proactive ergonomics is the best choice, but up to this time the traditional focus on ergonomics has always been based on reaction. (White, 2015).
Quality improvement to enhance worker performance at Kemya
Ergonomic interventions were applied in the human-machine work environment. The distance between machine and operator is significant: the operator should be a foot away, but the machine must have protective device to prevent accident when the operator controls the machine. Moreover, with automation the operator can control the machine without touching it; even then there comes a time that the operator has to “touch” the machine, for instance, during maintenance work. When chemical and machine are involved, the operator should wear protective gloves all the time.
These past few years, the company experienced a number of shutdowns which threatened production quality. Debottlenecking measures involved ergonomics intervention in the LDPE plant, which were quite unsuccessful in September 2015. As a result, there were a number of shutdowns, threatening plant productivity (ExxonMobil, 2016).
Ergonomics interventions are popular in the car industry. Some examples include that at the Volvo car manufacturing plant, ergonomics programs are a part of quality strategy. Poor employee performance is an outcome of ergonomics problems (Erdinc & Vayvay, 2008). Ergonomics intervention was applied to work posture in metal folding task, which was applied through Rapid Upper Limb Assessment (RULA) (McAtamney & Corlett, 1993 as cited in Erdinc & Vayvay, 2008). As a result, percentage of error and rejected products were reduced, leading to an annual saving of $20,000. In a plant producing printed circuit board, visual inspection was improved through increased accuracy with the introduction of ergonomic reference colours. Rejected boards were reduced and product quality enhanced. Time for component insertion in printed circuit boards was reduced by improving the design of insertion lines, introducing color-coded transistors, and provided easy-to-read polarity of diodes in the circuit (Erdinc & Vayvay, 2008).
Quality Improvement Through Ergonomics (QUITE)
Ergonomics is about quality and enhanced quality performance of employees.
Studies have found that poor employee performance in manufacturing, such as poor quality application may be the result of ergonomics problems (Munck-Ulfsfält et al. as cited in Erdinc & Vayvay, 2008). Researchers recommend regular ergonomics interventions to eliminate problems and enhance employee performance.
The methodology known as “Quality improvement through ergonomics” (QUITE) has become popular. It was designed in such a way that it can be applied in quality systems or in projects with existing quality applications. This methodology is applicable for manufacturing plants which have observed the following requirements: (1) there is a great amount of human participation through ergonomics principles that can enhance positive quality performance; (2) quality results are constantly checked particularly in operational aspects that use quality data and markers upon which ergonomics problems are related (this should be implemented by at least a quality department to the corporate level implementing quality management systems); (3) the process of quality management and ergonomics interventions are on a regular and continuous improvement strategy, such that it would bring a remarkable improvement to the work environment (Erdinc & Vayvay, 2008).
Ergonomics training should concentrate on enhancing employees’ knowledge on issues significant to occupational health, safety production quality. Knowledge and learning should lead to enhanced quality, improved physical postures, developed workstation design and the overall workplace environment. Another example is the ergonomics interventions in a metal manufacturing plant wherein material handling processes were reduced and accessibility of the materials was enhanced, including improvement of lighting conditions and other plant procedures (Axelsson as cited in Erdinc & Vayvay, 2008).
The ergonomics applications improve can improve the work environment, with workers on site as implementers of change. Ergonomics interventions and quality applications should be provided with technical know-how and with top management commitment and support. Drawing the technical and organisational perspectives need systematic, inclusive, appropriate methods that will lead to enhanced quality in manufacturing (Beatty; Govindaraju et al.; Hagt; Oakland & Tanner as cited in Erdinc & Vayvay, 2008). What are specified examples above are case studies but ergonomics and quality improvement methodologies, according to Erdinc and Vayvay (2008), are seldom studied and applied.
Ergonomics and Quality Management Systems
Ergonomics is related with quality management and ISO 9000 because it involves quality application, which is what ergonomics are all about. ISO 9000 involves the application of TQM, which emphasizes process efficiency. In the 1920s, W.E. Deming headed a group of the Bell Lab at the Western Electric’s Hawthorne Plant, which first introduced quality in telephones.
The group regarded quality as a kind of philosophy because it not only improved quality in the different areas like manufacturing, service, government, and education, but it also made their lives better. Deming is the most popular of the quality proponents; he helped Japan stand up to its feet after World War II by introducing quality to Japanese manufacturers. Deming introduced the statistical process control (SPC) and other quality techniques in manufacturing (Greer, 2001).
Deming’s quality improvement is similar to ergonomics which became popular in the 1990s. Deming introduced transformation and improvement of the practice of quality management (Anderson et al. as cited in Greer, 2001). Deming’s method includes “visionary leadership, internal and external cooperation, learning, process management, continuous improvement, employee fulfilment and customer satisfaction” (Greer, 2001).
Total Quality Management (TQM)
Total quality management is about focusing on customer needs and process improvements. Companies incorporate the elements in quality enhancement purposely to enhance market share (Chen & Chen as cited in Guion, 2010). With the rise of globalisation, the need for quality management techniques is a must. Because of the growing level of complexities in making products that suit to customers’ need, companies have to employ different quality management methodologies.
Although quality strategy may differ in the implementation method, the emphasis on relevant values of quality management are similar; when these are used properly, the outcomes are synonymous, such as increased profitability, competitive advantage, and increased market share (Popa, 2011).
Ergonomics has some similarities with other quality management philosophies and methodologies, in terms of context and quality application. These similarities can be found in process improvement strategies, like total quality management (TQM), just-in-time (JIT), lean manufacturing, six sigma, and supply chain management.
The literature has provided examples of successful implementation through systems thinking, functional integration, and enhanced communication infrastructures. These practices require managers/supervisors to work on cross-functional implementation teams and participate in a combined decision-making process (Gupta & Boyd, 2008).
TQM is more on continual improvement and focus on customer requirements, reduction of work processes, encouragement of long-term goals, and enhancing employee commitment and teamwork. TQM is a combination of quality and management tools to increase business profits and reduce losses (Gupta & Boyd, 2008). In the manufacturing sector, TQM refers to the firm’s ability to follow specifications. In the ISO International Standards Organisation) perspective, TQM is the totality of the qualities and traits of a product or service that satisfy customer needs and wants (Popa, 2011).
The study by Lin et al. (as cited in Almgren & Schaurig, 2012) found a direct relationship between quality and 2 ergonomic features, i.e. “time pressure and postural stress”. This was conducted to compare non-automation and semi-automation at a camera production plant. Mistakes were recorded every week to detect the causes of the mistakes.
The time for task completion and the posture of the workers’ physical body were considered the important variables. It was then found that more errors were committed when the task was done for a longer time which caused stress on the worker (e.g. headaches and muscle pains), and the worker’s posture caused back pains. (Almgren & Schaurig, 2012).
A study at a car manufacturing plant by Falck (as cited in Almgren & Schaurig, 2012) also found a relationship between ergonomics and quality, where ergonomically deficient task caused more errors than an ergonomically efficient task. The finding stated that the time to do a work task affected the effectiveness to do the task, i.e. the longer the work was done, the more errors were recorded and the shorter time the work task was done, the lesser the errors. The conclusion had similar results with the study by Lin et al. (as cited in Almgren & Schaurig, 2012), that ergonomics had something to do with quality.
Al-Darrab et al. (2013) argue that the new concept about organisational culture is that quality does not stand alone; it has to go along with safety, quality and health of workers which are provided in a safe and healthy workplace environment. This new concept provides new areas of study for quality. The new organisation is heading towards a philosophy of providing ecological features for its products and services (Eco Evaluator as cited in Al-Darrab et al., 2013). The consumption and disposal of these products do not cause too much harm to the environment. Consumers first ask information about these green products. Al-Darrab et al. (2013) further argue that these are features of the “integrated management systems” or IMS.
Lean Manufacturing and Job-Related Stress
In the early 1990s, manufacturers in the automobile industry began to widely adopt lean manufacturing as a way to reduce processes. However, research showed that lean manufacturing was associated with increased cumulative trauma disorders (CTD) (Brenner et al. as cited in Womack, 2007), and increased work stress due to an intensified workload (Parker Slaughter; Graham; Fucini & Fucini as cited in Womack, 2007).
The repetition of highly standardised work and part fitting problems and the acclaimed lean joint venture between Toyota and General Motors were related to WMSD injuries (Alder et al. as cited in Womack, 2007). However, some researchers argue that lean manufacturing can also have positive “energizing” effects on the worker and/or ergonomics, depending on how it is implemented (Liker; Genaidy & Karwoski; Zayko et al.; Adler & Borys: Alder & Cole as cited in Womack, 2007).
Lean management is for quality improvement and this is the aim of ergonomics. Ergonomics has the primary aim of reducing incidences of injury related with work environment to worker mismatches, and human performance improvement through enhancement of productivity and quality (Rethaber, 2010). Ergonomic risk factors are stressors that are characteristic of ergonomic-related injuries, such as repetition, force, awkward postures, contact stress, vibration (Phillips as cited in Rethaber, 2010).
The greater the number of repetitions performed, the greater the incidence of injury. Force refers to the amount of exertion necessary to perform a process or life, carry, push, or pull an item. The greater the amount of force exerted, the greater the incidence of injury (Chaffin & Andersson as cited in Rethaber, 2010). Awkward postures refer to the positioning of the body outside of a neutral posture. The more awkward the posture and the longer the posture is sustained, the greater the incidence of injury (Ross as cited in Rethaber, 2010).
Companies need a proactive approach for reducing ergonomic-related performance issues, rather than a reactive approach. A reactive approach will only help to reduce the performance issues attributed to the percentage of the indirect costs associated with WMSDs due to absenteeism, while the proactive approach will address the performance issues attributed to the indirect costs associated with WMSDs (Estes & Robson as cited in Rethaber, 2010).
Practical Application
Stanger (2002) describes how process improvement is performed in a workplace. Process improvement first begins with analysing all jobs to identify the precise physical requirements and then to create model workstations where job demands are simulated. Job applicants are required to work at the simulated jobs and their ability to perform work is objectively measured and then compared to the results from the existing workforce. Employees can then be matched to jobs for which they are physically best qualified.
Next intervention described by Stanger (2002) involves instituting a stretching program consisting of twenty-five warm–up exercises that are performed before starting work. These exercises are a way to lessen the physical demands of the work. It can be stated here that a professional athlete would not think of beginning strenuous athletic activities without a warm-up exercise. Exercises are designed to stretch the muscles used in the work and are performed before the start of the shift to help protect the body from injury (Stanger, 2002).
The next step is to train the workforce on ergonomic principles and involve them in participative ergonomics. The work group is taught basic biomechanical and ergonomic concepts, which help them identify safer and more effective ways to do their jobs.
A few volunteers from each work group help identify the jobs causing cumulative trauma injuries and they work with the process engineers to videotape the jobs. The volunteers then apply the ergonomic principles they have learned to improve work practices, postures, equipment, and product designs to protect themselves and their team members from injury. Where jobs cannot be changed significantly, job rotation is instituted (McGavin as cited in Stanger, 2002).
Another process improvement includes the utilization of an active work hardening program. Injured employees are brought back to work for a limited time but may perform only part of the job, sometimes as little as 15 minutes out of every hour. The time will be spent performing stretches and work hardening exercises and applying ice to the affected areas.
Oslay (as cited in Stanger, 2002) indicated that this process can be compared to the sports medicine approach used by injured athletes to regain strength and speed up the healing process. This reduces the time that the person must be off the job and strengthens the injured area lessening the possible re-occurrence of the original injury (McGavin as cited in Stanger, 2002).
Application of QUITE methodology at LDPE Plant
QUITE methodology involves determining work positions and difficulties of operators, including musculoskeletal risks and discomfort at upper extremities and back, and also visual difficulty. Ergonomics problems can affect operator performance and might result in operator error and injury. Most of all, the primary aim of this methodology is to improve product quality via enhanced worker performance. Ergonomics intervention is particularly emphasized in workers’ position in the work environment.
Researchers indicate that QUITE methodology can be inserted into existing quality systems, which is a concept emphasized earlier that ergonomics and quality have to go together and must be introduced in congruence with each other. Additionally, if there is an existing quality application, ergonomics can fill the gap and make quality improvement successful.
Training is vital. Ergonomics intervention should be planned gradually, with training given to supervisors and operators in selected lines. Training includes basic ergonomics principles and how to avoid awkward postures to prevent accident risk. Workers have to pinpoint areas where ergonomics problems occur.
Other ergonomics problems that pertain to noise, lighting, and safety measures have to be given equal preference. The objective of using proper ergonomics is to enable a person to perform his or her job in a natural, comfortable position. The body’s natural position is also known as a neutral position. While using instruments or manufacturing parts, the worker is at a safe distance and uses protective clothes and gloves.
This study focused on application of ergonomic applications in an LDPE plant IN Kemya. Interventions had to be applied because existing ergonomics caused injury. For instance, it became dangerous for the operator when he comes near the machine as there was no precautionary measure when he touches the machine. Injuries and muscle pains in the workers’ arms and spinal column reduced their performance, which triggered a number of shutdowns before 2012.
The company Al-Jubail Petrochemical Company and its manufacturing plant at Kemya have introduced and continuously modified ergonomics measures to reduce the incidents of accidents and injuries.
Before QUITE can be applied, Kemya needs to create the following environment:
- Participation and involvement from every member of the workforce, particularly those performing the job of LDPE console operator;
- Constant monitoring at the operational level, or checking of quality data and markers to ensure that ergonomic problems are addressed and solved, and continuous improvement strategy. Erdinc and Vayvay (2008) stressed that all the important points and data about quality should be well defined, addressed and reliable, e.g., number of shutdowns and high-quality production are indicated.
- In order to carry out ergonomics interventions effectively and to achieve quality improvement, application of QUITE methodology should be fostered with continuous improvement approach at both operational and management level.
Aside from the regular training and development, workers have to undergo continuous learning, particularly on occupational health and safety. The learning process should lead to knowledge in quality improvement in the workplace settings, especially in factors like improved physical postures, well-designed workstation, and the overall workplace environment. QUITE method aims for improvement of worker performance and quality products.
Employ management commitment
Management commitment is crucial to the implementation of ergonomics; this refers to top management, not just middle-level managers, because ergonomics intervention is a policy decision, and there cannot be a successful ergonomics intervention without a firm decision from the top; this is similar with what they call political will.
Therefore, the first step is to gain commitment of KEMYA president to support the quality improvement team after present to him User Alert idea in Kemya senior management meeting. It is this level of implementation that ergonomics can become successful. Management commitment to safety can help reduce quality and shutdown accidents in the workplace. According to Erdinc and Vayvay (2008), if QUITE application is led by management, commitment can be perceived in the different levels of the organization.
However, if this is started from the bottom, or from middle-level management, it would take some effort to convince management to commit to change. The use of case studies can convince management about QUITE application, even if managers are more familiar with quality application than ergonomics. In other words, managers should be given a brief orientation and training of the principles and benefits of ergonomics. Managers’ commitment to change should be seen by the workers through their physical involvement.
Determine scope
QUITE application can be inserted into an on-going quality improvement process. However, quality applications should first be specified before implementing QUITE methodology. This can be beneficial if it focused on a particular department of LDPE, task or process where ergonomics applications can be readily implemented and quality performance can be observed by the ergonomics team.
Quality performance should be associated with human performance on particular aspects of the operation so that ergonomics intervention could result in better quality. Potential areas of quality problems where there are poor employee performance and can cause low production rates can be the focus points for QUITE application.
- The first phase: List the repeated quality and shutdown problem causes by console operator mistake.
- The Second phase: Write precaution condition to avoid Quality and Shutdown event.
- The third phase: Export all active alert, response alert and the action has been done by every console.
- The fourth phase: Continuous improvement for the process
Plan participation
Participation of organization members is very important in the improvement process. Participation planning will have to involve organization members to help in the effective implementation of QUITE methodology. This needs the participation of managers, production and quality improvement personnel, occupational health and safety employees such as safety engineer (LDPE quality improvement team). In this phase, the names and responsibilities of group members should be properly specified. The organizational structure may have to be changed to demonstrate management commitment to QUITE methodology.
Table 1 Personnel who participated in ergonomics interventions
Establishing an ergonomics team is important for this phase. Ergonomics teams are usually composed of safety professionals, manufacturing engineers, maintenance, and most importantly, the people who actually do the work (Supervisor and Console) operation. The duties of the ergonomics team are: to review the company’s LDPE production records and identify the areas in the work environment where workers poorly perform leading to lower quality products; to look for statistical trends of accidents; to classify and evaluate different techniques a worker can use in performing a given job, particularly one of a highly repetitive nature; to predict mechanical stresses produced when a person performs a manual task; to determine how people learn to produce complex body movements; to predict time until fatigue in a manual task; and how changes can affect the type and degree of fatigue (Keller, as cited in Stanger, 2002).
Plan communication
In this step, important meetings will have to be held: one for the LDPE improvement team to discuss quality improvement, and another one for management to display the result of ergonomics intervention. The management and the team, to include the workers in the work setting, can discuss and conduct brainstorming techniques to identify potential ergonomics interventions.
Maintaining support and participation from all interested parties, along with effective communication are intrinsic parts of QUITE application. The principle behind this activity is to show that effective communication is a must to both ergonomics and quality improvement methods. To be successful in any field, players should be provided with an effective medium of communication. How communication is conducted by emails, in addition to a weekly meeting
Additionally, the reporting process is part of the communication system. Monthly reporting provided to KEMYA managers to gain their continued support (Done By LDPE Operation Manager), and to allow other workers the progress of the work, or the performance of the team. Every start and end of a particular step should be known by management.
Communication process for the vertical structure of an organization, communication is centralized and goes through the channel. But in ergonomics intervention system, communication can be horizontal and may not pass through the channel. This is demonstrated in the diagram below.
Communication protocol
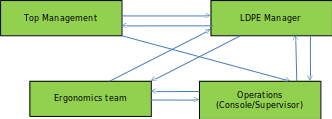
Assessment phase
Select tools/methods for assessment of ergonomics problems
The ergonomic team used several methods and tools in the assessment phase. The assessment method used in the research is the Strain Index (SI), which determines the force used in an assigned task. SI uses several variables like the force exerted, the time needed to use the force, hand and wrist position, the needed speed, and the time needed for the task (Moore & Garg, 2000 as cited in Drinkaus et al., 2005). Common risk factors were associated with repetitive tasks in the chemical manufacturing plant that caused musculoskeletal disorder (MSD). Using this method, the researcher conducted interviews on workers at Kemya.
There are six variables associated with the intensity of strain for each task, and these variables were collected through interviews and observation. The data were analysed, using the SI index and co-related with the literature. The six variables are the intensity of force used (refers to the force needed by the hand or wrist position), the time of effort or force needed (refers to the length of time to provide the effort), frequency of efforts for the time spent, wrist position, rapidity of the task (refers to the speed of the task required), and length of time for the daily tasks (Drinkaus et al., 2005).
Qualitative and quantitative methods were applied in the assessment process, i.e. we incorporated the results of the interviews with the data obtained from the Strain Index. Based on the qualitative interviews, the survey found that most repetitive tasks were the “hand grip,” wrists and fingers. The participants also indicated “monotony of work” as one of the psychosocial factors. We found that hand-grip, fingers and hands were high-risk factors that caused musculoskeletal disorder (MSD).
Strain Index (SI) can be attained by determining the six variables, and those with high-risk factors had also a high risk of morbidity, as obtained from the surveys conducted by Drinkaus et al. (2005). SI uses rating values, from 1 to 5, that determine the “intensity of exertion,” “time length of exertion,” “efforts used,” “hand-wrist position,” “speed,” and “length of time required for the whole day to accomplish the task” (Drinkaus et al., 2005, p. 143). This method provides reliable and effective recommendations that can be used in ergonomic interventions.
For example, in the surveys in the Kemya plant, we found through interviews and observation that most complaints were in the “hand-grip” areas of the workers. Workers exerted much effort, intensity, and length of time in working with the use of the hands and arms. The scores in the quantitative analysis, which can be incorporated in the qualitative data, will state whether such factor is high risk. A rating of 5 means it is “near maximal” and there is high morbidity, which further means that such task for the worker needs: reduction of time off work for the worker, more people or workers are needed to do the job, and more focus/attention is needed from the medical team and the ergonomics team.
In the analysis from the surveys and data taken from the workers, the following tasks needed ergonomic interventions:
The task of the console operator – this is performed by only 3 workers, working on shifts. The qualitative and quantitative data revealed that the task needs 5-6 workers, to work on 5 shifts in order to reduce the workload on the 3 workers. There should also be a reserve of an equal number of workers who come from the same department/section, since the workers permanently assigned to the task can take their leave anytime, and, also, with this solution, the duration or length of time exerted by workers during the day will be reduced. It has also to be noted here that the plant functions on a 24-7. Maintenance time should be extended to 2 weeks to a month.
Tasks of production employees working with low-density polyethene (LDPE) chemicals
There are about 50 workers working on 2 shifts. The plant has to double the number of workers to reduce the time of work and the workload. This will further reduce the number of shutdowns and turnover rates.
Awkward postures of workers
The method used in collecting data for awkward postures was indirect measurement, which is through questionnaires, an actual observation by the researcher, and video observation from CCTVs in the Kemya plant. Aside from interviews, observation is cost-effective in determining awkward postures in the chemical-processing plant.
Observation-based assessment can be obtained using the “paper-pen coding” method. This was used in the Kemya analysis. Through this method, the ergonomic team was able to observe the workers without disturbing them and what they were doing. According to researchers, this procedure lacks precision but the reliability of tools are usually varied (Dartt, 2010).
Assessing ergonomic problems
In this study, we used the “Posturegram,” a method invented by Priel (1974 as cited in Dartt, 2010), which emphasises the important position when a limb is used. In a form provided, the workers were asked to record the joints in their body when they were in a starting position with the use of reference points, for instance, x or y. This was effective when evaluating single postures instead of changing positions.
However, they did not use diagrams; instead, they compared their observations and the results of the interviews, and incorporated all these in the analyses for ergonomic interventions. In other words, they used a mix method of recording and observation. This way, the ergonomic team determined the static postures and dynamic ones, and also determined what effective ergonomic interventions were needed for the identified problems.
The ergonomic team also used computer-aided observational systems. As stated earlier, CCTV cameras were used in the plant, and the digital data were inputted in a software for analysis at a later time. Time-sampling can be used in the assessment process. This has several advantages. Using the video, the ergonomic team was able to observe positions in real-time, and all the other positions that included backward movement, slow movement, and any movement that was necessary for the assessment.
Assessing ergonomic problems can also be done using the process of “inter-method reliability”. The historical-based method is used in determining the hand-wrist position. The method evaluates the performance of LDPE instruments that determine yield data, especially on the same part or area (Dartt, 2010).
Assessment results
Assessment results should focus on issues that reduce workers’ performance like quality issue. There should be emphasis on the relationship between ergonomics problems and workers’ performance that could have led to quality performance. In the context of quality management, assessments should provide cause-and-effect diagrams and other similar tools like Pareto charts that can relate to ergonomics and quality (Axelsson, 2000 as cited in Erdinc & Vayvay, 2008). A review of this step can be considered if the relationship between ergonomics problems and workers’ performance is not determined.
The process of improving human performance began with identifying and resolving the environmental barriers to optimal performance (Wilmoth, Prigmore, & Bray, 2002 as cited in Rethaber, 2010). According to recent studies, the field of human performance technology is in a transition from focusing on training to focusing on performance (Guerra, 2003; Huglin, 2009; Jang, 2009 all cited in Rethaber, 2010).
The performance needs to be cognizant of the changes associated with an older workforce. As workers reach retirement age, more and more of these workers are opting to remain in the workforce. Organizations need to take measures to ensure that performance and productivity continue to improve (Bell, 2008 as cited in Rethaber, 2010).
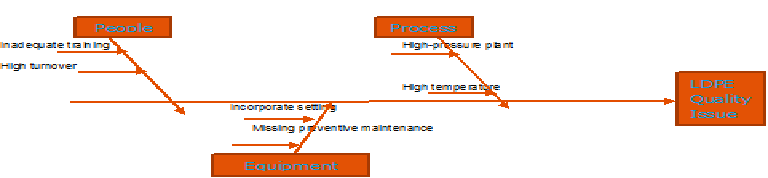
Adding cause and affect chart up to here
Select quality indicators
Quality indicators refer to higher product quality and higher organizational performance. Quality indicators will tell the ergonomics team whether quality performance through QUITE application was achieved. Selected indicators should correspond to the formed relationship between ergonomics problems, performance and pinpointed quality. There can be a number of indicators to be employed.
The Kemya User Alert has a term for ergonomics intervention. With this application, ergonomics reduced the number of shutdown, particularly in 2016, which led to an improved production of 325 kilotons of polyethylene and related products, from the previous 280 kilotons (ExxonMobil, 2016). The debottlenecking efforts were conducted in several phases, as a part of quality improvement. The plant applied ergonomics interventions, leading to enhanced production when shutdowns were reduced to the minimum.
Intervention phase
Plan ergonomics interventions
LDPE development team classify LDPE plant equipment is according to criticality of its process
First: Secondary Compressor
- Secondary: Primary Compressor
- Third: Extruder
- Fourth: Silos.
Initial intervention phase: Start with setup instructions and condition for principle process.
Training need to implemented intervention
Console operator how to use User Alert
- System engineer how to build the rule according to input from process and production engineers.
- Operator supervisor how to follow the operator performance during the shift if there is any pending alert
- Production and process engineers evaluate action was done by operator. Furthermore, study the response time from every console and the best way to improve console response
Interventions can be done through training, dissemination of information such as distributing manual regarding using User Alert in areas of continuous production (Erdinc & Vayvay, 2008).
The function of ergonomics is to minimize human operator stress and fatigue, and also promote work output and productivity (Phillips, 2000 as cited in Rethaber, 2010). This should be stressed from the start of interventions, the planning phase.
This should focus on elimination of ergonomics problems, and exemplify achievement of quality improvement at LDPE manufacturing plant. Work postures in the various tasks can reduce errors in the various tasks. Axelsson (2000 as cited in Erdinc & Vayvay, 2008) enhanced work postures using Rapid Upper Limb Assessment, and succeeded in improving work postures, increased use of resources, provided more relaxed product processes and comfortable operation atmosphere in a manufacturing plant. This reduced errors and rejected products for LDPE plant.
Interventions can bring innovations that are acceptable to workers in the plant. In order to do this, management should provide gradual interventions and not abrupt changes in the plant so that the workers would be able to adapt to the changes and be oriented to the new procedures.
Like any other project, pilot applications are necessary; in other words, it was ideal for LDPE plant to conduct pilot applications for intervention planning before implementing the wider scope of QUITE application for LDPE. This necessitated the involvement of top management and all possible workers in the plant as it provided easy implementation and acceptance of the of the change (Macleod, 1995 as cited in Erdinc & Vayvay, 2008).
Train people
Console operator
As mentioned, training is a major part of ergonomics. Training is also a form of participation. Like other fields of concentration, without training people are not equipped to go on with innovative projects and are not prepared to accept change. Successful implementation of ergonomics requires trained and well-prepared workers.
The console operator should be trained in IT and how to operate the console and User Alert system. Aside from this, training focuses on controlling “contact stress”. This is the result when an area of the body experiences a load, occasionally, repeatedly or continuously. In addition to being uncomfortable and in interference with work performance, contact stress tends to inhibit nerve function and blood flow and if not checked, can cause injury. This rule is there imposed when a person makes contact with an object.
On the other hand, pressure is a function of applied force over a contact surface area. Forces are vectors and are described by both magnitude and direction. Of special interest are normal and shear forces since these play an important role in human-product physical interface. Normal forces act perpendicular to the surface of a body while shear forces act tangential or along the surface. Normal forces, applied to a body results in pressure at the point and if these forces reach a certain magnitude, they can cause tissue breakdown in the affected body region.
Shear and frictional forces, occurring at the interface between the human body and a support device, can also cause tissue damage. When normal forces are present in addition to shear forces, a smaller amount of force is required to cause tissue breakdown. Research has shown that the amount of damage experienced by body tissues is dependent on not just the magnitude of the pressure, but also on its duration. In simple term, body disses can withstand higher loads for shorter periods of time (Nwaigwe, 2005).
The purposes of training are: to provide a common understanding about QUITE principles and application, and to give them the necessary knowledge of their work. Therefore, training should be able to explain the objectives and scope of QUITE methodology, assessment results and other important plans. Training aims to provide employees with a general understanding of ergonomics, and knowledge of the User Alert Training.
In the training phase, management should consider the educational background of employees, as some of them are not within college level and therefore do not have the necessary intelligence to absorb some learning lessons.
Employees have to be trained in physical ergonomics and design of the work environment. Ergonomics is a set of interrelated principles, which though look like simple and self-evident, refer to design of the work environment in relation to the product being created. These principles may refer to: limiting exposure to contact pressure, reducing distortion, reducing moisture in person-product interface, moderating heat build-up in person-product interface, limiting exposure to chemicals, reducing application of excessive force, moderating body motions, promoting postures of least stress, minimizing static load, providing clearance in the different sections of production area, and reducing exposure to vibration and impact forces.
After the training, a core group is formed composed of three ergonomists, an industrial hygienist, and a return to work specialist. This core group provides eight hours of training for cross functional groups at each facility. It also conducts comprehensive ergonomic surveys of the shop and leaves a trained team in place to follow-up with solution implementation and to handle subsequent ergonomic concerns.
Apply ergonomics interventions
Apply user alert
The User Alert is a computer software that informs operators of any trouble that needs immediate action. It is in the alert status, but not yet in the alarm position. Operators have to be well-versed with this system because it helps them in the conduct of ergonomics interventions, and in the operational aspects of work. The different steps in the operation are well defined in the system, and the operator is well informed and alerted of possible problems.
As mentioned, ergonomics intervention should emphasize a participatory approach, and must be provided with a pilot project before the whole application is introduced. Employees need time to adjust to change, even if it is ergonomic intervention. Constant intervention with employees and pilot applications would enhance interventions and attain employee acceptance.
Monitor changes
Monitoring the quality production and shutdown and alert event
The team must focus on ergonomics problems. Are the problems changed or altered as a result of the intervention? Addressing the ergonomics problems will take time, possibly weeks to months. In business, time is of the essence, the longer the interventions the higher the cost. Therefore, the team should set immediate, intermediate and long term goals. Again, interviews will have to be conducted to follow up employees’ perceptions of the effect of ergonomics intervention. This can draw primary data about changes in ergonomics problems. Reassessment should take place on the ergonomics problems, using the same tools and methods. Statistics will compare assessment results before and after interventions in order to provide data about significant changes..
Those who participated included the LDPE production manager, business planning engineer, machine sewing department supervisor and line supervisors. Effective communication was facilitated with weekly meetings and constant monitoring, along with frequent interviews on the employees. And report Monthly performance to KEMYA Senior Management
Assessment phase
They used the Quick Exposure Check (QEC) (David et al., 2005 as cited in Erdinc & Vayvay, 2008) as the assessment tool. The number of shutdowns and improvement of quality products, as mentioned earlier, had to be examined.
Intervention phase
The supervisors and operators underwent ergonomics training, which consisted of knowledge of the computer software, User Alert System, and improvement of the work environment. Employees were interviewed about ergonomics problems, and they were constantly reminded of a correct posture in the workplace. Others involved in the LDPE operation, such as the maintenance technicians, were asked to help operators. Ergonomics interventions were applied for three months. Changes were monitored, and significant improvement was noted.
Conclusions and future work
The study was a good example of effectiveness of QUITE methodology for manufacturing which highlighted quality problems and discomfort in LDPE operations. It can be concluded that ergonomics and quality are two interrelated factors that affect employee performance. Ergonomics improvement can trigger higher human performance. Furthermore, it will apply soon in another Kemya’s plant to solve the qulity issue they have it currently
Chapter 3: Methodology
Introduction
The methods used in this dissertation were case study and qualitative research using questionnaire, with email as a means of communicating with the participants. There are a number of advantages to this approach: (1) the appropriate number of respondents could be obtained and contacted quickly; (2) communications, from initial interaction follow-up can be accomplished through email; (3) electronic communication has been widely used and often favoured by research participants, as it makes the survey easily accessible from any computer with internet access; (4) it is less costly for the researcher to use, and the results are easily quantified or analysed using descriptive method. A disadvantage can be possible low participation by participants and an inability to track information on those who do not respond.
In understanding qualitative research, Creswell (1998) suggests that there are several compelling reasons for undertaking this method. The ability to describe “what” is occurring as opposed to “why” is inherent in qualitative research. Creswell suggests the use of qualitative inquiry focused on the interests and limitations of the researcher. Writing style, available resources and audience are considerations that often solidify the selection of this approach. Qualitative research is inductive by nature proceeding from an examination of the particulars found within the case moving to a broader, more generalized perspective (Creswell, 1998).
Kvale (cited in McIntosh, 2009) stressed on the propensity and extent of risk from the application of qualitative research. He gave the term “qualitative progressivity myth,” which refers to the “tyranny of intimacy” that underpins the apparent goodness and emancipatory intentions of the “warm, caring, and empowering dialogues,” also known as qualitative interviews. Reinharz (as cited in McIntosh, 2009) provided the metaphor of rape to describe the nature of the harm posed by interview research: “Interview research takes, hits, and runs.
It invades privacy, disrupts perceptions, utilises the pretences, manipulates the relationship, gives little or nothing in return, and once the researcher’s needs are satisfied, contact is broken off” (p. 80). Unstructured interviews typify sensitive research methods that aim to ascertain people’s in-depth experiences, and the interpretations, and meaning of such experiences. The impact on the participant may be different. This did not actually happen in the interviews because the Researcher used emails.
The questionnaire method is more comfortable for the participants: when they open their emails they answer the questions at a comfortable time. This Researcher decided that fifteen questions were enough and would not give burden to the participants who seemed to be busy all the time as they were concentrated on their work.
A case study approach was also relevant in this study because it required multiple sources of data in order to develop interpretations informed by the data (Yin, 2013). The most important sources of data came from the questionnaire and from the case study. This research used the Al-Jubail Petrochemical Company (Sabic, 2016) as a case study for the study of ergonomics interventions and quality application. The plant at Kemya and the 56 participants as sample were primary sources of data.
According to Yin (2013), a case study method must begin with a theory, which is a part of the hypothesis for this study. The hypothesis for this case study is: The injury and safety issues at Kemya’s LDPE plant are caused by inadequate ergonomics intervention; thus, the Kemya management has to continuously adopt ergonomics innovations to avoid musculoskeletal injury or cumulative trauma disorder (CTD), and conduct continual training and development (T&D) for the plant workers.
The activities should be part of the company’s quality management strategy. T&D is also a continuous activity for the company employees and management. The theory symbolises the summary statement of this study and all the other statements with corresponding methods and procedures, along with the instrument are based on this theory
The data collected in this study became easily available primarily because the participants believed that making space for dialogue and critical reflection of important issues is by necessity a collaborative act. They considered the sharing of information and knowledge, and understanding the value of differing knowledge and perspectives, as a key feature for creating a dialogue space. This Researcher and the participants understood the implicit need to collaborate to create clarity and meaning from ultiple perspectives.
Dissertations were included in this study because they are appropriate for a mixed-method of questionnaire and case study as they adhere to the standards of academic rigor required by this university.
Procedure
Sixty employees comprised of supervisors and workers who were working at the Al-Jubail Chemical Company were contacted through emails; their email addresses were given to this Researcher by an acquaintance who is currently employed in the plant. Of the 60 employees contacted, 56 responded positively, creating a response rate of 93%.
The participants were then informed about the nature of the research, that this was for purely academic purposes and that their identity would not be published or revealed to anybody. They were further informed that they had the right to deny the request and that the results of the survey would be incorporated in a database of which only this Researcher had access.
The questionnaire consisted of 15 interview questions pertaining to ergonomics and quality implementation at the Kemya manufacturing plant. Most of the questions were open-ended questions; these are questions needing explanatory sentences or paragraphs to draw most ideas and opinions of the participants regarding their work, particularly the ergonomics interventions and quality management at the plant.
The participants were cooperative in their responses to the questions as they provided straight and what can be considered as honest responses. They also provided suggestions on the ergonomics interventions and quality management at the plant.
Questions for the Participants
What are the issues related to quality products have you experienced at your plant?
- What quality management have you undertaken at the plant?
- What ergonomics intervention have you implemented to prevent injuries and provide quality production?
- Since when have you implemented ergonomics intervention?
- What particular part/aspect in the workplace do workers usually incur injuries?
- What ergonomics intervention did you apply?
- Were the injuries reduced after the interventions?
- How much has the company spent before and after intervention?
- What training programs have you conducted, if any, to implement ergonomics?
- Is training and development (T&D) fully implemented before the applicant is accepted? Please describe T&D methods.
- What rules/guidelines do you observe to prevent injuries?
- What other safety and physical working conditions do you suggest for the company to prevent injuries?
- In addition to ergonomics intervention, what other quality management strategies have you implemented at Kemya, if any?
- What are the outcomes of ergonomics intervention and quality management applied at the plant?
Excerpts of Participants’ Responses
Q-1 Issues related to quality products
- Reduced production, particularly with polyethylene and other chemicals, our main products
- Lower performance than expected of the employees, especially those in production side; as a result there was high turnover
- There were a number of shutdowns in 2011-2012 which heavily affected organizational performance and productivity
- Employee strength had to be reduced and it affected most of the plants of Kemya
Q-2 Quality management at the plant
- Quality management has been applied at the plant, the question is on ergonomics issues
- Before ergonomics intervention, quality was already implemented, particularly in the processing of polyethylene; in 2012, the plant produced high-quality low-density polyethylene.
- With quality improvement, Kemya can now produce 700,000 tonnes of ethylene annually, and has served the international market with its production of 1.1 million tonnes of polyethylene every year.
Q-3 Ergonomics intervention implemented at the plant
Ergonomics interventions include:
- Early detection of defective parts in order to reduce delays
- Workers can pinpoint and relay relevant information about the dangers and the areas that need improvement and change.
- If there are areas in manufacturing that fail, troubleshooting should include and provide possible explanation for the failure so that the incident will not occur again
- Correction of problems should be done through planning and implementation of mechanical or impromptu countermeasures.
- Problems and failures that are detected have to be planned and integrated into the system to become automatic safety controls, or as part of SOP; this way the problem will not occur again.
- Worker performance was noted which resulted in enhanced product quality and reduced turnover.
- Number of shutdowns was reduced, leading to increased production.
- The ergonomics applied were on the repetitive work. Work time was minimized leading to enhanced production, and reduced turnover in particular areas of production.
- Safety measures were implemented in some areas of the plant. We drew a line for workers and non-workers to be safe.
Q-4 Areas in the plant where ergonomics intervention was needed
Processing of chemicals and packing into finished product needs safety in handling; processing cost millions of dollars for the company, and so we applied automation aided by human labor.
We reduced the working time for the injured which only needed rest. They were absent from work for a day or two and came back to work the following day.
The injured workers received their regular pay and added rest.
Q-5 Reduced injuries after intervention
- Most of the injuries and accidents occur near the machines and the reactor. We have addressed this issue by providing “demarcation” line between the worker and the machine. Workers were special suits and gloves to prevent injury.
- Workers on duty at the machines are working on different shifts to prevent accidents.
- We have restricted personnel entering the “danger zone,” i.e. even employees of Kemya are prohibited to enter if they are not assigned to those areas.
Q-8 Training and development programs for new applicant employees
- Old and new employees, even those who have been with us for decades have to undergo regular training in operational matters and the workings of the plant. Employees are taught about organizational knowledge and are training in running the plant.
- New employees are oriented on their tasks and old ones also receive regular T&D.
- T&D encompasses the various functions of the different departments of the plant. First, new employees receive 1-2 months orientation. After this, they are immersed into the different tasks in the plant. Orientation is a long process of being well-knowledgeable of the plant’s operations. All new and old employees are required to undergo regular T&D so that ergonomics intervention and quality application are always fresh in their mind. Employees are always oriented of new applications and they also have to constantly read memos and information materials about processes in the plant.
Q-9 Guidelines to prevent injuries in the workplace
Management should be committed for change and for the success of the ergonomic intervention, not just implementing change for the sake of doing it.
Intervention involves the utilization of on-site therapy. This involves training the employees in basic anatomy and they can recognize the early indicators of cumulative trauma injuries. Workers are instructed to report muscle aches, stiffness, and soreness to the in-house therapist. If a problem is pinpointed, the therapist applies sports medicine techniques such as icing and micro-stimulation, which is a light electrical current that increases blood flow and speeds healing.
Q-10 Other quality management strategies
- Al-Jubail Petrochemical Company has an organisational culture that is based on safety, quality and health for employees and workers. Top management is committed for this quality management strategy.
- Since our plant is a chemical plant, we always ensure safety and health for our workers. Without this, the company could have spent a lot of money for hospitalization of workmen’s compensation.
- The company has attained lesser turnover because of quality management which has led to employees’ quality performance.
- Ergonomics principles coupled with quality management are ingrained in the company’s philosophy.
- The company has a culture of eco-friendliness and products and services are provided with less emphasis on profits, which is the last thing about the company’s activities.
Critical Analysis
KEMYA’s safety measures are provided in the program called SHER, which stands for “safety, security, health, and environmental incident rate” (Sabic, 2016). Training and development is a significant part of continual ergonomics intervention. An organisation cannot have an effective program of providing safety and preventing accidents and injuries without proper training for the workers in the field and in manufacturing.
Ergonomics intervention involved the de-bottlenecking of the LDPE plant to improve production. As mentioned in the literature, ergonomics intervention resulted in increased production, reduced number of shutdowns and turnover, and improved quality products. Debottlenecking means focusing on workers’ stress, possible causes of absenteeism, and pinpointing defects in the work area: employees’ tasks have to match with their strength. The time they are working should not be long enough that can make them overworked.
Ergonomics aim for quality, and that is why they are synonymous. Managers and employees who are trained in ergonomics realize that the overall concept of ergonomics is to match machine with human: the outcome can be comfort for both human and machine (comfort for a machine means it is not overworked like humans; if machines are not well-positioned, there might be increased shutdowns), enhanced performance for both man and machine, quality product, which may ultimately result in good organizational performance or higher and positive output.
These facts and factors were the gist of the surveys we conducted on the participants or employees involved in actual production of polyethylene and other chemicals for LDPE plant at Kemya. First, there had been ergonomics interventions and quality applications at the plant. But there remained problems. QUITE methodology and more quality applications were introduced.
All these factors must be studied, conceptualized and planned during ergonomics intervention. Perhaps, at the height of ergonomics problems management should consider stopping production in order to spot all possible errors and causes of malfunctioning. The job of the medical team is also a factor, since they have to deal with the cause of musculoskeletal disorders, how to deal with it, and what are their recommendations.
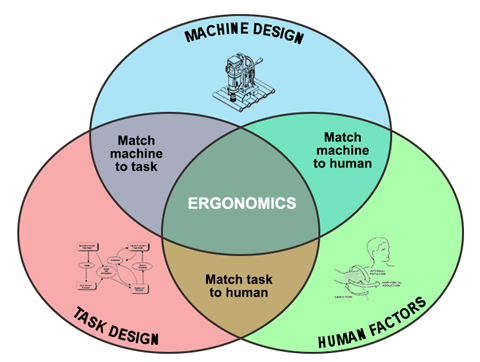
The subsequent activities or ergonomic interventions resulted in enhanced production and reduced leakages in the reactor. At first, quality applications were not enough, but due to ergonomics intervention, the problems were properly addressed. Quality issues and human resource development problems were also addressed.
A number of participants also indicated that the sources of injury and risk factors were repetition, awkward postures, and vibration. They had voiced out these factors and ergonomic issues were implemented. Most of the factors were about repetitions, the force exerted, and awkward posture. Kemya management was able to address the ergonomics issues by conducting continuous interventions.
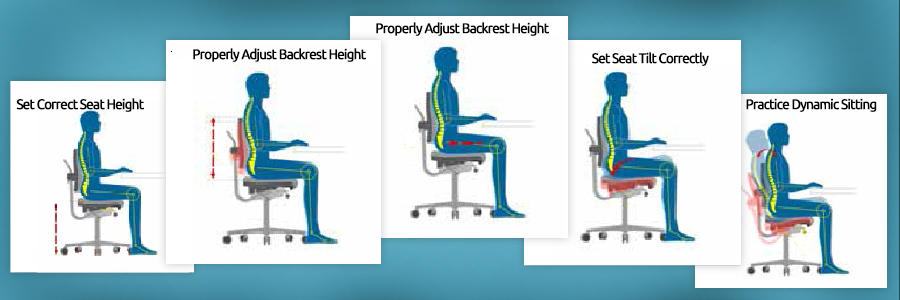
Working in the office and working with machines are two different things, but the conception of correct ergonomics to avoid injury is almost the same. Safety and health are also synonymous.
Chapter 4: Conclusion/Recommendations
Literature has provided studies on ergonomics interventions that parallel quality. Researchers recommend that these studies should focus not only on technical problems but also organizational aspects regarding systematic unification of ergonomics and quality in manufacturing (Axelsson, 2000 as cited in Erdinc &Vayvay, 2008). For example, Kemya is a labor-intensive plant, combining manpower and machines. An important aspect of ergonomics intervention is to match machine and human.
Ergonomics is significant to Kemya and the company because of the opportunities it provides to improving human performance at the work environment. As much as eighty to ninety percent of performance improvement opportunities are found in the environment (Cox, Frank, & Philibert as cited in Rethaber, 2010).
Ergonomics is also important to Kemya professionals and workers due to the direct and indirect costs of ergonomic-related performance issues in Saudi Arabia. Direct costs of ergonomics have been estimated to cost billions of dollars, given the number of international firms operating in Saudi Arabia. Reduced performance due to ergonomics problems can also run to billions of dollars.
It can be concluded here that the employees, who were trained in ergonomics interventions, became aware of the problems and helped in providing ergonomics interventions. Their responses to the questions are significant to the adequate implementation of ergonomics, which explains that the company has spent quite a little amount for costs of injuries for the workers at Kemya. This also explains the fact that the company has spent a large amount when it came to ergonomics interventions and quality implementation: the company has provided quality product, which positively affected the workers’ performance.
This does not mean that Kemya did not experience the negative ergonomics. The participants in the qualitative study revealed that the starting years of the manufacturing plant and the company Al-Jubail Petrochemical Company was a challenging time. The company had to continuously apply ergonomics interventions and quality management due to workplace injuries, reduced productivity, and lower quality products.
Managers and workers needed regular training and development, particularly in ergonomics intervention and quality implementation in the LDPE plant. An ergonomics task force (or team) was essential in the manufacturing plant. When introducing ergonomics within the manufacturing setting, this task force was the key to an effective quality enhancement. The team was composed of plant-level workers and management representatives. This strategy presented some challenges in aspects of information presentation, scheduling meetings, assigning responsibilities and getting new ideas.
Once a company decided to establish an ergonomics task force or team, the primary first step was to gain management support and relay it to all personnel. The company president or plant manager issued a memorandum articulating direct support of the move, along with the hope that everyone should cooperate in the group’s activities.
An ergonomics team may be comprised of line workers, safety and health professionals, a purchasing representative, an engineer, a maintenance worker, laboratory employees, office personal and representatives from other groups. Members were recruited by contacting department managers and requesting volunteers. Health workers like the nurse and safety department were also included.
Preventive measures should include “stretching” to reduce the risk of injury. Twice a day a tone can be sounded over the speaker system in the plant, reminding workers to stop working for a few minutes and stretch. Jepsen and Thomson (as cited in Rethaber, 2010) studied the impact of stretching to prevent MSD on the upper arm. The exercise focused on the different parts of the right arm. The researchers concluded that there was an improvement in the baseline neurological data and that stretching gave comfort to the participants. Nevertheless, they also concluded that stretching was not the only means to prevent injury.
In conclusion, ergonomics interventions were successful at the Kemya manufacturing plant due to the cooperative endeavours of the different departments and personnel in the company; this means participation of all employees to include top management. Ergonomics intervention is a continual activity for firms aiming for quality performance.
References
Ace Brokers: Saudi Arabia. (2016).
Al-Darrab, I., Gulzar, W., & Ali, K. (2013). Status of implementation of safety, quality and environmental management systems in Saudi Arabian industries. Total Quality Management, 24(3), 336-354.
Almgren, J., & Schaurig, C. (2012). The influence of production ergonomics on product quality: A research project conducted at a paced assembly line (Master of Science thesis, Chalmers University of Technology, Gothenburg, Sweden).
Creswell, J. (1998). Qualitative inquiry and research design: Choosing among five traditions. Thousand Oaks, CA: Sage Publications, Inc.
Dartt, A. (2010). Ergonomic exposure assessment: A study of rater reliability, method reliability, and sampling strategy (Doctoral thesis, Colorado State University).
Erdinc, O., & Vayvay, O. (2008). Ergonomics interventions improve quality in manufacturing: A case study. Industrial Journal in Industrial and Systems Engineering, 3(6), 727-745. doi: 10.1504/IJISE.2008.020683
ExxonMobil: Al-Jubail Petrochemical Company (KEMYA). (2016).
Greer, B. (2001). Total quality management and managing diversity: A comparative study of Malcolm Baldrige and AACSB business school examiners (Doctoral thesis, Kent State University Graduate School of Management).
Gupta, M., & Boyd, L. (2008). Theory of constraints: a theory for operations management. International Journal of Operations & Production Management, 28(10), 991-1012.
Henry, J. (2004). A study of psychosocial work factors and ergonomic risk factors and how they affect worker stress and musculoskeletal discomfort in assembly workers with a manufacturing environment (Doctoral thesis, Clemson University, South Carolina).
Kelby, J. (2014). Nuts and bolts of effective ergonomics programs. Professional Safety, 59(8), 53-54.
Latif, H. (2016). Saudi Arabia: 85% workplace injuries in construction, trade & industry sectors.
McIntosh, M. (2009). Participants’ perspectives of risk inherent in unstructured qualitative interviews (Doctoral thesis, University of Alberta).
Nwaigwe, A. (2005). Ergonomics considerations in IT-enabled computer-aided design for discrete manufactured products (Doctoral thesis, University of Pittsburgh).
Piatt, B. (2012). An action oriented research study of an ergonomics training program in a U.S. semiconductor manufacturing plant (Doctoral thesis, Fielding Graduate University).
Popa, M. (2011). Methods and Techniques of Quality Management for ICT Audit Processes. Journal of Mobile, Embedded and Distributed Systems, 3(3), 100-108.
Rethaber, J. (2010). Exploring the ergonomic competencies and proficiencies of human performance improvement professionals: A mixed methods exploratory study (Doctoral dissertation, Capella University).
Sabic: Facts and figures. (2016).
Stanger, L. (2002). The prevention of injuries in manufacturing utilizing ergonomic interventions (Doctoral thesis, Loyola University, Chicago, Illinois).
United States Department of Labor: Prevention of musculoskeletal disorders in the workplace. (2016).
White, C. (2015). Proactive ergonomics: Stopping injuries before they occur. Professional Safety, 60(6), 69-73.
Womack, S. (2007). A multi-methodological study of the effects of lean manufacturing practices of work-related musculoskeletal disorder risk factors and other injuries (Doctoral thesis, The University of Michigan).
Yin, R. (2013). Case study research: Design and methods. Newbury Park, CA: Sage Publications.