Executive Summary
This report introduces the process of a company quality system implementation. The issue is addressed from the perspective of an aspiring leader who is yet to acquire the respect and confidence of their followers. A good quality system acknowledges the complexity of the business landscape that comprises both the company and the stakeholder perspectives. When implemented with due diligence, a company quality system within the ISO 9001 framework helps the organization attain the required level of performance and generate better returns, while leaving both customers and employees satisfied. The implementation process is presented as a series of basic steps from designing the model to perfecting it. However, in this particular scenario, this plan needs to be complemented by Kotter’s model of change. By building the links between the two processes, a leader is provided with an optimal framework that will not only generate initial returns but also help them sustain the growth.
Background
Aspiring leaders face a series of challenges that originate from several spheres of their professional expertise. First of all, there is a strong need for gaining positive results in the new position, inspiring the team and reassuring the company’s executives. At the same time, long-term, strategic objectives may be difficult to attain shortly, which is why a considerate plan needs to be included to make gradual progress. Second, new leaders may see doubts and even resistance from their followers who are not yet convinced of the feasibility of the new appointment. This is particularly relevant for the people who are promoted to their first management positions and take command of the team of which they have been a part. These factors compose the primary set of challenges that is in the focus of the present report. In total, the key goal is to ensure that the team functions in the spirit of unity and rapport toward its operational and strategic objectives. For such a global task, a comprehensive system of quality management is required. This report proposed ISO 9001 as a leading quality management system for the team.
Introduction
Today, the business environment has become increasingly complex with an array of challenges affecting enterprises on both operational and strategic levels. In this regard, companies benefit from comprehensive formalized systems of documenting their internal and external processes and responsibilities. The point of these procedures is to attain the required levels of performance and efficiency that align with the company’s goals. Quality management systems coordinate the efforts made by diverse expert teams in terms of customer relations, professional operations, and growth objectives. This way, the entire operational unit can sustain its growth through perpetual improvement and planning. This is particularly important for aspiring leaders who need to consolidate their resources and give the new team the impetus that is required for further development. Through an advanced company quality system, they can rely on a well-established framework capable of channeling the resources in the right direction. At the same time, the very implementation of such a paradigm may be challenging unless a fitting change model is applied to consolidate the team.
Investigation
A modern quality management system is expected to comply with several key principles and criteria. It is expected to be in line with the requirements posed by the complex operational environment of the organization, as conditioned by the overall industry landscape. According to ASQ (n.d.), an optimal quality management system exists at the intersection of two key spheres of organizational functioning. From one perspective, it focuses on the needs of the customers, creating a positive image in the eyes of the target audience. This effect is attained through the quality of the products or services and their value, but it also depends on more sophisticated matters, such as corporate social responsibility. On the other hand, a full-fledged quality management system will also address the needs of the organization. Each company has to adhere to a specific set of regulations that exist to control the operations within a given industry. Furthermore, it is equally important to ensure that all employees can work in comfortable conditions that help them reach their full potential. When executed correctly, this system helps all components synergize to generate better returns for all parties.
Overview of the System
In light of the needs and requirements formulated prior, a quality management system standard known as ISO 9001 is proposed as an effective framework of reference. As ASQ (n.d.) informs, it is currently the dominant quality management system in the world, which is followed by the majority of prosperous organizations. In fact, the value of ISO 9001 is that it does not provide a ready-for-use, step-by-step plan of quality assurance. Instead, it represents a certain basis upon which the management can build a fitting framework for their particular organization. ISO 9001 introduces a structure of principles that is shown in Figure 1. Each of the elements represents a key area of expertise that needs to be included in the operational planning of the team.
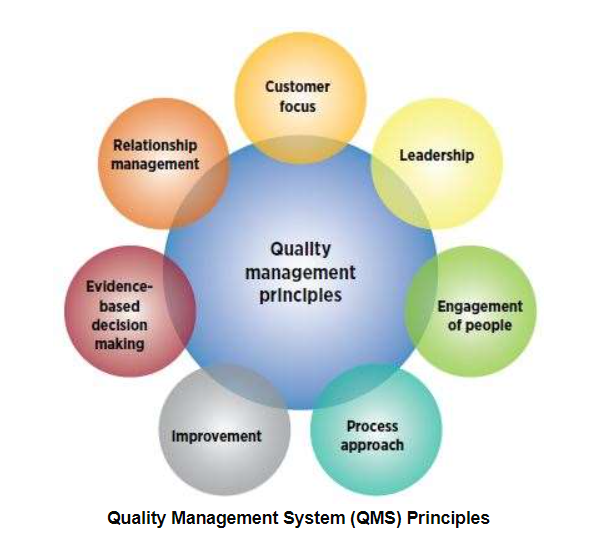
Key Principles
The principles of a quality management system inform the directions, in which the team will need to channel its efforts. Evidently, the exact nature of these efforts is to vary, depending on the exact position of the company or a specific unit. Importantly, a considerable emphasis is laid on the person-centered component of the overall framework. A quality management system acknowledges that people are engaged in the operational activity from all sides. There is a focus on the customer needs, as their satisfaction is the primary determinant of the organization’s performance.
However, the company side is also represented by people with their own expectations, interests, and needs. The key idea of a quality product is to find the right balance between all sides instead of disregarding one of them for the sake of the other. The “engagement of people” principle is expected to play a role of paramount importance in the introduction of the system. People are the key link between the non-human elements, as they power the product, produce value, and ensure the lasting impression of it. Thus, without the engagement on all parts, quality in its current understanding will not be attained.
Implementation of the System
The system’s implementation is expected to be challenging for an aspiring leader who may experience a lack of confidence on behalf of the team. Figure 2 shows the basic implementation process proposed by ASQ (n.d.). It provides guidelines for the key steps that being with formulating the company quality system to be introduced. The design is to have the ISO 9001 system at its core, and each principle will inform the specific policies depending on the company’s operational environment. However, this scheme cannot be used in isolation, as it does not address the necessity of engaging the people who drive the change.
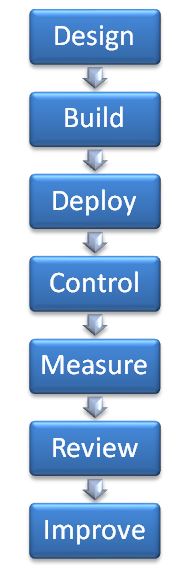
Therefore, Kotter’s change model is to be used simultaneously with the general implementation plan (Table 1). With the generally hesitant team, it is especially important to create a sense of urgency that is genuinely shared by the team (Kotter Inc., n.d.). This can be done through identifying an action group of the most loyal followers who will be more likely to become the role models to inspire the most hesitant members of the team. Through the volunteer army’s contribution, the design of the quality model will take its final form in light of all perspectives. The participation of this group will be needed from step one (design) until the pilot system is deployed. Next, upon experiencing the first positive outcomes of the initiatives, the level of support will grow, inspiring other members of the team. This will be the short-term win generation, formulated in Kotter’s framework. Upon this foundation, the progress will be sustained, bringing the team closer to institutionalizing the change. In this particular case, this outcome will consist of fully implementing the quality management system.
Table 1. Company Policy System Implementation Plan
Recommendations
Overall, the situation requires a stronger emphasis on the engagement of people in the process of implementing the company quality system. Furthermore, it is related not only to the customers or stakeholders of the organization but also to the team itself. For an aspiring leader, the doubts of their followers may become a serious barrier on the path of change. Thus, it is imperative to eliminate the concerns by proving that the chosen policy is optimal. For this purpose, Kotter’s change model appears to be a viable choice. It will be implemented along with the general implementation plan for the quality management system. More specifically, it can be presented as a timeline with two parallel, yet interrelated processes that will eventually lead to the ultimately positive outcome.
References
ASQ. (n.d.). What is a quality management system (QMS)? Web.
Kotter Inc. (n.d.). The 8-step process for leading change. Web.