Introduction
Liquefied Petroleum Gas (LPG) is a mixture of hydrocarbon gases, a large fraction of which is propane and butane (Khabibullin et al. 2010, p.1). The composition of LPG at any particular time varies according to its source, processing principles and season (Khabibullin et al. 2010, p.3). For example, the quantity of butane and butane vary during winter and summer. Gaseous LPG can be condensed to liquid at normal temperature by application of moderate pressure and lowering the temperature (Khabibullin et al. 2010, p.3). This property makes LPG easy to transport.
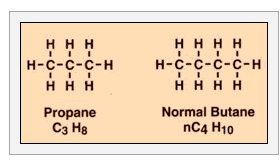
LPG in United Kingdom
United Kingdom is one of the biggest LPG producers in Europe. UK’s annual production is estimated at more than 5 million tonnes (26th World LP gas Forum & 2013 AEGPL Congress 2012). According to 2011 LPG consumption data, the major uses of LPG in UK are Industrial and Commercial (54%), domestic (27%), agriculture (10%) and automotive (9%) (26th World LP gas Forum & 2013 AEGPL Congress 2012). The nation’s major LPG distributors are Calor (SHV), Flogas, AvantiGas and BP.
Properties of LPG
This section discusses some of the important properties of LPG.
Vapour pressure
Vapour pressure is one of the most important properties of LPG as it affects handling and design of storage systems. Vapour Pressure is the pressure at which a liquid and its vapour are in equilibrium at any given temperature (Shipman 2005, p.6). LPG is gaseous at normal atmospheric pressure and temperature but is easily liquefied by moderate pressure and low temperature. This liquefaction enables easy transportation in pressurized tanks (Product description).
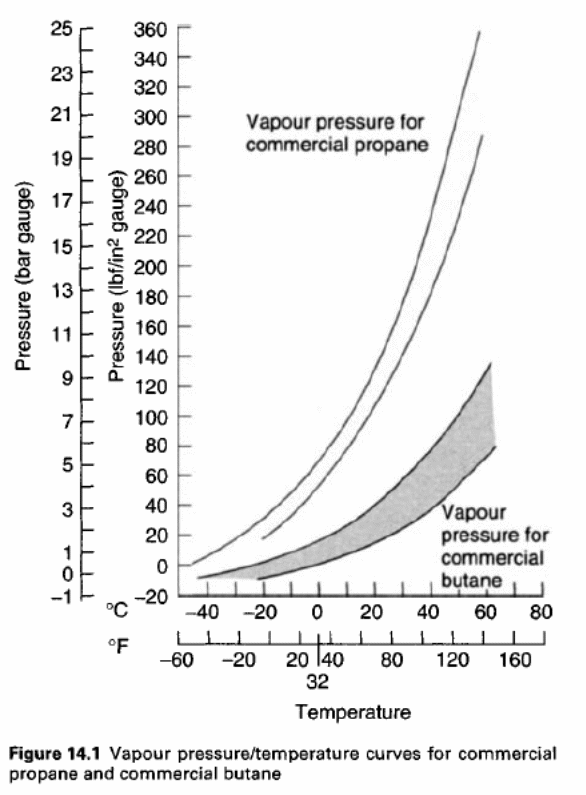
Combustion
Complete combustion in sufficient oxygen yields low volumes of carbon dioxide and water. This has made LPG be considered “clean” and potentially less damaging to the climate (Shipman 2005, p. 5; Product description). However, dangerous carbon monoxide can be produced in limited oxygen.
C3H8 + 5O2→ 3CO2 + 4H2O
2C4H10 + 13O2→ 8CO2 + 10H2O
Odour and colour
LPG is an odourless and colourless gas but an odorant such as ethanediol is normally added to it during production for safety purposes.
Calorific value
LPG has a higher calorific value (94 MJ/m3 or 26.1 Kwh) than natural gas (38 MJ/m3 or 12.6 Kwh).
Boiling point
At normal atmospheric pressure and temperature the boiling point of LPG ranges from -46oC to -2oC depending on the quantity of propane and butane (LPG properties).
Ignition temperature
The ignition temperature of LPG is around 500oC.
Toxicity
Neither butane nor propane has known toxicity.
Flammability
Flammability is the percentage of volume of a gas in a gas-air mixture needed to form a combustible mixture (Shipman 2005, p. 8). The flammability of LPG is that of its constituents, butane (upper 9.0, lower 1.8) and propane (upper 10.0 lower 9.0). These limits are much narrower than those of other fuels making LPG a much safer gas (Shipman 2005, p. 4).
Production of LPG
LPG can be produced in two main ways:
- From crude oil at petroleum refineries where LPG is a byproduct of gasoline and heating oil products (Environment Agency-UK 2005, p. 37).
- From natural gas at processing plants.
LPG is obtained during processing of natural gas.
Production from petroleum refineries
The feedstock for LPG at refineries is obtained from crude distillation and fractionating operations. LPG separation and recovery is achieved by cold-distillation under pressure using cryogenic cooling systems.
Process description
Pre-drying
Pressurized feedstock are pre-dried and passed through molecular sieve dryers. They are later regenerated using hot fuel gases.
Cooling and chilling
The regenerated feed stream is cooled and chilled. The residual vapor is then channeled to a refrigerated absorber where it is passed through gasoline adsorbents.
Fractionating phases
The liquid stream is passed through first and second fractionators to produce C3/C4 hydrocarbon, overhead streams and incomplete gasoline extracts. The C3/C4 overhead stream is passed through a third fractionator in order to split it into propane (C3) and butane (C4).
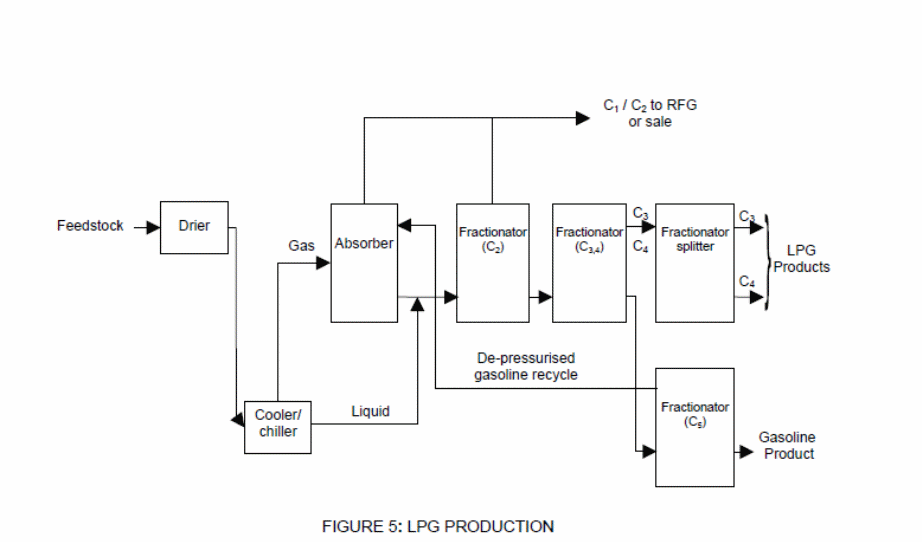
Production from natural gas
Natural gas is mined from deep oil wells and sent up mixed with crude oil. Initial stages of production are meant to separate natural gas from crude oil and improve its quality.
Process description
Gas-oil separation
Natural gas is separated from crude oil. This is achieved through natural gravity separation where lighter hydrocarbons float atop heavy oil or via multi-step gas-oil separation processes (Khabibullin et al. 2010, p.7).
Removal of condensates
Condensates are removed from the gas stream at the well head using mechanical separators (Khabibullin et al. 2010, p.7).
Dehydration
Water is removed from the gas stream to prevent the formation of hydrates.This is done using either ethylene glycol system or by adsorption using silica gel or activated alumina (Khabibullin et al. 2010, p.7).
Contaminants removal
Amines absorption and desulphurization and gravity are used to remove contaminants like Hydrogen Sulphide, carbon dioxide, water vapor, helium and oxygen.
Methane separation
Methane is separated from natural gas liquids using cryogenic processing and absorption methods.
Fractionation
All the above processing end with a bottom product that is fed to an LPG fractionating plant where it is separated into propane, butane and natural gas liquids.
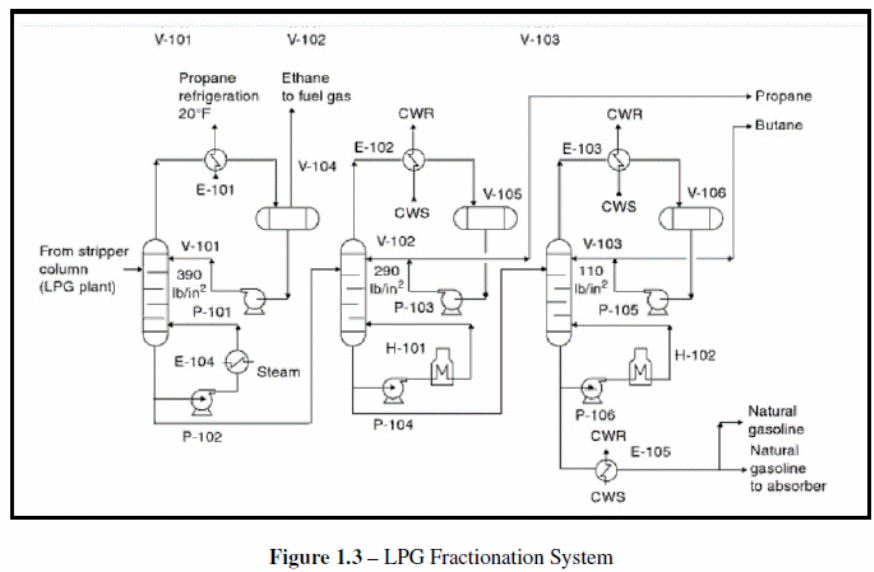
To improve quality, propane and butane from the fractionating system are passed through absorbent molecular sieves to remove sulphur compounds and water vapor. Following this treatment, the two gases are ready for storage and shipment.
Storage of LPG
The capacity of storage vessels for LPG range from thousands of tonnes for industrial users and refineries to a few hundred litres for domestic heating and cooking (Shipman 2005, p. 6). The following section examines small-scale and bulk storage of LPG.
Cylinder storage
Refillable cylinders are available for either commercial propane or butane. The cylinders vary in capacity from small-capacity ones of 11 liters to larger ones with capacity of over 100 liters. Apart from refillable cylinders, non-refillable cylinders have also been developed to cater for leisure and mobile users. Butane is normally stored in a blue cylinder weighing up to 15Kg (LPG supply chain). Commercial propane is commonly stored in red cylinders or bulk storage tanks when required for intensive heating and cooking (Product description). Commercial LPG in bulk tanks is stored under pressure of 7 to 10 bars. However, to be used in gas appliances, pressure gauge is used to lower it to a safe level of 37 mbar (Propane) and 28 mbar (butane) (Shipman 2005, p. 8; LPG Good safety practices in cylinder filling and handling).
Bulk storage
Bulk LPG is stored in one of the following ways depending on scale, location, environmental needs and the method of operation of a storage facility (WLPGA 2012)
Salt domes and tunnel caverns
These are usually constructed deep underground and are suited for very large scale pressure storage. They require suitable geographical and geological conditions. Many countries are shifting to underground storage due to low safety and maintenance costs (WLPGA 2012).
Cylindrical/spherical steel tank above ground storage
LPG storage tank installed above ground are required to be supported with a strong concrete base (LPG Good safety practices in cylinder filling and handling).
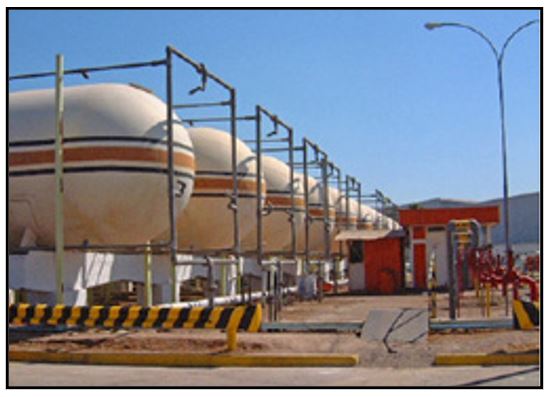
The size of the base is determined by the capacity of the tanks.
LPG tank capacity and concrete base dimensions (Comhairle nan Eilean Siar 2011)
During the installation of the tank the following must be observed:
- The tank must be placed at least 1.5 metres from any physical barrier to prevent mechanical damage to the tank and equipment
- The location should be provide easy access to a refilling tanker
- The concrete must meet the minimum standard thickness of 150mm
- A suitable fire extinguisher meeting the LPGA-UK code of practice must be placed near the tank.
LPG bulk tanks with capacity greater than 1200 have specific separation distances as shown below.
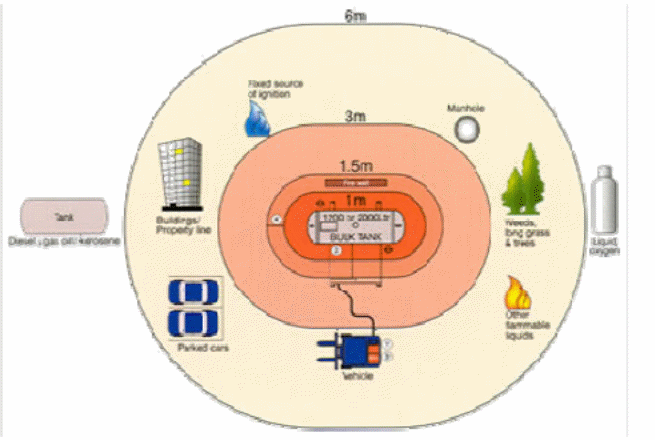
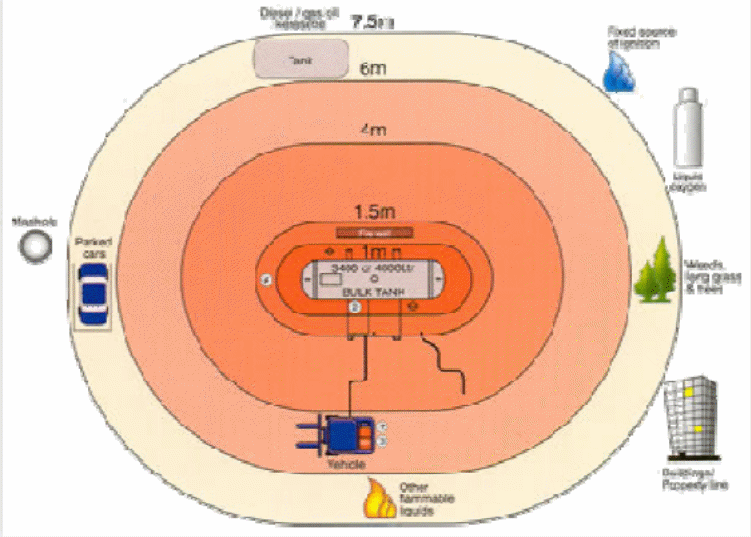
LPG bulk underground storage
In some countries, underground storage is the only permitted option for bulk to intermediate scale storage (WLPGA 2012). According to the World LPG Association (WLPGA) (2012), advancements in corrosion prevention technology and passive safety are making underground storage more attractive.
In the UK the following safety measures must be observed during any underground storage installation (Comhairle nan Eilean Siar 2011).
- Appropriate separation distance from physical objects as specified in Code of Practise for LPG.
- Before installation, a site survey must be carried out by a qualified and competent engineer
- The excavated underground area must be free of any electrical cable.
- The laying of the underground tank must not undermine foundations of nearby buildings
- The installation area must not be prone to flooding.
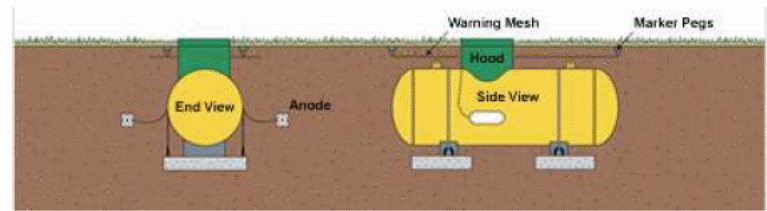
LPG Cylinder Filling Plant
A typical UK filling station is equipped with instruments for bulk storage, fluid pumping, filling, weighing, and leak detection.
Bulk storage
The size of storage is dependent on cylinder throughput and LPG delivery (Metcalfe 2006, p. 18).
Fluid pumping
Owing to the handling of LPG at boiling point, LPG pumping systems are designed to ensure there is minimum drop in pressure between the storage unit and the pump (Metcalfe 2006, p.18). The three common types of pumps today are the centrifugal /channel type, positive displacement gear and the vane type. A high filling rate is achieved by use of high differential head pump to overcome the high resistance to fluid flow occasioned by small valves on the cylinder.
Filling and weighing
Accuracy and exactness of filled weight is important in cylinder filling. Machines for filling and weighing should give greater control of filling weights (Metcalfe 2006, p.18).
Latest filling and weighing machines are electronic and their working is based on load cells. They are capable of achieving high accuracy and have advanced data collection and read out capabilities (Metcalfe 2006, p.18).
Handling and safety systems
In the UK motorized conveyors are used for handling full cylinders while manual handling is appropriate for empty ones (Metcalfe 2006, p.18).
For plants with high volume throughput carousels are used although they are not very popular in UK (Metcalfe 2006, p.18).
In regard to safety, safety systems usually incorporated shut off valves at the incoming liquid line to the filling point (Metcalfe 2006, p.18).
For fire safety, water drench systems are required to be installed above the filling machines. The filling point should also be thoroughly ventilated.
Leak detection
Leaks from filled cylinder can be detected by smell , use of soap water spray or sophisticated methods such as motorized conveyors equipped with water bath (Metcalfe 2006, p.18). Visual examination can also be employed to detect damaged cylinders (Metcalfe 2006, p.18).
Transportation
Although used as a gas, LPG is stored and transported as a liquid under pressure (Liquefied Petroleum gases).The choice of transportation medium depends on volume, medium of storage, nature of transport infrastructure and national regulations (WLPGA 2012; LPG supply chain).
Bulk transportation
Bulk transportation is normally from the original source (e.g. natural gas well or refinery) to major customers, bulk plants and cylinder filling plants. Bulk transportation can be by pipeline, rail or road (WLPGA 2012).
Non-bulk transportation
In this case LPG is transported in cylinders from bulk plants or cylinder filling stations to small scale users. This is usually done by road.
Storage of LPG during transportation
Trucks transporting LPG are uniquely designed to enhance safety and must be inspected during every trip. The truck storage may be a simple containerized tank or enhanced with LP gas transfer equipment (WLPGA 2012)
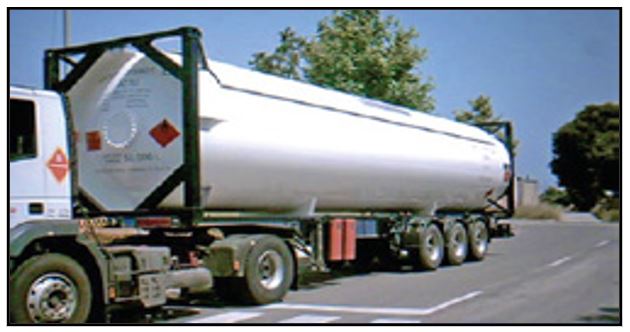
Transportation regulations
In UK, The Road Traffic (Carriage of Dangerous Substances in Package, etc) Regulation 1986 is one of the laws governing the transportation of LPG gas cylinders. It specifies the type of vehicle and training required for drivers (Liquefied Petroleum Gas (LPG) Safe working practices).
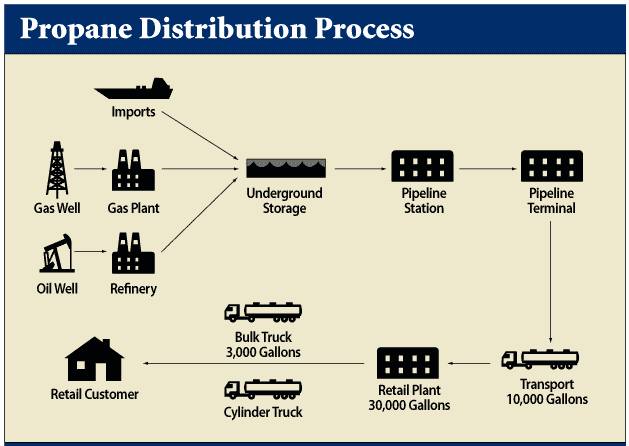
Uses of LPG
LP gas has many uses. The use of LPG is encouraged due to its cheap cost and environment friendliness occasioned by low content of contaminants such as lead, sulphur and aromatics (Khabibullin et al. 2010, p.3). Some of the major applications of LP gas are discussed below.
Heating
Due to its gaseous nature, LPG heating is easily controllable. This quality makes it ideal for industries requiring regulated heating such as glass and ceramics, metal smelting and farming to mention just a few.
Transport/automotive industry
LP gas has been used to power vehicles since 1940. Its use is encouraged due low cost and low quantity of contaminants such as lead, sulphur, metals and aromatics. Cogeneration
LPG is used for small-scale generation of electricity, steam and hot air through micro turbines and Combined Heat and Power technology (CHP).
LPG and Safety
LPG is a highly flammable gas and safety measures and devices are necessary to prevent its uncontrolled release that may result in explosion or fires (WLPGA 2012). The basic safety principles are outlined below:
- Large LPG facilities should not be constructed close to large population settlements.
- Firms dealing in LPG should promote safety culture within thin their premises and with their customers through training and sensitization programs.
- Fuel grade LPG should be adequately odorized to enhance detection of leaks.
- LPG gas cylinders should never be completely filled as environmental conditions may influence explosive expansion.
- Proper identification and warning signs should be placed at storage points and on transporting systems.
- Installation of LPG gas tanks and related appliances should be done by qualified and competent personnel.
Conclusion
LPG is becoming a popular fuel with each passing day. Due to low quantity of carbon dioxide it releases during combustion, LPG is championed as a replacement for petrol and other climate unfriendly gases. In addition to low carbon the other attractive features of the gas are huge abundance, low cost, relative safety and ease of transport. Apart from automotive industry, LPG is also extensively used in metal, building, aerosol and agricultural industries to mention just a few. Mass adoption of LPG by UK will mean the country will be at the forefront in cutting global carbon emission. LPG is a huge industry and more investment in it will guarantee more jobs and preservation of the environment.
References
26th World LP gas Forum & 2013 AEGPL Congress 2012. Web.
Comhairle nan Eilean Siar 2011, LPG storage. Web.
Environment Agency-UK 2005, Guidance for the Gasification, Liquefaction and Refining Sector. Web.
Khabibullin, E, Febrianti, F, Sheng, J & Bandyopadhyay, S 2010, Process Design and Economic Investigation of LPG. Web.
LPG Good safety practices in cylinder filling and handling n.d. Web.
LPG Properties 2012. Web.
LPG supply chain n.d. Web.
Liquefied petroleum gases n.d. Web.
Liquefied Petroleum Gas – Courtesy of AIP & World Petroleum Council 2009. Web.
Liquefied Petroleum Gas (LPG) Chapter 6 n.d. Web.
Liquefied Petroleum Gas (LPG) safe working practices n.d. Web.
Metcalfe, P 2006, ‘Cylinder filling-a history’, LP gas Magazine, p.18. Web.
Product description n.d. Web.
Shipman, H 2005, Liquefied Petroleum gas, Liquefied Petroleum Gas Association. Web.
WLPGA 2012, About LPG. Web.