Abstract
Business organizations are facing quality issues concerning their operations and products. Business scenarios are rapidly changing at a time when phenomena are not only influenced by the traditional aspects of economics but also by an accumulation of data. Therefore, management teams should adopt the best techniques to handle these matters to achieve exemplary results from business and economics points of view. Quantitative techniques are important methods that can be used by a firm to achieve a competitive advantage in the short and long run. The model a company chooses to handle quality issues depends on the complexity of the matters. This report describes how quantitative techniques can be utilized to handle the quality of goods and services. Results of the research show that three conceptual frameworks could be used in quality management that relies on the manipulation of data. These theories are network, linear programming, and assignment and transportation problem models. The results of the report may be utilized by firms in decision-making concerning quality management.
Introduction
Businesses strive to produce goods and services that meet certain standards. To achieve quality products, management teams must always adopt processes that are efficient and effective. Quality management requires unique principles as well as practices in the short and long run. Quality of goods and services is an important matter in contemporary business. Theory and experience are mixed to obtain a relatively large amount of knowledge. As stated by Beckford (34), firms have varied ways of achieving quality, but it must be understood that competition is beyond national boundaries.
Quantitative techniques are applied by managers when viewing phenomena through models that are critical to improving the quality of products. In management, these methods provide a systematic approach for the analysis of phenomena in business economics and economics in general. These techniques rely on measurements, quantification, and computations that result in statistical outcomes. Notably, these outcomes go a long way in supporting control, management, blending with other indicators as well as comparison with similar goods and services (McLean 74). This report describes how quantitative methods can be applied in quality management by firms to produce goods and services that are of unique standards (quality), which can enable them to achieve a competitive advantage.
The Context of Quantitative Techniques
Quantitative approaches to quality management rely on the utilization of numbers since measures are easily obtained when handling countable objects like the number of products. In most cases, specified devices and agreements should be used to achieve objective measurements of features such as time and price. If these conditions are not met and a numerical figure to represent a state as per a particular goal is required, it is critical to quantify that aspect. Quantification involves giving numbers to states of business reality that represent rules. Although numbers represent data, there could be issues concerning subjectivity and imprecision when quantifying elements (GQM) (Jaber 45).
Product Quality Assessment
If management teams want to assess the quality of products, they utilize inspections and tests. Inspections can be used in the initial phases when documentation is being done to mitigate defect spread, and greatly reduce the time and costs that would be associated with improvements. Consumers can confirm user interface prototypes while quality experts review analysis and design systems. The use of questionnaire templates that incorporate measurements and comments about quality go a long way in supporting reviews. In addition, it is critical to underscore the importance of quality experts as well as customers conducting tests at the end of all assessment projects (Beckford 54).
Quality assurance managers first define the standards they want to achieve. For instance, a team may choose the factor-criteria-metrics structure that can be utilized to define product quality, and it would involve four factors. First, functionality describes how a product is complete, adequate, and coherent. Second, satisfaction is assessed by determining the ease of use as well as general aesthetics. Third, maintainability includes several elements such as quality documentation, ease of modification, and portability. Finally, dependability is tested by quality management teams by finding out aspects of safety and error forbearance (Beckford 57).
To obtain these quality metrics, a team would gather data per three elements. First, diagram metrics would involve quantifying elements on diagrams and comparing them with numbers obtained in the past in similar projects (McLean 34). If the expected values would not be found for all projects, then estimations can be made. It is important to state that although diagram metrics are associated with a high level of objectivity, they are also typified by subjectivity, especially when expected values are applied. Second, evaluations with comments are numerical figures that represent subjective opinions or feelings concerning particular aspects of a project such as comprehension, aesthetics, as well as precision. Sometimes, these are more efficient than other elements since they describe attributes completely and adequately. Comments could be grouped on a scale of 1 to 5, with 1 indicating the lowest quality and 5 representing the highest quality. Finally, defect gathering based on distinct categories can be executed and later combined with results obtained from the diagram metrics element. The combination offers metrics that are good indicators of the quality of products. To ensure that the attention of a reviewer is maintained, templates would be utilized, and they combine quality matters with portions of documentation (Beckford 102). For example, a template would incorporate a diagram with narrations, relevant metrics, and errors (defects). Quantitative calculations utilizing formulas to model quality relationships can be used to automate the process.
Network Model
Manufacturers around the world are facing issues of globalization and quality rivalry from their business competitors. To handle these issues, a majority of manufacturers strive to achieve the highest quality, lowest costs, and shortest delivery times of goods. Notably, lifecycles associated with products are being shortened progressively to cater to the sophisticated needs of consumers. Outflow prevention is an essential method to handle defect matters. In addition, firms have established partnerships in industries to solve quality problems (Fuschi 283). These partnerships could be both internal- these handle design and production issues and external- to address matters experienced by suppliers concerning goods. Notably, management teams adopt high-quality manufacturing to obtain the highest levels of satisfaction of employees, customers, and other external stakeholders. This ultimate goal is achieved by preventing defect occurrences as well as by supporting progressive attainment of quality, cost, and delivery that are the results of the deployment of strategic quality assurance processes (Fuschi 283).
Four requirements are important technological elements in attaining quality, cost, and delivery goals. First, quality assurance networks should be strengthened by designing, developing, and executing assurance tools. Second, clear quantitative quality assurance definitions should be made clear. Third, management teams are expected to create a platform on which the skills of workers and information concerning past defects are arranged appropriately. Finally, employees who are familiar with particular manufacturing processes should be deployed. Therefore, the strategic execution of these elements (components) will go a long way in helping companies to avoid defects and progressively attain quality, cost, and delivery. Notably, four guidelines must be observed to achieve these goals. The initial one is assurance that involves the application of a quality network model. The second is improving relationships between supplying firms and manufacturers, and this is achieved by taking into consideration the opinions of these stakeholders about quality assurance systems. The third guideline is creating a database for a quality network that goes a long way in helping users to share information. The fourth component is the utilization of quality assurance techniques or tools to resolve past defect problems (Fuschi 285; McLean 98).
Linear Programming Model
Linear programming is a quantitative method for depicting how functions are related and determining their optimum points. Although real interactions of functions might be complex and difficult to describe, they can be simplified to learn patterns that be used to make business conclusions (Jaber 25). Since this theoretical approach relies on the optimization of variables, management teams can apply it to handle quality issues. To utilize the model to manage quality matters, teams should follow six steps. The first step involves defining the decision functions or variables, which describe choices or possibilities on which conclusions may be based. Second, the objective variables should be described, and they define what a company wants to achieve in terms of the quality of goods such as the shortest delivery route. Third, limiting issues should be highlighted. These problems can be arranged in a table that helps to achieve a visual summary. The fourth step involves drawing the practical region within which the specified conditions are met. If a firm stays within this area/region, then its quality management objectives will be attained, and it can make the optimal products, for example. The fifth step incorporates calculations that combine for optimal results. In this part, the best or optimal variable is mathematically obtained (Boonmee et al. 485). Notably, it can be located on any of the points of the practical region.
Let us assume company A has six deliveries to make in one day from a warehouse situated at point A. Buyers of the products to be delivered are located at U, V, W, X, Y, and Z locations. The numerical figures on the lines represent distances between the towns. This firm should choose the shortest route to attain the quality related to the delivery of goods to customers. By taking this route, it will also save fuel costs and time.
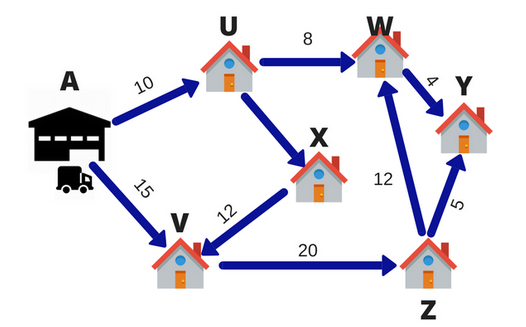
This firm will calculate several routes through which to reach the destinations and determine the shortest route. The ultimate goal in this context is to deliver the packages to the buyers on time. The method of choosing the optimal route in this scenario is known as operation research and is supported by the use of quantitative data. Operation research is a critical technique for supporting decision-making in economics that involves many methods to handle a system. The system in the above scenario is the delivery model.
Transportation and Assignment Problem Models
Assignment implies deploying employees to particular tasks in an organization. The deployment should be implemented in a manner that results in improving the quality of goods and services. Assignment problems can be handled using two methods, which are completer enumeration and the Hungarian approach. Notably, in both these methods, a particular worker can be assigned to a given task. In other words, an employee cannot be assigned to more than one task. It should be underscored that allocating more than one job to a worker lowers the level of quality of the involved products. A scenario may arise when the number of workers is bigger or smaller than that of the available jobs. This situation is known as an unbalanced problem and firms can solve it by ensuring that the number of employees available is equal to that of current tasks.
A transportation problem model is a theoretical approach to choosing routes in a network that supports the distribution of goods between manufacturers’ plants and warehouses located in different parts of a market. This model aims to achieve similar goals to those of the network discussed earlier in this report, but it employs unusual methods, which are VAM, LCM, as well as NWCR. An issue in this context is not associated with restrictions that are unique to assignment matters only. Several allocations can be implemented in rows and columns. Quality management searches for a distribution pathway that can result in cost reduction, profit maximization, and improvement of the delivery systems of a company (Boonmee et al. 488). Management teams should provide solutions to unbalanced situations that result from situations where the total demand is greater or less than the total supply. When using the transportation problem model to provide answers to product quality issues, businesses should know that the quantitative approach is utilized to determine an optimal strategy for moving commodities from sources to destinations. Each source has a particular number of units of a commodity, while each destination has a given quantity of demand, which is often known as the requirement (Boonmee et al. 495).
Conclusions
Modern-day businesses face competition from their rivals mainly due to the quality of goods and services they offer. For management teams to handle the issue of quality of products, they should utilize unique methods that would provide important outcomes both in the short and long run. Quantitative techniques are applied in business and economics to provide feasible solutions to many scenarios, some of which are related to the quality of goods and services. Since business situations keep on changing across industries, firms should progressively inspect and test the quality of their products. Three theoretical approaches have been described in this report.
First, the network model can be applied by firms to avoid product defects as well as to handle costs, quality, and delivery matters progressively. Second, the linear programming model is a technique that can be used to provide answers to difficult situations in business and economics. The method calculates variables to offer an optimal solution that can result in improved quality of products. The assignment problem model is a quantitative method for deploying workers to various tasks in the workplace. It should be noted that quality can only be maintained or improved when workers are assigned to jobs based on their skills and experiences. Finally, this report has established that companies can apply the transportation problem model to handle the delivery of goods from sources to destinations. The theoretical approach uses Hungarian and completer enumeration to provide practical solutions to transportation problems.
Works Cited
Beckford, John. Quality: A Critical Introduction. 4th ed., London, England: Routledge, 2016.
Boonmee, Chawis, et al. “Facility Location Optimization Model for Emergency Humanitarian Logistics.” International Journal of Disaster Risk Reduction, vol. 24, no. 1, 2017, pp. 485-498.
Fuschi, David L. “A Network Based Business Partnership Model for SMEs management.” Entrepreneurship and Sustainability Issues, vol. 3, no. 3, 2018, pp. 282-289.
Jaber, Mohamad Y. Learning Curves: Theory, Models, and Applications. New York, NY: CRC Press, 2016.
McLean, Mary. Understanding Your Economy: Using Analysis to Guide Local Strategic Planning. 2nd ed., London, England: Routledge, 2018.