Introduction
The present report can be opened with the help of the apt quotation by Green: “Challenger was a NASA tragedy” (par.1). NASA Shuttle Program started in the 1970s and its main aim was the creation of craft for transportation of cargo into space that would be reusable in contrast to the previous space craft that was constructed so that it could be used only once (Green para.2). The history of space exploration was opened by the launch of Sputnik 1 in 1957 which heralded a new era for astronomy (Beyond the Visisble II 1) while the brief history of the shuttles include the first space shuttle called Columbia which was launched in 1981 and was succeeded by the shuttle that is the focus of the present report, the Challenger, succeeded, in its turn, by Discovery in 1983 and Atlantis in 1985 (Green para.2). The total number of nine successful missions made “a record of service” of the Challenger before the tragic date of 28 January 1986.
On January 28, 1986, the Challenger was launched to explode 73 seconds after its lift-off (Davis para. 1). The tragedy is commonly called “the worst disaster in the history of our space program” (Davis para. 1) and it was televised live and replayed all around the world repeatedly so that the whole humanity could become the witness of the horrible tragedy. The same opportunity is offered to contemporary viewers as well, for instance, by means of “the chilling amateur footage” of the explosion recorded on a home video camera and revealed more that thirty years after the tragic accident (Luscombe para. 2). The explosion of the shuttle caused not only the destruction of the shuttle itself but also killed the while crew consisting of seven astronauts on board and set NASA’s manned spaceflight program back years (Luscombe para. 3), (1986: ‘That Y is burned into my mind’ para. 2).
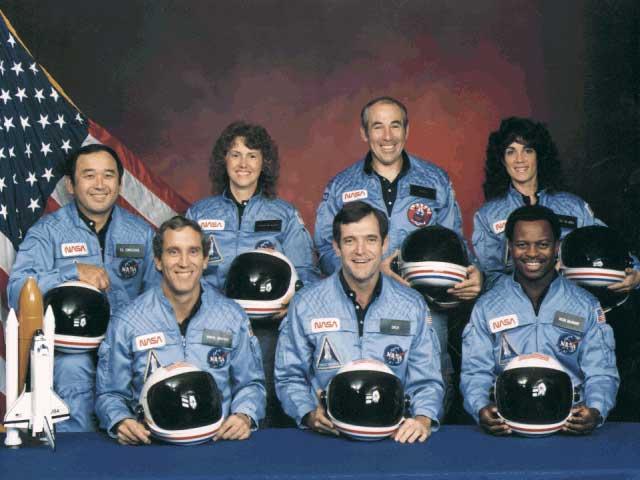
The tragic accident, provoked heated discussion and investigation of the causes of the explosion, giving rise the most commonly accepted hypothesis that the disaster was primarily caused by “a design flaw in the Shuttle’s solid rocket booster that was exacerbated by near-freezing air temperatures at the time of launch”. However, along with the major cause of the accident, there were other little-known factors, and had any of them not existed on that day, the tragedy might have never occurred. This is why there is the necessity to consider all these factors in complex and analyze them so that the possible risk of such tragedy happening again could be eliminated.
Reasons for the Disaster
To figure out the causes of the tragic disaster, it is of great use to consider different structural components of the space shuttle and understand how they function. It consists of two Solid Rocket boosters on the opposite sides of the External fuel Tank and an Orbiter on the upper side of the External tank as shown in the space shuttle diagram shown below.
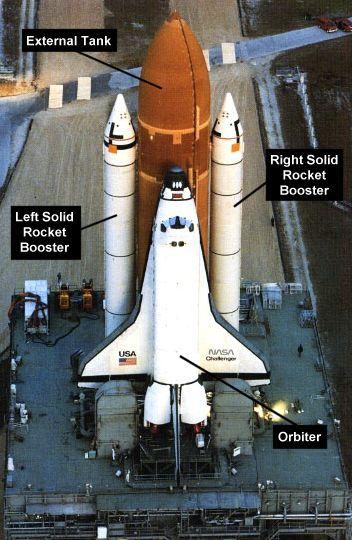
The Orbiter, as the name suggests, is the one that goes to space (Orbit), carries the crew members and the payload such as the satellite and station parts to space. The two Solid Rocket Boosters provide the propulsion needed to thrust the Orbiter into space in addition to the thrust provided by the Orbiter itself since the Orbiter cannot carry sufficient amount of fuel to take it to space. These Solid Rocket Boosters are made of numerous segments that contain solid fuel enclosed in a metallic exterior and are connected in such a way that in between the joints there are two O-ring rubbers which expand to fill the joints to avert the hot exhaust from escaping. These Solid rocket boosters ignite to generate the propelling energy and continue to burn until their fuel supply is exhausted while thrusting the Orbiter to space. As soon as they have fueled the Orbiter to rise up to a high altitude level of about 150,000 ft, the Solid Rocket Boosters are jettisoned by means of small unstable charges to set out in the Ocean where it is recovered and towed by tugboats to the seashore for renovation for the purpose of the use in the future air travel.
Finally, the last part of the shuttle is the External fuel Tank, which constitutes the largest part of the space shuttle. Three quarters of this tank are filled with liquid Hydrogen in the aft part while the remaining upper quarter of the tank section holds liquid Oxygen. The main function of this fuel tank is to fuel the three engines that are in the aft section of the Orbiter which also provide the propulsion force required to get the shuttle to space.
The propellant is feed into the External fuel tank through piping some hours before the launch of the flight and at the launch, the Orbiter is supplied with the fuel from the External fuel tank to feed three engines situated in the Orbiter for some minutes (about eight and a half minutes after take-off) after which the External tank is disconnected by the Orbiter to reach the main Engines cutoff. The external tank is disconnected as its fuel is already exhausted and it is jettisoned back from the Orbiter at a height of about 111,355m where the Tank burns up in the Ocean (Lockheed 1).
Reasons for the Space Shuttle Challenger Disaster
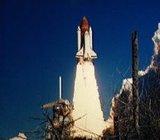
At it has been mentioned in the introductory part of the present report, the tragedy of the space shuttle Challenger occurred as a result of the structural failure of the both primary and secondary O-rings. The unusually cold temperature on the morning of the launch provoked the expandability of the O-rings (Davis para. 2). The aft field joint of the right Solid Rocket booster was sealed improperly, allowing the hot exhaust gas of about 3,315 oC from the rocket motor compartment to escape. These emanating hot gases burned and weakened the strut sustaining the Solid Rocket Booster and the exterior of the external fuel tank causing the liquid hydrogen to escape and feed the flame. At last, the external fuel tank loosened the Booster and allowed it to spin about the upper support due to this weakening. A whitish cloud could be seen on the recordings of the cameras during the flight that signified that some structural breakdown was underway.
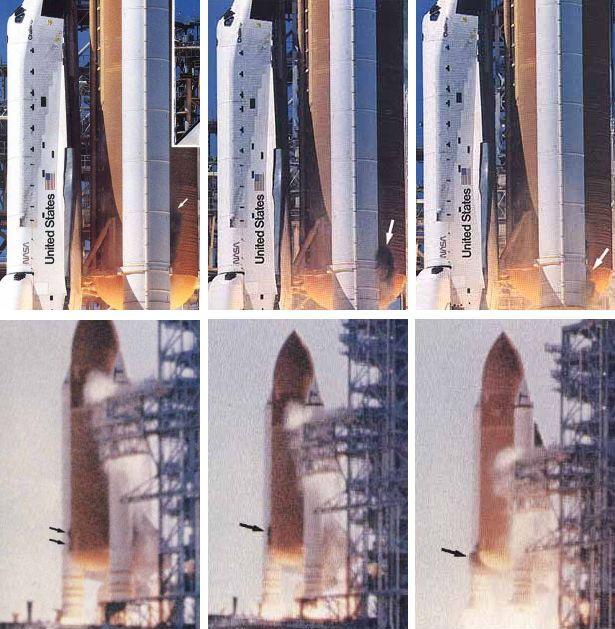
According to the ongoing camera recordings, the O-ring must also failed at some point during the mission and Pad Cameras recorded this during the launch showing some smoke coming out from the field joint of the right Solid Rocket Booster some few seconds after ignition. Some other incidents of smoke coming out the field joint were witnessed all along the mission as they can be observed in the picture below. Hence the evidence that the joint was not sealed appropriately and, consequently, the hot gases inside the Booster escaped eroding the O-ring rubber.
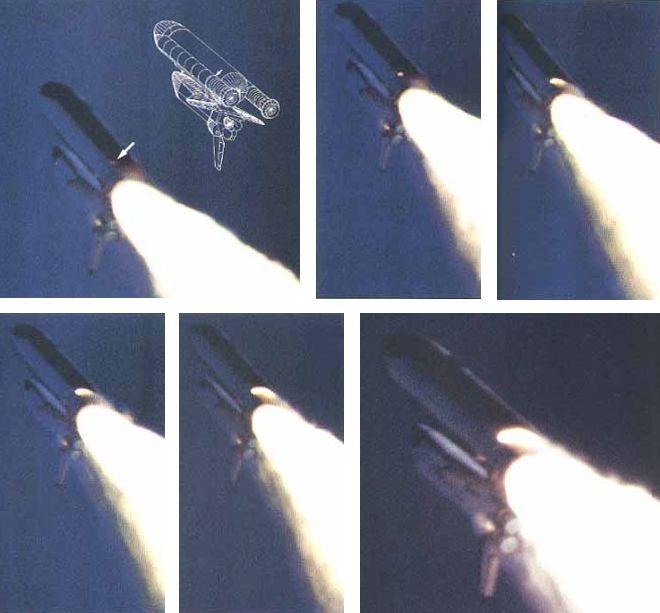
As the mission continued, no more smoke could be observed as the joint actually sealed. The sealing was most likely due to the burning fuel in the booster that heated the O-rings and expanded to seal the joint. The next explanation for the sealing of the joint is that the aluminum oxide in the rocket propellant melted due to heating and the cooling aluminum droplets sealed the joint. The joint remained sealed for some minutes as the flight went on and the force in the right Solid Rocket Booster maintained at the standard level. As the Challenger passed through the shearing air stream caused the solidified aluminum Oxide to get out of the already damaged O-rings resulting to the decline in chamber pressure and some fire was seen coming out from the in back field joint ( Aerographic: Space Shuttle Challenger Disaster para. 3-13).
This fire finally weakened the aft dome of the external fuel tank that eventually dropped from the rest of the reservoir and released a huge quantity of the liquid hydrogen, hence creating a rush forward that accelerated and pushed up the tank to the area separating Hydrogen and the Oxygen tanks. At the same time, the spinning right Solid Rocket Booster influenced the Oxygen tank leading to its failure. Consequently, the mixing of the Liquid Hydrogen and Liquid Oxygen burnt the whole shuttle and it fell into the Ocean to be recovered later (Wolk para.1-3).
Contrary to the common belief that the shuttle exploded itself, the Challenger crushed because of a structural breakdown. It then released some fuel, which vaporized to a cloud around the shuttle, creating a vision that the shuttle must have exploded.
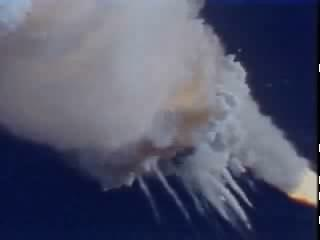
The second reason for the space shuttle disaster can be formulated as the poor decision making process. Though the engineers had sensed that there was a threatening problem, they proceeded and decided to launch the shuttle, though at first they advised NASA officials against the launch but recanted later that night (Davis para. 4). They could foresee that a breakdown of the Solid Rocket Booster could only occur during the ignition at the launch, but in contrast to their expectations, the motionless O-rings worked fine during the launch only for the breakdown to occur when the shuttle was at high altitude. This was the problem that could have been avoided if given a second thought. However, the organizational response to the technical problem could be characterized by “poor communication, inadequate information handling, faulty technical decision making, and failure to comply with regulations instituted to assure safety” (Vaughan 225).
The NASA management had also made a poor decision concerning the launch of the shuttle. Even when some inherent problems such as bad weather conditions and some doubtful structural failure were identified and communicated to NASA management team, the order to launch the shuttle was still given. Several times the schedule of the launch of the Challenger was altered and the launch was postponed five times due to unsuitable weather conditions and other factors, such as the delay in mission 61-C (Green para. 8) The temperature fell far below the level accepted for the launch of the shuttle, as the forecast had predicted the temperature close to 310 F (-10 C). The O-ring could not have sealed the joint completely due to this low temperature, hence opening up the joint when the temperature rose (Vaughan 2). Morton Thiokol, the contractor responsible for the construction of the Solid Rocket Boosters expressed certain anxiety about operating conditions of the O-ring as according to the design specification, the O-rings were not to operate at temperature below 120C (540F) as the rings had not been ascertained whether they could seal the joint perfectly at this low temperature conditions. Roger Boisjoly had already shown similar concerns regarding the temperature effects on the flexibility of the O-ring Rubbers to seal the joint and its capability to hold the high-pressure hot gases at the prevailing low temperature and Boisloy was the person who had the courage to tell the U.S. Congress that the Challenger should never have been launched “in sub-50 degree weather”. This low temperature could result in the formation of frost on the external tank (McConnel 219) and it was feared that the ice was to come loose and hit the shuttle protection thermal tiles, which could effectually hinder the shuttle launch (Adams and Balfout 95-97). All these concerns reported, NASA management still decided to ignore the signs and ordered the launch of the shuttle on the basis of “incomplete and sometimes misleading information” (U.S. Centennial of Flight Commission para. 11).
The measures to be taken to avoid such a disaster
In order to avoid such tragic accidents reoccurring, certain modifications of the shuttle should be designed to guarantee its reliability ether by using a new design which would eliminate the joint or redesign it. In case of the redesign of the joint, the O-ring should be able to function even under low temperature conditions. This will guarantee the sealing of the field joint to avoid gas leakage.
The crew rescue system also should be modified in such a way that it could provide maximum protection of the crew team in case of an accident by the introduction of safe mechanism of escape from the shuttle before it crushes. It was supposed that the crew did not die immediately when the Challenger crushed; and if their cabin got depressurized at the moment of the crush, the crew must have suffocated due to the lack of Oxygen. Personal air bags recovered from the shuttle showed that they must have been used, hence the supposition that if the Oxygen supply had been sustained, there could have been a chance for the crew to be rescued.
Finally, there should be a sufficient communication channel between the management and the scientists to facilitate appropriate decision making process. NASA safety regulations should be revised and strict execution of regulations governing the launch of the space shuttle should be given more importance. The management for various sections of the shuttle program organization should be reviewed so that every specialist involved would be accountable for the procedure (Guardian: Challenger Space Shuttle disaster amateur Video discovered para. 3-13).
Conclusion
After the tragedy, a commission was set up by the President aimed at the investigation of the causes of the accident. The presence of some technical problems in the design of the O-rings was proven; the NASA management has proved to be ineffective and erroneous since it was based on incomplete and even misleading information. The commission then recommended the modification of the design of the O-ring rubber to operate under different weather conditions, stringent adherence to shuttle launching conditions, and complete revision of the safety policy that had been relied on to schedule the launch of the space shuttle. After the application of the recommendation no incident of shuttle crash was reported until 2003 when another shuttle disaster took place in Columbia. However, the investigation conducted on this case identified no connection between the cases of the two disasters.
It is the necessary to mention that though the disaster occurred due to two basic causes analyzed in the present report, the management failure should be given primary attention. The final decision of NASA to lift off the shuttle was false as the weather conditions were not admissible for the launch; the launch should have been postponed on the basis of this concern (Vaughan 230). Finally, there is the guilt of the engineers as well since they showed their concerns to the management, but failed to prove their importance. Thus, they were only demonstrating doubt rather than taking the initiative and explaining to NASA management what the possible consequences of the launch before the tragedy happened.
Works Cited
Adams, Guy B. and Balfout, Danny. Unmasking Administrative Evil. New York: Sharpe Publishers. 2004.
Anonymous. Beyond the Visible II: The impact of space exploration on astronomy. 2010. Web.
Anonymous. Space Shuttle Challenger Disaster. 2010. Web.
Anonymous. Space Shuttle Challenger Disaster. 2010. Web.
Anonymous. 1986: “That Y is burned into my mind.” BBC. 2010. Web.
Anonymous. Whistleblower in Space Shuttle Challenger disaster speaks. 2010. Web.
Astrographics: Space shuttle Challenger. 2010. Web.
Davis, Phillip M. A look back at the Challenger disaster. Latest advice on engineering and the law. Design News, Boston, MA: Davis & White, P.C., 1996.
Guardian: Challenger Space Shuttle disaster amateur Video discovered. 2010. Web.
Greene, Nick. Challenging Disaster – A NASA Tragedy. 2010. Web.
Lockheed, Martin. The Future of Space is Now. Belmont: Sharpe Publishers, 2006.
Luscombe, Richard. Challenger space shuttle disaster amateur video discovered. Guardian. 2010. Web.
McConnell, Malcom. Challenger: A Major Malfunction. USA: Doubleday, 1987.
U.S. Centennial of Flight Commission. The Challenger Accident. 2010. Web.
Vaughan, Diane. “Autonomy, Interdependence, and Social Control: NASA and the Space Shuttle Challenger.” Administrative Science Quarterly, 35.2, (1990), 225-234.
Vaughan, Diane. The Challenger Launch Decision: Risky Technology, Culture, and Deviance at NASA. Chicago: University of Chicago Press, 1997.
Wolk, Alan. The Space Shuttle: A Perfect Safety Record But Not for NASA. 2004. Web.