Introduction
The modern business world is characterized by the constant increase in demand for various products as clients want to satisfy their diversified goods. It means that companies have to work with the growing number of products that should be delivered and stored appropriately. Under these conditions, effective warehouse design, supply chain management, and logistics acquire the top priority as the main determinants of firms’ success and their ability to continue their rise.
The following paper revolves around the warehouse design for medical supplies. These are a specific type of perishable goods that have to be kept safe before arriving at the pharmacy. For this reason, there are several critical demands for organizing their storing, management, and delivery, which come from the nature of products and the industry in general.
The “Through Flow” warehouse design is the best choice for pharmaceutical storage as it provides a linear order, flowing capacity, and temperature control zones, guaranteeing safe, accurate, and flexible product organization and configuration. Additionally, the chosen design helps to consider logistics issues and improve distribution processes, which is vital for the outcomes.
Industry and Product Characteristics
The pharmaceutical industry is a highly developed and attractive industry characterized by a stable rise. The growth in the number of chronic diseases and the increased attention to heal issues from various agents, such as government and individuals, precondition the increase in demand for medicines and their diversification. Thus, pharmaceuticals are very sensitive to multiple factors, such as external contamination or temperature changes.
Sometimes, even the lighting and other insignificant aspects can influence medicines (Abideen & Mohamad, 2019). Furthermore, drugs must be placed in a dry, devoid of humidity, or else, they will expire or lose their potential (SciSafe, 2019). Additionally, their expiration date should be considered as a primary factor for sorting them out. For this reason, the pharmaceutical industry is characterized by the specific demands for warehousing to avoid deterioration in the quality of products.
Furthermore, the appropriate supply chain management is fundamental to the sphere. It is vital to ensure that the product is in proper condition and delivered in a timely fashion. Since medical supplies are considered perishable goods, they require adequate packaging, storage, and careful handling (Abideen & Mohamad, 2019). Additionally, many pharmaceuticals have a relatively short expiration period, which should be considered by different actors of the distribution chain.
The distribution chain starts with the manufacturer of raw materials located local or abroad, which transports chemicals or raw packaging materials to the producer of medical supplies (Amarji et al., 2018). The pharmaceutical company receives a purchase order and manufactures the product using the raw materials and employs an advanced packaging system to deliver a safe, stable, and undamaged medical product (Amarji et al., 2018).
The pharmaceuticals are then directed to the wholesaler, who organizes appropriate storage conditions and supplies the goods to medical facilities or pharmacies. The movement of raw materials and packaged products is supported by logistics and transportation companies (Dani, 2015). Finally, the pharmaceutical product is distributed by healthcare facilities and pharmacies, delivering the end product to consumers.
In such a way, the peculiarities of products, such as their vulnerability, sensitivity to external factors, and the demands to supply chain management can be considered the vital characteristics of the pharmaceutical industry which should be considered when organizing the sufficient management model and selecting the warehouse design that will be able to ensure the highest effectiveness and minimize the negative impact of various risk factors. Goods should be delivered quickly and safely, which becomes the central demand for employed strategies.
Warehouse Layout
Considering the industry’s peculiarities mentioned above, the choice of the appropriate warehouse design becomes fundamental for preserving the high quality of products and their further distribution. For this reason, the final layout rests on the “Through Flow” model, which allows the pharmaceuticals to be moved in a “first-in-first-out” pattern. Several factors explain the utilization of the given model and its ability to ensure positive outcomes.
First, the choice of the given method is justified by the improved accessibility of goods (De Koster et al., 2017). As the pharmaceuticals demand the “first-in-first-out” system, this design’s linear order can ensure its productivity because the goods will travel in a single direction. The flow consideration, which presumes an adequate sequence of operations, should be included here as well.
This is especially relevant since the “through” warehouse layout consists of multiple channels that flow one way, thus involving a lesser risk of someone taking out the wrong product (De Koster et al., 2017). It guarantees better management of all products and preservation of their appropriate state.
Additionally, the throughput capacity is also identified in the case of storing pharmaceuticals. Different lines of this warehouse layout may have a temperature control function, not overlapping other areas. Because drugs are dependent on climatic changes, receiving and dispatching areas should be weatherproof. At the same time, the product specification consideration might be the most important as it presumes that drugs must be kept in an out-of-reach safe environment (De Koster et al., 2017).
Short expiration dates and decreasing potency of various pills can also be taken into account by creating special areas for such items (Filina-Dawidowicz & Postan, 2016). In such a way, the given warehouse design provides opportunities for creating various zones for storing different products and avoiding deterioration in the quality of goods, critical for the pharmaceutical industry.
Finally, the employment of the “Through flow” model helps to consider factors associated with logistics. The delivery of goods, their acceptance, and admission become more effective and well-organized due to the adherence to the given model. The existence of several zones with the direct flow of products helps to avoid unnecessary delays and ensure that clients will benefit from high-quality products.
The logistics issues can also be simplified due to the improved warehouse design and management. In such a way, the choice of the given model is justified by the needs of the industry, the demand to preserve the appropriate state of products by creating storing zones with various conditions, and by the reduced time needed to manage new goods.
Distribution Process
The product packaging and handling are two other fundamental factors that should be considered analyzing the supply chain and the distribution processes. The current requirement for drugs and their transportation process affect how they should be packed to avoid defects and damage caused to them during delivery. For this reason, receiving and dispatching areas in the warehouse should have special equipment to preserve integrity.
A similar demand is introduced for vehicles transporting drugs. They should be capable of guaranteeing a certain environment characterized by temperature, moisture, and lightning, regarding the specifications of products outlined by manufacturers. It will promote the increased effectiveness of the distribution process.
Packaging also plays a critical role in the distribution process. First, it impacts the cost of distribution as additional materials for vulnerable goods can increase the final price. For the pharmaceutical industry, the use of special polymer is preferable as it allows air circulation while limiting the entry of moisture, which significantly reduces medical supplies’ integrity. (Mafini & Loury-Okoumba, 2018). For this reason, the given material is preferred for drug distribution.
In large supplies, the products are delivered in the blister package to ensure additional protection. Sensitive medical equipment can be transported using the multi-compartmental trays to preserve its condition and avoid damage (Mafini & Loury-Okoumba, 2018). Moreover, the sort of product and its specifications will impact packing and cost of distribution. For instance, individual wraps packaging can be used for the most vulnerable or single products that demand special handling, and cartons become a possible option.
Cartons are usually manufactured from fiberboards and meet the requirement for storage at room temperature (Mafini & Loury-Okoumba, 2018). Ample supplies, such as over-the-counter medicine or basic pills, can be packaged using cartons allowing for the breakdown of medical products into smaller individual cartons for ready usage.
Finally, packaging and handling considerations should be discussed with a manufacturer to determine the optimal distribution practices and conditions needed for specific goods. Direct and dual distribution channels can be used regarding the existing demand and delivery time requirements. In such a way, the distribution of drugs might demand additional costs because of the increased attention to packaging and handling; however, these factors are fundamental for preserving the high quality of products and effective supply chain management.
Government Regulations
The importance of the pharmaceutical industry also means the increased significance of government regulations as the central tool for protecting citizens from poor-quality drugs and avoiding problems with storing, transportation, and delivery. For this reason, the recommendations affect both storing facilities, distributors, and manufacturers.
The role of government can also be seen in warehouse management as it introduces requirements for protecting goods from contamination, deterioration, and other external factors that might precondition the worsening in the quality of drugs. For this reason, several major acts and laws should be considered.
First, Good Manufacturing Practice (GMP) and the US Drug Supply and Chain Security Acts (DSCSA) require all supply chain partners to electronically track prescription drugs (De Koster et al., 2017). In this way, it can be seen whether or not the requirements are met, ensuring products are safe and effective to be distributed on the market.
Moreover, the given act allows Food and Drug Administration (FDA) to protect final consumers from using medicines that are stolen, contaminated, or harmful because of the disregard of demands for storing and transportation (FDA, n.d.). In accordance with the given act, all potentially corrupted drugs should be removed from the supply chain, which introduces additional demands to distribution and warehouse management.
The DSCSA act is also applicable for logistics provides, meaning that they should align their functioning with the given document. The third-party companies offering transportation services should also guarantee the increased attention to the conditions of goods and preservation of their high quality during the delivery. Additionally, the Code of Federal Regulations Title 21 introduced by FDA (n.d.) demands that all facilities for storing drugs should be protected from unauthorized entry to avoid stealing products.
Furthermore, there is a need for strict control presupposing recordkeeping and inventory management to avoid confusion. The given regulations affect distribution and sales as all changes should be noted and reported to regulatory agencies. As for the global distribution, the FDA and the international agencies, such as the World Health Organization and agencies of other states, establish a legal framework that should be observed (FDA, n.d.).
The Role of Logistics Providers
Because of the specific demands existing within the pharmaceutical industry, logistics providers must possess knowledge of pharmaceuticals as perishable medical goods differ from other products in their requirements for safety and longevity (Ghiani et al., 2013; Kaszubowski, 2014). Moreover, logistics providers ensure that products are transported under conditions required by the DSCSA. That is why transport and storage systems should have temperature control equipment to protect the quality of medical supplies.
Direct distribution channel, cooperation with the manufacturer, and proper packaging assist in timely delivery of products with a limited expiration period. For this reason, logistic providers play a crucial role in guaranteeing the stable functioning of the industry and effective supply chain management. These actors are responsible for monitoring the quality of products during delivery and reducing risks linked to external factors. For this reason, medical supplies are critically dependent on appropriate and effective logistic services.
The Impact of Reverse Logistics
Reverse logistics is another factor impacting the pharmaceutical industry. Thus, expired medical products’ disposal through regular channels poses a threat to the environment (de Campos et al., 2017). For this reason, expired or poor-quality medications should be returned to avoid adverse effects. However, it is vital to trace the returns along with the primary causes for the deterioration of the condition and the recall.
It means that warehouses should possess automated technologies allowing workers to improve reverse logistics operations and accept goods that should be returned to the manufacturer to minimize the threat to the environment or harm done to the third parties. In such a way, the selected warehouse design offers specific zones for accepting and storing delivered in terms of reverse logistic operations, which improves supply chain management and ensures avoidance of undesired outcomes.
Conclusion
Altogether, the pharmaceutical industry requires the warehouse and other elements of the supply chain to adhere to strict temperature, moisture, and ventilation conditions, while also following government regulations. For this reason, a “Through Flow” warehouse design is viewed as a perfect fit for addressing these issues and guaranteeing goods’ quality upon distribution. Moreover, the increased importance of packing and handling during the distribution process introduces specific demands to logistic operations, as their providers should guarantee the appropriate environment during transportation to avoid causing damage to products.
The existing FDA regulations emphasize the need for specific conditions for storing and transporting of drugs, which also introduces additional requirements for warehouse design. In such a way, the choice of appropriate storing practices and strategies is impacted by the peculiarities of the industry and goods, the major aspects of logistics, and the governmental regulations. The choice of practical warehouse design ensures effective supply chain management and minimization of the number of risks or problems during all stages of delivery.
References
Abideen, A., & Mohamad, F. (2019). Supply chain lead time reduction in a pharmaceutical production warehouse – a case study. International Journal of Pharmaceutical and Healthcare Marketing, 14(1), 61-88. Web.
Amarji, B., Kulkarni, A., Deb, P. K., Deepika, Maheshwari, R., & Tekade, R. K. (2018). Package development of pharmaceutical products: Aspects of packaging materials used for pharmaceutical products. In R. K. Tekade (Ed.), Dosage form design parameters: Volume II (pp. 521-552). Academic Press.
Dani, S. (2015). Food supply chain management and logistics: From farm to fork. Kogan Page.
de Campos, E. A. R., de Paula, I. C., Pagani, R. N., & Guarnieri, P. (2017). Reverse logistics for the end-of-life and end-of-use products in the pharmaceutical industry: A systematic literature review. Supply Chain Management: An International Journal, 22(4), 375-392. Web.
De Koster, R., Johnson, A., & Roy, D. (2017). Warehouse design and management. International Journal of Production Research, 55(21), 6327-6330. Web.
Food and Drug Administration. (n.d.). CFR – Code of Federal Regulations Title 21. Web.
Filina-Dawidowicz, L., & Postan, M. (2016). Optimal inventory control for perishable items under additional cost for deterioration reduction. LogForum, 12(2), 147-156. Web.
Ghiani, G., Laporte, G., &Musmanno, R. (2013). Introduction to logistics systems management (2nd ed.). John Wiley & Sons.
Kaszubowski, D. (2014). Determination of objectives for urban freight policy. LogForum, 10(4), 409-422. Web.
Mafini, C., & Loury-Okoumba, W. V. (2018). Extending green supply chain management activities to manufacturing small and medium enterprises in a developing economy. South African Journal of Economic and Management Sciences, 21(1), 1-12. Web.
SciSafe. (2019). Understanding the importance of temperature control in pharmaceutical stability. Web.
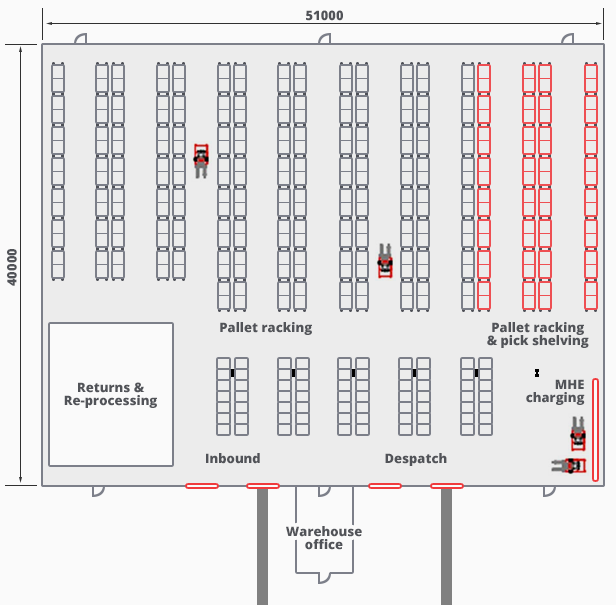