Executive Summary
Airlines conduct periodical MROs (maintenance, repair and overhaul) to upgrade the reliability and airworthiness of their aircraft. Parts have to be changed to provide safety and reliability to aircrafts. Parts coming from original manufacturers, the Original Equipment Manufacturers (OEM), have become so expensive that they accumulate a big portion of the budget of airline carriers.
Parts Manufacturer Approval (PMA) is the answer to airline carriers’ woes. Costs of replacement parts produced through the PMA system are up to 50 percent lower than the original OEM parts. This is the main reason why PMA has become popular. Parts manufacturers under the PMA system offer many benefits to aircraft owners in their MRO needs.
The U.S. Federal Aviation Administration (FAA) is the agency responsible for request approval of replacement parts. It is now supportive of the PMA system giving the industry some leeway in choosing low-cost replacement parts. The FAA also provides strict guidelines to the PMA system so that quality, reliability and airworthiness of replacement parts are not jeopardized.
OEM replacement parts were originally focused on engines and turbines but as cost-cutting measures of airlines grew, parts for other stages of an aircraft are needed; this includes replacement for electronic articles. OEM manufacturers believe that replacement parts market is their aftermarket and therefore a source of income. They have reacted to the popularity of the PMA system and parts that they have instituted measures to discourage airlines to support the PMA system. One reaction is to deprive the PMA manufacturers of the needed information for certain parts. OEMs also charged the quality, reliability and airworthiness of the PMA replacement parts, stating that this should be a primary cause of concern for the industry and the riding public because it involves safety. But there has been no concrete evidence that PMA replacement parts are of low quality, in fact, some airlines support PMA manufacturers and their products, indicating that the latter have better or superior performance than the original.
The FAA assures the industry that the procedures and guidelines are so stringent that they assure quality and reliability of the replacement parts. Once the request for design and production are approved, quality and reliability go with it; meaning the quality of the part can speak for itself as it can withstand vibration and heat in a flying aircraft.
The background of the PMA system has become intensive. This means it has been in practice since the last fifty years. It started in the eighties, became quite popular in the nineties, and now its popularity is gaining ground due to global events that have forced aircraft owners and airline carriers to dramatically cut costs: the aftermath of terrorist attacks against the United States, the intermittent wars in the Middle East and elsewhere in the globe, global terrorism and the United States’ war on terror, the SARS pandemic, calamities and natural disasters, and so on. These negative global events have slowed down travel and tourism and reduced profits and income of airline carriers.
North American airlines, the European and Asian airlines are continuously suffering from high costs of maintenance parts. Many airlines have resorted to outsourcing MROs to cut costs. Industry insiders believe that the ultimate solution to the high cost of maintenance is the PMA system where replacement parts approved by the FAA in the US, the EASA within the European Union and many other Asian countries, are of low-cost and quality oriented.
Introduction
Parts Manufacturer Approval (PMA) is an alternative to the expensive parts provided by Original Equipment Manufacturers (OEM). The Federal Aviation Authority (FAA) is now very supportive of the use and popularity of PMA parts. In a Special Airworthiness Information Bulletin, FAA authoritatively provided a reason why PMA parts’ popularity is emerging: airline owners and operators want to reduce maintenance costs particularly on replacement parts. (Azcué 2011, p. 2)
Engine manufacturers became worried of the competition posed by PMA but the blame rests on OEMs because of their expensive parts. FAA assures everyone – OEM manufacturers and the general public – that to acquire parts approval means following stringent procedures that would ensure quality, reliability and airworthiness of the replacement parts being applied for. Replacement parts that are FAA-approved ensure peace of mind for aircraft operators and owners and the public can rest assured that safety and airworthiness are the number one priority. FAA procedures are exactly the same with FAA guidelines imposed on OEMs. (Azcué 2011, p. 3)
Airlines have been using PMA parts over the last fifty years, but the need and acceptance escalated only very recently. The industry is vulnerable to economic downturns and whatever kind of disturbance. (Doll 2010, p. 2)
The effects of 9/11 and the subsequent economic downturn forced airlines, specifically the North American airlines, to initiate cost-cutting measures. Other countries particularly those in Europe and Asia followed and made their own approval, sometimes coinciding with the U.S. FAA processes and guidelines. The European Aviation Safety Agency (EASA) is the PMA’s counterpart in Europe which provides even stricter approval procedures. (Doll 2010)
PMA parts provide the solution with as much as 30 to 50 percent savings. The benefits offered by low-cost PMA parts enabled companies to earn savings in millions. Europe and Asia regions have already recognized that use of PMA parts in lieu of the high-cost OEM parts can reduce costs and provide savings particularly in the MRO (maintenance, repair and overhaul). This PMA popularity is bolstered with the emergence of low-cost carriers, approximately 50 carriers of the existing 80 carriers in Europe. They also outsource MROs; there is the emergence of third-party MROs. Europe has a disadvantage because there are no parts manufacturers except the existing OEMs. (Jensen 2006, para 2)
Martin Ambrose of the European Regions Airline Association (ERA) argued that there is still the great debate over PMA parts but which can favor the latter. According to Ambrose, PMA parts are an additional source to OEM parts; the two can be equal with respect to reliability but they can also fail. However, there is still the question of whether the lessor community would permit the use of replacement parts. Nevertheless, EASA has given the go and the assurance of the reliability of PMA parts. (Ambrose n.d.)
Historical Background
In the 1990s, there emerged spare articles for aircraft without FAA approval which when investigated was traced to suppliers. FAA advised suppliers to obtain a PMA. But there was again another issue on this when it was found that some articles were installed that were not type certificated products. These electronic articles were known as suspected unapproved parts (SUP). (FAA Advisory Circular 3a and 3b)
Why is there a need for PMA replacement parts? Why not require Original Equipment Manufacturers (OEM) to manufacture spare parts as reserve parts like what automotive and appliance manufacturers do?
The questions provide an immediate and definite answer: owners and operators as well as MROs do not want to buy OEM parts because the parts are too expensive. In these trying times, the airline industry needs to cut costs to remain in business. With Iran on the brink of closing the Strait of Hormuz, oil prices are likely to go up with travel and tourism going low. Oil and travel are related. And this is one of the reasons why air carriers have to consider using PMA parts as a means to save operational costs without sacrificing safety of the riding public. (Azcué 2011, p. 2)
High fuel prices will add to the airlines’ operating costs while less fuel-efficient planes are also costly to maintain and operate. Less fuel-efficient planes prompt airlines to retire the old ones. Michael Howard of AeroStrategy (Marpa 2011) explained that air carriers are retiring old aircraft in large quantities, an average of 400 aircraft a year. Continuing the operation of these aircraft and allowing them to fly would add more operational costs to the owners. The logical solution is to retire old ones and allow MROs to use PMA parts for those aircraft that don’t require high maintenance costs. (MARPA: economic outlook for the PMA marketplace 2011)
In 2004, in spite of an improvement in the airline business, US airlines had a collective deficit of $9 billion. Net profit, operating profit and total revenues of major US airlines are demonstrated in Appendix B. (Doll 2010, p. 2)
AeroStrategy provides analysis of the PMA market. Howard indicated that in 2010, the air transport MRO (maintenance, repair and overhaul) market was estimated at $43.6 billion but in 2007, it was high at $45 billion and $42.7 billion in 2009. Growth in the MRO market is seen at 3.5% this next decade and will reach $54.8 billion by 2019. MRO supply chain has to be simplified in order to gain cash, Howard said. Airlines have to cooperate with MROs to use PMA parts. (MARPA: economic outlook for the PMA marketplace 2011)
In 2009, the airline industry recovered $47 billion in excess inventory. Simplifying excess inventory is one way of saving; likewise reducing MRO excess inventory is a way of reducing spending. But this is not a permanent solution. Another way of saving, aside from PMA parts, is disassembly or parting out of aircraft. Surplus parts reached $2.3 billion in 2009. (Doll 2010, p. 2)
If fuel stabilizes at $80-$110 a barrel, there could be modest growth in the U.S. gross domestic product (GDP), that is, to include the airline industry. PMA growth was 4% in 2010, from $353 million to $367 million in 2009. (MARPA: economic outlook for the PMA marketplace 2011)
The growth potential for the use of PMA parts is great. MRO shops have been using PMA parts, and those non-OEM shops that are not using PMA are in the process of doing so. Airlines are becoming convinced of the acceptability of PMA. Other countries are now considering PMA parts. Japan has contracts with HEICO and Wencor to use PMA parts. (Jensen 2006, para. 13)
PMA parts are considered new because they are manufactured according to specifications and guidelines by the FAA. PMA suppliers can deliver parts anytime. (Doll 2010)
Definitions and Concepts
Parts Manufacturer Approval or PMA is an official approval from the FAA on the design and production of aircraft replacement parts. The PMA system has a go signal by the U.S. FAA to manufacture aircraft replacement parts subject to stringent procedures. PMA has become a system itself wherein TC or certificate holders are authorized to manufacture and supply aviation parts to owners, operators and aviation agencies in lieu of the parts originally manufactured by OEM companies. PMA parts are subject to FAA regulations and guidelines. PMA approval includes the design and production, two important aspects of the PMA approval system. (Federation Aviation Administration: parts manufacturer approval (PMA) 2011)
There is currently big demand for PMA parts because of the high-quality and low cost attributes as compared to OEM parts. OEM parts are becoming too costly that airlines have demanded other sources of parts. (Doll 2010)
The government through the FAA has the authority to screen and approve manufacturers in their application to manufacture aircraft replacement parts. Aircraft parts manufacturing and sales are a part of the so-called aftermarket which expanded due to airlines’ cost-cutting measures. From its inception in the 1980s, obtaining FAA approval has always been difficult. Many had failed but others who followed the guidelines to the letter succeeded. (Azcué 2011, p. 2)
The FAA made moves to help PMA applicants because government regulators saw the potential of improving replacement parts manufacturing and what it could do to the airline industry. The FAA conducted an “enhanced enforcement” to educate manufacturers about the significance of approval or certification processes. As a result, many parts were approved. Manufacturers who had previously no PMAs could now apply and acquire certifications in accordance with the FAA regulations. So there was a resurgence of approved PMA parts. The Modification and Replacement Parts (MARPA) has a goal to harmonize the standards set by FAA which became effective by April 16, 2011. (Azcué 2011, p. 2)
The FAA Aircraft Certification Service issued a bulletin stating that parts being licensed to TC/PC holder, PMA, and STC can be used interchangeably because these products are approved in compliance to the provisions of Title 14 of the Code of Federal Regulations (14 CFR). Therefore, PMA or STC parts are approved replacement parts pursuant to FAA regulations. (FAA Aircraft Certification Service: special airworthiness information bulletin 2008)
FAA authorizes some manufacturers of aviation parts in accordance with the requirements of the PMA system. PMA parts hold the quality and airworthiness of parts manufacturers by OEM for as long as manufacturing provisions and requirements are followed. The FAA’s motivation and warning states that for as long as a manufacturer does not infringe upon another manufacturer’s patent, the former can manufacture a part that can be installed on an aircraft. (Stephens 2008, para 2)
Moreover, PMA parts are not considered bogus or fake because they follow certain quality standards and systems during manufacturing. The big difference is that they are much cheaper than parts manufactured by OEM, which provide the needed benefits airlines expect with respect to safety and validity, and airworthiness. (AEROSUP: FAA PMA aircraft parts distributor 2009)
The airline industry has accepted the fact that PMA parts offer the same quality with even better performance than OEM with respect to safety and reliability. (Yi cited in Holland 2008, p. 53)
Terms and Acronyms
Terms and acronyms used in this Report (U.S. Department of Transportation FAA: advisory circular 2010): Original Equipment Manufacturer (OEM). Original Equipment Manufacturers are so-called manufacturers of engines, turbines and other major parts of an aircraft. Actually, an engine is a combination of outsourced parts, manufactured by suppliers, making OEMs systems integrators and not manufacturers as what they are called. Legally, “OEMs are Type Certificate and Production Certificate holder” (Doll 2010, p. 5)
Code of Federal Regulations (CFR). The Code contains rules from the Federal Register, formulated by the executive departments and other agencies of the U.S. government. (Code of Federal Regulations 1999)
Parts Manufacturer Approval (PMA). This is a system defined in the CFR that provides procedures and guidelines for requests and approval of replacement parts of an aircraft. Requests and applications are forwarded to the Aircraft Certification Office which has jurisdiction over the geographic area where the application/request is made. (MARPA.org: what is PMA? 2012)
Type Certificate (TC). Type certification assures that the PMA part follows the stringent guidelines set by the FAA. (Code of Federal Regulations 1999)
Supplemental type certificate (STC). This is issued to an aircraft owner who does not introduce a major change on an engine, and his change may not require a type certificate. (Code of Federal Regulations 1999)
Suspected unapproved parts (SUP). Any replacement part that did not pass or is not applied for request with the FAA is called SUP. (Code of Federal Regulations 1999)
Design approval holders (DAH). This pertains to the PMA manufacturer with an approved design of a PMA part. (Code of Federal Regulations 1999)
Aims
This paper aims to conduct a study, including background and concepts of the PMA system, how it evolved and the many challenges PMA manufacturers encountered in the course of its introduction into the aviation replacement parts.
Objectives
The study focuses on the advantages and disadvantages of the PMA system and the replacement parts industry in relation to the aviation industry. Through the vast literature on the PMA system provided by the different organisations and stakeholders, this Researcher dug up records, ideas, concepts and opinions of people involved in the replacement parts industry and provided a clear emphasis on the advantages and disadvantages of the PMA parts.
Other specific objectives include:
- To know and understand how the PMA system works;
- To discuss the pros and cons of the PMA system and why is there a need for PMA replacement parts;
- To investigate the quality and reliability of the PMA parts compared to the OEM parts;
- To determine how the Federal Aviation Administration (FAA) approve application for PMA parts and the processes of approval;
- To determine how the industry lays down the framework for the PMA system;
Deliverables:
- Advantages and disadvantages of the PMA system;
- Background of the PMA system and the OEM;
- Background researches on the FAA and FEASA, two regulatory agencies from the United States and Europe, respectively, pertaining to procedures in PMA parts approval;
- An investigation into the procedures of the various regulatory bodies regarding the PMA parts industry
- Definitions and concepts of the PMA system;
- Background and the monopoly of the OEM;
- Maintenance-repair-overhaul sector of the aviation industry;
- Background and operations of the various organisations involved in the replacement parts industry and the PMA;
- Other topics of great importance in the replacement parts industry.
Differences between PMA and Bogus Parts
The question of bogus parts attributed to PMA parts is being posed by OEM manufacturers. PMA could be mistaken for bogus parts but PMA parts performance so far proves that there are those approved parts that performed better than the genuine parts or those manufactured by OEM. Moreover, PMA parts should not be mistaken as bogus because the approval process is legal and follows a stringent method of production. The PMA is approved by the FAA of the United States, the EASA of Europe and other government agencies of other countries whose guidelines are also parallel to the FAA guidelines and regulations. (Doll 2010, p. 4)
Another thing is the performance of PMA parts with respect to reliability and airworthiness, and longevity. True, both OEM and PMA parts can fail and have their own weaknesses. This is true with any other man-made object or appliance. But many airlines and organisations that have been using PMA have attested to the PMA’s quality and reliability. (Doll 2010, p. 4)
FAA authorities have also assured the public that they are on guard of bogus parts and warned repair stations not to use bogus parts for they surely will backfire on their performance, safety and airworthiness. Using bogus parts is a criminal offence under U.S. laws. Violators can be meted jail terms with corresponding huge fines. But there are those in the airline industry that have kept their mouths closed on the subject of bogus parts. Why? They could be using some parts for substitute. Others said that the airline industry is susceptible to this kind of problem. FAA is investigating some cases of airlines using bogus parts. (AV Buyer: bogus parts: are they still a problem for business aviation 2009)
Bogus has a term in the FAA dictionary and this is “suspected unapproved parts” (SUPs). Bogus refers to different instances and uses in the aircraft under maintenance, for example, it can refer to parts with incorrect documentation, counterfeited or copied parts with no quality but look like the original, and parts made from inferior raw materials. These parts could also be the result of thief, or from unlawful manufacturing, and not checked for quality. (AV Buyer: bogus parts: are they still a problem for business aviation 2009)
The FAA’s stern warning is that without its approval, parts are considered “Unapproved parts” and must not be considered PMA parts or OEM parts. FAA inspectors only recognize legitimate parts from licensed OEMs and FAA-approved PMA parts manufacturers. Investigators easily recognize the markers and features in PMA parts. (AV Buyer: bogus parts: are they still a problem for business aviation 2009)
Armando Leighton of CRS Jet Spares however says that with today’s technology, it is so difficult to spot an SUP and sometimes the only way to spot an illegal part is through documentation. There are also instances that SUP fabrication is superior than PMA or the original OEM parts that only those with expert knowledge of the original can recognize a bogus part. FAA has issued a directive to its governing bodies that documentation is very important and if this is not produced along with the parts, it should not be used. (AV Buyer: bogus parts: are they still a problem for business aviation 2009)
There could be infiltrators of counterfeited parts, especially now with airlines’ cost-cutting measures. Leighton says that there were many counterfeiters in the past because these parts could be made in ordinary machine shops Doing business with PMA has produced vigilance among manufacturers and buyers. They are now more aware of the presence and infiltration of bogus parts. Any suspected parts are reported to their loop or the manufacturers. (AV Buyer: bogus parts: are they still a problem for business aviation 2009)
Technology has helped them track bogus parts, especially with fast communication. PMA manufacturers have also made use of holograms in tracking genuine parts and distinguishing them from bogus or unapproved parts. Leighton says that it is somewhat the same as tracking counterfeit dollar bills. (AV Buyer: bogus parts: are they still a problem for business aviation 2009)
The solution really is vigilance, for no one will sell bogus parts if no one buys. The FAA has made great efforts in instilling awareness to the aviation industry and provided difficulties to bogus manufacturers and sellers. There is also the danger of using bogus parts without one knowing it but if documentation processes are followed, then there’s no reason of using bogus parts. FAA and PMA standards have been stricter because of these circumstances, and to get a part approved it would take about six to twelve months. FAA informs the industry and the public through its website the procedures needed in applications and approval requests. The information can range from ordinary procedures to how to spot or recognize SUPs or parts for an airframe or engine. ((AV Buyer: bogus parts: are they still a problem for business aviation 2009)
Vigilance on avoidance of bogus parts has been observed by many involved in repair and maintenance and those on safety and airworthiness. Experts are one in saying that the FAA has been successful on this regard. If you know the paper work, deal with authorized vendors, and be watchful about these parts, there could be no reason a bogus part could infiltrate. There might be some mistakes that could not be avoided because, as Leighton says, aircraft owners and operators buy thousands of parts annually, but for as long as safeguards are observed mistakes can be avoided. What to do if someone finds a bogus part? The bogus part should be quarantined and immediately reported to the FAA office. The best defense is to trace the origin of the SUP. It is necessary to buy parts from reliable vendors. (AV Buyer: bogus parts: are they still a problem for business aviation 2009)
Procedures in PMA Approval: Europe Aviation Safety Agency (EASA) and Federal Aviation Administration (FAA)
The U.S. FAA
In the United States, PMA parts purchased should have FAA-PMA marks that include the name, trademark and other important details of the product, but not missing out the model designation for the part installation. Some parts which are too small for marking or etching should have a tag as it is enclosed in a plastic bag. But what is most important in purchasing PMA part is the PMA letter of approval which lists the part number that differs from an OEM part by a prefix or a suffix, and the eligibility for the product. (Lombardo 1999)
FAA regulations state that manufacturers of replacement and modification parts that will be installed on a type-certificated product should have a PMA. The design of a PMA part and the already-approved design of corresponding OEM part are “exactly the same” (Doll 2010, p. 7).
ACO and MIDO
Responsible for approval of PMA applications is the FAA’s Aircraft Certification Office (ACO) and the Manufacturing Inspection District Office (MIDO). The ACO determines whether the part can provide the airworthiness standards. There are many ACO offices in various parts of the United States that provide services to PMA applicants. If the applicant’s part is too complicated and considered critical, then the local ACO will pass this on and coordinate the matter with the Certification Management ACO (CMACO) which is an agency much more authoritative and experienced on matters pertaining to airworthiness standards. On the other hand, the MIDO is the office responsible for auditing the manufacturing facility. The MIDO sees to it that the production and quality system can produce the part according to the approved design. (Doll 2010, p. 6)
Two prerequisites have to be made in order to attain approval:
- FAA has done an intensive review of the design of the part and that it is assured that the requirements of FAA regulations are met; and
- FAA examined how the part was produced or manufactured according to existing production quality system and it is convinced that there is an existing system that applies quality production according to FAA standards. (MARPA: economic outlook for the PMA marketplace 2011)
A PMA features design and production approved by the FAA for replacement parts. Design and production are two most important aspects of approval requests. The FAA’s guidelines on safety standards have to be met in the design stage. The production system should also satisfy FAA’s production standards. In case of third party manufacturers, the PMA can also be used using the two aspects of approval requests. (Azcué 2011, p. 1)
The manufacturer must prove that the part has the qualities of the original that it intends to replace. Parts that need modification can also use PMA and is applicable for supplemental type certificates (STC) holders. In case of articles used or installed in an aircraft, a PMA for replacement parts can be issued under a Technical Standard Order (TSO) certification for as long as the article is within the product’s type design, and the part is a replacement part for the product. The PMA can be changed for a minor modification but the product has to meet the required airworthiness. (U.S. Department of Transportation (Federal Aviation Administration): subj: parts manufacturer approval procedures 2008)
The design approval has to be based on the OEM design of a particular part. The FAA formulated three standards on the design approval:
- Identicality with an OEM design agreement – the OEM’s design is an approved design, therefore, the PMA applicant’s design that is identical to this design is already approved.
- Without an OEM design agreement – the applicant will have to prove that his part is identical with an OEM part.
- Tests and other methods – The applicant will have to prove through tests that his PMA part is identical or better than the originally approved part. (Doll 2010)
After the part has been tested whether it met the airworthiness standards, the next step is to determine the criticality of the part. Will the part fail and what will be the causes – are some of the underlying questions. After this test analysis, the results will be classified into three: critical, important, and not-critical or important. Most approved PMA parts are not considered critical or important. Other problems involving part complication, a more detailed plan is needed, such as a Project Specific Plan wherein testing is more rigorous and detailed. The procedures are costly for the applicant. Sometimes the applicant will need an OEM representative sample to be used as a benchmark. (Doll 2010)
A fabrication inspection system is also needed to provide assurance that the approved part has conformed to the design data and is now safe for use. The requirements for this system are the same as the OEM requirements. The requirements include: conformity of the materials to the design; processes that should conform to the required specifications; drawings should be available to FAA personnel; major design changes should be approved by the authorities; and many more. (Doll 2010)
Processing of application for PMA has been stringent and this is no surprise to PMA manufacturers who understand the requirements of airworthiness and reliability. Some PMA companies produced only non-critical parts, but others have made bold moves of producing critical and sophisticated parts to really compete with OEMs. (Doll 2010)
There are instances that PMA parts perform better since PMA manufacturers now have access to the latest technology and information necessary to make state-of-the art aviation parts. So what airlines do is to go to PMA manufacturers in order to improve their cost-cutting measures. OEM manufacturers are therefore restrained to raise prices. This makes the competition advantageous to the aircraft industry. (Companies and markets.com: parts manufacturer approval (PMA) parts: a global strategic business report n.d.)
The FAA also worked with other regulatory bodies around the world in order to forge ties with respect to aircraft safety and production. The agreements that they have worked out include the Bilateral Aviation Safety Agreements (BASAs). The aim is to form a regulatory network which will focus on the airworthiness of aviation parts. In an agreement under the BASA treaty, both parties will respect the findings and certifications of either party. PMA approved parts can be sold and applied in the countries that have a BASA treaty. However, critical parts will have a separate study. (Doll 2010, p. 12)
The United States has signed a BASA with the European Aviation Safety Agency (EASA) of the European Union, and airworthiness authorities of the countries of Brazil and Argentina. BASA has helped in the settlement of fees. When an airline requires the use of PMA parts in another country, the regulations are provided in the State of Registry of that country. Sometimes, a host country will require the certificate of airworthiness of the PMA part in question or certification from the FAA that the part meets the FAA guidelines. (Doll 2010)
There are several BASAs the United States has signed with about 42 other nations. Approval for the use of PMA parts has been one of the relentless efforts of the government to support the replacement parts industry and this is to spread to other countries through Bilateral Aviation Safety Agreements (BASAs).
European Aviation Safety Agency (EASA)
The EASA is a legal and independent body created by the European Parliament and Council Regulation, whose objective is to provide a system for air safety.
The main tasks of the EASA are:
- To formulate laws and support Member States in the adoption of these laws;
- To assist in the monitoring process of those laws;
- To provide certification after thorough inspection and processes are done.
The agency conducts studies and provides knowhow on the subject of aviation safety and environmental preservation and protection. (De Florio 2006)
In Europe, manufacturers follow regulations formulated by the European Aviation Safety Agency. EASA established regulations on PMA parts which are quite stricter than the FAA regulations and procedures. These regulations are governed by certain principles which are:
- There are regulations for parts design and separate regulation for production;
- The manufacturer must show their design capability;
- Non-TC holder applicants should have coordination with and support from TC holders when major design changes are needed on the part;
- Designs made by non-TC holders are considered design change. (European Aviation Safety Agency 2009, paras. 3-6)
EASA has split the approval process into two, the production and design, in accordance with Regulation (EC) 1702/2003 Part 21. Production of parts by a company or organisation should have a corresponding Production Organisation Approval. The design process can be a part designed by a TC holder, or if there is an ETSO authorization, and lastly if it is a recognized standard part. (European Aviation Safety Agency: preliminary regulatory impact assessment 2009, paras. 8-9)
Replacement parts by a non-TC holder which carries a major change in design must have a Design Organisation Approval (DOA). This should be coordinated with the TC holder unless the applicant can show that the design can stand on its own, and the applicant must be able to show that the change is not significant. Parts designed by a non-TC holder should be marked EPA (European Part Approval). This is equivalent to U.S. parts marked PMA.
The European Aviation Safety Agency has reservations over the U.S. PMA system, arguing in its publication that it does not ensure the airworthiness requirements. In comparing the two systems, the EASA (EPA) and FAA (PMA), there is conceived strictness (for EASA) and laxity (for FAA) in the regulations and enforcement of their procedures. The EASA demands design capability of the manufacturer while FAA does not demand the design. In 2006, FAA made attempts to correct the discrepancies or differences so that Europe and US can almost have the same procedures when it comes to parts approval. (European Aviation Safety Agency: preliminary regulatory impact assessment 2009, paras. 8-9)
The EASA approved some parts under the PMA system on some conditions: the part is certified that it is not a “critical component”; the part conforms to some design specifications of a license; and the PMA holder can prove that the part is approved by the Agency. (European Aviation Safety Agency: decision no 2007/003/C of the executive director of the Agency 2007)
In issuing the guidance, EASA gave its approval for PMA parts but some conditions have to be met, such as, regulations for design and production have to be distinct; design capability should be clearly stated; and, a replacement part being held by someone who is not a TC holder is already considered a change in the particular part. (Dickstein 2009, para. 2)
Inventory Locator Service (ILS)
Inventory Locator Service aids organisations and firms through the electronic market. It provides a database of buyers and sellers in the replacement parts industry. Replacement parts manufacturer, MRO shops, and firms involved in repair and maintenance of aircraft of various types and approved by the FAA, are included in the list. (Doll 2010, p. 35)
Information ranges from shop availability, prices offered, and other vital information. The list or database is ongoing and any new information is added. If someone wants to transact with the firms listed in the ILS, the customer has to transact business directly with the firm and not through the ILS. Traffic for business and individual transactions has reached 20,000 a day. Line items in the database are estimated at thirty-one million and users range from 3,000 and more. (Doll 2010, p. 35)
ILS however targets the surplus sector and policing for this kind of market is believed difficult despite FAA’s requirements on the use of appropriate tags. Surplus parts come from OEM firms, therefore there is an assurance of quality because the parts are original that come from retired aircraft that had been “cannibalized’. AOG buyers that are in a hurry to get their needed original part when such part is not available from the OEM will usually go to ILS. (Choudhury & Konsynski 1998)
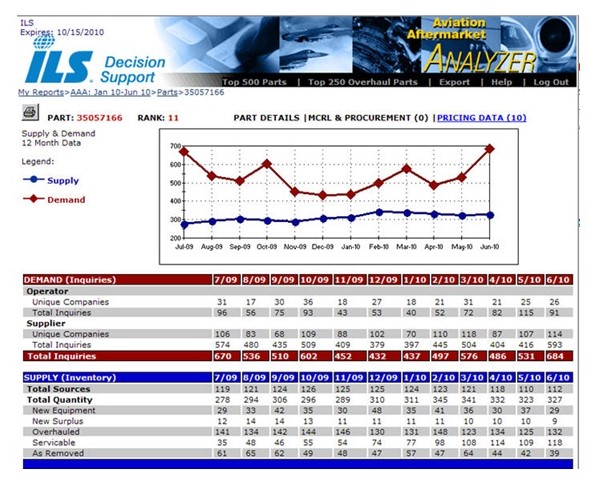
This ILS tool provides access to a database of parts currently in demand by customers in the aviation market. The tool provides a graph (as shown above) which leads the customer to identify market trends. The information for the Analyzer is constantly checked and updated by ILS administrator.‘ After Market Analyzer’ is important for customers who are involved in the replacement parts market.
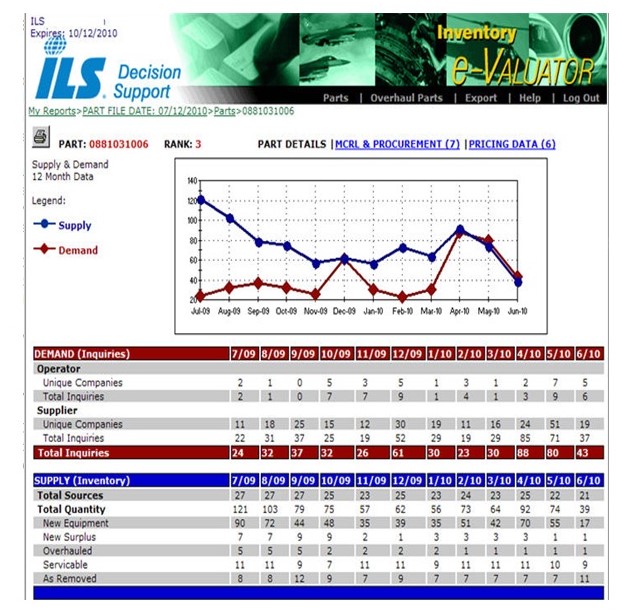
This Inventory Analyzer enables the customer to analyze replacement parts currently in use by the customer’s company. Information on supply, demand and prices is provided by the website’s database and the customer can analyze the market. Information is also constantly updated.
The Monopoly
Monopoly arises when there is no competition. This is true with any industry and the airline industry is no exception. Airlines need replacement parts for engines. Automobiles and equipments newly introduced in the market had the same problem. Replacement parts solely came from OEM companies, although as stated, most of these parts were outsourced parts and not manufactured in-house by OEM companies. They had a monopoly for what is called aftermarket. OEMs set the prices and airlines could do nothing.
Without PMAs, OEM manufacturers had the exclusive right and role in the aircraft aftermarket. Airlines were complaining of the high cost of maintenance. The industry has been struggling because of world economic pressure, the outbreak of bird flu epidemic and several other natural calamities that affected world travel and tourism. Any disturbance affects world travel and the airline industry. (Doll 2010, p. 2)
HEICO co-president Eric Mendelson says that OEM pricing has been perceived “abusive”. Because of their “abusive aftermarket pricing practices”, airlines have been asking PMA companies to develop parts in order to create competition against OEM. (Holland, 2008, p. 54)
According to the consulting firm AeroStrategy, aircraft maintenance accumulates about 9.4 percent of an airline’s expenditures, and of this, approximately 35 to 40 percent go to parts, with engines and components representing 56% and 27%, respectively. In 2005, the parts expenditure represented $15 billion, with PMA parts taking a 3% share. (Jensen 2006, para. 5)
As an aircraft goes to maintenance, the cost of maintenance has to be reduced. AeroStrategy said that in 2009, the airline industry spent about $17 billion on spare parts. PMA has considerably reduced the costs. A leading PMA supplier had said that a customer can save as much as $130,000 on an engine overhaul using PMA replacement parts. Another US airline reported a saving of $40 million in materials. (Doll 2010, p. 2)
Purchases of replacement parts come from airlines which anticipate their routine or periodic MRO and from AOG or aircraft on ground. About 20% of purchases come from emergency purchases. OEMs and their distributors sell new replacement parts. When the PMA system emerged, PMA companies competed with their new PMA parts, subjected to FAA procedures. (Doll 2010, p. 5)
OEM parts are the original parts from equipment in an aircraft, which are issued with a corresponding TCDS. A brand new engine for example is made up of OEM parts and other outsourced items and materials. As time goes by and with constant use, some parts in the machine have to be replaced. MRO shops have two options in replacing the old part: OEM or PMA part. The PMA system provides an FAA-approved replacement part. (Lombardo 1999, p. 70)
Before the PMA system, OEM had a monopoly for prices of individual engines. Price increases for various parts in aviation ranged from 3-6% annually. Airlines challenged the monopoly by urging manufacturers to fabricate replacement parts which are considered cost drivers. (Azcué 2011)
The OEM monopoly was exacerbated by stringent rules and guidelines coming from the government and FAA. In Europe, it was perceived more stringent with EASA’s guidelines that considered FAA’s regulations too lenient. Moreover, OEM manufacturers continued to make moves that were considered “anti-PMA” by providing information about strict airworthiness guidelines in their publications. (Azcué 2011, p. 2)
Lufthansa Technik was the first to challenge the monopoly to reverse engineer the parts which were even better than the original. In 1997, Lufthansa Technik owned a 20% stake in the company HEICO Arospace which began to manufacture engine parts. Prices for engine parts started to fall by as much as 30-50%. This time, the monopoly was challenged. (Henningsen 2010, p. 50)
Globalization also emerged as a savior. MRO focused on engine overhaul with some outsourcing techniques. Shops were established to challenge material costs. Manufacturing was done on a centralized basis but with shops in some parts of Asia like Manila and Australia. Transportation and shipping were kept at the minimum but man-hour for manufacturing was still intensive. Overhaul of some engine parts needed more man hours and so Lufthansa made a joint venture with MTU, a German company. Engines were sold with different PMA parts manufactured. Other companies and manufacturers were formed which produced low-cost replacement parts. (Henningsen 2010, p. 50)
With the airline industry’s continued patronage over PMA parts, OEMs seemed to mellow down their attack on PMA manufacturers. Their anti-PMA campaign became fruitless because of the support from various airlines that have experienced benefits from PMA use. But it has been clearly perceived that the issue really boiled down to economics as OEMs consider the parts industry as their aftermarket. (Doll 2010, p. 10)
OEM versus PMA
The controversy continues but either camp claimed victory. The battle lines, though clear in the eyes of the airline and MRO industries, are getting blurred because of the continuous attacking statements on the quality and validity of certain parts.
The question as to why should an airline company choose PMA over OEM has been answered by the opposing organisations. PMA parts manufacturers argue that their parts should be chosen as replacement because PMA parts are low cost and offer the same quality and service if not better than the original. OEM companies, on the other hand, argue that PMA manufacturers do not have enough research and development for their products – they just copy and that is all. This puts the safety and reliability into question.
OEMs also said that the FAA is too lenient or not strict in their approval processes to the PMAs yet too strict to the OEMs. OEMs complain that when their products have PMA parts and malfunction during operation, it is they the OEMs who get the blame and sued along the way. (Doll 2010, p. 5)
Additionally, according to OEMs, lessors are not yet amenable to using PMA parts. While there are some areas that seem to be true, PMAs do not accept it and argue otherwise. Jason Dickstein of MARPA disagrees. He said that lessors (or the leasing community) have all been accepting and “embracing” the PMA system and the parts it produces. Airlines should be one with the lessor statement that PMAs are acceptable and good as the original. Dickstein further said that if lessors and airlines agree, there is what he calls a “win-win” situation. And even OEMs can agree with it. (Holland 2008, p. 50)
Nevertheless, the FAA is quick to add that a PMA part with corresponding FAA-approved marks is as good as the original and can be applied on an OEM product. (Lombardo 1999)
Jeff Dark of Jet Parts Engineering (cited in Holland 2008) argued that OEMs have been trying to portray that airline companies do not want to sign lease agreements on aircrafts that use PMA parts, therefore lessors do not want to use PMAs. In this case, lessors use the lease agreement against PMAs. But some operators are PMA friendly who insist on using PMA replacement parts.
Others are more persistent and argumentative, like for example BELAC president Chong Yi, who says that lessors would like to add PMA parts into their array of useful and quality replacement parts. Engine fleets being used by lessors include the CF6 and PW4000. Yi further adds that lessors praise these mature engines and they hear positive comments from operators who do not want to spend too much money for parts that are not reliable. There is a continuing number of worldwide operators who patronize the PMA system. Nevertheless, Howard says that the continued talk and patronage of the PMA systems is being done in the “exclusive” area of opinion among the powerful in the industry and not in the open. Those who are in the leasing company are not really open in their support of the PMA. This means it remains an open secret that the higher ups in the leasing community support the use of PMA. OEMs do not want to take the matter into long discussions. They say that using PMA is a question of value loss or engine valuation. There might be immediate benefits such as cost savings but the question is on the value of the engine in the future. (Howard 2008)
Moreover, FAA support and information campaign conducted on the industry and the general public, the mind set on PMA is that it is an integral part of an engine and therefore it is not anymore an issue. PMA parts and suppliers are not anymore the subject of controversy. (Howard 2008)
So the attack comes from both sides although the aggressive part comes from OEMs. According to Andy Shields, Vice President of PMA at Wencor, the question is not in the context of safety of using PMA parts, but has changed to pure commercial strategy. Shields argued that OEMs are attempting to aggressively re-take the hold of the monopoly. Their reaction to the popularity of the PMA is so strong that they have made tactics to fight the competition. OEM tactics include withholding component maintenance manuals (CMMs) and information on Instructions for Continued Airworthiness (ICA). (Holland 2008, p. 53)
Other manipulative tactics include the issuance of memorandum warning OEMs not to use FAA-PMA parts. Dark and Mendelson have asked airlines to be courageous in their transactions against the OEMs who try to control them; rather they should be the ones to control the OEMs. Mendelson further said that OEMs also deserve respect in the kind of engines they make, but OEMs made the new technology because they wanted to control or monopolize the parts industry. The real profits come from the MRO and controlling the supply would allow the OEMs the monopoly they always wanted to take hold. (Howard 2008)
Additional cost to airlines is the tactic by OEMs which is known as the “power by the hour” tactic. An OEM maintenance facility refuses to reassemble PMA parts back into an engine so the customer has to buy OEM original parts. Power by the hour maintenance plan forces the customer to pay on “time and material basis” to the maintenance shop, which adds costs to maintenance and generates more profit to OEMs. (Doll 2010, p. 16)
PMA companies charged back that OEMs have resorted to scare tactic, that once aircraft owners use PMA replacement parts on their engines, the warranty becomes voided. Larry Shiembob, CEO of EXTEX, said that this is one of the scare tactics that portrays the quality and reliability of PMA. The PMA is a threat to the OEM parts and its aftermarket. (Stephens 2008, para. 11)
With respect to quality, the PMA can speak for itself, according to PMA manufacturers. The PMA program requires synchronized actions of several departments to include supply, engineering, quality management, purchasing, and so on. Supply needs to focus on effective supply chain. Purchasing will have to focus on the business side of the program. Engineering needs constant reviews on the quality of PMA design. Quality assurance will have to look on the supplier’s methods. All of these departments have to work together but should ensure that the work in each department is not delayed and hindered by internal factors. (Doll 2010, p. 21)
Costs of PMA parts
As discussed in previous sections, the costs for PMA parts are relatively lower than OEM parts. And this is precisely the reason why PMA is more popular than the original. PMA parts can cost up to 50% lower than OEM. (Doll 2010)
Safety and performance are almost the same, perhaps even better than the original. But the PMA parts market is vulnerable to recession considering that during recession, airlines have the tendency of repairing their aircrafts instead of buying new ones. The 2009 recession sent ripple effects not only on the main industry but also on the aftermarket, the parts industry. (Companies and markets.com: parts manufacturer approval (PMA) parts: a global strategic business report n.d.)
Economic considerations are turned on the debate that PMA parts offer short-term benefits while OEMs are for long-term gains. There are contracts in the airline industry that do not recognize the use of PMA parts. The reason is to protect “liquidity and marketability in the industry”. Other contracts perpetrated by OEMs have excluded the use of PMA parts, precisely to preserve engine value and other OEM anti-PMA measures. OEMs continue to state that using their parts will create economic benefits in the long run. (Holland 2008, p. 54)
The PMA continues to be popular. As of 2009, there have been 300,000 approved PMA parts. The number is increasing year by year as there more applications being requested by PMA manufacturers. There is an estimated 35,000 parts increase annually. (PMA parts: the market & major suppliers 2009, p. 32)
Reliability of PMA Parts
In engine maintenance, replacing parts with bad material is like poisoning the fleet. The question is: is PMA a bad material? David Doll answered with a resounding ‘No’. The approval process tells that PMA parts are reliable and safe. (Doll 2010, p. 25)
The performance of the approved PMA parts can attest to the airworthiness of the parts. In 1992, PMA approval significantly increased. And how PMA competes with OEM parts can be determined through the Airworthiness Directives issued by FAA. David Doll did this and found that of the 287 Airworthiness Directives for turbine engines issued, only three were attributed to PMA parts and 286 were for the OEMs. (Doll 2010, p. 8)
Of the three PMA parts which received ADs, they were found to be clones of OEM designs which experienced the same problem. One PMA part was found to be the cause of a helicopter accident but this part was also a clone of another OEM which experienced the same mechanical problem. (Doll 2010, p. 10)
The continued oppositions and lobbying of OEMs who have always said that PMA is not safe prompted a study known as the FAA Repair, Alteration and Fabrication (RAF) Study. This was conducted in 2008 which aimed to conduct a review of the process, regulations and practices on the conduct of applications and approvals of replacement parts. The result of the investigation is that there was no evidence of failure or unsafe conditions in the processes and that PMA applications that resulted into parts applied in repairs and alterations, had increased substantially but there were less service difficulties and airworthiness directives caused by the parts. (Doll 2010)
The question of quality and reliability has been answered by the FAA itself. Their stringent approval procedures before a part is approved for manufacturing are proof enough that what comes out are quality-oriented replacement parts, the ones that can withstand intense vibration and heat when an aircraft is in the air. PMA parts quality is not anymore a question because in general, once an application is approved, quality goes with it. OEM continues to question the safety requirements of PMA replacement parts. (Azcué 2011, p. 2)
Quality assurance checks reliability of PMA parts. Airlines are well versed when it comes to quality assurance. Airlines have expert people to inspect the quality of people conducting the maintenance. The quality assurance people are busy all the time conducting audit on maintenance suppliers. (Doll 2010, p. 26)
Outsourcing Maintenance
Some companies outsource their maintenance requirements as a strategy to avoid the small details of material procurement. But there are disadvantages to this kind of strategy. OEMs also have some sort of control on maintenance and they can avoid PMA parts in the process. Airlines have a wider marketplace; they also have the aftermarket, an additional source of income, which includes the MRO. But some airlines outsource this stage of the aftermarket. (Doll 2010)
Outsourcing is not new. It is a strategy in business that continues to dominate business functions all throughout the world. With globalisation and the continuing changes in technological advances, extensive development is going on in business and organisations. The primary aim of outsourcing is to reduce costs, the same as putting spare parts in an OEM engine. One benefit of outsourcing maintenance is that the airline does not need to worry about the materials needed if only the MRO organisation follows the guidelines and contents of the contract. Outsourcing has been practiced by firms throughout the world. It’s only now that we feel its presence. Outsourcing has become a necessity by many firms because of the tendency of firms to grow horizontally and vertically. (Eltschinger 2007)
The problem with outsourcing maintenance is that OEMs do not accept PMA into outsourcing shops. Then again, OEMs do their usual scare tactics, that shops have to get away with PMA parts. (Doll 2010)
PMA Experiences of Airlines and Organisations: The Stakeholders
MARPA
MARPA is the acronym for Modification and Replacement Parts Association, an organisation of manufacturers, providers and organisations with stake in the PMA business. Its primary mission is to promote quality standards of the PMA system and helps PMA suppliers. It works with regulatory bodies and other government agencies on the promotion of the PMA system. It worked with the FAA in formulating the Continuing Operational Safety regulations. (Doll 2010, p. 28)
MARPA’s annual conference is held annually every October and here PMA suppliers meet and consult with problems pertaining to the industry. David Linebaugh of Delta Airlines chairs the airline committee whose job is to have a close relationship between PMA suppliers and airlines. (Doll 2010, p. 28)
Chinese Air Carriers
There are 80 carriers in China and most of these carriers have expressed the benefits they experienced on the reliability and savings by introducing PMA parts in their aircraft. Feng Xiabao of Hainan Airlines expressed confidence on PMA along with Jason Wang of China Southern who said that they have no more doubts about the PMA. The Chinese airline operators have now focused on product support mechanisms on PMA manufacturers. (Dickstein 2010)
PMA parts have become popular among MRO shops in Northeast China. The CFM-56-5C replacement parts were reported to have increased performance for engines. It was remarkable on a CF6-80 engine. (Dickstein 2010)
Delta Airlines
David Linebaugh of Delta Airlines has positive comments for PMA manufacturers, saying that PMA companies are open to improvements of increasing safety and reliability. PMA parts are not hard to find, in contrast to OEM which has always been unavailable and cannot even meet Delta’s needs and specifications. Linebaugh says that his focus is if the part works. (Dickstein 2011)
At Delta, the part application should have an introduction and description as to what it is and what it does. When changes are made to the OEM design, a clear explanation should be provided. The part is subjected to a series of questions by the airline. Linebaugh explains that there are rejections for some applications and one of the major reasons is eligibility. The design process is very important for PMA, the reason why Linebaugh of Delta and many other airlines adhere to PMA. (Dickstein 2011)
Seginus Inc.
Seginus Inc. is a manufacturer of FAA approved PMA parts, the latest approved have been starter generators, landing generators, carbon brushes, aircraft bearings, and a host of 200 parts in development. They also manufacture military helicopter components and their on-sale displays include bearings. Seginus approved parts are also used in various industries. In its website, Seginus states that it delivers quality parts on time and its mission is to manufacture PMA parts at a very low but competitive price. (Seginus: Seginus Inc. announces FAA approval of their latest PMA parts 2011)
About 300 of the company’s PMA products are still under development. Sophisticated ones are manufactured with the strictest guidelines from the FAA. This includes turboprop variants and other military components. Seginus insiders said that they see the potential of supplying PMA parts to the military. The company’s mission is to supply the world of aviation with the highest quality replacement parts at the lowest cost. (Seginus: Seginus Inc. announces FAA approval of their latest PMA parts 2011)
Shown in Appendix A is the “Seginus Parts List for OEM and PMA parts”. The saving that an airline company gains in buying a PMA part in lieu of an OEM part is about 30 percent. The common percentage difference between the two prices is 30%.
HEICO Corporation
HEICO is a corporation that provides low-cost products and services to civil and military aircraft. It is still considered a “small” company, having been considered one of the “Best Small Companies” by Forbes magazine. The parts are for industrial turbines, targeting systems and even missiles. HEICO’s Flight Support Group is the one responsible for the manufacture and distribution of FAA-approved parts for engines and other parts of an aircraft. Lufthansa Technik has a 20% stake over Flight Support Group. As mentioned earlier, Lufthansa Technik is one of the pioneers in the PMA parts manufacturing when the company sensed the ‘abusive pricing’ of OEMs. (HEICO: company profile n.d.)
The company is also proud to announce that their quality performance boasts of 44,161,164 parts sold since 1985 and since then there has been no service bulletins, Airworthiness Directives or shutdowns that have been issued against their parts. This means quality and reliability of their products are not an issue. Performance is the evidence that PMA can be relied upon. (HEICO: HEICO parts group n.d.)
PMA Parts made by HEICO
HEICO has a record of 5,000 PMAs and produces about 400 quality new PMA parts. Its laboratory is based in Hollywood equipped with state-of-the-art laboratory equipment producing replacement parts needed by the airline industry. Their products are of different designs, FAA approved, and range from nuts and bolts to bearings and other interior parts of an engine. The engine parts include CFM56, CF6, CF34, PW2000, PW4000, V2500, and more. They also have accessories for aircraft which include ACMs, batteries and battery packs, and so forth. (HEICO: HEICO PMAs n.d.)
When it comes to publications and instructional manuals, HEICO has papers on Instructions for Continued Airworthiness for PMA parts. This means the company is concerned with the product and its future performance. All these are part of the FAA guidelines to inform the customer about all aspects of the product. An example of this is Technical Instruction HAC 10-002, which is about PMA parts.
The Technical Instruction (TI), which is FAA-approved, contains information about the parts, eligibility and installation and how they can be used as replacement.
The TI HAC 10-002 refers to the Continued Airworthiness of PMA part P/N KT43-1276 Bolt. This FAA approved part is a replacement for an OEM manufactured part P/N 43-1276 which was installed on Boeing 757-200, 757-200PF, 757-200CB, 757-300 Series Aircraft. The original part has been documented with an extensive failure history.
The manufacturer of PMA part P/N KT43-1276 Bolt is Turbine Kinetics, Inc. which introduced a material change in the product from low-alloy steel to “Inconel 718”, an FAA approved as per Advisory Circular AC20-127, issued in July 8, 1987, which states the failure rate of low-alloy steel and instructs to replace it with Inconel 718 or stainless steel bolt. The introduction of this new material has made the PMA replacement better than OEM.
The TI HAC 10-002 details the installation locations of the PMA part on the wheel assembly of the Boeing aircraft. The TI further certifies that the Airworthiness Limitations for the OEM part are valid for the PMA part numbered P/N KT43-1276 with the exception on the life-limited part aspect of the PMA replacement.
The last part of the TI is an instruction for visual inspection and nondestructive test inspection. It instructs to have an inspection on all areas of the bolt and eliminate defective ones. Ultrasonic inspection should be done on each bolt. The details are further explained in HEICO’s website. (HEICO: technical instruction HAC 10-002 rev. N/C, Jan 13, 2010)
Interview with Mr. Jeremy Flaherty, Strategic Contract Manager, HEICO Aero Parts Group, c/o British Airways
Mr. Flaherty emphasized ‘identicality’ in the manufacture of PMA parts. A manufacturer has to prove that a PMA is identical through design, drawings, material and production.
A PMA manufacturer has to have access to information on the original part, provide the drawings and the design. A manufacturer should understand the product, design it, and it must be well-engineered. To provide identicality, one has to get hold of the original part, study, produce the drawing, and an engineering representative or consultant should examine it and indorse the requirements for FAA approval.
A license PMA manufacturer has to show the “face, form and function”. “The face” means the part has the shape of the original and it can function just like the original. Mr. Flaherty says that a PMA manufacturer can’t change the material unless Airworthiness Directives dictate to do so for reasons of failure rate.
Millions of PMA parts are shipped throughout the world. Independent PMAs have license from FAA, and they also have permission from OEMs.
When a manufacturer has a customer, an airline for example, the customer has to approve the parts. But Mr. Flaherty says that if a customer wants a product made, it should follow the face-form-and-function principle.
Mr. Flaherty narrated his knowledge of the beginnings of the PMA. He said the PMA was mistaken as bogus or fake. But the PMA has proven its reputation. A manufacturer has got to have a reputation in introducing the part. If a PMA manufacturer changes the original, he must be responsible for it.
Mr. Flaherty says that there are now a number of airlines using PMA parts because if they don’t use PMA parts, their airplanes wouldn’t fly.
Mr. Flaherty made mention of the United States bilateral agreement with other countries particularly the EASA of the European Union. The EASA does not want critical parts but in the United States, critical parts are admitted. Other bilateral agreements are with China and some countries in the Middle East. They have several strategic places in the world where they ship millions of PMA parts, but they have no existing partnerships. As to reliability, he says that when it cracks, it’s because of the material, for example the alloy which has to be changed. Changes have to be FAA approved.
Mr. Flaherty showed to this interviewer some potential PMA parts and their important characteristics. Their company can provide 20-30% discount, much lower than the OEM price. They have existing partnership with engineering and manufacturing companies that produce good if not better replacement parts than the original OEM parts. They also have the ability to drop down costs.
According to Mr. Flaherty, OEMs are making good money from the aftermarket sales. They are blaming the PMAs for their low sales in the MROs. PMA companies sell cheaper parts that are reliable and with quality and are much better than the original OEM parts.
Now OEMs have resorted to scare tactics and have kept information about original parts. They have spread myths that when it’s not OEM, it’s not good. But PMAs have done much product improvement on the face, form and function. Statistically, they have made PMA parts more reliable than the OEMs.
AEROSUP Inc.
AEROSUP Inc. is a company that delivers low-priced high-quality parts that follow PMA guidelines. AEROSUP is a distributor which has contact with many distributors and MRO shops around the world. It also adheres to quality and follows the standards set by FAA. In its website, AEROSUP says that their primary goal is to help customers (airline owners and operators) reduce maintenance cost at the same time acquire high-quality aviation parts. (AEROSUP: FAA PMA aircraft parts distributor 2009)
Great Lakes Aero Products, Inc. (GLAP)
Great Lakes Aero Products started its humble beginnings in 1973 at Benton Harbor, Ml. when its founder, John Zofko Jr., purchased Aircraft Components, a company which initially manufactured aircraft windshields and windows. John was employed as an engineer with General Motors but later resigned and concentrated on improving the company. In 1993, the company incorporated its name to Great Lakes Aero Products, Inc., now the world’s leading manufacturer of stringent lens, wing tip landing light lens and tail cone lens. (Great Lakes Aero Products, Inc.: history n.d.)
Products of Great Lakes Aero are FAA-approved which comply with the PMA replacement parts system. Windshields and windows are carefully designed, properly and legally documented, and described and contained with an appropriate PMA &STC information manual. PMA parts are shipped with corresponding insurance coverage.
Appendix D is a price comparison of two companies: Great Lakes Aero Products, Inc. which sells PMA parts, and Hawker Beechcraft which is an OEM company.
From the parts list, we can see a great discrepancy. Let’s take one part after another; for example, the first item, a Sun-visor is sold at $508.34 by Beechcraft, but a PMA counterpart for this being sold by Great Lakes Aero Products is just worth $54. The discrepancy is so big that a customer can gain a saving of $454.34 (89.4%). The second item is a windshield with lenses which costs $2,131.11 from Beechcraft but only costs $494 from GLAP or savings of $1,637.11, equivalent to $76.8%. The sixth item, a rear window, provides 93%, or $1,532, savings for the customer. The comparison provides a big difference between OEM and PMA prices for windows with lenses.
GLAP’s products are manufactured in-house and not outsourced – they make their own products which are all FAA-approved and follow the PMA replacement system of approval. Quality is assured and warranties are issued for all GLAP products and can be returned, except for some parts, like the custom trimmed parts, which cannot be returned.
Disadvantages of using PMA Parts: Favoring OEMs
There has been a common misconception that OEMs (Original Equipment Manufacturers) are manufacturers of new aircraft or engine. David Doll, who has spent 40 years in the airline industry particularly in engine maintenance, is candid about it: OEMs never manufacture the products they sell. (Doll 2010, p. 1)
An aircraft or engine that an OEM sells is a combination of internal manufacturing and parts manufactured by external suppliers. OEMs use outsourcing as a way of obtaining finished products, such as engines, and this method allows them to be called system integrators instead of manufacturers. Another astonishing fact is that today’s PMA suppliers were once OEM suppliers. An OEM is not a legal entity and the corporation that proves the legality of the design and manufacturing system is the Type Certificate and Production Certificate holder. (Doll 2010, p. 5)
OEMs and their ‘defenders’ assert that although using PMA replacement parts provide savings for as much as 30-50 percent, as what PMA manufacturers argue, this does not translate into long term gains. By using OEM original parts, airlines can save money because of the quality and airworthiness that their parts can offer. This means by installing PMA replacement parts on an aircraft, it is subject to continuous maintenance and repair. But it is also a misconception that there would be loss of residual value on engines and blades when using PMA parts.
According to Charles Willis of Willis Lease Finance, the use of PMA engine parts would create a lesser valued engine. “There may be immediate cost savings but what about the value loss to the engine?” Willis was concerned that customers would not accept the technical aspect of using PMA parts on engines. (Holland 2008, p. 52)
OEMs have been pictured as the villain but defenders of OEM, like GE’s Conner, state that OEMs have been involved in the aftermarket such as engine services, for example product life-cycle cost of ownership, new parts manufacturing and subsequent delivery, maintenance and development including engine overhaul and repair. This OEM presence in the aftermarket is an answer to customer demands – customers have often looked to OEM manufacturers to deliver more value-added solutions to their engines. GE provided their ‘OnPoint’ solutions such as flexible overhaul and material solutions. GE also introduced risk transfer elements which referred to competitive maintenance services.
Conner says that PMA offered competitive OEM solutions which were coursed through airline-affiliated MRO providers. Connor explains: “This provides airlines more choices of non-OEM services providers who offer other unique value propositions (e.g. aircraft MRO, geographic proximity and relations, etc.).” (Holland 2008, p. 56)
PMA parts only cover about three percent of the amount used for maintenance and the disadvantage is that there are “long-held, internal approval processes” for PMA parts. The processes are conducted by the engineering and quality assurance departments that account for the delay. PMA parts have long, stricter procedures than OEM parts. Before PMA parts can be installed, it would take about 12.2 months, and validation period takes three years. (Jensen 2006, para. 7)
Another disadvantage is that PMA parts are not listed in the OEM catalogue, although companies that sell PMA parts have their websites that provide information regarding their products. Still, the easy way is OEM catalogues of parts available which airlines have easy access.
To analyze the advantages and disadvantages of the PMA system, it can be said here that the advantages far outweigh the disadvantages. Strong supporters of the PMA even state that there are no disadvantages as the PMA has truly helped airlines in their cost-cutting measures and has lifted the spirit of the industry because one of the worst problems of the industry has been solved, the maintenance cost.
Every now and then, an aircraft particularly its engine has to go to the shop for maintenance. Parts have to be replaced; operations have to be disturbed. And the high cost of replacement parts for engines and other parts in an aircraft has been under control, or under monopoly of a few organisations. When the PMA came, it was like the industry welcomed a savior.
Conclusion
A new phenomenon about the PMA popularity is the emergence of replacement parts in large numbers. Airlines can now shop for the best PMA that manufacturers can offer, and at low cost. This new phenomenon carries with it a new industry and a series of activities. For example, regulatory agencies such as the FAA, the EASA, and other government agencies in other countries, have to strengthen their regulations and procedures to respond to commercial and private pressures; supply chain has to be improved and new companies/suppliers might emerge; and many other issues have to be addressed.
The demand for PMA parts continues. The trend has been going on in many countries and goes as far as Southeast Asia, Europe and South America. Airlines realize the benefits of PMA replacement parts through cost savings and the services derived.
The recent recession has had a profound effect on industries, particularly the airline industry. Aircraft owners and operators have to acquire savings; they can’t afford to continuously apply MROs with very high cost genuine parts. The PMA system and the parts and services it offered have helped the airline industry in recovering the losses as a result of the many disturbances in the industry. PMA parts for almost every aspect of an aircraft are available in the market. Traditionally, it was not so because PMA parts were only focused on engine parts provided by OEMs. (Azcué 2011, p. 3)
The Department of Defense also patronizes PMA replacement parts. The U.S. Air Force is one of those that has supported the PMA industry and has made it even successful. U.S. military aircraft use PMA parts. Twenty-nine percent of aircrafts flying over U.S. air space belongs to the U.S. Air Force. The use of PMA parts by the Air Force has greatly reduced the Air Force’s spending for maintenance, repair and overhaul (MRO). (Stephens 2008, para. 38)
Aircraft owners and operators especially airline carriers prefer PMA over OEM parts because of the following:
- Very low cost but quality and airworthiness do not change, in fact, even better
- PMA is FAA-approved system particularly on safety and airworthiness
- Production follows FAA guidelines pertaining to the approved design
- PMA parts are always available
- PMA manufacturers are open to improvement and correction from perceived flaws. (Holland, 2008)
As much as possible however, PMA manufacturers strictly follow FAA guidelines in order to avoid these flaws.
The OEM companies were shock of the PMA phenomenon that they reacted with their countermeasures. At first, they had the monopoly. Now, they receive stiff competition from competitors, some of whom were their very own co-OEMs. OEMs instituted aggressive measures to defend one of the sources for their revenues and ensuing conflict resulted into debates over the reliability of PMA parts, and the scare tactics issued by the OEMs themselves against the PMA companies.
To recap what has been discussed in this paper, there are no doubts that PMA replacement parts now popular in the market and patronized and bought by most airlines and MRO shops are much lower in cost compared to the original OEM parts. The comparison of OEM and PMA parts can make us conclude that making PMA parts items inside the OEM engines is more than acceptable. Performance of PMAs has surpassed past performances of OEMs. Quality and reliability cannot be questioned. Advantages are more than disadvantages. Cost of PMA parts are much lower than OEMs. Finally, this is a big help to airlines in their cost-cutting measures considering the intense globalisation, terrorism, pandemics and natural disasters that have hampered global travel and tourism.
References
AEROSUP: blog (n.d.) 2012, Web.
AEROSUP: FAA PMA aircraft parts distributor (2009) Web.
Ambrose, M. (n.d.) PMA: the European perspective, European Regions Airline Association, Web.
AV Buyer: bogus parts: are they still a problem for business aviation (2009) Web.
Azcué, S, (2011) Parts manufacturer approval: a debate on non-original manufacturer parts and this expanding market, Web.
Choudhury, V. & Konsynski, B. (1998) “Inter-organizational information systems and the role of intermediaries in marketing channels: a study of two industries”, in C. Kemerer (ed.), Information technology and industrial competitiveness, how IT shapes competition, Kluwer Academic Publishers, Massachusetts, pp. 67-80.
Code of Federal Regulations (1999) Office of the Federal Register, National Archives and Records Administration, United States of America.
Companies and markets.com: parts manufacturer approval (PMA) parts: a global strategic business report (n.d.) Web.
De Florio, F. (2006) Airworthiness: an introduction to aircraft certification: a guide to understanding JAA, EASA, and FAA standards, Elsevier Ltd., Burlington, MA.
Dickstein, J. (2009) EASA considers promoting replacement part manufacturing in Europe, Web.
Dickstein, J. (2010) Chinese air carriers discuss their positive experiences with PMA, Web.
Dickstein, J. (2011) Getting your PMA parts into Delta, Web.
Doll, D. (2005) PMA 2005 – the industry matures, Web.
Doll, D. (2010) The airline guide to PMA, Web.
Eltschinger, C. (2007) Source code China: the new global hub of IT (information technology) outsourcing, John Wiley & Sons, Inc., New Jersey.
European Aviation Safety Agency: decision no 2007/003/C of the executive director of the Agency (2007).
European Aviation Safety Agency: preliminary regulatory impact assessment (2009).
FAA Aircraft Certification Service: special airworthiness information bulletin (2008) SAIB: NE-09-40. Web.
Federation Aviation Administration: parts manufacturer approval (PMA) (2011) Web.
Great Lakes Aero Products, Inc.: history n.d., 2012, Web.
Henningsen, A. (2010) Globalization for growth in the aviation maintenance repair and overhaul industry, in R Ijioui, H Emmerich, M Ceyp & J Hagen (eds.), Globalization 2.0: a roadmap to the future from leading minds, Springer, Germany.
HEICO: company profile( n.d.) 2012, .
HEICO:HEICO parts group (n.d.) 2012.
HEICO: HEICO PMAs (n.d.) 2012.
HEICO: technical instruction HAC 10-002 rev. N/C, 2010, Web.
Holland, J. (2008) ‘What next for PMA parts?’ Aircraft Technology, Issue 114, pp. 50-56.
Jensen, D. (2006) Plotting the potential for PMA parts, Web.
Lombardo, D. (1999) Aircraft systems, McGraw-Hill, United States of America.
MARPA: economic outlook for the PMA marketplace (2011), Web.
MARPA.org: what is PMA? (2012) Web.
PMA parts: the market & major suppliers (2009) Web.
Seginus: Seginus Inc. announces FAA approval of their latest PMA parts (2011) Web.
Stephens, E. (2008) PMA vs. OEM: the business of getting (and keeping) customers, Web.
U.S. Department of Transportation FAA: advisory circular 2010, Web.
U.S. Department of Transportation (Federal Aviation Administration): subj: parts manufacturer approval procedures (2008) Web.
Appendices
Appendix A
Appendix B
Appendix C
List of Abbreviations/Acronyms
- AC – Advisory Circular (FAA)
- ACM – Air Cycle Machine
- ACO – Aircraft Certification Office
- AD – Airworthiness Directive
- BASA – Bilateral Aviation Safety Agreement
- CAA – Clean Air Act
- CAA – Civil Aviation Authority
- CAR – Civil Air Regulations
- CFR – Code of Federal Regulations
- EASA – European Aviation Safety Agency
- EC – European Commission
- EC – European Community
- EPA – European Parts Approval
- ERA – European Region Airlines Association
- ETSO – European Technical Standard Order
- EU – European Union
- FAA – Federal Aviation Administration
- FAR – Federal Aviation Regulations
- FS – Flight safety
- GDP – Gross Domestic Product
- GLAPIN – Great Lakes Aero Products, Inc.
- ICAN – International Commission for Air Navigation
- ICAO – International Civil Aviation Organization
- IEE – Institute of Electrical Engineers
- IEEE – Institute of Electrical & Electronic Engineers
- ILS – Inventor Locator Service
- JAA – Joint Aviation Authorities
- JV – Joint Venture
- MARPA – Modification and Replacement Parts Association
- MA – Merger and Acquisition
- MIDO – Manufacturing Inspection District Office
- MRO – Maintenance, Repair, Overhaul
- OEM – Original Equipment Manufacturer
- PMA – Parts Manufacturer Approval
- STC – Supplemental Type Certificate
- SUP – Suspected Unapproved Parts
- TC – Type Certificate
- TCDS – Type Certificate Data Sheet
- TSOA – Technical Standard Order Authorization