Introduction
Composite materials are typically made of more than one element with different chemical or physical properties. Combining these materials helps bring out new tackles with different features separate from the individual component. However, it is essential to realize that the two materials that make composite structures must not melt each other. Composite structures have been used in the airplane industry since the 1960s, following fiber development with high molecular weight. In this case, carbon fibers helped improve the thermoset stiffness to mass ratio, hence opening room for more applications in aerospace (Moors et al., 2019). This paper evaluates how composite wing spars on business aircraft can enhance wing performances and other costs towards maintenance. In addition, the paper gives a clear description of the general sustainability of the environment towards composite wings, especially during maintenance.
Composite Materials effect on Wing Performance and Cost during Maintenance
To start, it is crucial to understand that weight is one of the significant factors worthy of consideration for machines that are heavier than air. With this consideration, most designers have made necessary attempts to improve the weight-to-lift ratio from the first take to the air (Moors et al., 2019). In this regard, composite materials have played a significant role in weight reduction. Today, three critical types are used: grass, carbon fiber, and reinforced epoxy.
Considering composite as versatile materials, they are used for structural and component applications. This is standard practice evidenced in all spacecraft and aircraft. The different types specified above have different mechanical properties that enable them to be used in various areas of aircraft construction (Moors et al., 2019). For instance, carbon fiber is known for its unique lethargy behavior, making it less predictable. Generally, carbon fiber, one of the composite materials alloys, is the most widely used element in aerospace applications.
Recently, the airplane market has experienced a significant advancement that aims at helping it to reduce costs, and proper endurance to huge loads, alongside enhanced security. This is due to the orientation of composite materials’ multifunctional and novel elements. In the modern airplane industry, composite parts are considered 20-50% lighter than their competing versions (Moors et al., 2019). In this regard, it is essential to realize that composites typically appear stiff and more robust yet relatively light in weight. Its weight-to-strength ratio is considered many times higher than aluminum or steel (Wunderlich et al., 2021). The preference of composite materials for use in airplane wings is a result of their specific advantageous features, which include:
- Considerable specific stiffness and strength; longer fatigue span.
- Increased creep resistance.
- Resistance to wear.
- Enhanced rust resistance.
- Thermal conductivity and density.
Wings made from composite materials are some of the most crucial parts of the airplane, which help in providing support and lift to the entire weight of the aircraft as well as its content. The wings also consist of flaps, which refer to the movable parts of an airplane moving in the same direction, enabling the plane to make a slow movement.
The increase in the composite material application is pegged on specific material features, which resonates from strength, lightweight, few parts, and high stiffness. In this case, the composite material has proved to be stronger than aluminum (Baley, Bourmaud and Davies, 2021). The material in question is lighter than steel, implying decreased corrosion, power use, and cost. In addition, composite materials have less stress and cost since the average number of cables required between parts is few. Moreover, the material has proven more robust by more than two times than steel. An advanced composite element is formed from fibrous components that are usually embedded in a resin matrix with fiber lamination in alternating directions to enhance the stiffness and strength of the material (Baley, Bourmaud and Davies, p. p.106333, 2021).
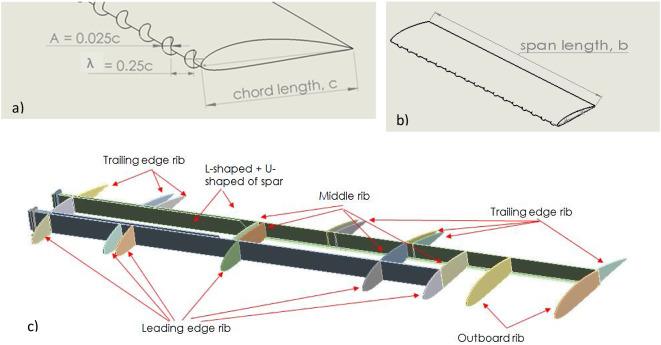
Figure 1 above is an example of a wing made of composite material to enhance the stiffness and strength of a wing. The three-layer skin, two spars, six leading ribs, five middle ribs, seven trailing ribs and two outboard ribs are fiber components used to make a firm wing (Basri et al., 2019). The fiber makes the joints between the spar, rib, and skin more adhesive. Fibre components provide a wing’s good elastic and strength properties (Basri et al., 2019). The strength of the wing is a major component for airplane stability to facilitate stability by preventing the airplane from rolling. Composite materials in wing design enhance performance by strengthening the wing hence more airplane stability.
Manageable weight through enhanced particular stiffness and strength is the main driver for improving materials for airframes. Despite this fact, the issue of affordability is crucial as it facilitates changes to new material, even in light of good performance benefits (Wunderlich et al., 2021). In this case, the cost to be considered includes initial purchase price life support, including repair and maintenance and other significant expenditures. For this reason, there is a need to ensure a balance of weight savings against the cost.
Other important considerations that one needs to ensure when selecting materials for airframe application include the safety level of the instrument, which is achieved through conventional alloys. This implies that retaining a high degree of lasting strength in the presence of joint damage for the specific component is a significant issue (Baley, Bourmaud and Davies, 2021). In addition to the material’s support cost, the durability level is also one of the significant factors worthy of consideration. This involves general resistance to recurrent strain and environmental loss through service time. In this regard, damage rate and tolerance to the same determines replacement frequency, inspection cost, and the repair need of the structure.
The issue of lightning protection using fibers fitted with an airplane has been reported to be relatively conductive with the ability to dissipate ultra-high currents coming from a lightning strike. In this regard, the external walls of composite materials are fitted with composite elements that consist of a layer of conductive material necessary for lightning strike defense (Baley, Bourmaud and Davies, 2021). This is done because composite components are inferior conductors compared to aluminum. Continued modification of composite materials has made them more common, especially in civilian aircraft (Alam et al., 2022). The increasing demand for composite materials results from the expectation of a reduction in weight, life-cycle cost, and the number of parts. A properly constructed composite structure can lead to a good design, simplified manufacturing, and lighter components compared to standard metal structures.
It is clear that composite materials tend to provide strong structure airplane wings due to metallic allows with desirable lighter weight, which helps minimize fuel performance and improve performance. In this regard, it is worth noting that weight reduction is one of the most significant advantages of composite materials on airplane wings (Samuel, Sumaila and Dan-Asabe, 2021). This is the critical factor that guides its selection for airplane wing use. Other notable advantages include resistance to corrosion and fatigue damage. These factors help reduce general operation costs in aircraft operation and further its efficiency.
In today’s business environment, the use of hybrid composite materials in airplane wings is becoming increasingly common, especially among medium and small-sized operators. The type in question is made from a combination of glass fibers and carbon, with the primary aim being to attain an appropriate technical solution (Jena and Gupta, 2019). Advanced materials are known for having great potential in damage resistance and longevity. However, it is essential to realize that composites’ general strength and longevity tend to vary depending on the fiber orientation between the layered structures (Jena and Gupta, 2019). In this regard, the best features can be attained by ensuring proper alignment of the fiber direction with the significant load direction.
Additionally, composite materials can be cast into different shapes and sizes in airplane wings compared to their metallic counterparts. In this regard, they tend to reduce the number of parts that make up specific components and the need for joints and fasteners, hence giving two folds advantages (Samuel, Sumaila and Dan-Asabe, 2021). Fewer joints and fasteners imply less assembly period, bringing forth significant gain in terms of time saved in the entire process. However, less assembly period needs to be offset by the higher duration needed in the first place fabrication of the component. The individual layers are chopped into desirable shapes and then fitted on the former in the specified sequence to attain a desirable composite structure. This combination is subjected to continuous pressures and temperatures to ensure the ‘curing’ of the material.
Today, most airplane designers are fitting their dream planes with composite materials on their wings due to the reduced cost of fuel, enhanced aerodynamics, and fewer parts requirements. It is evident from the above analysis and in the airplane market that the lighter the plane, the less cost of its operation (Alam et al., 2022). Using composite materials in an airplane’s spar wings helps reduce its weight by 20% compared to traditional aluminum planes.
In addition to a decrease in weight, aerodynamics is another significant element for aircraft fuel efficiency. In this regard, we note that the sleeker design of an airplane helps in making it more fuel-efficient. This is because composite materials can produce smoother yet very complex geometrics (Reddy, Suresh and Shivakumar, 2021). In addition, the stiffness characteristics of composite materials help in the use of swept designs of wings, especially in commercial aircraft. This feature helps in reducing fuel costs by 5% because of a decrease in aerodynamic drag.
Composite materials also help reduce the number of parts required to make spar airplane wings. This is due to the general ability of composite materials to be modeled where each mold is appropriately designed to accommodate other parts (Reddy, Suresh and Shivakumar, 2021). Because of the fewer parts required to make the plane, it is now clear that less time will be required, and fewer workers will now be required to assemble the wing parts, hence reducing operation costs (Samuel, Sumaila and Dan-Asabe, 2021). These combined factors help reduce the cost of making an airplane wing.
Environmental Impact on Composites Wing Spar during Maintenance
Focusing on the effect of the composite material on the environment, it is essential to realize that airplane tends to release more harmful indexes of CO2, although in small percentages. This is due to high attitudes, which make the released gases fall directly to the already highly concentrated greenhouse phases, intensifying the global warming phenomenon. In this regard, aircraft weight is a significant variable that can help in reducing the probable effect of the gases released daily in the atmosphere (Jena and Gupta, 2019). Also demonstrated in figure 2 below, the oxygen used by airplane passengers in the cabin is sourced outside through the fuselage therefore, excess CO2 emissions affect the oxygen available in the carrier cabin (Yan et al., 2020). Therefore, the use of composite materials in airplane wings helps in curbing such effect due to the use of light materials, which leads to less fuel consumption that translates to reduced release of CO2.
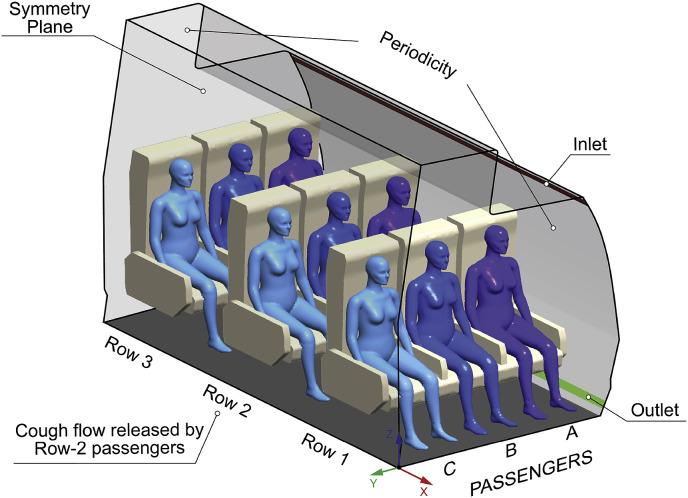
Most airline firms have announced plans to make their operation more sustainable in terms of cost and environmental pollution. However, this has proved to be a challenging activity. Airlines are employing several ways intending to reduce emissions. In this regard, composite material in airlines wings and other plane parts has become everyday activity (Reddy, Suresh and Shivakumar, 2021). Other activities include a coating to make places more aerodynamic, lighter, and resistant to all forms of wear and tear. All these activities, although costly, are fashioned to ensure sustainability in environmental preservation alongside a reduction in the operation costs of the planes.
During airplane maintenance, burnings from composite materials tend to be hazardous especially released from fiber-reinforced materials. The gases released are toxic, and this poses a great challenge to aircraft firms in the management of such harmful pollutants during maintenance. In addition, the toxic chemicals released from the burning of organic resin during maintenance tend to produce pollutants in the environment, capable of causing chronic or acute respiratory complications (Bons, 2020).
The aviation industry considers all possible efforts capable of addressing its impact on the environment. Some of the notable evidence includes decreasing fuel consumption through such practices as the use of wingtips, the wise use of energy, and operational efficiency (Mansor et al., 2019). In this case, process science and materials have been leading the efforts. The use of composite fibers reinforced with other polymers has helped make lighter aircraft wings. This effort is known to have contributed to at least a 15-14% decrease in fuel use (Bons, 2020). This effort is widely appreciated due to its outstanding efforts in ensuring a reduction in carbon dioxide released. The practice is evidenced in all families of Boeing 787. Most Dreamliner is said to have more than 50% of composite material on their wings and other parts hence attaining 20-25% efficiency than their counterpart plane (Bons, Para. 13, 2020).
In terms of weight reduction, thermosets are known to be heroes. Its use in many platforms has significantly helped in carbon dioxide decrease and fuel-saving throughout the airplane’s life. However, technology use presents challenges (Mansor et al., 2019). This is because the manufacturing process is energy-intensive and time-consuming. In addition, landfilling has been the historical disposal method for most polymer composites (Reddy, Suresh and Shivakumar, 2021). However, essential advancement has been made to ensure the proper recycling of all composite materials (Bons, 2020). For instance, the application of dissolving and vaporizing resignals has made it possible for Boeing to recycle its excess composite materials. This has significantly helped minimize the solid waste disposed to most landfills by more than a million pounds annually.
The use of composite materials in making airplane wing spars and other parts instead of precious metals proves to be more efficient in terms of aerodynamic manipulation, effectiveness, and fuel-saving. The existing flexibility gives room for a change in the traditional plane designs in the industry (Jena and Gupta, 2019). Commercial aircraft in the future are expected to have designs where wings and fuselage combine as in most military aircraft. This kind of design dramatically helps enhance the lift-to-drag plane ratio enabling the plane to be highly aerodynamic with a considerable reduction in weight. The recent introduction of planes with curved fuselage and fatter helps to enhance the flow of air alongside an increase in cabin space. In this regard, thinner and longer wings fitted in planes will help in reducing drag, hence improving fuel efficiency. It is essential to realize that a U-shaped airplane tail aids in decreasing engine noise. Composite materials are the primary facilitator of all these perceived concepts.
While using composite materials in aircraft has existed for several decades now, the practice is becoming increasingly common as manufacturers look for novel ways to maximize this incredible resource. Because of the evidenced incredible strength, smooth finish and lightweight composite materials have become ideal for building airplane wings (Othman, 2019). Combining all these strengths helps reduce composite materials’ operation and manufacturing costs. However, it is essential to realize that composite materials also pose a significant challenge due to their stiffness. In wind damage, it is difficult for the material to bend and allow repair to the damaged parts (Othman, 2019).
Moreover, the strength of the material makes it hard to establish when its interior structure has been smashed. Comparing this with aluminum, one can tell that aluminum is damaged because of its ability to bend. For this reason, executing repair to the composite material is extremely expensive and time-consuming.
In addition to the above composite material weaknesses, it is essential to note that the component tends to weaken at temperatures close to 150 degrees. For this reason, the operators are required to take more precautions and ensure they avoid fires. It has been established that fires resulting from composite materials release highly toxic fumes and micro-elements into the air leading to environmental pollution. Besides, temperatures above 300 degrees are capable of causing structural failure (McIlhagger, Archer and McIlhagger, 2022). Finally, composite materials are known to be expensive in their initial cost. However, their initial costs are usually offset by savings in the long term.
In light of the ever-increasing environmental lobbying and fuel costs, commercial flights are subjected to an under-sustained push to enhance their performance. In this case, weight reduction is the primary determinant that can help in providing a sustainable solution. Apart from the day-to-day cost of operation, aircraft maintenance programs can be simplified by reducing corrosion and component count (Reddy, Suresh and Shivakumar, 2021). The existing competitive nature of the aircraft creation industry helps to ensure any chance to reduce the cost of operation is maximally exploited and explored where possible.
Conclusion
In conclusion, it is clear that using composite materials, particularly in airplane wings, has helped create efficiency in terms of environmental protection and operation cost. However, the component is costly, poses difficulty when executing repair, and is highly risky when exposed to certain degrees of heat. For this reason, researchers need research to determine the most appropriate alloy combination that can help eradicate some of the significant weaknesses associated with the material. This will help encourage its universal application in other industries, such as motor companies that aim to minimize environmental pollution through the use of lighter vessels. On the other hand, there is a need to minimize the initial cost of acquiring composite materials to encourage their use in various facets of the industry. With the continuous increase in global warming issues, manufacturing companies are encouraged to enact plans on how to reduce air pollution. Therefore, minimizing the composite material’s acquisition cost will help enhance its demand and use in various classes of airplanes. Although such measures are likely to take longer before full realization, they are crucial due to the above essential abilities associated with the material.
Reference List
Alam, M.A., Ya, H.H., Sapuan, S.M., Mamat, O., Parveez, B., Yusuf, M., Masood, F. and Ilyas, R.A., (2022). Recent Advancements in Advanced Composites for Aerospace Applications: A Review. Advanced Composites in Aerospace Engineering Applications, pp.319-339.
Baley, C., Bourmaud, A. and Davies, P., 2021. Eighty years of composites reinforced by flax fibers: A historical review. Composites Part A: Applied Science and Manufacturing, 144, p.106333.
Basri, E.I., Sultan, M.T., Faizal, M., Basri, A.A., Abas, M.F., Majid, M.A., Mandeep, J.S. and Ahmad, K.A., 2019. Performance analysis of composite ply orientation in the aeronautical application of unmanned aerial vehicle (UAV) NACA4415 wing. Journal of Materials Research and Technology, 8(5), pp.3822-3834.
Bons, N., 2020. High-fidelity Wing Design Exploration with Gradient-based Optimization. The University of Michigan Press (Doctoral dissertation). Web.
Jena, S. and Gupta, A., 2019. Embedded sensors for health monitoring of an aircraft. In Sensors for Automotive and Aerospace Applications (pp. 77-91). Springer, Singapore.
Mansor, M.R., Nurfaizey, A.H., Tamaldin, N. and Nordin, M.N.A., 2019. Natural fiber polymer composites: utilization in aerospace engineering. In Biomass, Biopolymer-Based Materials, and Bioenergy (pp. 203-224). Woodhead Publishing.
McIlhagger, A., Archer, E. and McIlhagger, R., 2020. Manufacturing processes for composite materials and components for aerospace applications. In Polymer Composites in the Aerospace Industry (pp. 59-81). Woodhead Publishing.
Moors, G., Kassapoglou, C., de Almeida, S.F.M. and Ferreira, C.A.E., 2019. Weight trades in the design of a composite wing box: effect of various design choices. CEAS Aeronautical Journal, 10(2), pp.403-417.
Othman, M.F., 2019. Aeroelastic Tailoring of Composite Aircraft Wings with Uncertainty Quantification for Robust and Reliable Design (Doctoral dissertation, University of Bristol).
Reddy, S.S.P., Suresh, R., MB, H. and Shivakumar, B.P., 2021. Use of composite materials and hybrid composites in wind turbine blades. Materials Today: Proceedings, 46, pp.2827-2830.
Samuel, B.O., Sumaila, M. and Dan-Asabe, B., 2021. Manufacturing of a natural fiber/glass fiber hybrid reinforced polymer composite (PxGyEz) for high flexural strength: An optimization approach. The International Journal of Advanced Manufacturing Technology, pp.1-12.
Wunderlich, T.F., Dähne, S., Reimer, L. and Schuster, A., 2021. Global Aerostructural design optimization of more flexible wings for commercial Aircraft. Journal of Aircraft, 58(6), pp.1254-1271.
Yan, Y., Li, X., Yang, L., Yan, P. and Tu, J., 2020. Evaluation of cough-jet effects on the transport characteristics of respiratory-induced contaminants in airline passengers’ local environments. Building and Environment, 183, p.107206.