Abstract
Membrane filters are in growing popularity all over the world. These types of filters have found various uses in many industries and sectors. One notable use of membrane filters is in the treatment of water for drinking and domestic use. Membrane filters offer cost-effective and practical solutions to drinking water quality issues. Membrane filters are able to remove impurities and microorganisms from water samples. There are different types of membranes with each type having its unique pore size and purification abilities. In most practical applications, more than one type of membrane is often used as each has its own abilities and operational parameters.
To prevent clogging and operational issues, the pore sizes are usually reduced gradually in filtering processes. This study will attempt to create an understanding of the different types of membrane filters and their individual characteristics. The abilities and limitations of each type of filter will also be assessed. The different types of materials used in membrane filters have also been analyzed and appropriate recommendations are given.
There are two notable types of membrane filters namely inorganic and organic filters. This study attempts to investigate whether inorganic filters are more suitable for industrial and water treatment processes when compared to organic filters. Membrane filters have been found to be beneficial to society both as a method of providing clean and safe water but also as a provider of proper solutions to separation and purification problems in all fields of life.
Introduction
Water treatment is a vital need of any city and urban population. This is because water is a basic amenity that supports animal and plant life. Contaminated water has serious effects on the health of people and is known to cause death and damage to human bodies. Water is the foundation on which cities and towns are built. In earlier civilizations, towns and trading centers were built around waterholes, rivers and water masses. This is because life cannot exist without water. (7)
This principle still holds true and the quality of life in any city or urban center in the modern world is greatly dependent on the water resources available and on the quality of these water resources. For city planners the biggest headache is usually in ensuring that there is sufficient amount of water available for a city’s inhabitants and that waste water will be easily eliminated to avoid contamination of the city.
Water is becoming a scarce resource with the earth’s fresh water resources being on a steady decline. This poses a great risk for future generations as there is a possibility that they may lack enough resources to use. It is due to this knowledge that scientists have devised means and ways that could be used to recycle and purify waste water and create utility for it. (10)
The world is being overpopulated and the available fresh water is becoming impure and unclean for human use. Fresh water springs are being polluted by industrial wastes, rivers are being flooded with runoff from farms due to over-cultivation and in general, the clean water reserves that were once present do not exist anymore. This has brought about the need for the development of purification and treatment systems that are geared towards reclaiming impure water and making it safe for human consumption.
Water is known to harbor diseases and pathogens that are very dangerous. Examples of water borne diseases include amoeba infections, cyclosporiasis, microsporidiosis. Such diseases cause effects such as vomiting, diarrhea, vomiting and loss of weight. Contaminated water can cause diseases when used to prepare food in households. The capability of water to act as a vector for harmful diseases calls for proper treatment of water resources.
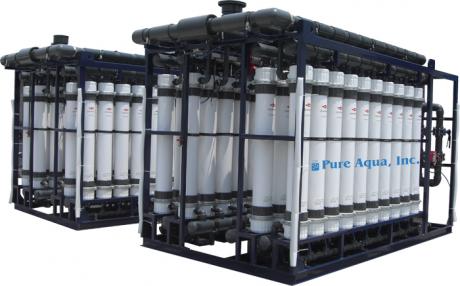
The end objective of any water treatment process is to remove contaminating substances from the water and to make it safer for human consumption. There are four steps that are usually taken in a water treatment process. The first step in any water treatment process is to settle huge and heavy particles. This is usually done in huge settling tanks where the water is allowed to stay still without disturbance to allow for heavy particles to settle to the floor of the tank.
The second step is to filter lighter particles that have failed to settle at the bottom of the tank. Filtration is done by fine filters that capture microscopic particles that are suspended in the water. There are various methods used in the filtration of water for human use namely membrane filtration through the aid of pressure pumps, rotary filters, filters using vacuum drums, and sand filters. Other methods such as chlorination and the use of ultraviolet rays are very commonly used in water purification processes. (11)
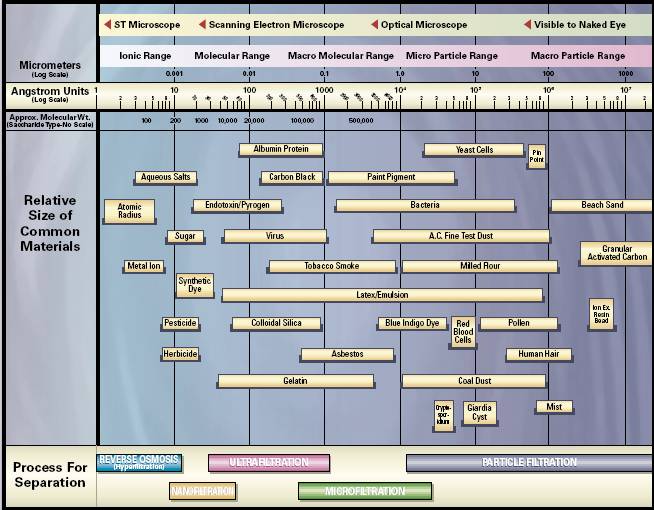
This study will focus on water purification using pressure-driven membrane processes. These types of filters operate on the principle that when a liquid is forced through a membrane that has small pore sizes the membrane can trap impurities and unwanted particles thus resulting in a purified solute. A setup that involves the use of a pressure-driven membrane filter must-have pumps that create high pressure at one end and force the liquid to flow through the membrane leaving behind captured particles. The membrane material used is sometimes made up of polymers. The pressure membrane filter casing is usually made of steel or hardened plastic.
Such filters have an inlet and outlet pipe. The inlet pipe delivers untreated water to the membrane and the outlet pipe delivers filtered water from the membrane to the outlet. The filter is divided in to two cavities, one for unfiltered water and another for purified water. The membrane is what separates these two cavities. The membrane is usually folded / coiled so as to increase its surface area of contact with the fluid. The membrane coils are carefully placed into the casing and leakages in the membrane are checked to ensure efficient performance. The casing properties must also be put into consideration so as to ensure that the casing has the ability to withstand high pressures that may be needed so as to ensure that the fluid flows through the membrane.
A membrane filter is measured by the size of pores of its membrane. In the design of a membrane filtration system it is very important to properly determine the desired particle size so as to be able to make an informed choice of the type of membrane filter to be used. The type of membrane filter used is also dependent on the properties of water being filtered and its source. Water that has small particles suspended will require smaller membrane pores compared to water that has larger particle suspended.
Membrane filters may employ a successive layer of membranes that are gradually decreasing in pore size. Such an arrangement increases the useful life of the membrane compared to filters that only use one membrane that is expected to produce the required water purity. This is because of the reduced cases of clogging and obstruction of the pores of the membrane. There has been an increased usage of the membrane filtration method in the past 10 years. This is because people have realized the benefits and simplicity of this technique compared to other methods. (13)
Types of Pressure Driven Membrane Filters
There are various types of pressure driven membrane filters. Each type has its own unique properties and areas of application. There are four notable types of membrane filtration processes namely, nanofiltration, ultra filtration, microfiltration and reverse osmosis.
Microfiltration
Microfiltration is a process used to remove contaminants from a solute and produce a purified product. This type of filtration process can both be used for liquids and gases. Examples of micro-filters that are used for gaseous purposes include gas masks and filters. This type of filtration is able to extract impurities that are larger than the pores of the filter membrane. Impurities that happen to be smaller than the filter membrane undergo partial filtration and may at times go unfiltered. It is due to this reason that multiple membrane layers are usually employed so as to capture any small particles that may escape through the membrane
The average size for the pores of microfilters is usually between 0.1 to 10 micrometers. Due to the size of the pores of micro membranes, they are able to capture microorganisms such as bacteria and remove them from the fluid matter. However micro filters are not able to filter viruses because viruses are very small in size and tend to pass through the membrane pores.
Micro filters are used to filter solutions that have concentrations of between 2 to 3 percent of unwanted large matter. If the recommended concentration of the large matter is exceeded the filters tend to clog and a great reduction in operational efficiency is noted. This type of filtration process is very suitable as it is cheaper compared to the other membrane filtration techniques. The reason for this is because the fluid in micro filters do not necessarily have to be pumped so as to go through the membrane. This is because micro filters have relatively larger pores compared to other membrane filters.
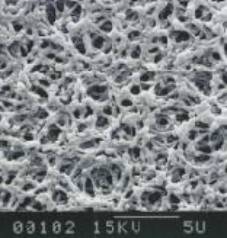
Microfiltration could also be done with the aid of pumps in instances where high flow and filtration rates are required. However in some instances this is not necessary; is an increase in the overall costs of the system. This filtration technique is commonly used in filtering drinking water and for use in laboratories and industries. Micro filters are commonly used in mineral water preparation plants as this method is able to separate harmful pathogens at minimal pumping or low pressures. This method was initially used for treating municipal water supply lines without chemical treatment. However, as water became more contaminated and unsafe chemical treatment and microfiltration had to be incorporate to ensure public safety and health.
Micro filters are most common type of membrane filters in use in industries and water treatment plants. This is because they are easy to construct, and cheap to maintain.
Ultra filtration
Ultra filters on the other hand have pores of sizes between 0.001 and 0.1 micrometers. Ultra filters are more refined compared to micro filters as they are able to remove smaller matter as compared to micro filters. The ultra filtration setup is able to remove substances such as colloids, polymeric molecules of both organic and inorganic nature and viruses from a solution. However colloids and polymer molecules that have low molecular weights are allowed to pass through the membranes. (20)
Because of the relatively small sizes of the pores of micro filters they employ the use of hydrostatic pumps that generate a high pressure so as to create a flow of fluid from high pressure regions to low pressure regions; leaving behind matter with high molecular weights. Ultra filtration is known to be a safe and sure way of treating water. Unlike other methods such as micro filtration that allow viruses to pass through, ultra filtration filters up to viruses and ensures that drinking water is safe.
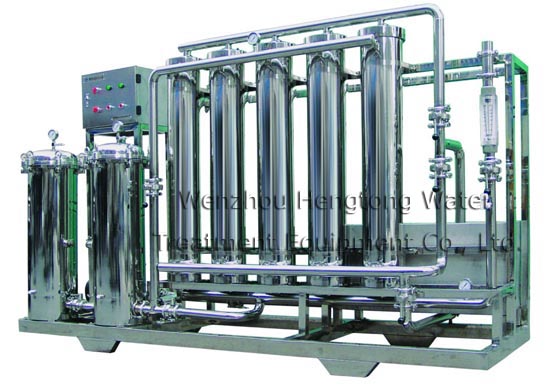
Benefits of using ultra filtration as a water treatment process include:
- Water that is of high quality and safe for human consumption can be produced
- Water of consistent quality and purity can be produced using the method
- Lower costs involved in the purification process and there is no use of expensive water treatment chemicals
- Good for the environment as the use of chemicals is minimized
- Ultra filters are compact and easy to install
Ultra filtration is commonly used as a pretreatment process for water before nanofiltration and reverse osmosis. This is done to reduce the impurity content in water before it undergoes the later processes. Pretreatment by ultra filtration is done so as to eliminate the possibilities of damage to nanofilter and reverse osmosis membranes.
Pretreatment processes are also done before any ultra filtration process so as to protect ultra filter membranes. Filters with pore size of between 0.5 and 1.0 millimeters are used. All pretreatment processes are done to protect membrane filters from damage that may arise due to clogging, rapture of membrane surface due to sharp objects and deformation of the filter membranes.
There are different types of ultra filter membranes namely; hollow fiber membranes, tubular membranes and spiral wound modules. Hollow fiber membranes are made up of membrane tubes of diameter between 0.6 mm and 2.0 mm that filter solutions and allow the permute to flow into a cavity around the fibers. Tubular membranes on the other hand involve a membrane core that filters the solution and releases the solute into an outlet tube.
Tubular membranes maintain high flow of the solution and this minimizes instances of clogging making tubular membranes suitable for viscous fluids and those that have high amounts of impurities. The last type of ultra filter is the spiral wound membrane type. This makes use of a long film of membrane that is wound to form wavy coils. The advantage of the spiral wound membrane is that it is compact and there is increased surface area for the filtration of the solute. This means that this type of ultra filter is able to produce more volumes of solute per unit area compared to the other types. However the spiral wound membrane is prone to clogging and damage in cases where the solute quality is low. (17)
Factors that affect the performance of ultra filters include the flow rate of the solute, the temperature of the solute and the operating pressure of the system. When the velocity of flow of the solute is increased the amount of permeate increases and vice versa. The amount of permute produced also increases with an increase in temperature or pressure. However these two factors must be kept in check as excessively high pressures result in clogging / compaction of matter on the membrane. Excessively high temperatures also result in damage of the membrane.
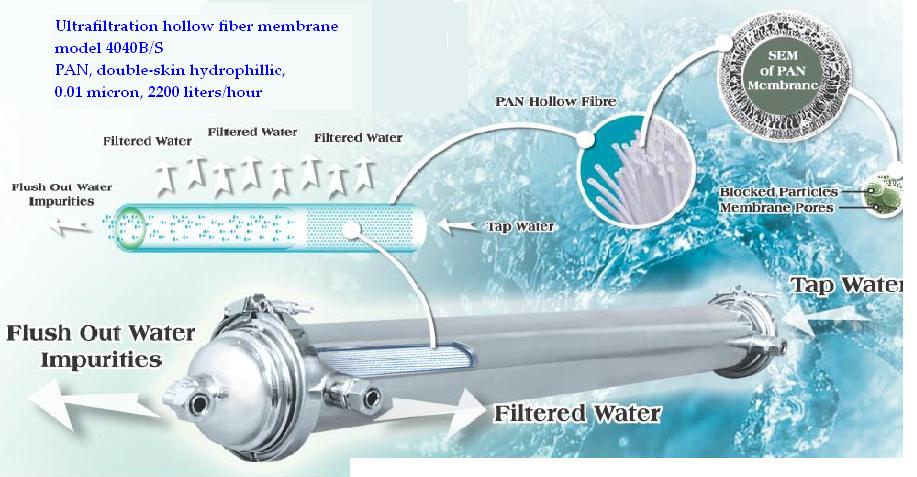
Nanofiltration
Nanofiltration is mainly used for softening drinking water, removal of microscopic contaminants and elimination of unwanted coloring from water. Nanofiltration is able to remove coloring compounds from water. In industrial setting, nanofilters are used to remove dye coloring from water. Nanofiltration is a pressure dependent process and cannot function at low pressures. The pressure is responsible for forcing the water molecules in the solute to flow in to the permute.
Nanofilters are also able to select salt ions and control their flow. This type of membrane filter allows monovalent ions to pass through it but rejects multivalent ions. The average pore size of a nanofilter is approximately 1 nanometer. However unlike micro filters and ultra filters, nanofilters are classified according to the molecular weight ratings of the filter. Nanofilters make use of anti scaling compounds so as to prevent damage of the delicate membranes.
Applications of nanofilters
Nanofilters are used in a wide range of applications such as :
- Filtration of dangerous chemicals from ground water
- The extraction of dangerous and harmful heavy metals from water. Examples include lead and mercury elements
- Softening of water
- Treatment of water contaminated with agricultural chemicals such as nitrates from fertilizers
- Removal of phosphates and soap compounds from water. This can be used in the treatment processes of laundry water
Nanofiltration offers realistic solutions to water treatment problems all over the world. This is because of the reliability of the process and its ability to remove discoloration and soften drinking water. This technology is widely used in developing nations where water is a serious problem. Examples where nanofilters are in large scale use is Africa where access to clean water is limited. Nanofilters are provided to the people with the aid of humanitarian organizations and governments in an attempt to improve the quality of water available to the people as well as the quality of life.
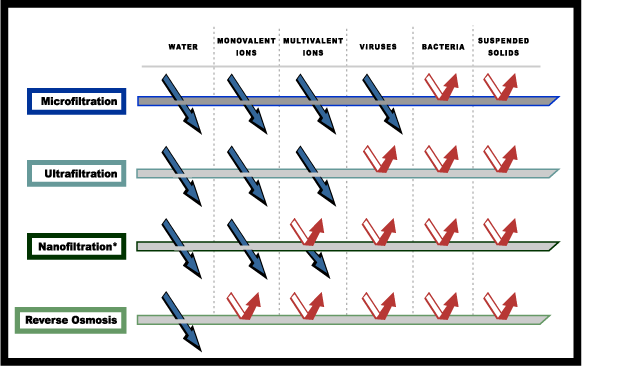
Reverse osmosis
This type of filtration process is applied in areas where the operator intends to remove the ions present in a solute. (2)
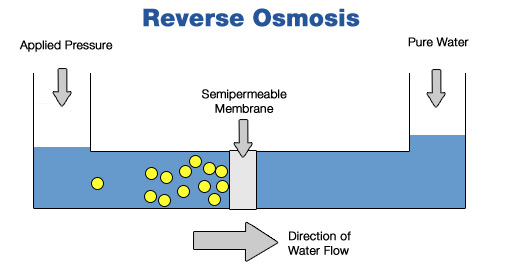
The principle behind reverse osmosis is that it makes use of a pressure difference between the solute region and the permute region. This causes flow of fluid from the solute side to the permute side. However, unlike other filtration methods, reverse osmosis does not allow the flow of ions through the semi permeable membrane. (2)
This type of filtration is done in instances where pure water that is free of ions is needed. However reverse osmosis cannot be used as an exclusive water treatment option and it has to be used in conjunction with other water treatment processes such as ultra filtration and nanofiltration.
The difference between reverse osmosis and other methods of filtration is that it makes use of high pressure, difference in concentration levels and diffusion to separate water molecules from a solute. Other methods of filtration on the other hand use the size difference between the molecules and the pores so as to separate contaminants from the solute. Such methods are independent of factors such as salt concentration and diffusion. (19)
The reason for this dense barrier is to enable it to withstand high pressures that may be imparted on the membrane. Reverse osmosis cannot occur in the absence of high pressure since the pressure is what forces the fluid particles through the membrane. The membrane in its structure is designed to allow fluid particles to go across but prevent salt ions from flowing. Reverse osmosis is mainly used in the purification of water for various uses namely:
- Extraction of drinking water from sea water with high salt concentrations
- Preparation of purified water for use in treating wounds in hospitals
- In lead acid batteries to avoid the reaction of salts in the water with the battery components
- Treatment of water to be used in boilers to avoid formation of salt deposits in piping and tanks
- Treatment of water for industrial cooling purposes
- Used to remove salts from effluent water
- Applied in the concentration of juices and foods. Examples include fruit juices that are concentrated so as to minimize transportation and handling costs
- Used in the manufacturing process of whey and concentrated milk solutions
- It is applied in hydrogen formation processes and helps to avoid the mineralization of the electrodes
Materials of Filter Membranes
Inorganic membranes
This type of membrane is made up of material that is not of biological nature. Inorganic membranes may be made up metal or ceramic compounds. Inorganic membranes can be defined as those that do not have covalent carbon bonds.
Inorganic membranes are cost effective and cheap to maintain. This is the reason for their increased use in industries and science laboratories. Inorganic membrane development processes are underway in an attempt to produce better and more effective membranes for use in industries. (1)
The two most common types of inorganic membranes in application are ceramic and metal membranes
Ceramic membranes
Ceramic membranes are mainly made up of glass, zirconia compounds, titania and alumina. This type of membrane is used in hostile environments that would otherwise damage organic membranes. Ceramic membranes are known to withstand high acidity and tolerate high temperatures. The main factors that affect the choice of a membrane in industries is the ability of a membrane to withstand harsh operating conditions and the amount of repair and maintenance that the membrane needs. Ceramic membranes require minimal maintenance and are easy to install. (5)
Membranes of ceramic nature usually filter out solutes and produce purified permutes as they have small pores that strain the solute. These membranes are also produced from carefully selected materials and thus are not harmful to the users or the environment. Ceramic membranes are the most environmentally friendly type of membrane that are in production. Inorganic membranes are also known to have a longer working life compared to organic ones. The long working life coupled with resistance to high temperatures, physical stability, chemical stability and continuous operation abilities make the ceramic membrane the best choice in modern industrial applications.
The ceramic membranes can also be sterilized using steam as they are not temperature sensitive. They are also resistant to abrasion and can therefore be used on solutes that portray abrasive properties. Another advantage of ceramic membranes is their ability to produce high amounts of permute per unit membrane area; high flux. Ceramic membranes are also resistant to bacteria attacks and are able to filter solutes that have high bacterial contents with minimal damage to the membrane. Lastly ceramic membranes when not in use can be dried and stored. Unlike other types of membranes, ceramic membranes do not undergo any damage due to dry storage. (6)
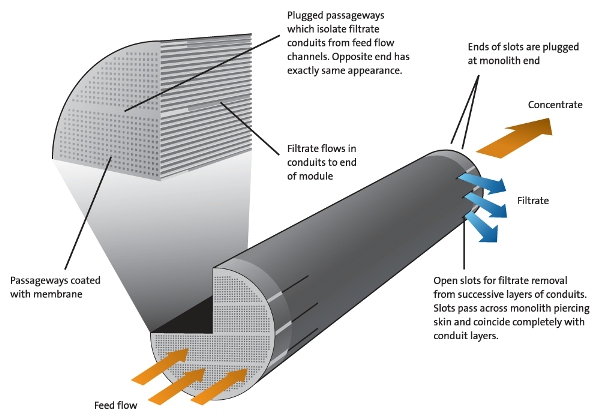
Shortcomings of ceramic membranes include high transportation and storage charges due to the high weight of the membranes. Ceramic membranes are also costly to produce and manufacture as they are made up of expensive components.
Applications of ceramic membranes
- Treatment and purification of waste water
- In chemical factories as a separation and cleaning agent, catalyst separator, removal of salts from solutes and in the recycling of industrial solvents
- In metal factories as a treatment option for oil emulsions, a means of extracting heavy metals from solutes, treatment and filtration of industrial waste water.
- In paper factories as a means of removing salts from solutes, extraction and removal of fats from emulsions and separation of yeast.
- In food industries as a juice concentrator, in milk sterilization, whey sterilization, filtration of juices and wines and in the removal of water from food so as to increase shelf life.
- In recycling and treatment facilities as a separator of water and oil in emulsions, removal of chemicals from solutes, removal of living microorganism from domestic use water, in sewage treatment facilities and in swimming pools as a cleaning agent for the water.
Metal membranes
Metal membranes are usually made up of alloys of platinum and palladium elements. The membranes are then casted to form plates of the elements. These plates are then oxidized to form oxides of the period 3 elements. The plates are then sintered to form membranes that are suitable for filtering water. (9)
Metal membranes were widely used for hydrogen separation in the 1950s. Its ability to maintain a high flux rate in hydrogen separation processes made it very favorable for use in hydrogen involved industries. However a major setback that hindered and caused the slow development of metal membrane technology is the exorbitantly high cost of these membranes.
Recent developments on the metal membrane technology include the development of an ultra thin metal membrane that involves the coating of a thin palladium coating on a polymer skeleton. This is said to reduce the overall cost of the membrane and improve on hydrogen flux. Another development is the use of cheaper elements for the membrane such as tantalum and vanadium and then coating these elements with a thin film of palladium.
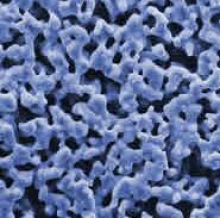
Metal membranes are mainly used for hydrogen separation processes. This is because of the relatively high hydrogen flux rates that these membranes provide. Metal membrane technology is still a relatively expensive method of extracting hydrogen as it requires high temperatures of up to 370 degrees Celsius and high feed pressures so as to function as intended. It is due to these reasons that the use of metal membranes and the development of these membranes is on a limited scale. In the near future replacements shall be found and this will be an obsolete technology. (8)
Metal membranes are also used in ultra filtration of fruit juices and wines in food industries. Although there are cheaper alternatives some manufacturers still prefer metal membranes compared to ceramic ones.
Organic membranes
The term organic membrane refers to membranes that are formed due to the covalent bonding of long carbon chains. Organic membranes are membranes that are made up or from living matter. Living matter refers to plant or animal tissue / matter. Organic membranes are not preferred as they are sensitive to heat and harsh conditions as compared to inorganic membranes. The most common type of organic membranes are polymeric membranes.
Polymeric membranes
Polymeriuc membranes can be designed to have different pore shapes and sizes. This makes this type of membrane flexible and able to assume different functions. For example an oval shape of pores can be created to fit a specific type of solvent. Studies have shown that irregular membrane pores tend to release more particles compared to even ones. Recent technology has enabled the easy production of even pores that could be customized to produce any shape with ease. (12)
The means of operation of polymer membranes is through diffusion, particularly Knudsen diffusion. The Knudsen theory proposes that diffusion occurs in such instances due to the collision of the fluid particles with the walls of the pore and thus this facilitates the movement of the particles. The average pore size of polymer membranes is usually between 3 and 45 nanometers. (15)
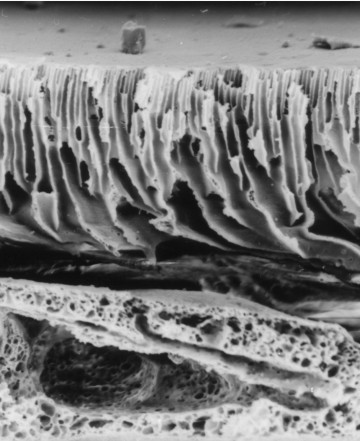
Polymeric membranes are used for the enrichment processes of natural gases, separation processes of oxygen and nitrogen and extraction of organic substances. Below are the shortcomings of organic membranes:
- They are sensitive to abrasion
- Cannot be used in acidic and highly basic environments due to their tendency to become corroded
- Are sensitive to clogging and compactions in unsuitable fluids
- Are not durable and have a short life span
- Require complex maintenance activities to be carried out to avoid fast wear of the membranes
- Cannot be subjected to dry storage
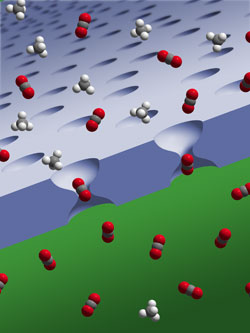
Composite membranes
Both inorganic and organic membranes each have their own limitations. It is these unique limitations and strengths that have prompted scientists to develop better and improved types of membranes. Composite membranes are made up of both organic and inorganic membranes and are proving to be better than each individual type of membrane when used on its own. Composite membranes are usually made up of alternating layers of organic and inorganic membranes that are joined together to form a membrane. (16)
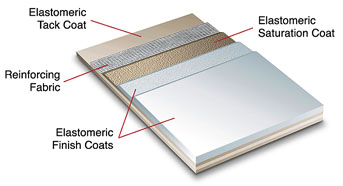
Composite membranes may also be made up of alternating layers of polymer and reinforcement membranes. An advantage of composite membranes is that they can are usually thin than other types membranes. This improves the flux properties of the membranes and makes them more efficient. (14)
Advantages and Disadvantages
Economical aspect
Membranes filters are known to be effective and efficient ways of waste water treatment. This is because of their ability to separate various fluids and elements according to the desired parameters. Membrane filters are also known to have a long working life as compared to other type of filters. A setback that membrane filters face is that they cannot be reused after completing their useful lifespan. This is why damaged membrane filters are usually disposed and new filters fitted. This is very costly as it causes the maintenance activities become a little steep.
Membrane filters however are not very costly to operate as they need simple equipment and facilities to function as intended. Membrane filter setups are usually very simple with inlet and outlet cavities separated by a membrane. The flow and output from a membrane filter can also be controlled by varying the pressure of the feed pump and this makes membrane filters a very flexible alternative. (18)
Membrane filters are very useful in many world economies. This is because their fields of application are limitless; membrane filters can be employed in municipal treatment plants, factories, industries, hospitals and research stations. This is because they offer practical solutions to separation and purification problems. Limitations of membrane filtration systems include operational parameters, membrane types, running costs, useful life and compatibility with the fluid medium.
Some types of membrane filters are relatively expensive but this does not mean that membrane filters are generally expensive, but is a representation of a few exceptions. In general membrane filters are economical and of great utility to stakeholders in different sectors of the economy.
Environment
Membrane filters have been extensively supported by environmental conservationists. The past 20 years have seen massive supplies of membrane filters to Africa and other developing nations. Such countries and regions of the world usually have clean drinking water problems. The available water resources are usually unfit for human consumption and domestic use as they often contain impurities and microorganisms that are harmful to humans.
Earlier solutions to the water crisis in developing nations proposed for the boiling of water before drinking and before using the water to cook. However, energy is another problem in such countries and the easily available sources of energy include firewood and charcoal. Boiling of water as a treatment option though beneficial to the people and medically safe, was harmful and destructive to the environment. Membrane filters offer a solution to this problem as they provide clean water for people to drink and at the same time help to conserve the available energy resources. (20)
Unlike treatment processes such as chlorination, filtration membranes do not involve the use of any chemical compounds. This makes membrane filters an environmentally friendly option as there is minimal risk to the environment posed by this type of filters. Chlorination is a risky type of treatment process as the chemicals used have to be handled properly to avoid contamination and / or poisoning of the environment. Membrane filters are an almost ‘natural’ way of treating fluids by using the basic laws of physics and chemistry.
Membrane filters also have a low carbon footprint compared to other types of water treatment. The reason for a low carbon footprint is the fact that membrane filters are very simple in their designs and mode of manufacture. The energy consumption of membrane filter units is also low as the only energy input required is for pumping purposes. The overall effect caused by membrane filters is the reduction of energy consumption, reduction of carbon emissions from the manufacturing to the operating phases and minimization of chemical use. This shows that membrane filters are good and suitable for the environment. (13)
Public health
Water has been a vector for diseases for as long as records show. It is due to the sensitivity and importance of water that water treatment techniques have been developed. The health and quality of life of any population depends on its water supplies. Membrane filters offer a practical and sure way of treating drinking water. The technological knowhow needed to operate a membrane filter is relatively low and this makes membrane filters a suitable solution for water treatment problems. Membrane filters themselves do not pose any threats to the general public unlike other types of water treatment. (3)
Chlorination is a widely used method of water treatment. However it is also very technical as careful measurement and analysis of chlorine proportions in the water need to be done before the water is released to the public for use. In cases where there have been errors and large amounts of chlorine are used this can cause harm to human health. This makes chlorination a technical and very sensitive water treatment option.
Some chemical elements used in the production of membrane filters are however harmful to the environment. Examples include vanadium, palladium and glass fibers that can cause great harm to the public if released or leaked into the environment. Membrane filters, even though they are beneficial also pose a significant threat to the environment.
Membrane filters therefore cannot be underscored for their contribution to promoting public and community health all over the world. Even though the raw materials used to produce the membranes pose a risk to public health, membrane filters have made much more contributions to public health than they have caused damage.
Aspects of operation
A disadvantage of membrane filtration processes is the need for constant pumping and creation of high pressures so as to facilitate the process. Some membrane filtration processes also require very high temperatures and pressures making the operation activities of filter membranes a little cumbersome and intensive. When compared to other processes such chlorination membrane filters require much more energy in the form of pumping and temperature regulation. (4)
Membrane filtration is also a very delicate process and must be well monitored. The membranes used for the filters are usually very sensitive and prone to damage. This means that the suitable parameters for the operation of the membranes must be maintained in order to ensure proper functioning of the membranes. Clogging is another problem that is encountered in the operation of membrane filters. This calls for routine and intensive maintenance of the membrane filters so that they can function properly. These extra requirements call for additional costs and staff who are involved in the operation of the filters. Other techniques such as chlorination do not need constant repair and maintenance of equipment like membrane filters. This makes membrane filters expensive and cumbersome in their operation aspects.
Careful operation of membrane filters is also needed in instances where the system is not automated. This is because the temperatures of the fluid solutes and permutes need to be regulated depending on the type of membrane and fluid being treated. An advantage of membrane filters is that they are compact and easy to move to different areas of operation. Other methods of water treatment such as chlorination or ultra violet ray water treatment are not easy to shift; change operating stations. The operation progress and processes of membrane filters can be effectively monitored as the membrane filtration processes are centrally located and easy to control compared to other treatment processes. (6)
Application of Membrane Filters
Membrane filters are used in a wide variety of applications. Due to their ease of use and production these types of filters have found their way into many homes and industries. Another advantage of these filters is they able to adapt to different conditions and environments. This flexibility has allowed for the development of membrane filters that are suitable for different temperatures, pressures and solutes.
Below is a comprehensive list of the various applications of membrane filters:
Chemical uses
- Used in the separation and cleaning of chemical substances
- Used in the concentration of chemical solutions such as metal hydroxide solutions
- Used in the preparation of catalysts as a separator
- Recovery of coloring compounds from solutions e.g. pigments
- Extraction of salts from solutions
- Used in the recycling processes of solvents; organic solvents
Petrochemical uses
- Used in the separation of olefin and paraffin. Olefins are polymer fibers that are also known as polypropylene. Olefin is often used in the manufacturing of synthetic fibres for use in textile manufacture. Light olefin elements can be extracted from paraffin using membranes.
- Membranes are used in the separation and recovery of solvents. Membrane technology can also be used to recycle and purify solvent substances. This technology is used on substances such as glycerin and methanol.
- Membrane filters are also used in the removal of wax substances from solvents.
- Removal of waxes from oils to produce ‘dewaxed oils’
- Membrane filters are used in the dehydrogenation of paraffin and olefin substances. Dehydrogenation involves the removal of hydrogen from the paraffin and olefin
- Used in the steam reforming processes of methane gas
Food and beverage
- Used in the purification of beers and wines in brewing industries
- Used in the purification of drinking water before bottling so as to ensure that the water is free of impurities and safe for human consumption
- Removal of water and fluids from foods and natural juices as method of preservation
- In dairy industries as a way of sterilizing milk and whey
Biotechnical uses
- Membranes are now extensively used in the purification and treatment of bioreactor constituents
- Used in sterilizing inputs to bioreactors; feed streams
- Used in deactivating and minimizing the effects of biocatalysts
- Membranes are used in the filtration processes of bioreactor raw materials.
- Sterilization of fermentation matter
- Purification of proteins
- Removal of salts from whey so as to make it suitable for storage and / or consumption
Engineering uses
- Extraction of heavy metals from metal solutions
- Treatment processes of water emulsions
- Treatment processes of oil emulsions
- Treatment of waste water from engineering industries; water containing metal particles formed from grinding and milling
- Treatment of and purification of water from glass and glass fiber manufacturing industries
Paper industries
- Used in the removal of salts from solutions used in the paper industry
- Extraction of fats and solids from fluids in the paper industry
- Used in the separation processes of yeast materials
- Used in the removal of water from biological matter in paper factories
Waste treatment and environmental uses
- Used in the separation processes of oil and water
- Treatment of waste water from sewer lines
- Treatment of water used in ponds, baths and swimming pools
- Removal of micro organisms from fluids and water
Recent Developments in Membrane Filters
In the past years there have been extensive research and development activities on membrane filters. This is because of the great benefits that they provide in various sectors of life. Development and advancement of membrane technology will surely be of benefit to future generations.
Micro filters
A major problem encountered in the use of micro filters is the inability to develop high flow rates and the same time trap the required particle sizes. This is because for a micro filter to have good trapping qualities it usually has reduced flow properties. A new type of micro filter that has been found to be have high flow properties and good trapping abilities is made of polysulphone. (9) Polysulphone membrane filters have larger cartridges and this is meant to improve the flow properties of the filter. Advantages of polysulphone filters include, increased flow rate, better trapping abilities and long cartridge life.
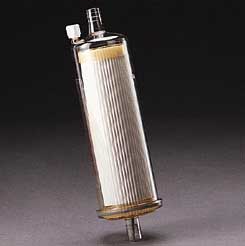
PVDF (Polyvinylidene fluoride) sintered membranes have also been found to have good flux and impurity capture abilities. PVDF undergoes sintering to form membranes that are suitable for microfiltration.
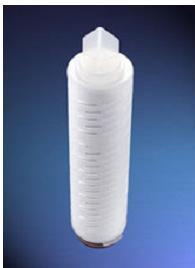
Ultra filters
Ultra filters are of vital importance to food industries and manufacturers. Their development is vital to these sectors. (1) It is owing to the financial backing and support provided to researchers by these industries and the financial incentives to manufacturers that has fueled the development of ultra filter technology. Hydrophilic PES (Polyethersulphone) is a new type of membrane that is known to be tough and resistant to harsh operating conditions. This type of membrane is slowly replacing traditional ultra filter membranes. An example of this type of membrane is the Accupor that was developed by the American Membrane Corporation.
A later development of the PES membranes is the BTS (B cell-specific tetraspanning) membrane. This membrane has a smaller thickness as compared to the PES. The reduced thickness results in an increase flow rate in these membranes.
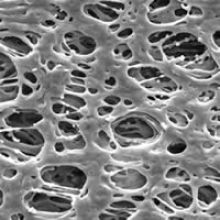
Nanofilters
Nanofiltration technology has been improved by the introduction of regular nanopores. Regular nanopores have various advantages such as the ability to filter impurities effectively and maintain a good flux. A new method that has been devised to manufacture nanofilters is by the use of a SU-8 photo resist compound formed by cross linking in presence of UV energy. The SU-8 formation is done through the regulation of the evaporation rates of this compound during its fabrication process. The SU-8 is used as a nanofilter in biological and pharmaceutical applications. (5)
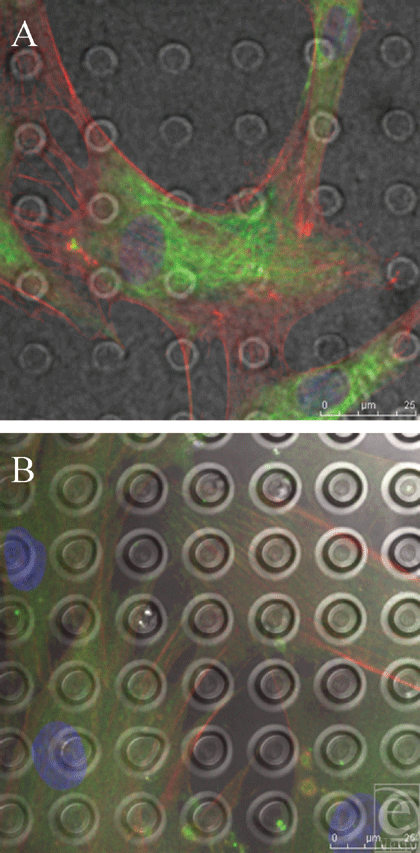
Reverse osmosis
A major weakness of reverse osmosis membranes is their sensitivity to chlorine and other chemical compounds. The sensitivity of these membranes limits their mode of application. Eltron a leading membrane developer has introduced a membrane for reverse osmosis that is more resistant to the oxidizing effects of chlorine and other compounds. This ER-HFI membrane is thinner than other types of reverse osmosis membranes and is able to filter more solute at potentially lower pressures. (16)
This membrane also has enhanced resistance to oxidation from transition elements and has god mechanical abilities. ER- HF1 and ER-HF2 membranes are currently in their development phases and have not yet gone into commercial production. However, these membranes will surely be useful all reverse osmosis operators once they have been released into the market.
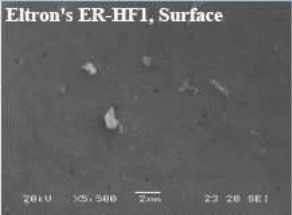
Zeolite membranes are another innovation when it comes to membranes for reverse osmosis. Zeolite membranes have been found to have pores that are suitable for reverse osmosis / molecular and ion filtration. These membranes are very stable and thus a suitable option for modern reverse osmosis operations. The membranes are fairly resistant to chemical, thermal and mechanical stimuli. These membranes are made up of zeolite crystals and the reverse osmosis is made possible as a result of inter crystalline pores. Zeolite membranes have various advantages over the commonly used polymer membranes. (7) These include:
- Improved life span and durability
- Capable of rejecting organic matter unlike polymers
- Can be used in the filtration of liquids with high TDS (Total dissolved solids) levels
- Membrane regeneration is possible with the zeolite membranes
- Capable of operating efficiently in both acidic and basic environments
However the zeolite membranes due to their crystal nature are very sensitive to pressure. The operating pressures of a zeolite membrane are lower than that of a polymer membrane. If subjected to excessively high pressures the membranes undergo failure. These membranes are used in the purification processes of water that is produced from coal- bed methane. They have found practical use in this sector and are gaining popularity over other types of membranes.
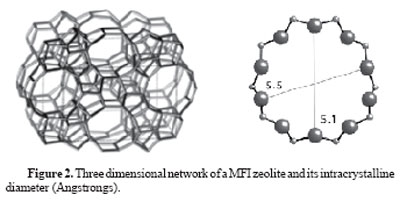
Conclusion
Membrane filters have proven to be essential to the daily processes of individuals and organizations. This is because of the adaptability of membrane filters and their ability to suit various types of environments and needs. There are various types of membrane filters with each type of filter having its unique properties. The wide selection of membranes to choose from is beneficial to users and experts from different fields. Membrane filters have found their use in many areas ranging from homes, to paper manufacturing industries.
Membrane filters have also been found to be evolving and on a continuous trend of improvement. This is owed to the advancement and development of membrane technologies. New and simple ways of membrane production have been found and this has aided in improving the versatility and flexibility of use of this type of filters. New technologies have also facilitated the massive production of membranes and this has aided in reducing the filter membrane prices over the years. This is due to economies of scale and ease of marketability of this type of membranes.
Research and studies on membrane sciences have also assisted scientists in coming up with new and improved membrane materials. Each type of material is capable of operating at unique temperatures, pressures and solute parameters.
The development of new membrane materials has facilitated the creation of specialty areas for each type of membrane. Synthetic membranes are known to be hardy and adaptable to harsh working conditions therefore are suitable for acidic, corrosive and generally hostile environments. Organic membranes were the earliest types of membranes but are steadily being replaced by inorganic membranes due to their enhanced strength and performance potential. Inorganic membranes are far much cheaper in the long run and with this kind of economical justification, they have become the preferred option.
Membrane filters have been found to be of great benefit to sectors such as the economy, food and beverage industries, environmental conservation, public health and consumer safety, pharmaceutical industries, and chemical / petroleum product industries. Although these filters face some few shortcomings and limitations they are by far more of a benefit than an evil to humans in general. With proper maintenance and careful use membrane filters are capable of providing long and reliable services to all concerned stakeholders regardless of the field of application. New uses and techniques of membrane filtration are being developed on a daily basis and the future holds promises of modified and improved membrane filters.
References
- Afonso MA. Green separation processes: fundamentals and applications. London: Wiley VCH; 2005.
- Asano T. Water reuse: issues, technologies, and applications. New York: MacGraw Hill; 2007.
- Boddekker KW. Liquid separations with membranes: an introduction to barrier interference. Berlin: Springer-Verlag; 2008.
- Bose CA. Inorganic membranes for energy and environmental applications. New York: Springer Link Publishers.
- Drioli E. Membrane Operations: Innovative Separations and Transformations. New York: Wiley VCH; 2009.
- Frankel M. Facility Piping Systems Handbook: For Industrial, Commercial, and Healthcare. New Jersey: MacGraw Hill; 2009.
- Golden AD. Modern food microbiology. New York: Springer Link; 2005.
- Koltuniewicz BA. Membranes in clean technologies: theory and practice. London: Wiley VCH; 2008.
- Li K. Ceramic membranes for separation and reaction. New York: Wiley and Sons; 2007.
- Li NN. Advanced membrane technology and applications. New Jersey: Wiley and Sons; 2008.
- Mallada R. Inorganic Membranes: Synthesis, Characterization and Applications. New York: Elsevier Advanced technology; 2008.
- Nath K. Membrane Separation Processes. New Delhi: Prentice Hall India; 2008.
- Nunes SP. Membrane Technology: Volume 4: Membranes for Water Treatment. London: Wiley VCH; 2010.
- Pabby KA. Handbook of membrane separations. New York: CRC Press; 2008.
- Patnaik, P. Dean’s analytical chemistry handbook. New Jersy: Macgraw Hill; 2005.
- Rizzuti L. Seawater Desalination: Conventional and Renewable Energy Processes. New York: Springer Link; 2009.
- Sammells FA. Nonporous inorganic membranes: for chemical processing. London: Wiley VCH; 2006.
- Singh R. Hybrid membrane systems for water purification. New Delhi: Elsevier Publishers; 2006.
- Sutherland K. Profile of the International Membrane Industry. New York: Elsevier Advanced technology; 2005.
- Toledo R. Fundamentals of food process engineering. New York: Springer Link; 2007.