Waste or used tire is a mixture of rubber fillers bound with giant blenders. A typical tire combines 30 ingredients during its production phase (Ahmet 23). The features of tire production include ply, belt, shoulder, spie, & grove, beads, sidewall, read and rib. The production process combines different rubbers extracts called Banbury mixers to produce a dark rubber mix. Consequently, the mixture is then cooled in a special mill to improve its composition. The tire features are threaded into its properties to give a fished product (Kurt 18). Consequently, the finished product is compressed and cured with rubber molds to engrave the manufacturer’s identity and brand differentiation. However, the life cycle generates concern for environmentalist. Used tires cause environmental hazards and pollution if not properly managed. The effects of these challenges influenced the recycle measures of environmentalists and standard control agents (Mojtowicz 8).
As a result, several recycling designs have been invented to reduce the health challenges of used tires. The procedures include collection, transporting, sorting, shredding, steel removal, grinding, testing, and distribution. However, these methods can be expensive compared to the compaction machine and clamping system. This report will describe the aims, technical information, problems, design concept, recycling procedures, and health benefits of recycled tires. The paper will explain the features of tire compaction and clamping system.
Aims and Objectives
Tires are manufactured with rubber, steel, and synthetic materials under pressure and gravity. As a result, the product becomes difficult to manage under normal conditions. The aims of the tire design machine include time efficiency, cost reduction, hazard control, raw materials availability, and waste control. However, the paper will focus on the tire compaction machine and clamping system Thus, an effective clamp and the compaction machine will reduce the menace of tire combustion.
Benefits of a Tire Compaction Machine
The products of tire conversion include mouse pads, rubber mulch, car mats, carpet underlay, parking curbs, speed bumps, roof shingles, and soaker hoses. Thus, an effective design of the tire compaction machine will save oil, energy, reduces pollution, influence reuse, improve landfill mass, reduce health problems, and emissions (Murugan 2760).
Technical Information
The compaction machine uses force, size, and pressure design to recycle waste tires. However, an effective clamp system must accommodate the size load and speed markings of used tires. The paper will summarize the size, load index, and speed markings of different tires. Tire production stipulates safety requirement using specific recommendations. The technical information about tire includes size, pressure, speed, load index, and force. As a result, manufacturers engrave the information on each product as required by law. The information provides guidance and tire options for different vehicles. This paper will summarize the load index, speed markings, and pressure chart of various tire products.
Please note that the speed ratings indicated the load capacity per tire. Thus, the value of each speed marking must be referenced to standard guidelines.
The load index measures the tire capacity to resist pressure, force, and speed.
An example for 13 rim tire
Problem to Solve
To mitigate the effects of used tires in the environment, tire compaction and clamp design are recommended to solve the problem. The effect waste tires include pollution, health challenges, fire outbreak, storage space, transportation cost, and human safety.
Design Concept: Compaction Machine and Clamp System
The punch and die device uses pressure, and forces to bear and hold waste tires. The features of the punching device include a stripper, tire punch and the die. However, the clamp machine maintains a punch sequence and selection to improve the cut registration. The die punching machines can be used for die cutting, rubber shredding, embossing, and creasing jobs. Thus, waste tires are clamped and pressurized into various sized to ease transportation. The punch design depends on the manufacturer’s modification. However, manufacturers embed staples, clamps, flywheels, and cutters in the punch design to improve performance. The punch design can be mechanical, electronic, or pneumatic (Owen and Mervyn 790).
The design concept depends on its use and concept. However, the bulk density of each machine determines its use. Thus, an efficient compaction machine must pressurize and shred many tires to reduce labor time. The design is controlled by replaceable baled to boost efficiency. Consequently, the waste tires are mounted on a motorized piston which is driven by a pneumatic machine (Ozden 893). The cutter is placed inside the clamp wheel, which rotates at intervals to improve the cutting edge. The die section of the clamping system engages the cutting edge to regulate the piston’s balance. However, the piston mechanism engages the pressurized rotation of the die to reinforce the cutting motion of the punching machine.
Health and Safety
Tire shredding require careful monitoring and implementation program. The tire components can cause health problems to the operator if not properly managed. As a result, the operator must wear a protective vest to avoid shredding hazards. Consequently, the synthetic components released during cutting must be cleaned to avoid environmental pollution. The machine components must be cleaned and lubricated daily to avoid rusting. The work area should have proper ventilation to avoid toxic inhalation and heart attack. However, a safety aid box must be labeled and position at strategic points.
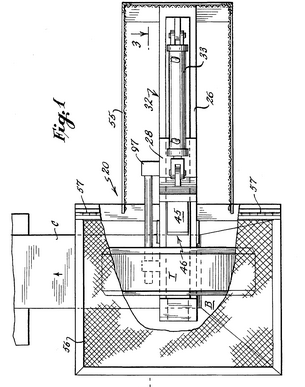
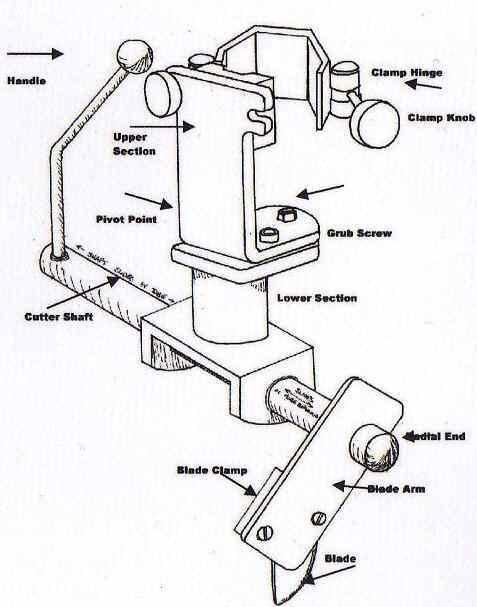
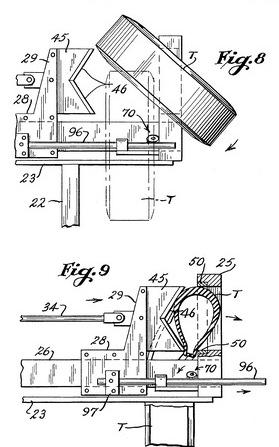
Works Cited
Ahmet, Turer 2012, Recycling of Scrap Tires. Web.
Kurt, Reschner 2011, Scrap Tire Recycling; A Summary of Prevalent Disposal and Recycling Methods. Web.
Mojtowicz, Auisch. Pyrolysis of scrap tires: Can it be profitable? Web.
Murugan, Suram. “The Use of Tyre Pyrolysis Oil in Diesel Engines.” Waste Management 28.12 (2008): 2743-2749. Print.
Owen, Rosenboom and Mervyn Kowalsky. “Reversed In-Plane Cyclic Behavior of Posttensioned Clay Brick Masonry Walls.” The Journal of Structural Engineering ASCE 130.5 (2004): 787-798. Print.
Ozden, Ben. “Seismic base isolation using low-cost Scrap Tire Pads (STP).” Materials and Structures 43.6 (2013): 891–908. Print.