Introduction
ABC Company is a large American company engaged in the production and manufacture of truck transmissions in the wider American truck market. The company is currently undertaking a reorganization process that will see it outsource some of its manufacturing process to Europe. This will happen as part of a piece part operation that will see the manufacture of gears and shafts shift to its sister plant in Europe. The company’s previous operations saw the company manufacture gears and shafts for its primary market but the re-organization process to be undertaken will involve the manufacture of new equipment in its European plant (apart from the gears and shafts).
To achieve this objective, the company seeks to move into a cell manufacturing plant which outlines the project for this study. This project has a six-month deadline to be completed on 24th May 2011. I have been appointed as the project manager and my task is to ensure the swift transition into the cell manufacturing setup. In light of this task, I have identified five specific areas of study encompassing new plant equipment, new suppliers or existing suppliers increased supply, human resource issues, plant layout, and production planning, and an overall plan of the entire project (encompassing the above four issues). These issues provide the bedrock to this study because they will outline my plan of action of how they ought to be managed.
Plant Layout and Production Planning
The plant layout of the project implies that the dispositions of equipment, manpower, and such like resources need to be done in a good manner (MBA Knowledge Base 2011, p. 1). In ensuring the project has a good plant layout, the design of the building ought to be carefully developed, such that, it is complementary to the location and movement of the work to be undertaken. This strategy is important in eliminating any possible instances where employee frustrations (as a result of congestion, waste, and inefficiencies) are evidenced. Since coming up with a good plant layout involves a lot of complex procedures that may incorporate aspects to do with economics, architecture, business administration, and the likes; the production manager must oversee the activities under this task (MBA Knowledge Base 2011, p. 1). This is important because the production manager is empowered with the knowledge of how to factor in economics, architectural skills, and the likes in the plant layout.
Possible problematic areas that can be evidenced in this task involve over-sophistication of the plant layout, such that, it becomes difficult for other project staff to work with. Another problem area is the development of ineffective plant layouts where all aspects of the project are not encompassed. With such risks abound, the company must seek a second opinion before the adoption of the plant layout developed by the production manager. Most importantly, the developed plant layout ought to be communicated to the project manager and the managerial committee because the project manager has the overall oversight of how the project is to be carried out. The managerial committee will assist in evaluating whether the plant layout is complementary to the vision and goals of the organization. The plant layout for this project will be as follows:
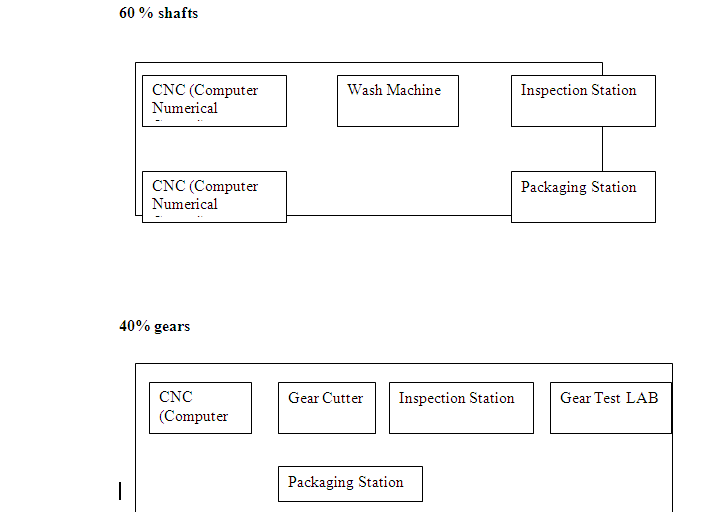
Considering this task is coupled with the production planning process, the goals of the organization must be factored into the entire process because it is through the production planning process that the organization can produce output that is complementary to the organization’s goals. This task ought to be carried out as the first procedure in the project management process because it acts as the blueprint through which all the other project tasks will be based on. This can be evidenced by the fact that the plant layout and production planning process will be determinant on the type of plant and equipment to be sourced, as well as the human resource needed to operate the purchased plant and equipment. However, the appropriate production schedule for this project can be borrowed from the provided outline which stipulates that “the 100 employees hired should go in 3 shifts. 1 shift of 33 employees are producing shafts(cells) , 1 shift of 33 employees are producing gears(cells), 1 shift of 33 employees are packaging. They must produce cells until 31 March and then all of them concentrate on packaging, 1man (6.00am-2.00p.m) 2 man (2.00 pm – 10.00 pm) 3 man (10.00 pm – 6.00 am)”. Considering this task is the first in the project management task, the first month of October 2010 will be dedicated to accomplishing this task.

New Plant Equipment
Getting new plant and equipment will be the second step to be undertaken in the project management process. This role will be undertaken by the company engineers because they have the required knowledge for picking out the appropriate plant and equipment for the job (Robinson 2010). This task will have to be done after liaising with the company management and the suppliers. The company management will be important because they will determine the financial capability of the company to source the best equipment and plants for the job (Bell 1995, p. 84). The suppliers on the other hand will be vital in this task because they will establish whether the procured plant and equipment is available, and at what time can they be delivered?
The number of machines to be bought will be seven and they will be comprehensively installed, to sum up, three parts of the production process. These parts will constitute the manufacture, assembly, and storage points. This task will be carried out within three weeks to give ample time to other project officers to complete their tasks as well. Three weeks is deemed the appropriate schedule because some plant and equipment parts may take long before they are delivered to the project site. Other considerations include the amount of time the company will take to carry out a thorough market survey to get the best suppliers and goods in the market (at a convenient cost). In detail, the first week will be dedicated to sourcing; the second week to making the purchase (after consultations) and the third week will be set aside for delivery. The following Gant chart best depicts this situation:

The possible problem areas to be encountered in this task are delays and the purchase of wrong or defective plant and equipment which can significantly affect the overall completion or quality of the entire project (Sharma 2010, p. 2). To avoid these possible problematic areas, the right project staff needs to be assigned the duty of purchasing the right plant and equipment. The staff also needs to have the required knowledge and experience in procurement procedures so that chances of sourcing the wrong type of equipment are significantly reduced. To avoid the problem of significant delays from the suppliers, the company will have to source reliable suppliers who have a good track record of supplying equipment in good time. A background search of suppliers therefore ought to be undertaken. However, the company can also rely on some of their most trustworthy contacts to recommend the best suppliers in the market.
New Suppliers and Existing Suppliers
Fox (2010) notes that getting good suppliers is not an easy thing and there is no shortcut to finding a good supplier. He also, notes that companies should do background research on their suppliers. Developing a good relationship is also key in getting a good supplier and therefore the procurement department should strive to develop good relationships with new and existing suppliers. The price offered by given suppliers is also important in choosing the right suppliers because some rogue suppliers may take advantage of the company by charging exorbitant prices for their goods.
Any organization needs to have back-up suppliers, just in case the recommended ones fail to deliver. Though this may be an expensive exercise, the company needs to ensure that the project runs in good time and is done in the right way. This is one strategy through which the company can use as a timing control method. Sourcing back-up suppliers should especially be done in situations where the suppliers’ goods are critical for the success of the project. Fox (2010) affirms that when suppliers are mandated to supply essential goods for the success of the project, it is essential that at least two or more suppliers be sought to provide the same good and services incase the recommended suppliers fail to meet the project standards. In this context, Fox (2010) also explains that “Having two suppliers also puts us in a better negotiating position when it comes to discussing important issues such as time to manufacture, the quality of components and workmanship and price” (p. 4).
Getting new suppliers (as a distinct project task) will be carried out by the purchasing manager as the primary person mandated to seeking or retaining new and existing suppliers. However, the company’s managerial team also needs to be briefed on the activities carried out by the purchasing manager, but more importantly; the project manager needs to be briefed by the purchasing manager on the conduct and progress of the suppliers’ activities. New suppliers will be identified after a comprehensive interview process to select the best. However, before the ultimate decision to choose the best supplier is done; we will visit their sites, recommend the provision of sample goods, and then after satisfactorily evaluating our options, we will negotiate the price of goods delivery (from the most appropriate supplier). Though some supplies may take longer than the project recommends (more than six months) to deliver the goods, we will ensure that the goods procured take a shorter time. This will be done through the inclusion of the most efficient and fast delivery methods available to us (even if the costs may be high). Secondly, we will be able to do this by awarding the supply tender to the supplier who is near the project location. The schedule for this task will be two months where both months will be used for the same purpose. The following Gantt chart depicts this situation:

The problems to be anticipated in this task majorly resemble the problems anticipated in the sourcing of plant and equipment. It is at this project stage that the issue of delays becomes quite evident, in the sense that, suppliers may disappoint from time to time. This is the reason why it is recommended that a back-up group of suppliers is sourced. The strategies to be adopted in mitigating these problems are also the same as those evidenced in the sourcing of plant and equipment.
Human Resource Planning
The task of sourcing the right personnel for the project management process will be the fourth stage in the project management process. This is because the human resource staff to be sourced will be essentially hired to operate the plant and equipment sourced. This task will essentially be done under the watch of the human resource manager and the human resource department (Lukey 2006, p. 163). Again, the human resource manager needs to brief the company’s managerial team and the project manager on the progress of recruiting and training the human resource team. Briefing the management will be important because the managerial team essentially determines the financial resources to be used in the recruitment and training of new staff. Briefing the project manager will also be important in ensuring that new and existing staff correctly fit into the project goals and aims.
Getting the right staff for a given task is not an easy job, however, for this study; the project management process requires a total of one hundred new employees. To get the right staff, therefore, the company should adopt a rigorous recruitment and selection criterion that factors in the skill requirements of the new staff, as well as the competency requirements of the job in question. This task will be undertaken from the start of April and will end in May. This will be done in form of advertising whereby at the end of May, interviews will be carried out to weed the best from the worst. After this task is undertaken, qualified employees will be required to start work immediately but ten out of the one hundred new employees will be required to go to Germany to be trained; after which they will be required to share their skills with the rest of the team. The following Gantt chart depicts the schedule:

The problem areas to be anticipated in this project management process include poor time scheduling (to mean the recruitment and training of new workers will surpass the two-month deadline). Secondly, there is the risk of incurring more financial costs than those allocated. This may result from inflation or employee demands that will prompt the organization to rethink its human resource practices. Thirdly, the company faces the risk that some of the newly recruited employees will opt to fall out of the program. In mitigating financial risks, the company can resort to drawing up a contractual agreement with the employees to outline their financial expectations in detail so that each party is aware of what to expect. Secondly, in ensuring the task runs in the stipulated schedule, the human resource manager will have to be availed with their required tools in time (to start the process in good time as well).
Secondly, a succinct schedule needs to be drawn up by the human resource manager to guide the activities of the other human resource department staff so that the entire process fits into the two-month schedule. It will also be an important procedure to flow a given project precedent set by other human resource teams that have been able to complete such tasks in a given time. This strategy will expose the human resource team to the challenges to expect in the process and how they can avoid them (to beat the schedule). Considering there is the provision of time to train people, there will be, say, a month of training which will imply that no production will be taking place at the time. There will also be a month to install the equipment and for servicing purposes, we will require an additional month, plus 20-25 Gear Cutters and 50 CNC (some require 2 years to install, some 3 months therefore we should check carefully). We will take gear cutters that require the shortest time to install. Lastly, in mitigating the risk of some of the employees falling out of the program, the company should recruit more employees (than the required number – 100) so that the excess number can be used to replace the ones who have given up.
Overall Gantt Chart
The overall Gantt chart will encompass all the above time schedules. Comprehensively, it will be as follows:

Network Diagram
The network diagram showing the respective dates of project completion is as follows:
Conclusively, the scope of my job will be defined by the roles of a project manager where I will coordinate most of the functions of the project. Most of the functions to be undertaken in the project are to be effectively managed to ensure the project falls within the required schedule. The project management process will also be undertaken to ensure the quality of the project is within high standards. To ensure the project is effectively managed various tools of analysis such as risk management tools and following previous project precedents will be used. To effectively deal with any human resource issues in the course of undertaking the project, we will also completely vet the employees to work in the project so that high standards of cooperation will be observed.
References
Bell, M. (1995) Trade Technology And International Competitiveness. London, World Bank publications.
Fox, M. (2010) Step 3: Have Back-up Suppliers. Web.
Infonet. (2011) Gant Chart. Web.
Lukey, T. (2006) Software Project Management fro Dummies. New York, For dummies.
MBA Knowledge Base. (2011) Plant Layouts. Web.
Robinson, J. (2010) Steps to Buying Your Next Concrete Plant. Web.
Sharma, R. (2010) Critical Path Examples. Web.