Executive Summary
The process of production is one of the most important practices in any organization. It should be managed in the most efficient way to assure the organization of production. Operations management is the process by which the production process is managed in an organization (Greasley 8). Some of the most important areas that organizations should effectively manage include the supply chain and the quality of their products.
Some of the other measures that should be taken include adequate designing of the organizations’ production processes and planning of their inventories. Toyota and Coca-Cola companies are some of the most successful organizations in the world, with their operations internationally being recognized. These companies have adopted different ways of managing their supply chains to ensure quality management in their operations.
Proper operations management should ensure that the materials used in the production process are available and adequately utilized. The product design should also be incorporated in the process that ensures collaboration with suppliers and the end-users. Another function in operations management is communication, which should be carried out in ways that are in line with the organizational goals and objectives (Lussier 27).
To understand the importance of operations management in organizations, it is necessary to compare companies with working policies on the same. The following essay is a case study of Toyota and Coca-Cola companies. The study presents quality administration and supply chain management methods that each company applies in its operations management. A comparison of the two is also made.
Operations Management: Toyota vs. Coca-Cola
Brief Company Backgrounds and Profiles
Coca-Cola Company
Coca-Cola Company is the leading manufacturer of soft drinks in the world. It also leads to the marketing and distribution of these non-alcoholic drinks. There are over 3300 brands of drinks produced by the company and its partners. Its operations span over 200 countries and territories. The company has managed to establish itself on the global front. As such, it is a multinational business located in many parts of the world with its headquarters in Atlanta (Smith 78). Some of the other areas that the company works in partnership with the locals of the area in which it operates include health, education, leisure activities, as well as environmental conservation.
The company was founded in 1886 in Atlanta, with the first glass-bottled beverage being introduced in 1899. The company continued to improve with the development of the various shapes of bottles. The expansion rate of processes and packages was rapid in the 90s (Smith 79). Quality management was emphasized in the mid-90s due to the prevailing competitiveness need. The company remains one of the most successful multinational businesses, with billions of dollars in profit every year.
Toyota Company
Toyota Motors Corporation (TMC) is a Japanese company that specializes in the manufacture and sale of various models of cars in different countries. The company was founded in 1937. It started as a small company just like any other at the time, with the man responsible for its development being Akio Toyota. Before the start of operations, Akio had conducted adequate research in the markets and the industry. He only embarked on its development after satisfaction that it was a credible investment.
1950 was significant for this company, having manufactured more than 100,000 vehicles for the local and international markets. The company also started exporting its manufactured cars to the United States after this year. This step saw its rapid expansion. The sale of its cars had reached over a million by the end of 1960. The main offices are located in Japan at a place called Toyota City in Aichi. The company is also involved in other ventures such as the financial services that it offers to various clients. The company is also a leader in terms of the number of vehicles produced every year.
Quality Management
Quality management in the production process is essential in the performance of an organization. It involves ensuring that all products are developed with high standards and in line with the achievement of the organizational objectives. It is important to note that everyone in the organization is responsible for quality maintenance. Operation management has four major objectives: quality, delivery, cost, and flexibility. The organization should ensure that it meets customers’ expectations or possibly exceed them to satisfy them and eventually win their loyalty to become a competitive advantage (Rose 69).
Coca-Cola Company
Although other industries are in place to make drinks, just like the Coca-Cola Company, it is much evident that Coca-Cola is far much ahead of all of them in terms of customer attraction and retention. The finding is sufficient for one to realize that there must be some unique features that the company has, which have helped it remain at the top despite the high competition. These features include product quality, product packaging, and product advertisement amongst others. For instance, the industry in which the company operates is sensitive in terms of quality, as health concerns are raised if the quality is not maintained.
The first detailed attempts to ensure maximum quality management in Coca-Cola date back to 1995 because of competition and the desire to satisfy the local markets and/or maintain consistency in the company’s products. The quality assurance policy was named The Coca-Cola Quality System (TCCQS). The system has grown to be the branded quality management system for the company (Smith 78).
TCCQS involves the continuous application of the most current practices in the production process, with these practices being geared towards the production of quality products. TCCQS is also focused on the satisfaction of customer needs. This strategy is guided by the principle that the organization is a global symbol of quality. TCCOS is also tasked with the management of environmental stewardship and safety in the organization (Smith 78). The system constantly changes to ensure that it is relevant. Some of these changes include simplification, modernization, standardization, and alignment with other external quality assurance organizations and the provision of external services such as training in quality management (Smith, & Melissa 79).
TCCQS has a working framework called Evolution 3, with quality assurance being the main guiding principle. This model also constitutes other facets such as safety and environmental control. Four basic layers of promise, namely policy, assurance, and control (Smith 79) define it.
The model is also constructed with the basic requirements as required by other professional quality assurance bodies such as the Global Food Safety Initiative (GFSI) and the International Standards Organization (ISO) (Smith 79). The safety standards are also aligned with those required by the OHSAS and the SGS-ICS. Some of the processes that the policy has contributed to ensuring their safety include manufacturing, cleaning, and sanitizing processes. The company has also embarked on the simplification of organizational safety standards, which are distributed in the relevant employees and stakeholders, with adequate documentation of all safety processes.
Toyota Company
Toyota has a quality management policy in place. This policy is anchored on three different levels of the organization. The levels at which quality is guaranteed in the organization include the customer level, the management level, and the company level. These levels are important in the management of quality at Toyota. They are the main platforms that it uses in its operations. At the customer level, Toyota is actively engaged in the collection of feedback and other information on customer satisfaction. It carries out surveys on the quality of vehicles that it sells. If the vehicles are not of good quality as per the organization’s standards, they are recalled back, thus leading to loss of revenues. The company also makes different models, which suit the needs of its customers based on the feedback that they can obtain from them.
Vehicles are also scrutinized and tested rigorously after they are manufactured to rule out any faults. At the employee level, training is the most common tool that the company uses to ensure the products it produces are of high quality. The imparting of skills to employees is recognized as one of the main ways in which organizations can improve the efficiency of their operational processes and in effect the quality of their goods. Toyota has invested in this strategy.
At the innovation level, Toyota has invested in research in the development of vehicles that are safe whose standards are high and competitive on the international market. The company spends a significant part of its budget on new technology and innovation. It is constantly introducing new models, which are better in terms of quality and phasing out the older models. Despite all these processes, the company has had to recall some of the models in the past including the recall of more than 600,000 Tacoma trucks manufactured between 2005 and 2009. This move is reported to have cost the organization billions of dollars.
Comparison of Quality Management
Quality management is essential for both companies. The operations manager insists on quality production. Quality at Toyota is guided by the word KAIZEN, which means continuous and consistent improvement. Its operational management strategies are applied within three major levels. The company aims to produce quality products to improve its production each day. The company has had major setbacks in the past, with some of its products being recalled from the market-leading to significant losses. The company has therefore invested in quality assurance within the various levels.
Lakhal, Pasin, and Limam observe how quality management is important in terms of sustaining the operations of an organization (625). It also creates value for stakeholders. Quality management in an organization may be necessary to meet or even exceed customer needs, thus ensuring exemplary performance.
The Coca-Cola Company is also committed to ensuring quality production. One of the most significant factors in the success of any organization in the food and beverage industry is quality. An organization has to produce quality products to succeed in a highly competitive industry. In ensuring quality, the company establishes strong governance while strictly complying with the applicable regulations and standards.
Products are manufactured according to the given specifications that are available via a quality management program that is used to measure the quality of operations. Policies are strictly followed in production. The program enables Coca-Cola to maintain the highest standards in its production, as well as safety, quality, environmental, and safety standards. Also, the products have to undergo testing in modern laboratories where they are checked using appropriate technologies and state of–the art methods available in the Coca-Cola Company. Quality at the company is maintained through The Coca-Cola Quality System (TCCQS).
Supply Chain Management
Supply chain management involves the management of all stages involved in moving the products of a company from the manufacturer, all through to the final consumers. It is the chain through which goods move from the storage of raw materials, through manufacture or work in progress, to finished goods, and finally to the consumer point.
The Coca-Cola Supply Chain Management
The foremost soft drink company has developed an effective supply chain management that has enabled it to be the leader. The supply chain management utilized in the company is focused on the end-user and the delivery of quality services to the customers. The supply chain developed ensures that its products are at their destination at the required time and the right quantity. Coca-Cola Company’s supply chain includes the suppliers, the manufacturers, the distributors, retailers, and the final consumers of the beverages (CSC Report 2).
Despite its dominance on the international front, the company continues to invest and apply innovation in its supply chain. The company has a unique supply chain. It only produces syrup, which is later sold to the other subsidiary companies elsewhere in the world. These companies are responsible for the canning and distribution of the finished products within the territories that they have been allocated. The bottlers finally sell the products to retailers who sell this to consumers. The cost of suppliers in the supply chain is controversial due to the secrecy surrounding the manufacture of the syrup. The downstream operations of the company are however run as a franchise, with the independent bottlers being responsible for the sales of the company. They also distribute the final product as stated above.
Toyota Company Supply Chain Management
As has been witnessed by Coca-Cola, Toyota is dedicated to its supply chain management. The aim is to ensure satisfaction for all major stakeholders. The supply chain management focuses on variety, velocity, variability, and visibility. The company ensures the availability of a variety of options from which customers can choose. Variety is based on market demand, as well as the company’s operations. The company has been able to produce vehicles that are suited to the needs of every customer. Velocity, on the other hand, ensures that there is a steady and consistent flow of goods via all processes involved in the supply chain.
Under variability, all inconsistencies are managed with caution to cut costs and maintain high quality. Visibility serves to ensure that all processes are transparent to the relevant authorities. This facilitates maintenance, continuous learning, as well as quality improvement. Toyota’s supply chain is efficient and effective. It ensures that all processes are observed. It also aids in maximizing customer satisfaction (Iyer, Seshadri and Vasher 35).
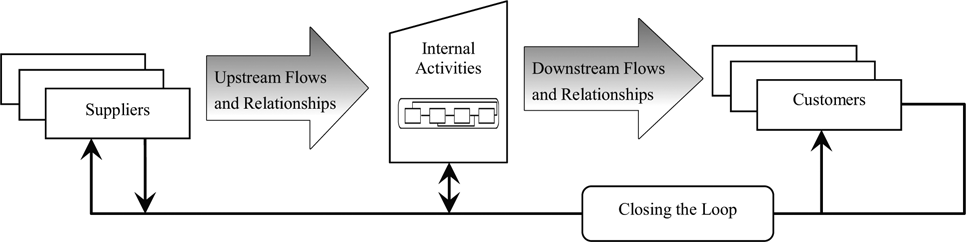
Comparison of Supply Chain Management
The two companies have adopted a unique supply chain to complement their international accreditation. Toyota has a simple supply chain consisting of suppliers, manufacturers, and retailers who are located in various parts of the world. The company also utilizes a lean supply chain, which has been developed over the years to reduce wastage, improvement of Value Added (VA) services, and reduction of the Non-Value Added ones (NVA). Coca-Cola, on the other hand, has a long supply chain with many players in different parts of the world.
Both companies have adopted effective supply chain management strategies as discussed above. These strategies are focused on the end consumer of their products. For Toyota, the supply chain is managed from the suppliers onwards through a simple and inclusive strategy. Coca-Cola, on the other hand, has a complex supply chain. This exists in two levels, both upstream and downstream (CSC Report 2). The supply chain is therefore difficult to manage and control, with the upstream chain affecting the services provided to consumers.
Conclusion
In conclusion, the adoption of proper operations management is an important factor in the success of an organization. Some of the important factors include proper management of process design, inventory planning, quality, and the supply chain. The paper has discussed some of the strategies in place for the quality and supply chain management in the two leading global firms, namely Coca-Cola and Toyota. Both have an effective quality management program in place, although failures in Toyota have cost it much through its instances of recalling some of its products. The companies also have proper supply chain management policies in place as factors in their success.
Works Cited
CSC Report. Coca-Cola supply chain management success story. London: Sage, 2013. Print.
Greasley, Andrew. Operations management. Los Angeles, CA: SAGE Publications, 2008. Print
Iyer, Ananth, Sridhar Seshadri, and Roy Vasher. Toyota supply chain management: A strategic approach to the principles of Toyota’s renowned system. New York, NY: McGraw-Hill, 2009. Print.
Lakhal, Lassaad, Federico Pasin, and Mohamed Limam. “Quality management practices and their impact on performance.” International Journal of Quality & Reliability Management 22.6(2006): 625-646. Print.
Lussier, Robert. Management fundamentals: Concepts, applications, skill development. Mason, OH: South-Western/Cengage Learning, 2009. Print.
Rose, Kenneth. Project quality management: Why what and how. Boca Raton, FL: J. Ross Pub., 2005. Print.
Smith, Melissa. “The hard truth about soft drinks.” Natural Food Merchandiser 26.3(2005): 76-78. Print.