Background
Activity-Based Costing (ABC) is a useful accounting method that enables managers the collection, analysis, and evaluation of a business’s investment and expenditure habits. The aim of such activities is to streamline production processes and reduce costs (Syreyshchikova et al., 2021). Specifically, ABC saves the company’s resources such as time and money to increase profitability. ABC’s basic mechanism involves the assignment of costs to products based on manufacturing overhead, unlike traditional methods that base costs on materials, labor, or marketing overhead (Hansen, Mowen, & Heitger, 2021). Therefore, the method is most efficient and logical where overhead costs are not even across the products. A good example is in specialized production where low-volume products require minimal machine hours and several indirect costs. Such products have inaccurate overhead costs under the traditional method and lead to net losses in financial documents.
ABC Implementation
Implementing an ABC system requires resources and time, as it is a complex process. It begins with breaking down business activities into their basic components. The most manageable approach is to select candidate products for the ABC system or begin with a single product (Quesado & Silva, 2021). Once the method is proven beneficial to the company, other products are then introduced in a gradual manner. For each product, departments and individuals must collaborate to determine direct and indirect costs associated with every task. Managers can utilize special software to organize the ABC process or hire consultants (Wegmann, 2019). Figure 1 summarizes all the steps typically followed in establishing ABC (Syreyshchikova et al., 2021). Nevertheless, the process of ABC implementation differs from one company or industry to the other due to differences in products and cost drivers.
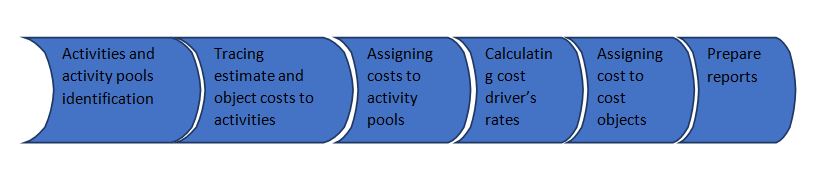
Total Quality Management and ABC
Total quality management (TQM) requires managers to continuously improve business processes and activities. A contemporary approach to successful quality management entails production cost reduction and improvement of quality (Quesado & Silva, 2021). Some established elements of TQM include the reduction or elimination of non-value-adding activities, a flexible workforce, streamlined production flow, supplier cooperation, reduction of lead times and defects, and efficient equipment maintenance. ABC provides an effective mechanism for identifying activities that do not add value, avenues for cost reduction, and identification of workforce and equipment problems (Syreyshchikova et al., 2021). Managerial accounting introduces the calculation of variance to determine the difference between actual and budgeted expenses and revenue. Similarly, ABC will reveal the cost drivers for every product and enable the identification of quality failures. Continuous activity analysis in TQM seeks to eliminate tasks that do not add value to the final product (Quesado & Silva, 2021). Managers can then check the associated costs to determine the impact of such eliminations on revenue and pricing. Gradually, the process moves from quality and cost control to quality building-in and cost reduction.
Supply Chain Costing and ABC
Managerial accounting includes business logistics costs and their optimization for efficiency. Managers can use ABC to improve logistics cost allocation to various objects. Logistics is the process of delivering the right product to the customer at the lowest cost, right condition, and desired time. ABC is the most effective accounting method for gathering and analyzing all the cost data related to logistics (Duran & Afonso, 2020). Traditional costing systems allocate costs on a volume basis, making it impossible for managers to determine true consumption costs. Integrating ABC into the supply chain requires a definition of the relationship between logistics costs and activity-based costs. For instance, some main logistics costs include order processing, transportation, inventory carrying, and warehousing costs. Figure 2 summarizes the basic steps in integrating ABC into supply chain as presented by Duran and Afonso (2020).
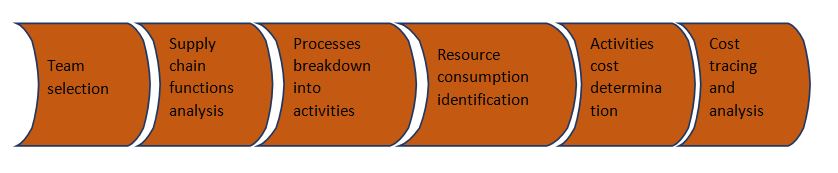
Activity-Based Budgeting
From ABC, managerial accounting can benefit from utilizing activity-based budgeting (ABB) instead of traditional budgeting. ABB is a rigorous method of researching, analyzing, and recording every cost-incurring activity in a company with the aim of creating efficiency and lowering overall costs (Wegmann, 2019). Traditional budgeting would only adjust a previous budget based on business changes or inflation. ABB, however, involves thorough scrutiny of every activity that incurs a cost to the company. Continuous scrutiny produces higher profit margins and decreases costs for most activities. It begins with the identification of cost drivers, which are activities that incur revenue or expense for the business (Wegmann, 2019). It proceeds to the determination of the number of units per activity identified in the first step above. Finally, the cost per unit is calculated and utilized in budgeting. Managerial accounting must involve ABB to equip managers with the latest and most efficient budgeting method.
Theory of Constraints
Theory of constraints (TOC) is another alternative to traditional costing that managerial accounting should include for managers’ preparation. When ABC is applied alongside TOC, there are contradictory results. Therefore, managers must know when to utilize each of these paradigms for optimum profitability. TOC focuses on improving performance with the aim to increase earnings today and in the future (Mabin & Balderstone, 2020). Unlike ABC, which emphasizes costs, TOC emphasizes throughput, making the two paradigms conflicting. Figure 3 shows the five key steps of implementing TOC adapted from Mabin and Balderstone (2020). ABC can be applied alongside TOC but for different uses and using distinct methods. Managers can utilize TOC for short-term gains, especially in eliminating constraints to improve production or performance. However, ABC is important for the long run as it continuously improves cost management.
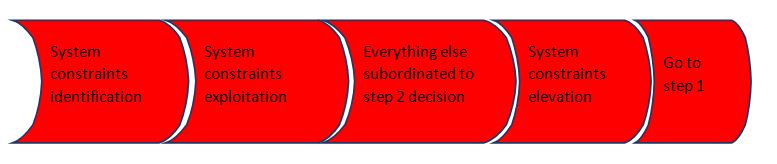
ABC Advantages
ABC provides managers with accurate and realistic production costs for particular items, allowing them to make effective business decisions. Making such informed decisions ensures that cheaper production means are utilized, quality materials are purchased, and product pricing is optimum (Hansen, Mowen, & Heitger, 2021). Data gathering processes also improve because management members are directly involved in identifying costs for every activity. If a manager has products that are more expensive in their portfolio, ABC facilitates the assignment of specific overhead costs. When applying ABC, the manager can separate expensive products from the rest and allocate a befitting budget. A similar procedure is followed during pricing to ascertain that each product group is sold at its best price.
Managers can measure production efficiency for each product and initiate improvements where necessary. Assigning value to direct and indirect costs allows the manager to break down activity costs to their lowest level and influence efficiency in the production from the bottom up. ABC offers managers more accurate data to make profit projections. Traditional costing methods do not account for nonmanufacturing costs, hence providing less accurate data than ABC (Syreyshchikova et al., 2021). With such accurate data, managers make profit margin estimations and projections that are more achievable and realistic. In addition, if profit estimation shows undesirable targets, managers can transfer or lower production costs to affect pricing strategies and improve revenue margins. ABC also enables the identification of low-value and wasteful products because their profit margins are extremely less than desired. There are industries that cannot utilize traditional costing methods because of their nature of operations (Syreyshchikova et al., 2021). For example, the service industry cannot use traditional methods due to a lack of direct production costs. Managers in the service industry can use ABC to apply costs directly to the services offered, improving pricing strategies, and overall performance.
ABC Disadvantages
Managers should know the challenges of using ABC over traditional costing methods. Firstly, ABC is more time-consuming than traditional methods because costs are determined and evaluated for each product rather than dividing total costs by total units of production (Syreyshchikova et al., 2021). Products must be broken down into activities, which are then categorized into activity pools. Managers can create a specific team for the ABC process or outsource the service that should include management-level staff. Outsourced teams have greater experience and will yield better results in shorter spans of time. The process of gathering ABC data is costly and might require more resources than traditional methods. Outsourcing specialist teams and obtaining recommended software increase payroll and office expenses. However, once the system is established, it is more cost-efficient in the long term.
If the required data is not readily available for any reason, implementing ABC becomes even harder. The data and information a company keeps about production costs and processes depend on the programs and methods in use. Since ABC does not follow a traditional accounting system, most software will not have captured all the data required for the process. The ABC team will spend more time and resources to track all the necessary data (Hansen, Mowen, & Heitger, 2021). Additionally, they must train production workers and manufacturing teams on how to input the correct ABC data into the system going forward. Lastly, smaller companies with fewer overhead costs may not find ABC beneficial. They are more likely to utilize market-based data rather than internal production information.
How Managerial Accounting Helps Managers to Carry Out Business Objectives
Managerial accounting comprises the processes involved in ensuring company managers are facilitated to make the most effective business decisions. These activities are mainly data and information identification, analysis, interpretation, and communication (Jiambalvo, 2019). The data is drawn from every field of accounting but is optimized for decision-making purposes. Any information that does not support managerial decisions is not included in these accounting reports to avoid time wastage.
Types of Managerial Accounting and their Help to Managers
Product valuation and costing help managers understand the expenses or costs associated with production. Costing is the processing of determining the exact costs of producing the goods or services and includes subcategories such as indirect, direct, fixed, and variable costs (Jiambalvo, 2019). Other areas under this accounting include marginal costing and analysis, and break-even analysis. The purpose of this section is to determine overhead costs, breakeven point, cost of goods sold, and contribution margin. This type of accounting helps managers to control business expenses to increase revenue margins.
Cash flow analysis focuses on the decisions that affect how cash flows into and out of the business. The two methods of implementing this accounting type include cash or accrual basis (Jiambalvo, 2019). The decisions facilitated by this analysis ensure that a business retains enough cash for daily operations. For example, a manager will decide if to purchase a piece of equipment on cash or credit depending on the forecasted cash flows.
Inventory turnover analysis is a type of managerial accounting that involves a company’s inventory sales and replacement within a period. The analysis facilitates decisions in the manufacturing, purchasing, marketing, and pricing of goods (Jiambalvo, 2019). It also identifies expenses associated with inventory, such as inventory carrying costs. Inventory management ensures that a company does not run out of stock and does not have excess inventory to incur high carrying costs.
Accounts receivable (AR) management is another type of managerial accounting that involves managing a company’s creditors. The analysis produces an aging report that shows how long accounts have been held without payment. Managers use this information to select the accounts with high credit risks and take immediate action to recover the money (Jiambalvo, 2019). For example, the credit manager might discontinue business with customers who always pay late.
Budgeting and forecasting is another major type of managerial accounting. They focus on a business future to show their plans of operation. Traditional budgeting relied on past performance and market dynamics to project future operations. Trend analysis is the process of determining future events from historical patterns (Jiambalvo, 2019). Variances between the budgeted and actual revenues and expenses are also noted when making projections. Variances also help to make key decisions about resource allocation, equipment maintenance, and labor management. Metrics such as internal rates of return, net present value, and financial liquidity ratios are used in budgeting.
Important Managerial Accounting Reports
The cost managerial accounting report contains details such as labor, overhead, materials, inventory waste, and all added manufacturing costs. They help managers to see profit margins from a manufacturing perspective and identify any loopholes in materials usage, labor efficiency, and problems with equipment. Performance reports contain companywide, departmental, and individual employee performance during the reporting period (Jiambalvo, 2019). Problems identified in these reports must be investigated further in more specific reports, such as supervisor feedback from departments for individual employees. Unfavorable variances in sales or revenues can be investigated further in the cost reports. The accounts receivable aging report, as mentioned earlier, shows the customers who are delaying making their payments. It helps the manager to identify credit risky customers and take precaution.
References
Duran, O., & Afonso, P. S. L. P. (2020). An activity based costing decision model for life cycle economic assessment in spare parts logistic management. International Journal of Production Economics, 222, 107499.
Hansen, D. R., Mowen, M. M., & Heitger, D. L. (2021). Cost management. Cengage Learning.
Jiambalvo, J. (2019). Managerial accounting. John Wiley & Sons.
Mabin, V. J., & Balderstone, S. J. (2020). The world of the theory of constraints: A review of the international literature. CRC Press.
Quesado, P., & Silva, R. (2021). Activity-based costing (ABC) and its implication for open innovation. Journal of Open Innovation: Technology, Market, and Complexity, 7(1), 41.
Syreyshchikova, N. V., Pimenov, D. Y., Kulygina, I. A., & Moldovan, L. (2021). Hybrid model for calculating quality costs. Russian Engineering Research, 41(4), 382-386.
Wegmann, G. (2019). A typology of cost accounting practices based on activity-based costing-a strategic cost management approach. Asia-Pacific Management Accounting Journal, 14, 161-184.