Introduction
It might seem at first glance that differences between the classical and mechanical pencils are minor, to say the least. However, the former’s main issue manifests when it is sharpened – it is not reusable, with the majority of its material wasted. To address that issue, people developed the mechanical version; it required no sharpening and was overall more comfortable due to various manufacturing and design practices. These practices changed and evolved as time passed; the question this report is going to answer is how strong is the emphazis on users’ satisfaction in the mentioned practices? First, it will discuss the functions expected of the mechanical pencil and how they are incorporated into its design. Consequently, the report will focus on the manufacturing side of mentioned design parts, describing the materials, their processing and possible improvements, with the purpose of connecting the design and materials into a single manufacturing process.
Design and Materials
Design
The pencil’s design is predominantly influenced by the functional requirements (FR). According to Gopalakrishnan et al. (2018), there are nine general requirements to mechanichal pensils. First of all comes the pencil’s advantage over pen – the ability to erase the written text (FR1 – Erasing). Then, pencil needs a container for the eraser and lead (FR2 – lead storage, FR3 – eraser storage). Pencil’s lead has to be simple and reliable in manipulation; thus, it requires means for its advance, support while using, and fixation (FR4 – advance, FR5 – support, FR6 – position). Additionally, pencil should be convenient; therefore, it requires a grip and clip for holding (FR7 – grip, FR8 – clip). Finally, all components have to be accomodated in a single pencil body.
The mentioned functions are distributed between pencil’s parts that are consequently manufactured. Traditional 5-part pencil design uses the following functional distribution: eraser (FR1), lead chuck (FR2, FR4, FR5), body (FR3, FR7), lead sleeve (FR6), and clip to hold (FR8). The pencils with this design are available in the market and can be viewed in the Figure 1. However, the market availability of showcased model does not necessarily mean that it is the only design version since the required functions can be redistributed among pencil parts if needed.
Materials
Lead
Classic pencil leads are made from white clay (kaolinite) and graphite – a natural mineral, one of the allotropic forms of carbon, which has a layered structure. In its modern form, the classic pencil lead was invented in 1794 by Nicolas Jacques Comte, a talented French scientist, and inventor (Knápek et al., 2019). He developed a recipe for mixing graphite with white clay and made high-quality rods from these materials. Graphite is crushed and mixed with water and clay to make a thick paste; this paste is then fired in a kiln. Strength is achieved by heat treatment, in which the clay hardens. By varying the proportions of the mixture, it is possible to produce rods of different hardness. The addition of other materials to the manufacturing process, for example, polymers, might further increase the lead’s characteristics and variability.
Eraser
The most important raw material for an eraser is rubber. Rubber can be natural or synthetic – erasers made of both types have the same properties. Their cost-efficiency is dependent on the development of genetic engineering for the former and chemistry for the latter (Dunuwila, Rodrigo, & Goto, 2018). Synthetic rubber exists in various forms – the rubber made from butadiene and styrene is among the most common versions (Dunuwila, Rodrigo, & Goto, 2018). Natural rubber is obtained from the latex produced by the rubber tree. To become an eraser, the natural rubber must first be dehydrated from the latex, which increases the rubber content to 60% (Dunuwila, Rodrigo, & Goto, 2018). The liquid rubber concentrate is consequently turned into dry rubber sheets with the addition of acid. Finally, the erasers are formed after heating the rubber – natural or synthetic – mixed with certain ingridients, such as vegetable oil, sulfur, pumice and specific pigments.
Body
In comparison to the lead and eraser, pencil’s body has a greater influence on the design and usability. The study conducted by Inoue et al. (2021) was mainly focused on the pencil’s design; however, apart from anything else, they incorporated the pencil’s body material into their research. As a result, the urethane (polyurethane) proved to be the most preferred material. Urethane is one of the primary products of the polymer industry. It has excellent chemical stability, high elasticity, corrosion resistance, easy modification, high drug loading efficiency, and high gloss (Mazi & Esen, 2021). Because of all these properties, it is widely used in biomedical applications, adhesives, civil engineering, rubber, synthetic leather, paint industry, and automotive industry (Mazi & Esen, 2021). Urethane is usually produced in the presence of homogeneous catalysts by bulk or solution polymerization of polyols and diisocyanate (Mazi & Esen, 2021). In polyurethane technology, two types of catalysts are used: amine catalysts and organometallic compounds. The latter is less preferred because of the environmental pollution it creates due to its metal content. Amine catalysts are more preferred than organometallic catalysts despite being volatile and malodorous.
Conclusion
The mechanical pencil’s manufacturing process showcases the adaptation of cost-efficiency to user satisfaction. The pencil’s design emphasizes its functionality, describing nine functional requirements incorporated into five pencil parts. The lead’s hardness, strength, and elasticity become the variables in its manufacture, providing different types as a result. The eraser’s production is not explicitly dependent on the source of rubber; thus, it can be produced according to the most cost-efficient means of the region. Finally, despite having some productional issues, the polyurethane body of the pencil showcases high user satisfaction, which makes the urethane pencil’s design the frequent choice for production.
References
Dunuwila, P., Rodrigo, V. H. L., & Goto, N. (2018). Sustainability of natural rubber processing can be improved: A case study with crepe rubber manufacturing in Sri Lanka. Resources, Conservation and Recycling, 133, 417-427.
Gopalakrishnan, P. K., Kain, H., Jahanbekam, S., & Behdad, S. (Eds.) (2018). Graph partitioning technique to identify physically integrated design concepts. International Design Engineering Technical Conferences and Computers and Information in Engineering Conference. American Society of Mechanical Engineers.
Inoue, M., Suzuki, W., Yamada, S., & Aoyama, K. (2021). A universal design method that considers variability in user requirements: a case study of mechanical pencil design. Journal of Advanced Mechanical Design, Systems, and Manufacturing, 15(2), JAMDSM0022-JAMDSM0022.
Knápek, A., Sobola, D., Burda, D., Daňhel, A., Mousa, M., & Kolařík, V. (2019). Polymer graphite pencil lead as a cheap alternative for classic conductive SPM probes. Nanomaterials, 9(12), 1756.
Mazi, H., & Esen, Y. (2021). New, Effective and Reusable Polymeric Heterogeneous Catalysts for Poly (urethane) Production. Catalysis Surveys from Asia, 25(1), 93-100.
Appendix
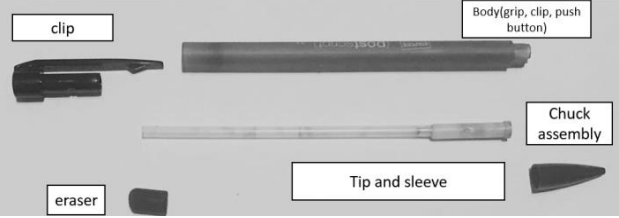