Abstract
The paper’s primary purpose is to demonstrate the impact of the digital era on the implementation of Lean Six Sigma. Moreover, it aims at defining the concepts of Lean Six Sigma and Industry 4.0 by raising the preliminary research question “How the Digital Era impacts the implementation of Lean Six Sigma?” Hence, the study uses secondary data analysis and the systematic literature review to collect and narrate the data. The sources were obtained from reliable databases for scientific research, namely ScienceDirect and Scopus. Therefore, peer-reviewed articles, proceedings, and online resources were analyzed and compared to reveal the significance of digitalization for the Six Sigma methodology. The Industry 4.0 technologies were illustrated and explained how they are used in Lean Six Sigma DMAIC. As a result, Lean Six Sigma is an essential foundation for efficiently combining Industry 4.0 technologies with business processes for organization success.
Introduction
The Lean Six Sigma methodology is currently successfully used by the world’s dominant firms in all industries. Singh and Rakhi (2018) emphasize that Lean Six Sigma is an essential business strategy to enhance the quality and productivity of companies. Nonetheless, the continuing and emerging technological trends are reshaping business processes and presenting new development opportunities. Titmarsh et al. (2020) highlight that Industry 4.0 offers expanding accessibility, data availability, and growing IT capabilities. Thus, the paper identifies the Lean Six Sigma and Industry 4.0 concepts and discusses how organizations can combine them. Consequently, the latest development and impact of digitalization on the Six Sigma implementation are investigated.
Literature Review
Lean Six Sigma
Notably, Lean Six Sigma manages the blueprint and advancement of products and processes. Lean Six Sigma originated from two terms, ‘Lean’ and ‘Six Sigma’ (Six Sigma Daily, 2020). Consequently, ‘Lean’ refers to a methodology developed by Toyota for any standard process enhancement via determining and removing waste in the industry (Silantyev et al., 2019). Hence, ‘Six Sigma’ was created by Motorola; this method is applied for recognizing and extracting the root causes of faults and errors employing variation reduction in business manufacturing and processes.
Thus, the combination of two methods helps firms to refine business processes. Prasad et al. (2020) highlight that Lean Six Sigma focuses on operations and activities which make products or services more valuable; the remaining is examined as waste. Singh and Rakhi (2018) justify that Lean Six Sigma can be used in various industries, such as manufacturing, finance, education, health care, and human resources. Lean Six Sigma contributes to increasing organizational knowledge by addressing crucial issues in order to allow managers to consider better decisions (Juliani & de Oliveira, 2020). Based on Yuen et al. (2016) and Timans et al. (2016), the considerable advantages of Lean Six Sigma include reduction in inventory, error-free processes development, productivity enhancement, and customer satisfaction growth. According to Silantyev et al. (2019), the Lean Six Sigma term is associated with Continuous Improvement steps, namely Define, Measure, Analyze, Improve, and Control, as shown in Figure 1.

Consequently, the ‘Define’ step is characterized by specifying the project’s problem statement and objectives, obtaining customer information and understanding their needs, establishing team responsibilities, and alleviating project risks. The second step, ‘Measure,’ refers to determining cause and effect connections between process inputs and outputs, calculating performance metrics, and conducting a cost-benefit analysis (Silantyev et al., 2019). Thus, during the ‘Analyze’ phase, companies identify and verify potential root causes through investigational analyses. The fourth initiative, ‘Improve,’ is associated with planning, designating, and applying tools to eliminate waste. Finally, ‘Control Roadmap’ is created to enable outstanding success, reveal opportunities, and complete the business case.
Thus, through using DMAIC initiatives, a company can remarkably improve processes and increase value for customers. Antony et al. (2017) indicate that Lean Six Sigma should be seen as one of the most superior and reliable business process enhancement methodologies. Nowadays, many companies and organizations around the globe use Lean Six Sigma to achieve success. The future of Lean Six Sigma depends on Industry 4.0 and innovative technologies.
Industry 4.0
Industry 4.0 refers to the evolving technologies which offer new business opportunities. The critical characteristic of Industry 4.0 is that it integrates innovative technologies and changes the traditional ways of business operating (Six Sigma Daily, 2020). Moreover, Industry 4.0 technologies provide the real potential to increase the influence of Lean Six Sigma in the manufacturing field (The Manufacturer, 2018). Silantyev et al. (2019) acknowledge the fundamental technologies that formulate Industry 4.0 are Internet of Things, 3D Printing, Drones, Artificial Intelligence, Virtual Reality, among others, as illustrated in Figure 2 below.
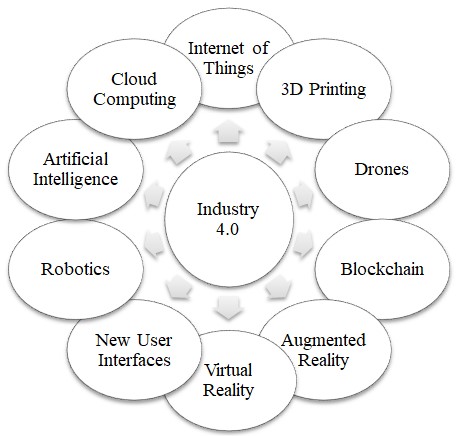
Additionally, companies can use these technologies in business, manufacturing, and transactional processes to introduce improvements. The digital evolution, namely Industry 4.0, is modifying the way organizations operate. For instance, Industry 4.0 upgrades process integration and product connectivity and assist firms in achieving better performance (Dalenogare et al., 2018; Ghobakhloo, 2020). Moreover, new technologies are changing industries’ focus from mass to custom-tailored production. Essentially, the digitalization of business processes is the driving force behind a company’s success.
Research Methods
To answer the preliminary research question “How the Digital Era impacts the implementation of Lean Six Sigma?” the secondary data analysis and the systematic literature review were deployed as research methods to collect and narrate the data. The research goal was to evaluate peer-reviewed articles published in the last five years and credible online resources to ensure credibility. Engin et al. (2020) claim that a systematic literature review is a process of searching articles in various databases and evaluating them to obtain necessary information. The sources were extracted from trustworthy sources for scientific research, such as ScienceDirect and Scopus, to verify quality assurance and data reliability. Consequently, the thirty-five peer-reviewed articles, proceedings, and online resources were analyzed and compared to understand the impact of digitalization on the Six Sigma methodology.
The Latest Development and the Impact of Digitalization on the Six Sigma Implementation
With the evolution of digitalization, traditional methodologies are often combined with new technologies. Lean Six Sigma and Industry 4.0 offer possibilities to companies for better data analysis and processes optimization (Bhat et al., 2021; Arcidiacono & Pieroni, 2018). Sanders et al. (2016) argue that Industry 4.0 provides high-end technology solutions to facilitate Lean Six Sigma’s enhancement. For instance, Analytics and robust data mining in the ‘Measure’ and ‘Analyze’ phase of Lean Six Sigma combined with technologies will result in a well-founded decision, improved product quality, and the Turn-Around-Time (TAT) reduction (Bhat et al., 2021; Dogan & Gurcan, 2018; Júnior et al., 2018). Sodhi (2020) states that future processes “will embed more technology and may become smarter, but they will remain processes” (p. 5). The deployment of both Industry 4.0 and Lean Six Sigma can be implemented by any organization, regardless of its size (Tortorella & Fettermann, 2018). Thus, Industry 4.0 would not replace the Lean Six Sigma methodology, however, rather dramatically improve it.
Consequently, the new digital technologies can be used to intensify DMAIC initiatives. Hofmann (2021) claims that Six Sigma methods should become more flexible due to digitalization to provide a faster response to customers’ needs and requirements. Notably, there is a necessity for Lean Six Sigma to move towards digitalization. Javaid et al. (2021) inform that digitalization is suitable for Six Sigma methods to accelerate uninterrupted improvement. Digitalization affects Six Sigma significantly; for instance, paper-based processes are replaced by various mobile solutions (Rio, 2019). Martinez (2019) emphasizes that digitalization and new technologies are tools and drivers for processes brilliance. The Industry 4.0 technologies can be combined with the Lean Six Sigma methodology to improve business processes, as shown in Figure 3.
Therefore, data accumulation and measurement are completed with the assistance of the Internet of Things, Artificial Intelligence, and robotics. Cui et al. (2020) inform that the Internet of Things is crucial for operational excellence. Basios and Loucopoulos (2017) argue that the fundamental idea behind Industry 4.0 is to connect virtual and real realities into the Internet of Things (IoT). Thus, the Six Sigma DMAIC will be strengthened by IoT, which allows collecting, measuring, analyzing, and controlling data, inputs, and outputs more efficiently.
Additionally, 3D printing can be utilized in the ‘Improve’ phase of DMAIC. Hence, 3D printing is used to create prototypes and present new products and ideas faster (Chiarini & Kumar, 2020). Therefore, companies can use 3D printing instead of traditional prototyping methods to increase the value for customers. Goffnett et al. (2019) present a theoretical study illustrating that drones can be used successfully in the Lean Six Sigma DMAIC in a logistics field. In addition, drones have the capacity of scanning places and taking photos; therefore, they can be used in ‘Measure’ and ‘Control’ steps.
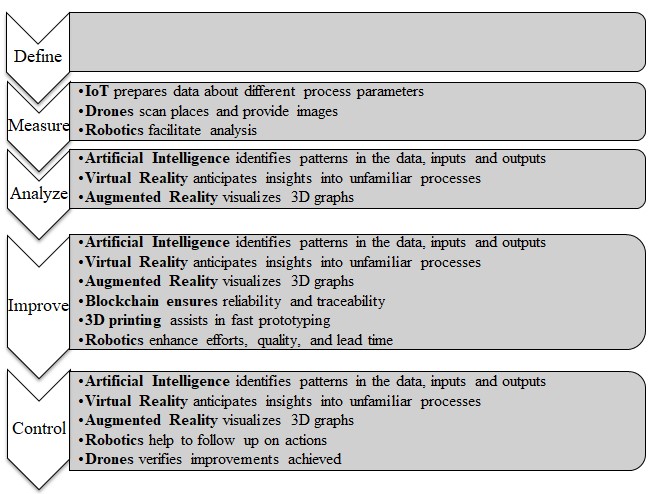
Essentially, blockchain technology is a brilliant solution for the ‘Improve’ phase because it ensures traceability and reliability. Blockchain technology improves the management of data obtaining processes and makes them accurate and intelligent (Giacalone et al., 2021). Augmented reality assists in refining and controlling business processes. Rifqi et al. (2021) suggest that the interaction of Lean Six Sigma with augmented and virtual realities makes processes easy to implement. Sordan et al. (2021) determined that virtual reality and augmented reality can be applied in training activities. Moreover, augmented reality and virtual reality may be used to visualize 3D graphs in the ‘Analyze,’ ‘Improve,’ and ‘Control’ phases.
Robotics is another effective mechanism that can be combined with Lean Six Sigma. Companies usually employ robotics to achieve quality improvement (Yadav et al., 2021). According to Silantyev et al. (2019), robotics accelerates repeating operations of data reformatting with the support of Machine Vision and Natural Language processing. Therefore, the concept relates to the DMAIC’s ‘Measure,’ ‘Improve,’ and ‘Control.’
Moreover, Artificial Intelligence assists in investigating patterns in the data and defining the connection between inputs and outputs. Companies may apply Artificial Intelligence, namely Machine Learning, to synthesize and boost the success elements of Lean Six Sigma (Perera et al., 2021). Szedlak et al. (2020) argue that Industrial AI applications are vital for organizations to achieve success. Therefore, AI ensures that data is processed intelligently and accurately.
Lessons Learned and Conclusions
Lessons
As a result, Industry 4.0 definitely influence the Six Sigma implementation. Essentially, Industry 4.0, together with Lean Six Sigma, enhances customer engagement through better and faster connectivity (The Manufacturer, 2018). Chiarini & Kumar (2020) acknowledge that Lean Six Sigma provides a “good base to remove waste and minimize variation before embarking on automation and use of cyber technologies” (p. 9). To conclude, Lean Six Sigma can be a crucial base for successfully combining Industry 4.0 technologies with internal and external processes (Chiarini & Kumar, 2020). Haartman et al. (2021) justify that Industry 4.0 facilitates Six Sigma and Lean methods. Various Industry 4.0 techniques and Lean Six Sigma methodology can work in practice to add more value to offerings, processes, and products.
Conclusions
In the era of digitalization, organizations are forced to adapt their processes and old models to rapid technological change. Digitalization is a modification of a business using the latest digital technologies; for example, Industry 4.0 is characterized by technological trends such as artificial intelligence, blockchain, virtual reality, robotics, among others. Lean Six Sigma is a proven method based on systematic waste disposal and business process optimization and includes the following steps: Define, Measure, Analyze, Improve, and Control, briefly, DMAIC. Consequently, the Industry 4.0 technologies should be applied in Lean Six Sigma DMAIC to improve company productivity, add additional value to products and services, and enhance customer experience. To conclude, the Digital Era provides excellent opportunities and efficient tools for implementing Lean Six Sigma.
References
Antony, J., Snee, R., & Hoerl, R. (2017). Lean Six Sigma: Yesterday, today and tomorrow. International Journal of Quality & Reliability Management, 34(7), 1073-1093.
Arcidiacono, G., & Pieroni, A. (2018). The revolution lean six sigma 4.0. Int. J. Adv. Sci. Eng. Inf. Technol, 8(1), 141-149.
Basios, A. and Loucopoulos, P. (2017). Six Sigma DMAIC enhanced with capability modelling. 2017 IEEE 19th Conference on Business Informatics (CBI), 2017, pp. 55-62, doi: 10.1109/CBI.2017.70
Bhat, V.S., Bhat, S. and Gijo, E.V. (2021), Simulation-based lean six sigma for Industry 4.0: An action research in the process industry. International Journal of Quality & Reliability Management, 38(5), 1215-1245.
Chiarini, A., and Kumar, M. (2020). Lean Six Sigma and Industry 4.0 integration for operational excellence: Evidence from Italian manufacturing companies. Production Planning & Control, 1–18.
Cui, L., Gao, M., Dai, J. and Mou, J. (2020). “Improving supply chain collaboration through operational excellence approaches: An IoT perspective”, Industrial Management & Data Systems, Vol. ahead-of-print No. ahead-of-print.
Dalenogare, L. S., Benitez, G. B., Ayala, N. F., & Frank, A. G. (2018). The expected contribution of Industry 4.0 technologies for industrial performance. International Journal of Production Economics, 204, 383-394.
Dogan, O., & Gurcan, O. F. (2018). Data perspective of Lean Six Sigma in industry 4.0 Era: A guide to improve quality. In Proceedings of the International Conference on Industrial Engineering and Operations Management Paris.
Engin, B. E., Khajeh, E., & Paksoy, T. (2020). Lean Manufacturing and Industry 4.0: A framework to integrate the two paradigms. In Logistics 4.0 (pp. 350-360). CRC Press.
Ghobakhloo, M. (2020). Industry 4.0, digitization, and opportunities for sustainability. Journal of cleaner production, 252, 119869.
Giacalone, M., Santarcangelo, V., Donvito, V., Schiavone, O., & Massa, E. (2021). Big data for corporate social responsibility: Blockchain use in Gioia del Colle DOP. Quality & Quantity, 1-27.
Goffnett, S. P., Paquet, A. N., Strong, O. M., & McCarron, K. P. (2019). Replication of a Six Sigma black belt case study: GEP box’s paper helicopter experiment in a drone logistics scenario. International Journal of Productivity and Quality Management, 27(1), 17-65. doi: 10.1504/IJPQM.2019.099628
Haartman, R. V., Bengtsson, L., & Niss, C. (2021). Lean practices and the adoption of digital technologies in production. International Journal of Services and Operations Management, 40(2), 286-304. doi: 10.1504/IJSOM.2021.118260
Hofmann, M. (2021). Influence of digitalisation on process optimisation. In A Holistic Approach to Process Optimisation (pp. 121-134). Springer, Wiesbaden.
Javaid, M., Haleem, A., Singh, R. P., Rab, S., Suman, R., & Khan, S. (2021). Exploring relationships between Lean 4.0 and manufacturing industry. Industrial Robot: Vol. ahead-of-print No. ahead-of-print.
Juliani, F., & de Oliveira, O. J. (2020). Lean Six Sigma principles and practices under a management perspective. Production Planning & Control, 31(15), 1223-1244.
Júnior, F. M., Montenegro, M., Thadani, R., Pedroso, G. A., & de Oliveira, M. A. (2018). Industry 4.0 as a way to enhance Lean Manufacturing and Six Sigma. In Proceedings of European Lean Educator Conference (pp. 152-160).
Martinez, F. (2019). Process excellence the key for digitalisation. Business Process Management Journal, 25(7), 1716-1733.
Perera, A. D., Jayamaha, N. P., Grigg, N. P., Tunnicliffe, M., & Singh, A. (2021). The application of machine learning to consolidate critical success factors of lean six sigma. IEEE Access, 9, 112411-112424. doi: 10.1109/ACCESS.2021.3103931
Prasad, A., Kurup, A., Jishnu, K., Abhisek, G., Samanta, A. K., & Varaprasad, G. (2020). Lean Six Sigma solutions for quality improvement in healthcare sector: A systematic review. In 2020 International Conference on System, Computation, Automation and Networking (ICSCAN) (pp. 1-5). IEEE. doi:10.1109/ICSCAN49426.2020.9262289
Rifqi, H., Zamma, A., Souda, S. B., & Hansali, M. (2021). Positive Effect of Industry 4.0 on Quality and Operations Management. International Journal of Online & Biomedical Engineering, 17(9).
Rio, R. (2019). Lean Six Sigma with digitalization and Industry 4.0. ARC Advisory Group.
Sanders, A., Elangeswaran, C., & Wulfsberg, J. P. (2016). Industry 4.0 implies lean manufacturing: Research activities in industry 4.0 function as enablers for lean manufacturing. Journal of Industrial Engineering and Management (JIEM), 9(3), 811-833. doi:10.3926/jiem.1940
Silantyev, A., Tyagi, A., Dejonckheere, J., and Theuns, L. (2019). What would continuous improvement look like in the Industry 4.0 world? PWC.
Singh, M., & Rathi, R. (2018). A structured review of Lean Six Sigma in various industrial sectors. International Journal of Lean Six Sigma, 10(2), 622-644.
Six Sigma Daily. (2020). The importance of process improvement in Industry 4.0. Six Sigma Daily.
Sodhi, H. (2020). When Industry 4.0 meets lean six sigma: A review. Industrial Engineering Journal, 13(1), 1-12.
Sordan, J. E., Oprime, P. C., Pimenta, M. L., da Silva, S. L., & González, M. O. A. (2021). Contact points between Lean Six Sigma and Industry 4.0: A systematic review and conceptual framework. International Journal of Quality & Reliability Management.
Szedlak, C., Poetters, P., & Leyendecker, B. (2020). Application of Artificial Intelligence In Small and Medium-Sized Enterprises. In Proceedings at 5th NA International Conference on Industrial Engineering and Operations Management.
The Manufacturer. (2018). Sigma accelerate Industry 4.0 and IoT? The Manufacturer.
Timans, W., Ahaus, K., van Solingen, R., Kumar, M., & Antony, J. (2016). Implementation of continuous improvement based on Lean Six Sigma in small-and medium-sized enterprises. Total Quality Management & Business Excellence, 27(3-4), 309-324.
Titmarsh, R., Assad, F., & Harrison, R. (2020). Contributions of lean six sigma to sustainable manufacturing requirements: An Industry 4.0 perspective. Procedia CIRP, 90, 589-593.
Tortorella, G. L., & Fettermann, D. (2018). Implementation of Industry 4.0 and lean production in Brazilian manufacturing companies. International Journal of Production Research, 56(8), 2975-2987.
Yadav, N., Shankar, R., & Singh, S. P. (2021). Critical success factors for lean six sigma in quality 4.0. International Journal of Quality and Service Sciences, 13(1), 123-156.
Yuen, K. F., Thai, V. V., & Wong, Y. D. (2016). The effect of continuous improvement capacity on the relationship between of corporate social performance and business performance in maritime transport in Singapore. Transportation Research Part E: Logistics and Transportation Review, 95, 62-75.